Electrical equipment is integral to modern operations across industries, powering essential systems and machinery. However, this reliance has inherent risks, including electric shock, burns, fires, and equipment damage. These hazards can result in severe injuries, costly downtime, and even regulatory penalties without proper safeguards. Guarding electrical equipment is not just a safety measure but a critical responsibility for organizations to protect their workforce, property, and compliance standing.
This blog delves into the importance of effectively guarding electrical equipment, the risks of neglecting this practice, and proven methods to ensure safety and efficiency. Whether you want to enhance your workplace safety protocols or comply with regulatory standards, this comprehensive guide will equip you with actionable insights to safeguard your operations and promote a secure environment.
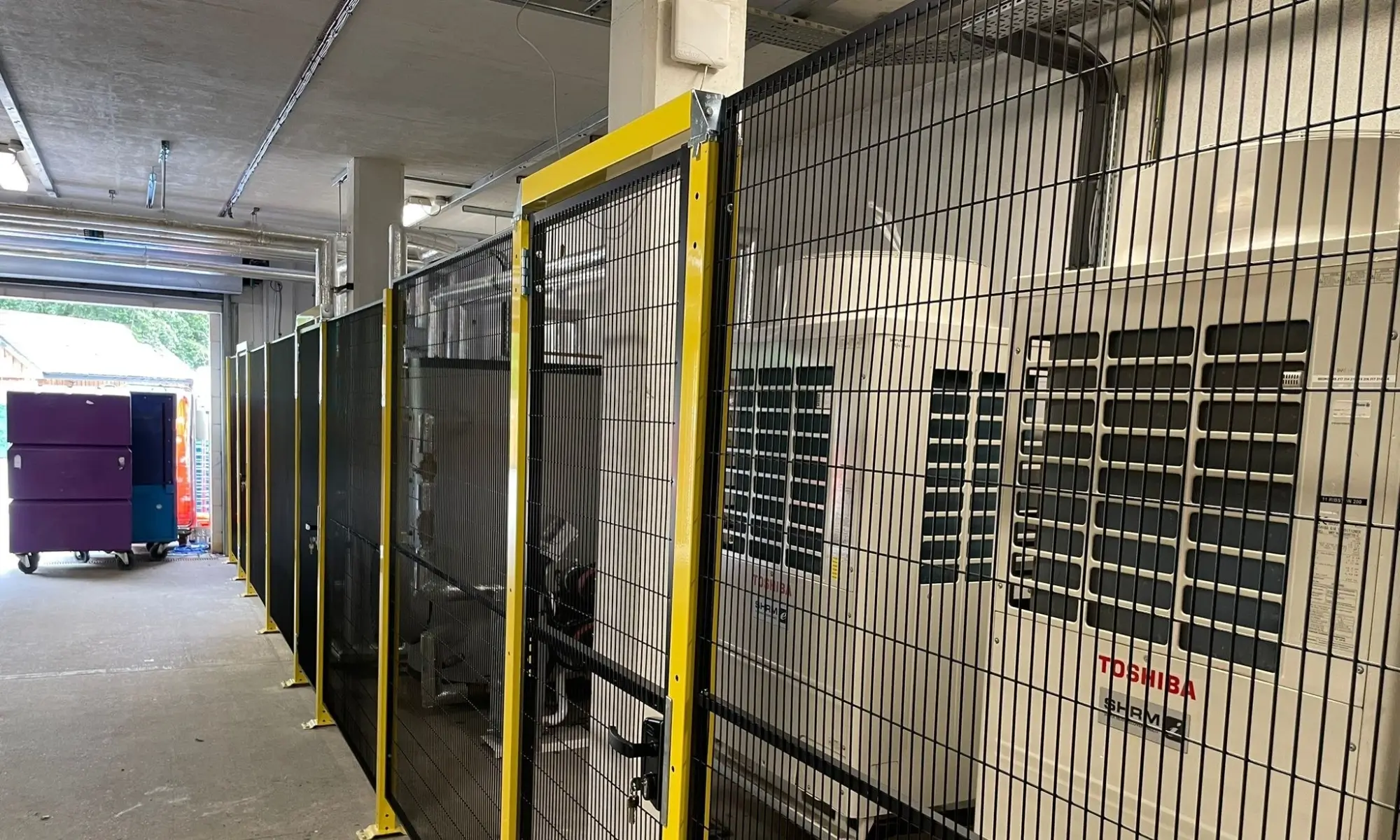
Effectively Guarding Electrical Equipment
Electrical guarding is the process of enclosing or protecting electrical equipment to prevent accidental contact with live parts or electrical hazards. Electrical guarding is an essential aspect of electrical safety and is necessary to protect employees and property from electrical hazards.
