Workplace safety is a fundamental aspect of any organization, as accidents can lead to severe physical injuries, emotional distress, and financial burdens for both employees and employers. Despite ongoing efforts to improve safety standards, workplace accidents remain a common challenge across industries. Understanding the causes and nature of these accidents is essential for creating a safer work environment.
This blog explores the definition of workplace accidents, highlights their key characteristics, and outlines the 12 most common causes, offering practical strategies for prevention and promoting a culture of safety and well-being in the workplace.
What are Workplace Accidents?
Workplace accidents are unexpected and unplanned events that occur while an employee is performing their job duties, resulting in physical injury, illness, or harm. These accidents can range from minor injuries like cuts and bruises to severe incidents such as fractures, burns, or even fatalities. Workplace accidents can also lead to psychological stress and trauma, especially in cases involving violence or life-threatening situations.
Key Characteristics of Workplace Accidents:
- Location: The accident must happen at the workplace or while the employee is engaged in work-related activities (including remote work or business travel).
- Connection to Job Duties: The incident must be linked to the employee’s work tasks or the working environment.
- Injury or Harm: The event results in some form of physical or psychological injury, damage, or distress to the employee.
- Unintentional: Workplace accidents are typically unintended, though they may result from negligence, lack of training, or failure to follow safety protocols.
Examples of Workplace Accidents:
- A worker slipping on a wet floor in an office.
- A construction worker falling from scaffolding.
- An employee getting electrocuted due to faulty wiring.
- A warehouse worker sustaining a back injury from improper lifting.
- A chemical spill leading to respiratory issues for employees nearby.
- A manufacturing worker losing a finger due to an unguarded machine.
Common Causes Of Workplace Accidents
Workplace accidents can occur in any industry, and they can result in injuries, lost productivity, and financial burdens for both employees and employers. Here are 12 common causes of workplace accidents:
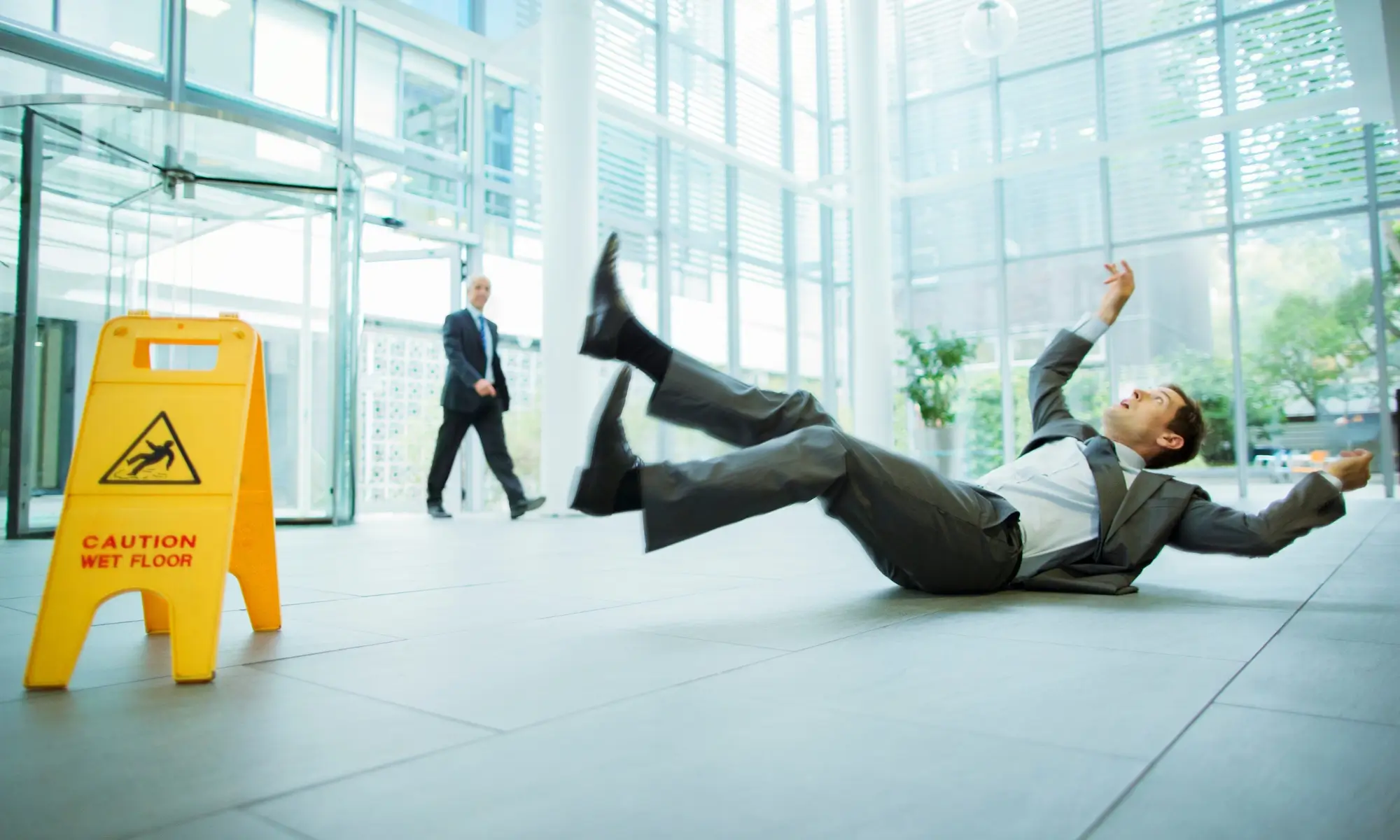
1. Slips, Trips, And Falls
Slips, trips, and falls are common workplace accidents in various settings, from offices to construction sites. These accidents can lead to serious injuries, lost productivity, and high financial costs for employees and employers. Here is a more detailed explanation of the various factors that contribute to slips, trips, and falls in the workplace:
- Wet or slippery floors: Spills, leaks, or recently mopped floors can create slippery surfaces, increasing the risk of employees slipping and falling. In outdoor settings, weather conditions such as rain, snow, or ice can make surfaces slippery and hazardous.
- Cluttered work areas: Poor housekeeping or a disorganized workspace can lead to obstacles and hazards that may cause employees to trip and fall. These hazards might include scattered tools, boxes, other equipment, and cables or cords running across walkways.
- Loose rugs or mats: Rugs, mats, or floor coverings that are not properly secured can cause employees to trip or slip. This can be particularly dangerous in high-traffic areas or near stairs and entryways.
- Uneven surfaces: Uneven or damaged flooring, such as cracked tiles, potholes, or irregular surfaces, can cause workers to lose their footing and fall. In outdoor settings, uneven ground, like holes or depressions, can also pose a tripping hazard.
- Inadequate lighting: Poor lighting can make it difficult for employees to see and navigate their surroundings, increasing the risk of slips, trips, and falls.
- Stairs and steps: Unmarked or poorly maintained stairs and missing or damaged handrails can increase the likelihood of falling accidents.
- Footwear: Inappropriate or ill-fitting footwear can contribute to slips and falls, particularly if employees are not wearing shoes with proper traction or support.
Employers should maintain clean and organized workspaces, ensure adequate lighting, repair damaged or uneven flooring, and provide appropriate footwear for employees to minimize the risk of slips, trips, and falls in the workplace. Regular safety training and reminders can also help employees be more mindful of potential hazards and take the necessary precautions to prevent accidents.
2. Poor Ergonomics
Poor ergonomics refers to workplace conditions that do not support the physical well-being of employees, leading to discomfort, strain, or injury over time. Ergonomics focuses on designing workspaces, tasks, and equipment to fit the needs and abilities of employees. Inadequate ergonomics can contribute to a range of musculoskeletal disorders (MSDs), affecting muscles, nerves, tendons, joints, and other soft tissues. Some common issues related to poor ergonomics include:
- Inadequate workstation setup: Workstations that are not properly adjusted to an individual’s height, reach, or body shape can force employees to work in uncomfortable positions, causing strain and discomfort over time. For example, a poorly positioned computer monitor may require the worker to crane their neck, while a chair without proper lumbar support can contribute to lower back pain.
- Incorrect posture: Sitting or standing in improper positions for extended periods can put undue stress on the body, leading to MSDs. Poor posture may include slouching, hunching over, or not using the backrest of a chair, all of which can contribute to back, neck, and shoulder pain.
- Repetitive motions: Performing the same motion or task repeatedly, such as typing, lifting, or using a particular tool, can cause strain and wear on specific body parts. Over time, this can lead to conditions like carpal tunnel syndrome, tendinitis, or bursitis.
- Forceful exertions: Tasks that require employees to use excessive force, such as lifting heavy objects or applying pressure when using tools, can lead to muscle strains and other MSDs.
- Awkward positions: Twisting, bending, reaching, or working in other uncomfortable positions for extended periods can place stress on the body and increase the risk of MSDs.
To improve ergonomics in the workplace, employers should consider the following steps:
- Provide adjustable workstations, chairs, and other equipment to accommodate individual needs.
- Offer training on proper posture and body mechanics.
- Encourage regular breaks and stretching exercises to alleviate strain.
- Rotate tasks to reduce the risk of repetitive motion injuries.
- Implement engineering controls, such as lift assists, to minimize forceful exertions.
- Assess and address ergonomic risks as part of an ongoing workplace safety program.