Guarding involves locating or enclosing electric equipment to ensure people do not accidentally contact live parts. Effective guarding requires equipment with exposed parts operating at 50 volts or more to be placed where it is accessible only to authorized people qualified to work with it. Recommended locations are:
- A room, vault, or similar enclosure;
- A balcony, gallery, or elevated platform; or
- A site elevated 8 feet or more above the floor.
Sturdy, permanent screens can also serve as effective guards. Conspicuous electrical safety signs must be posted at the entrances to electrical rooms and similarly guarded locations to alert people to electrical hazards and forbid unauthorized entry.
By following these steps, you can help ensure that your electrical equipment is properly guarded and that your employees and customers are protected against electrical hazards. It is also important to continually assess and update your safety procedures and guarding to ensure that they are effective and meet the changing needs of your business.
Importance Of Guarding Electrical Equipment
Guarding electrical equipment is extremely important to prevent injury or damage. Electrical equipment can be dangerous and cause electric shock, burns, fires, explosions, and other serious accidents if not properly guarded. The following are some reasons why guarding electrical equipment is crucial:
- Protecting employees: Proper guarding of electrical equipment can prevent employees from being injured or killed by electric shock or other electrical hazards. Guarding also helps employees follow safe work practices and use appropriate personal protective equipment.
- Preventing damage to the equipment: Guarding helps to prevent damage to electrical equipment from accidental contact, environmental factors, and other sources of damage. This can help extend the equipment’s life and prevent costly repairs or replacements.
- Complying with regulations: Many regulatory agencies, such as OSHA (Occupational Safety and Health Administration) and NEC (National Electrical Code), require electrical equipment to be guarded to protect employees from electrical hazards. Compliance with these regulations can help to avoid fines, legal penalties, and reputational damage.