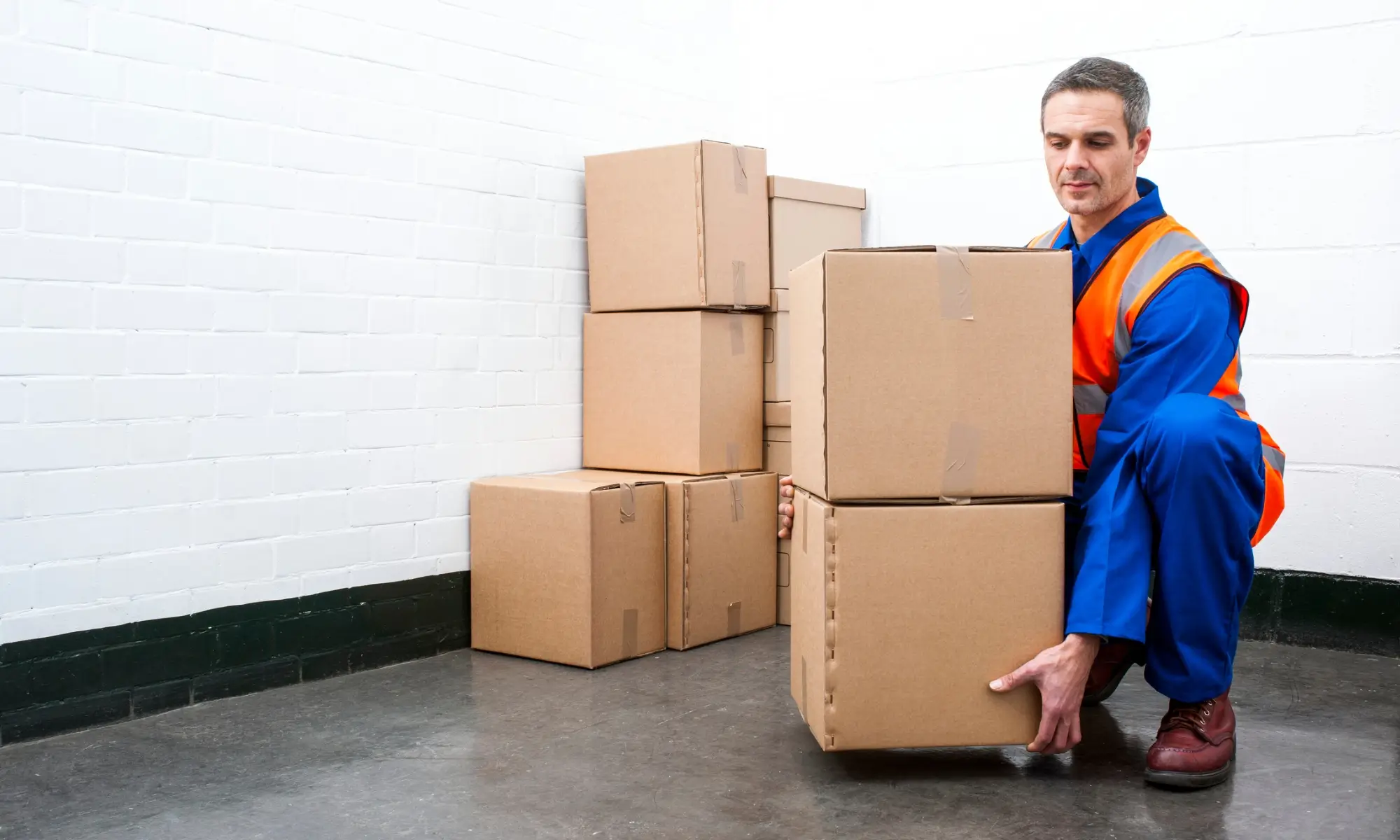
3. Manual Handling And Lifting
Manual handling and lifting refer to tasks that involve using the human body to lift, lower, push, pull, carry, or otherwise move objects. These tasks are common in many workplaces, from warehouses and construction sites to offices and retail environments. When done improperly, manual handling can lead to various injuries, including strains, sprains, or hernias. Some factors that contribute to these injuries include:
- Incorrect lifting techniques: Lifting heavy objects with poor form, such as bending at the waist instead of squatting, can place excessive strain on the back, neck, and shoulders, leading to injuries like muscle strains and herniated discs.
- Overexertion: Attempting to lift or move objects that are too heavy without assistance or mechanical aids can cause employees to overexert themselves, resulting in muscle strains, sprains, or other injuries.
- Awkward postures: Lifting or carrying objects in uncomfortable positions, such as reaching overhead or twisting the body, can increase the risk of injury.
- Repetitive motions: Performing manual handling tasks repeatedly over time can lead to wear and tear on the body, potentially causing injuries like tendinitis or carpal tunnel syndrome.
- Lack of training: Employees who have not received proper training on safe lifting and handling techniques may be more likely to use poor form, increasing their risk of injury.
To prevent manual handling and lifting injuries in the workplace, employers should:
- Provide training on proper lifting and handling techniques, emphasizing the importance of using the legs to lift, keeping the load close to the body, and avoiding twisting or bending at the waist.
- Encourage employees to ask for help or use mechanical aids, such as hand trucks, dollies, or hoists, when lifting or moving heavy objects.
- Implement task rotation to minimize repetitive motions and reduce the risk of injury.
- Assess and adjust work processes to minimize the need for manual handling or to make tasks safer and more ergonomic.
- Promote a safety culture that encourages employees to prioritize their well-being and to report any unsafe practices or conditions.
4. Inadequate Training
Inadequate training significantly contributes to workplace accidents, as employees who have not received proper instruction may be unaware of the necessary precautions, procedures, and techniques to perform their tasks safely.
Conducting a safety stand down can provide an opportunity to reinforce proper training and address any gaps in knowledge, helping employees better understand safety protocols and procedures. The lack of appropriate training can manifest in several ways, leading to increased risks in the workplace:
- Unfamiliarity with equipment or machinery: Employees who have not been trained on the correct usage, maintenance, and safety features of equipment or machinery may misuse or mishandle these tools, leading to accidents or injuries.
- Ineffective use of personal protective equipment (PPE): Workers who have not been trained in properly selecting, using, and maintaining PPE may be more vulnerable to injury or exposure to hazardous substances or conditions.
- Unsafe work practices: Without proper training, employees may develop and follow unsafe work practices, such as improper lifting techniques or bypassing safety procedures, which can lead to accidents or injuries.
- Poor hazard identification and communication: Insufficient training may result in employees being unaware of potential hazards or not knowing how to communicate risks to their colleagues, increasing the likelihood of accidents.
- Inadequate emergency response: Employees who have not been trained in emergency response procedures may not know how to react appropriately in the event of an incident, potentially exacerbating the situation and increasing the risk of injuries or fatalities.
To mitigate the risks associated with inadequate training, employers should:
- Develop and implement comprehensive training programs that cover the specific tasks, equipment, and hazards associated with each employee’s job responsibilities.
- Ensure that employees receive training on the proper use of PPE and understand its importance in preventing injuries and exposure to hazardous materials.
- Regularly evaluate and update training materials and methods to remain relevant, effective, and aligned with industry standards and regulations.
- Offer refresher training courses to help employees maintain their knowledge and skills and to keep them informed of any changes in procedures, equipment, or regulations.
- Foster a workplace safety culture, encouraging employees to actively participate in training, ask questions, and report concerns about their work environment or tasks.
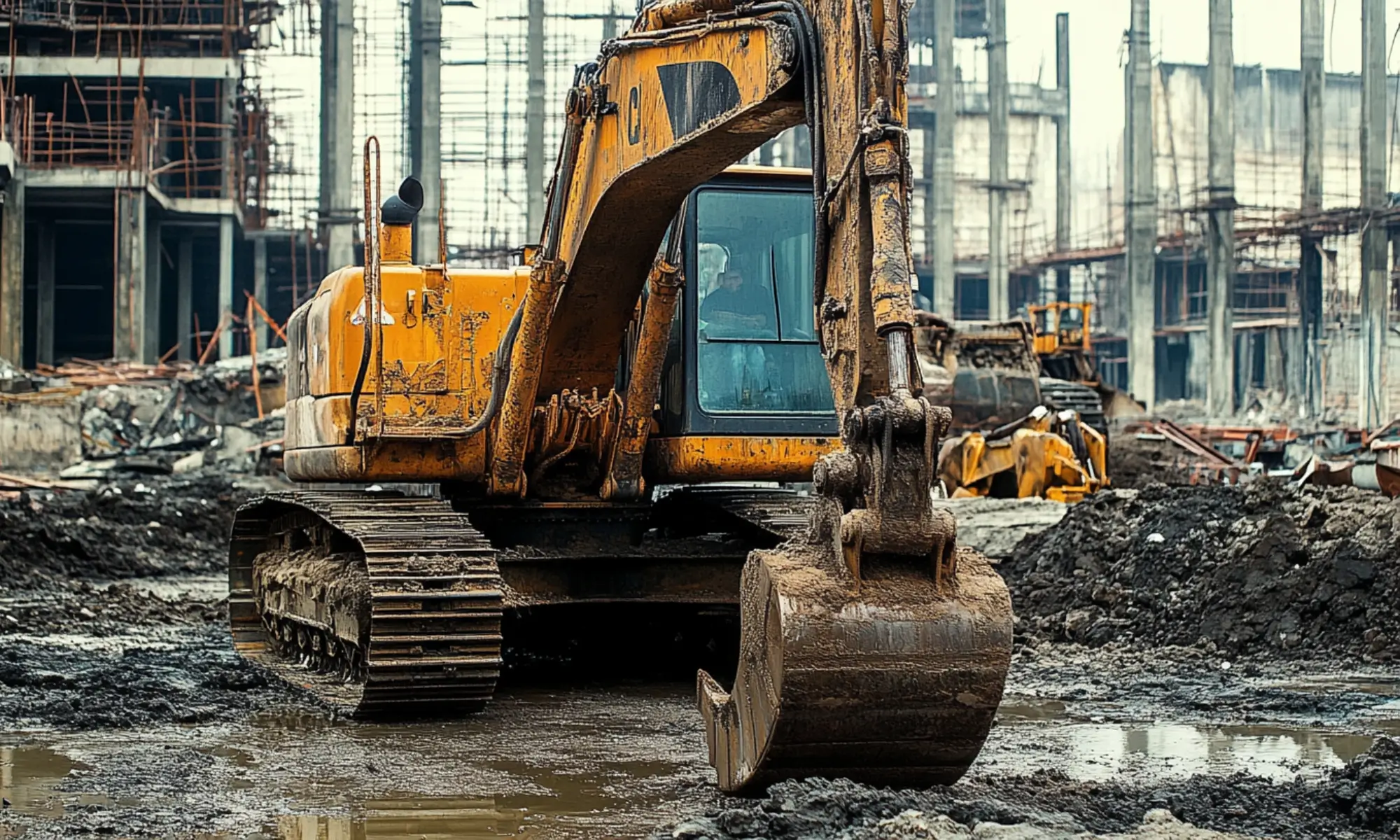
5. Faulty Or Poorly Maintained Equipment
Faulty or poorly maintained equipment can pose significant risks in the workplace, as it may not function as intended or may fail unexpectedly, leading to accidents and injuries. Various factors contribute to the hazards associated with faulty or poorly maintained equipment:
- Malfunctioning components: Equipment with malfunctioning parts, such as brakes, gears, or safety features, can lead to unexpected failures or accidents, putting workers at risk.
- Wear and tear: Over time, equipment and tools can become worn, damaged, or less effective due to regular use, increasing the risk of accidents or injuries.
- Inadequate maintenance: Failing to perform regular inspections, repairs, or maintenance can result in equipment becoming unsafe or unreliable, which may lead to accidents.
- Outdated equipment: Older equipment may not meet current safety standards or may lack modern safety features, increasing the likelihood of accidents or injuries.
- Improper modifications: Unauthorized or improper modifications to equipment can compromise its safety and effectiveness, potentially leading to accidents.