- Improving productivity: Properly guarded electrical equipment allows employees to work more safely and efficiently without fear of injury or damage to equipment. This can help improve productivity and reduce downtime due to accidents or equipment failures.
In summary, guarding electrical equipment is essential for protecting employees, preventing damage to equipment, complying with regulations, and improving productivity. Proper guarding should be a priority for all organizations that use electrical equipment.
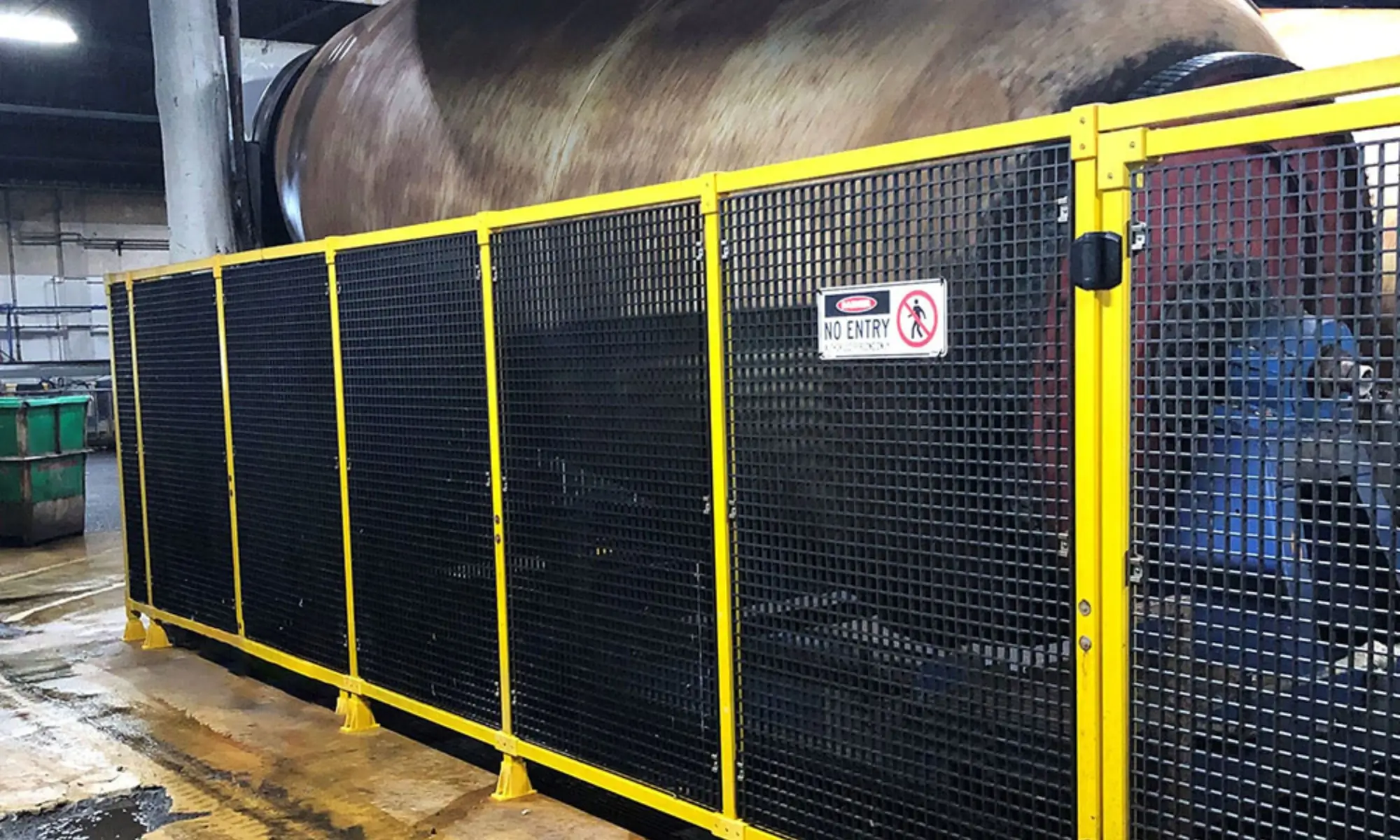
Risks Of Not Guarding Electrical Equipment
Not guarding electrical equipment can result in serious risks to employees, equipment, and property. Some of the risks associated with not guarding electrical equipment include:
- Electric shock: The most obvious risk of not guarding electrical equipment is the potential for electric shock. Electric shock can cause serious injury, including burns, muscle contractions, and cardiac arrest. In some cases, electric shock can even be fatal.
- Burns: Unguarded electrical equipment can produce high levels of heat that can burn employees or damage nearby property.
- Fires and explosions: Electrical equipment not properly guarded can create sparks, arcing, and other heat sources that can start fires or cause explosions.
- Property damage: Electrical equipment that is not guarded can damage property, including buildings, machinery, and other equipment.
- Financial losses: In addition to physical risks, not guarding electrical equipment can result in financial losses due to damage to equipment, property, and potential legal liabilities.
- Regulatory penalties: Failure to properly guard electrical equipment can result in regulatory penalties, fines, and legal liabilities.
- Loss of productivity: Accidents related to not guarding electrical equipment can result in lost work time, lower productivity, and increased costs.
In summary, the risks of not guarding electrical equipment are significant and can result in serious injury, property damage, financial losses, and regulatory penalties. Proper guarding of electrical equipment is essential for ensuring employee safety and protecting property and equipment.