To minimize the risks associated with faulty or poorly maintained equipment, employers should:
- Implement a regular maintenance and inspection schedule for all equipment, ensuring that necessary repairs or adjustments are made promptly.
- Train employees on the proper use, maintenance, and inspection of equipment, emphasizing the importance of reporting any signs of wear, damage, or malfunction.
- Replace outdated or unsafe equipment with newer models that meet current safety standards and have appropriate safety features.
- Discourage unauthorized modifications to equipment and ensure that any alterations are made by qualified personnel in accordance with manufacturer guidelines and safety standards.
- Establish a system for tracking equipment maintenance and repair history and any incidents or accidents involving equipment to help identify trends or recurring issues that may warrant further investigation or action.
Employers can help prevent accidents, reduce downtime, and create a safer work environment for their employees by prioritizing equipment maintenance and safety.
6. Chemical Exposure
Chemical exposure in the workplace can occur when employees come into contact with toxic or hazardous substances during their job tasks. These substances may include solvents, cleaning agents, pesticides, industrial chemicals, or airborne particles. Exposure to such chemicals can have both immediate and long-term health effects, depending on the type, concentration, and duration of exposure. Common health issues associated with chemical exposure include:
- Respiratory problems: Inhalation of toxic substances, such as vapors, fumes, or dust, can cause irritation or damage to the respiratory system, leading to conditions like asthma, bronchitis, or even lung disease.
- Skin irritation: Direct contact with hazardous chemicals can cause burns, rashes, or other skin irritations. In some cases, chemicals can be absorbed through the skin, potentially leading to systemic health effects.
- Eye irritation: Exposure to chemical vapors, splashes, or airborne particles can cause irritation, burns, or injury to the eyes, potentially leading to vision impairment or blindness.
- Neurological effects: Exposure to certain toxic substances can affect the nervous system, resulting in symptoms such as headaches, dizziness, or even long-term neurological disorders.
- Cancer and other long-term health effects: Chronic exposure to some hazardous chemicals, such as asbestos or benzene, can increase the risk of developing cancer or other serious health conditions.
To minimize the risk of chemical exposure in the workplace, employers should:
- Conduct a thorough hazard assessment to identify potential chemical hazards and determine the appropriate control measures.
- Implement proper storage, handling, and disposal procedures for hazardous substances, following all applicable regulations and guidelines.
- Provide appropriate personal protective equipment (PPE), such as gloves, goggles, and respirators, to protect employees from direct contact with hazardous chemicals.
- Train employees on the proper use, handling, and storage of chemicals, as well as the potential health risks associated with exposure and the necessary precautions to minimize those risks.
- Ensure proper ventilation and air filtration systems are in place to reduce airborne chemical hazards.
- Establish an emergency response plan for chemical spills, leaks, or other incidents, including procedures for containment, cleanup, and reporting.
By proactively addressing chemical hazards and providing employees with the necessary training and protection, employers can help prevent chemical exposure-related health issues and create a safer work environment.
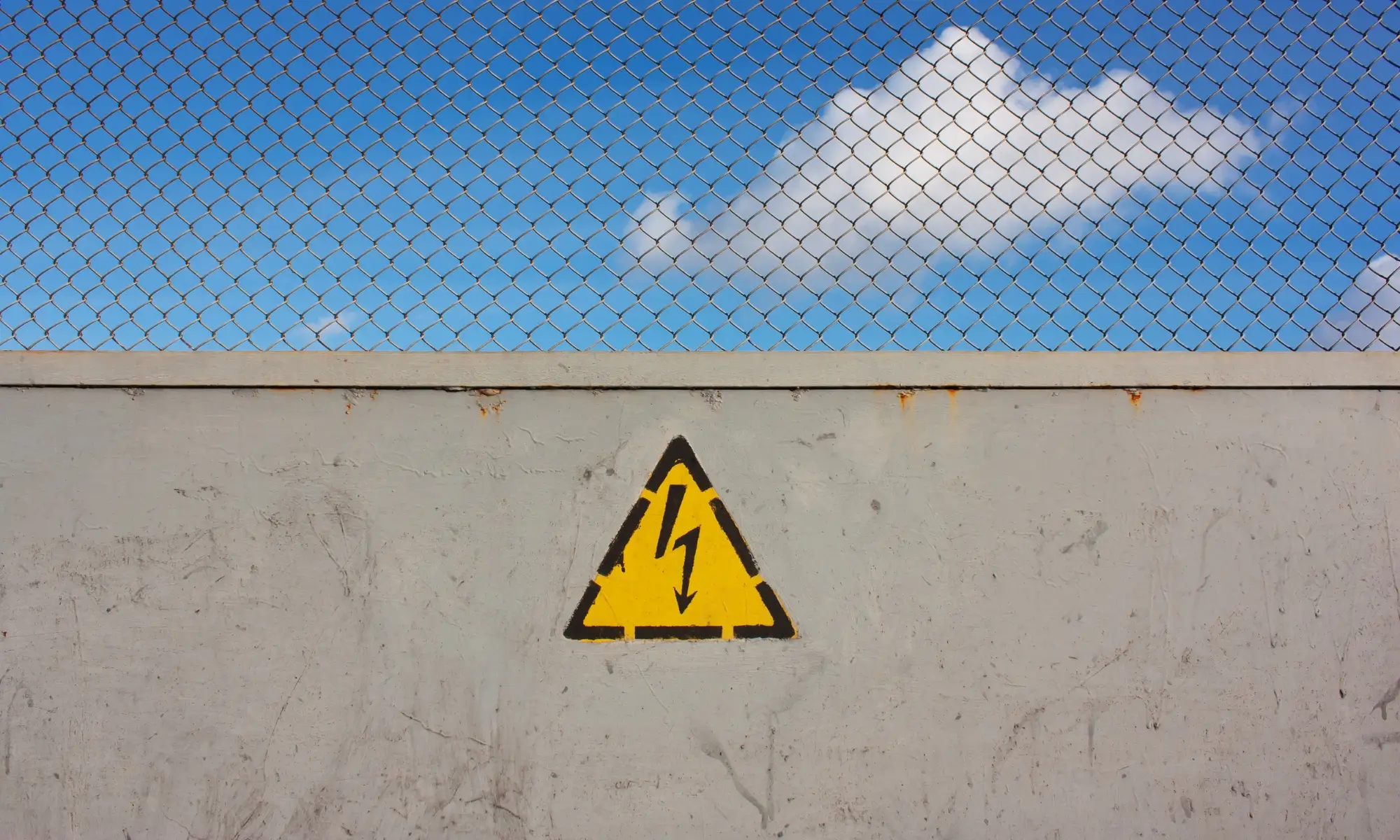
7. Electrical Hazards
Electrical hazards in the workplace pose significant risks to employees and can lead to serious accidents, including electrocution, fires, or explosions. These hazards can result from a variety of factors, such as faulty wiring, improper grounding, or the use of damaged electrical equipment or tools. Some common causes of electrical hazards include:
- Faulty wiring: Damaged, frayed, or exposed wires can lead to electrical shorts or arcing, which can cause fires, explosions, or electrocution.
- Improper grounding: Inadequate grounding of electrical systems can result in voltage fluctuations or electrical shocks when employees come into contact with improperly grounded equipment or machinery.
- Damaged electrical equipment or tools: The use of electrical equipment or tools with damaged cords, plugs, or casings can expose employees to the risk of electrical shocks or fires.
- Overloaded circuits or outlets: Overloading electrical circuits by using too many devices on a single outlet or by using extension cords improperly can result in overheating, which may cause fires or damage to electrical equipment.
- Lack of proper safety devices: Electrical systems lacking proper safety devices, such as circuit breakers, ground fault circuit interrupters (GFCIs), or arc fault circuit interrupters (AFCIs), can increase the risk of electrical accidents.
- Working in wet or damp conditions: The presence of moisture can increase the conductivity of electrical current, raising the risk of electrical shocks or short circuits.
To minimize electrical hazards in the workplace, employers should:
- Conduct regular inspections of electrical systems, equipment, and tools to identify and address potential hazards.
- Ensure proper grounding of electrical systems and equipment, following all applicable codes and regulations.
- Train employees on safe work practices when working with or around electricity, including the proper use, inspection, and maintenance of electrical equipment and tools.
- Implement procedures for locking out and tagging out electrical equipment during maintenance or repair work to prevent accidental energization.
- Provide appropriate personal protective equipment (PPE) for employees working with or around electricity, such as insulated gloves, non-conductive footwear, and safety goggles.
- Enforce a safety culture that emphasizes the importance of electrical safety and encourages employees to report any hazards or concerns promptly.
By addressing electrical hazards proactively and ensuring employees follow safe work practices, employers can help prevent accidents, protect their workforce, and maintain a safe working environment.
8. Falling Objects
Falling objects in the workplace can pose a significant risk to employees, especially in environments like construction sites, warehouses, and manufacturing facilities where items are often stored or moved at elevated heights. Objects can fall from shelves, scaffolding, cranes, or other elevated surfaces, leading to serious injuries or even fatalities. Common injuries resulting from falling objects include head trauma, broken bones, lacerations, and bruises.
Several factors contribute to the risk of falling objects:
- Improper storage: Overloading shelves or stacking items haphazardly can increase the likelihood of objects falling.
- Unsecured loads: Failing to secure materials or equipment during transport or lifting can result in objects falling from vehicles, cranes, or other moving equipment.
- Insufficient barriers or guarding: Lack of proper safety measures, such as toe boards or guardrails, can allow objects to fall from elevated surfaces, putting workers below at risk.
- Poor housekeeping: Cluttered work areas and improperly stored tools or materials can increase the likelihood of objects falling or being knocked over.
To minimize the risk of falling objects in the workplace, employers should:
- Implement proper storage procedures, ensuring that shelves and racks are not overloaded and that items are stacked securely and neatly.
- Train employees on safe material handling and lifting techniques, emphasizing the importance of securing loads and using appropriate lifting equipment.
- Install safety features, such as guardrails, toe boards, or netting, to prevent objects from falling from elevated surfaces or work areas.
- Require employees to wear appropriate personal protective equipment (PPE), such as hard hats, to protect against potential head injuries from falling objects.
- Encourage good housekeeping practices, maintaining clean and organized work areas to reduce the risk of accidents.
- Establish a safety culture that emphasizes the importance of preventing falling object hazards and encourages employees to report any concerns or unsafe conditions.
By taking these proactive measures, employers can help reduce the risk of injuries from falling objects, creating a safer work environment for their employees.

9. Vehicle Accidents
Vehicle accidents in the workplace can occur in various settings, such as warehouses, construction sites, and manufacturing facilities, where forklifts, trucks, or other vehicles are used to transport materials and equipment. Collisions involving these vehicles can result in severe injuries or fatalities to both drivers and nearby workers. Some common causes of workplace vehicle accidents include:
- Operator error: Lack of proper training, inattention, or careless operation can lead to collisions or loss of control of the vehicle.