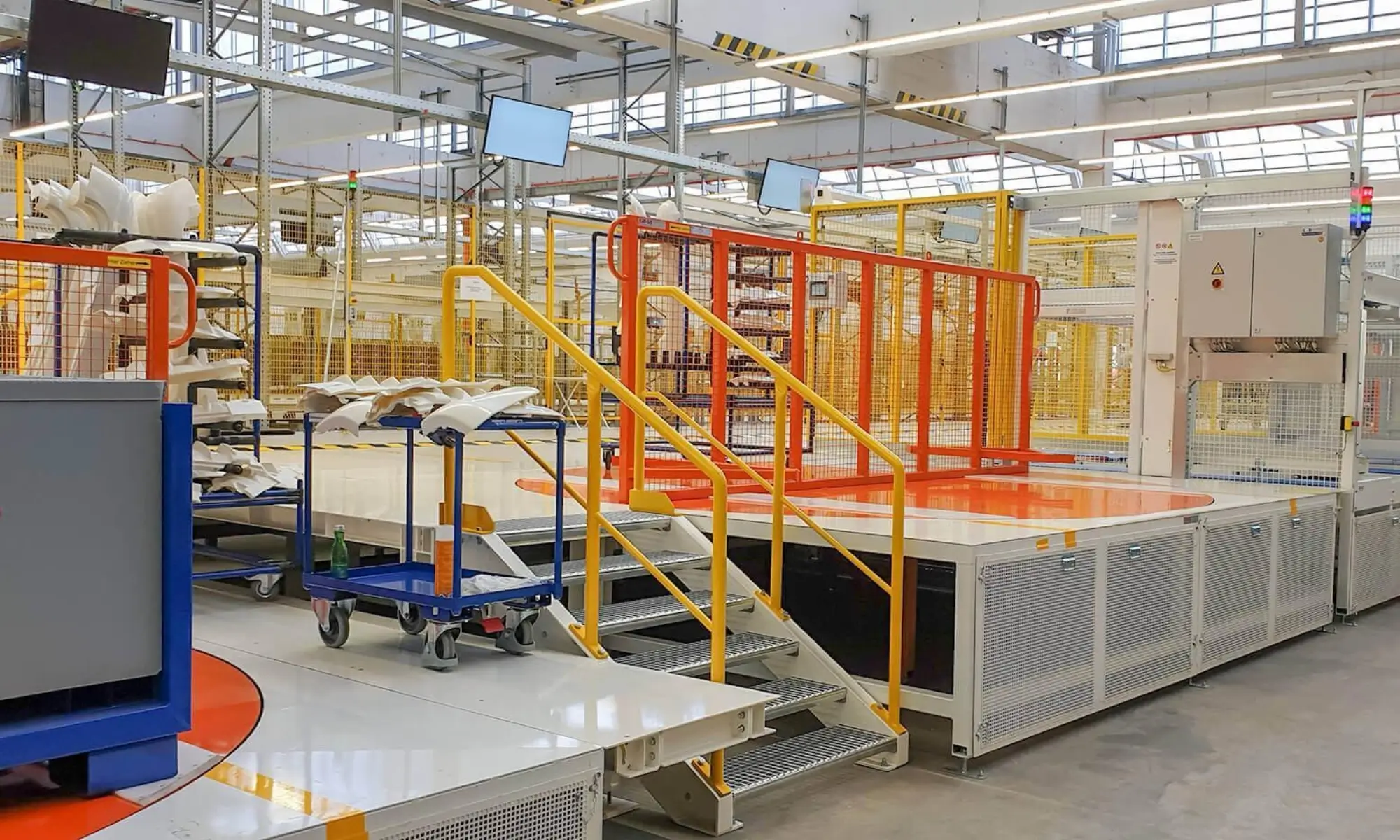
Methods For Effectively Guarding Electrical Equipment
Maintaining electrical equipment is essential to preventing accidents, protecting assets, and ensuring compliance with safety regulations. Below are detailed explanations for each best practice, along with a summary in bullet format for clarity.
1. Use of Enclosures
Enclosing electrical equipment in durable, non-conductive materials such as fiberglass or polycarbonate ensures protection from environmental elements and accidental contact with live parts. These enclosures prevent unauthorized access and are particularly effective in harsh or high-traffic environments. They should be designed to withstand physical impact, moisture, and dust, maintaining the integrity of electrical systems. Secure enclosures with locks to restrict access to trained personnel only.
Key Points:
- Enclose equipment in durable, non-conductive materials.
- Protect against environmental factors like dust and moisture.
- Restrict access with locks to authorized personnel.
- Use impact-resistant enclosures for added durability.
- Example: Fiberglass or polycarbonate enclosures.