- Speeding: Driving too fast for the conditions or exceeding posted speed limits can increase the risk of accidents.
- Poor visibility: Blind spots, inadequate lighting, or obstructed views can make it difficult for operators to see workers, obstacles, or other vehicles, increasing the risk of collisions.
- Mechanical failure: Faulty brakes, steering systems, or other mechanical issues can cause accidents if not addressed promptly.
- Inadequate traffic controls: Poorly designed or maintained traffic routes, lack of signage, or unclear right-of-way rules can contribute to confusion and accidents.
To minimize the risk of vehicle accidents in the workplace, employers should:
- Provide comprehensive training for all vehicle operators, covering safe driving practices, vehicle operation, and maintenance procedures.
- Implement and enforce speed limits and other traffic rules to promote safe driving behaviors.
- Ensure adequate visibility by providing sufficient lighting, installing mirrors at blind spots, and keeping traffic routes free of obstructions.
- Conduct regular inspections and maintenance of vehicles to identify and address any mechanical issues before they lead to accidents.
- Design and maintain clear, well-marked traffic routes, including pedestrian walkways and designated vehicle lanes, to reduce the risk of collisions.
- Encourage a safety culture that emphasizes the importance of safe driving and vehicle operation, and encourages employees to report any hazards or concerns.
By proactively addressing potential vehicle accident risks and fostering a safety-conscious work environment, employers can help protect their employees and reduce the likelihood of serious accidents involving vehicles.
10. Inadequate Safety Gear
Inadequate safety gear, or lack of proper personal protective equipment (PPE), can significantly increase the risk of workplace injuries. PPE protects workers from various hazards, such as impact, chemical exposure, heat, and electricity. When workers are not provided with appropriate PPE or fail to use it correctly, they become more vulnerable to injuries. Some common types of PPE include:
- Hard hats: Protect the head from impact injuries caused by falling objects or collisions.
- Safety goggles or glasses: Protect the eyes from flying debris, chemicals, or other hazards.
- Gloves: Protect the hands from cuts, burns, chemical exposure, or other injuries.
- Respiratory protection: Protects the lungs from inhaling hazardous particles, vapors, or gases.
- Hearing protection: Protects the ears from loud noises that can cause hearing damage.
- Safety footwear: Protects the feet from punctures, impacts, or electrical hazards.
To ensure workers are adequately protected by PPE, employers should:
- Conduct a hazard assessment to identify potential risks in the workplace and determine the appropriate types of PPE needed to protect employees.
- Provide employees with the proper PPE, ensuring it fits correctly and is in good condition.
- Train employees on the correct use, maintenance, and limitations of their PPE, emphasizing the importance of wearing it consistently and appropriately.
- Regularly inspect PPE for signs of wear, damage, or degradation, and replace it as needed to ensure its effectiveness.
- Foster a safety culture that prioritizes PPE and encourages employees to report any concerns about their safety gear or working conditions.
By providing appropriate PPE and promoting its consistent use, employers can significantly reduce the risk of workplace injuries and create a safer work environment for their employees.
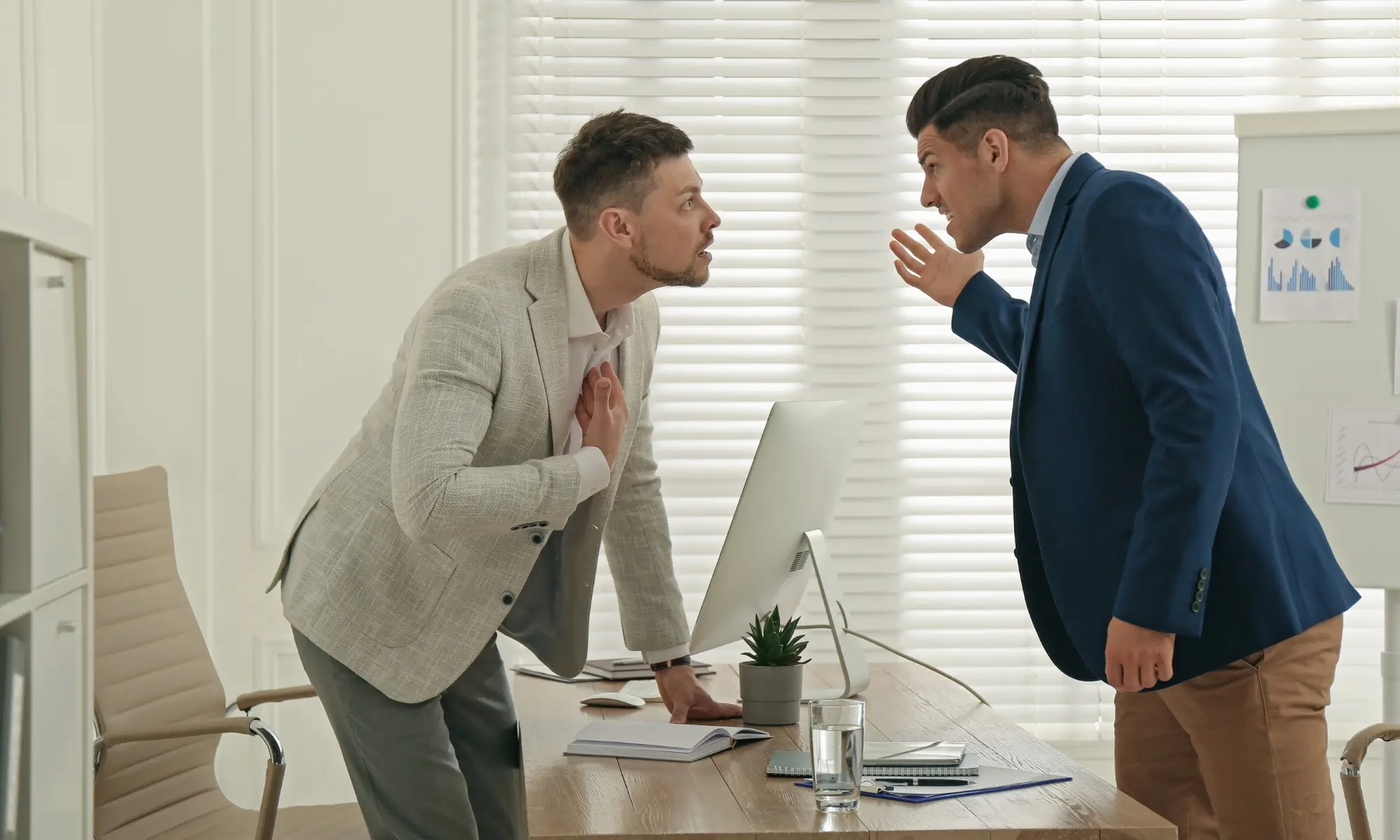
11. Workplace Violence
Workplace violence refers to any act or threat of physical violence, harassment, intimidation, or other disruptive behavior that occurs at a work site. Conflicts or coworker disputes can escalate into physical altercations, leading to injuries or even fatalities. In addition to physical harm, workplace violence can have psychological and emotional consequences for both the victims and witnesses.
Several factors can contribute to workplace violence:
- High-stress environments: Jobs with high-stress levels, tight deadlines, or heavy workloads can create employee tension and conflict.
- Lack of conflict resolution training: Inadequate conflict resolution or communication skills training can make it more difficult for employees to resolve disagreements peacefully.