2. Implementation of Lockout/Tagout Procedures
Lockout/Tagout (LOTO) systems are essential during maintenance or repair to prevent accidental energization of equipment. This process involves isolating energy sources and attaching tags indicating the equipment is being serviced. Proper training and consistent application of LOTO procedures enhance workplace safety and ensure compliance with standards.
Key Points:
- Isolate energy sources during maintenance or repair.
- Attach tags to indicate equipment is under service.
- Prevent accidental energization of equipment.
- Provide thorough training on LOTO procedures.
- Enforce consistent application across all operations.
3. Grounding
Grounding ensures electrical faults are safely redirected to the ground, minimizing the risk of electric shock and equipment damage. Proper grounding systems connect all conductive parts to a reliable earthing point. Regular inspections should verify the integrity of grounding connections, ensuring they are functional and compliant with safety standards.
Key Points:
- Redirect fault currents to the ground to prevent shocks.
- Connect conductive parts to a grounding system.
- Inspect grounding connections regularly for functionality.
- Ensure compliance with electrical safety standards.
- Reduce risk of equipment damage and operational hazards.
4. Insulation
High-quality insulation prevents electricity from escaping wires and equipment components, ensuring safety and efficiency. Insulating covers shield live parts, reducing the risk of accidental contact. Properly rated insulation for voltage and current levels is critical for maintaining electrical system integrity and user safety.
Key Points:
- Use high-quality insulation materials for wiring.
- Cover live parts with insulating barriers.
- Prevent electricity from escaping equipment.
- Ensure insulation is rated for the voltage and current it handles.
- Example: Rubber insulation for wires.
5. Physical Barriers
Physical barriers like fences, screens, or panels effectively restrict access to hazardous electrical areas. Clear warning signs should accompany these barriers to alert personnel about the dangers. Barriers also protect equipment from unintentional contact or damage in busy environments.
Key Points:
- Install fences, screens, or panels to restrict access.
- Mark hazardous areas with visible warning signs.
- Protect equipment from accidental contact or damage.
- Ensure barriers are sturdy and appropriately positioned.
- Example: “High Voltage” signage in industrial settings.
6. Elevated Placement
Mounting equipment 8 feet or higher keeps it out of reach of unauthorized individuals and reduces accidental exposure to live parts. Alternatively, equipment can be housed in secured rooms or on elevated platforms, providing additional safety and security in critical areas.
Key Points:
- Mount equipment 8 feet or higher to restrict access.
- Use secured rooms or elevated platforms for additional protection.
- Ensure only authorized personnel can access mounted equipment.
- Enhance safety in high-risk or high-traffic areas.
- Reduce accidental exposure to live parts.
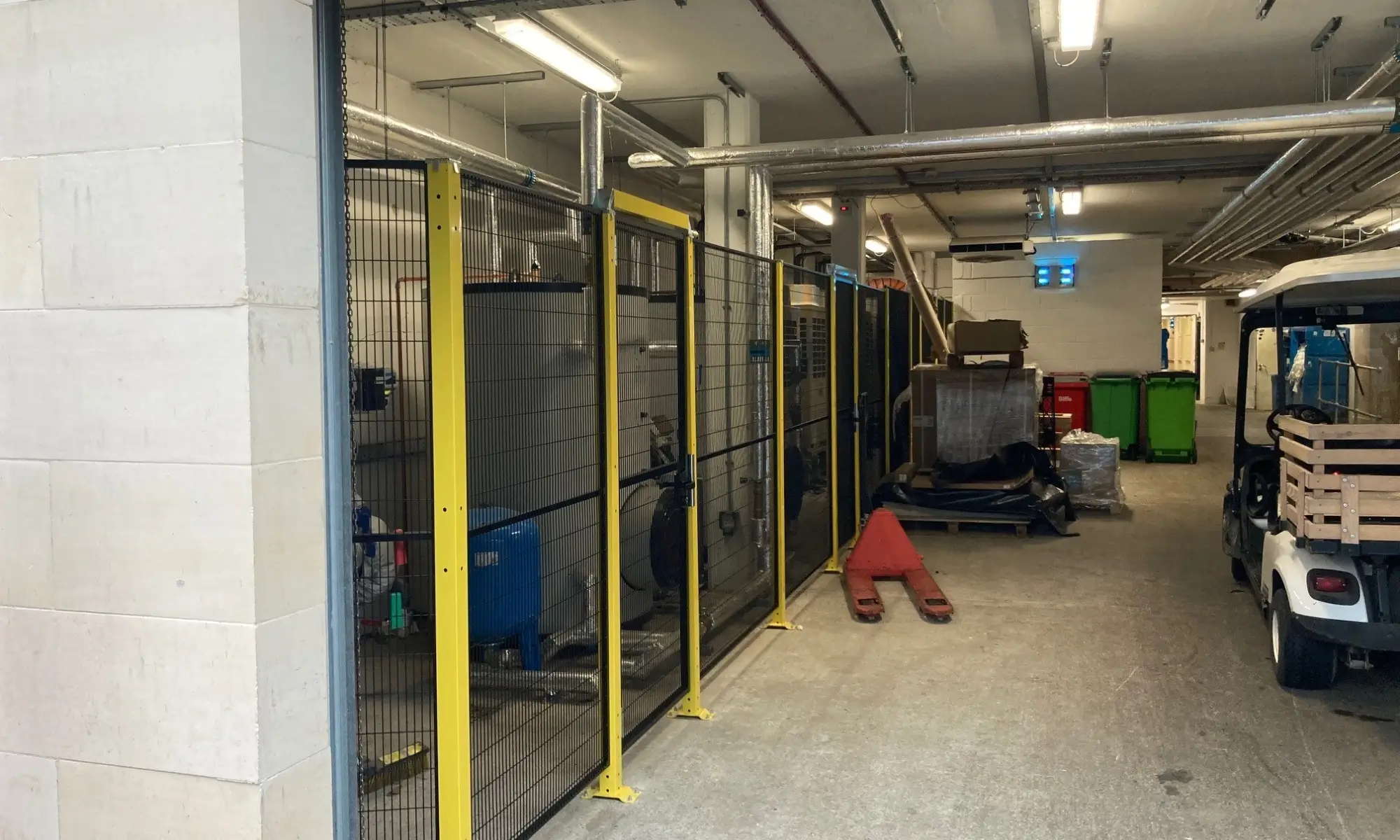
7. Regular Maintenance and Inspection
Routine inspections and maintenance are vital for identifying and rectifying wear and tear before accidents occur. Testing safety mechanisms like circuit breakers and verifying grounding systems ensure the equipment remains operational and safe. A proactive approach to maintenance minimizes downtime and reduces repair costs.
Key Points:
- Conduct regular inspections for wear and tear.
- Test safety mechanisms like circuit breakers.
- Verify the integrity of grounding systems.
- Replace damaged or worn components promptly.
- Prevent accidents and minimize equipment downtime.
8. Training and Education
Training employees on identifying electrical hazards and safe practices empowers them to respond appropriately to risks. Regularly updated training ensures that staff stays informed about evolving safety standards and technologies. Empowering employees with knowledge is a critical step in creating a workplace safety culture.
Key Points:
- Train employees to identify electrical hazards.
- Provide education on proper safety protocols.
- Regularly update training programs to reflect new standards.
- Promote a culture of safety and awareness.
- Empower employees to respond appropriately to risks.
By implementing these best practices, organizations can create a safer workplace, protect their employees, and ensure compliance with regulatory requirements. Prioritizing electrical equipment safety not only mitigates risks but also fosters efficiency and trust within the workplace.
Conclusion
Guarding electrical equipment is not merely a compliance requirement but a crucial measure to ensure the safety of employees, equipment, and property. Failing to guard electrical equipment can lead to devastating consequences, including severe injuries, costly repairs, operational downtime, and regulatory penalties. Organizations can mitigate risks and create a safer, more productive work environment by implementing effective methods such as enclosures, lockout/tagout procedures, grounding, insulation, and regular maintenance.
Investing in employee training and adhering to electrical safety standards further solidifies a safety and operational excellence culture. The importance of safeguarding electrical equipment cannot be overstated—it is a vital step in minimizing hazards, maintaining compliance, and protecting the well-being of everyone involved. Prioritize safety, and ensure your workplace is prepared to handle the demands of today’s electrical systems securely and efficiently.