- Substance abuse: Employees struggling with substance abuse issues may be more prone to aggressive behavior or impaired judgment, increasing the risk of violent incidents.
- Inadequate security measures: Poorly secured workplaces can make it easier for disgruntled employees or outside individuals to enter and engage in violent behaviour.
To minimize the risk of workplace violence, employers should:
- Implement a zero-tolerance policy for workplace violence, clearly outlining the consequences of violent behavior and emphasizing the importance of maintaining a safe and respectful work environment.
- Train employees in conflict resolution, communication, and de-escalation techniques to help them effectively handle disagreements and tensions.
- Encourage open communication and provide channels for employees to report concerns, grievances, or potential threats without fear of retaliation.
- Implement security measures, such as access control systems, surveillance cameras, and security personnel, to deter and respond to potential acts of violence.
- Offer employee assistance programs (EAPs) or other resources to support employees struggling with personal issues or stressors that could contribute to violent behavior.
- Foster a positive workplace culture that promotes teamwork, respect, and inclusivity, reducing the likelihood of conflicts and aggression among employees.
By proactively addressing the risk factors associated with workplace violence and promoting a safe and supportive work environment, employers can help protect their employees and reduce the likelihood of violent incidents.
12. Human Error
Human error is a major contributor to workplace accidents, and it can result from various factors, including stress, fatigue, distraction, and lack of training. Some examples of human errors that can lead to accidents in the workplace include:
Failure to follow safety procedures: When employees neglect safety protocols, such as locking out equipment during maintenance or wearing proper personal protective equipment, they increase the risk of accidents.
- Inattention or distraction: Employees who are distracted or not paying attention to their surroundings may fail to notice hazards, resulting in accidents.
- Poor judgment: Employees may make poor decisions, such as taking shortcuts or bypassing safety measures, in an effort to save time or complete tasks more efficiently.
- Lack of training or experience: Employees who are not properly trained or lack experience in performing certain tasks may be more prone to making mistakes or taking unnecessary risks.
To minimize the risk of human error in the workplace, employers should:
- Provide comprehensive training on safety procedures and protocols, emphasizing the importance of following them consistently.
- Encourage a safety culture that prioritizes the well-being of employees and emphasizes the importance of safety in all aspects of the job.
- Ensure employees are properly rested and not overworked, reducing the risk of fatigue-related errors.
- Implement technology and equipment to reduce human error, such as automatic shut-off switches or sensors that detect potential hazards.
- Conduct regular safety audits to identify potential hazards and workplace improvement areas.
- Encourage employees to promptly report any potential hazards or concerns and take corrective action as needed.
By proactively addressing potential human errors and fostering a safety-conscious culture, employers can reduce the likelihood of workplace accidents and create a safer, healthier work environment for everyone.
Conclusion
Workplace accidents can have serious consequences for both employees and businesses, including physical injuries, financial losses, and reduced productivity. By understanding the common causes of workplace accidents—such as slips and falls, poor ergonomics, inadequate training, and human error—employers can take proactive steps to minimize risks and create a safer work environment. Implementing comprehensive safety protocols, providing proper training and equipment, and fostering a culture of safety and accountability are key to preventing accidents. When employers and employees work together to prioritize safety, they can reduce workplace accidents, improve employee well-being, and enhance overall business performance.