Chemical hazards are present in various forms daily, including in the workplace. Exposure to hazardous chemicals can lead to serious health effects, including cancer, respiratory illnesses, and skin irritations. Therefore, controlling these hazards is of utmost importance to ensure the safety and well-being of workers.
The hierarchy of control is a framework used to manage and control workplace hazards. It prioritizes the most effective methods to control hazards, from the most effective to the least effective. This framework can also be applied to control chemical hazards, and it provides a structured approach to managing these hazards.
This blog will discuss the hierarchy of control and how it can be used to control chemical hazards. We will go through each level of the hierarchy and provide examples of how it can be applied in the workplace. By the end of this blog, you will better understand how to control chemical hazards and ensure the safety of workers in your workplace.
Common Chemicals Hazards You Need To Know
There are many hazardous chemicals that people may come into contact with in their daily lives. Here are some common chemicals and their hazards:
- Bleach: Bleach is a strong oxidizing agent and can cause severe skin and eye irritation, respiratory distress, and even death if ingested.
- Ammonia: Ammonia is a highly irritating gas that can cause respiratory distress and burns to the eyes, skin, and respiratory tract.
- Pesticides: Pesticides can cause a range of health problems, including skin irritation, respiratory problems, and neurological damage.
- Lead: Exposure to lead can cause a range of health problems, including developmental delays, cognitive impairment, and damage to the nervous system.
- Mercury: Mercury is a toxic heavy metal that can cause brain and kidney damage and respiratory problems.
- Asbestos: Asbestos is a fibrous mineral that can cause lung cancer, mesothelioma, and other respiratory diseases when inhaled.
- Formaldehyde: Formaldehyde is a carcinogenic gas that can cause respiratory distress, skin irritation, and cancer.
- Benzene: Benzene is a highly flammable and carcinogenic chemical that can cause leukemia, anemia, and other blood disorders.
- Carbon Monoxide: Carbon monoxide is a poisonous gas that can cause headaches, nausea, and even death when inhaled in high concentrations.
- Hydrochloric Acid: Hydrochloric acid is a highly corrosive acid that can cause severe skin and eye irritation, respiratory distress, and even death if ingested.
It’s important to be aware of the potential hazards of these chemicals and take appropriate precautions when handling them or being exposed to them. Always read the labels, follow safety instructions when using chemicals, and wear protective clothing and equipment when necessary.
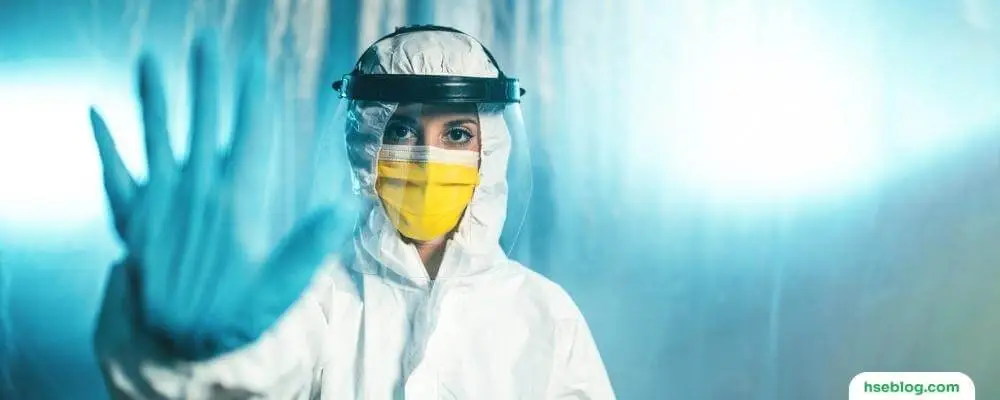
How To Control Chemical Hazards | Hierarchy Of Control
The Hierarchy of Control is a system that prioritises different control measures based on their effectiveness in reducing exposure to chemical hazards. The system consists of five levels, each building upon the previous one to provide increasing levels of protection.
1. Elimination/Substitution
Elimination/Substitution is the first level of the Hierarchy of Control, and it involves eliminating the chemical hazard altogether or substituting it with a less hazardous substance. This is the most effective level of control as it completely removes the hazard from the workplace, eliminating the risk of exposure.
Examples of Elimination/Substitution include:
- Replacing a toxic cleaning agent with a non-toxic one.
- Using a less hazardous chemical in a manufacturing process.
- Substituting a hazardous material with a non-hazardous one.
- Eliminating a step in the manufacturing process involves using hazardous chemicals.
Elimination/Substitution is the most effective level of control because it removes the hazard from the workplace altogether. This level of control can be achieved by modifying the chemical process or by using a different chemical with similar properties but less risk of harm to workers. It may also involve redesigning the product or process to avoid using hazardous chemicals altogether.
Substitution is often the preferred method for Elimination/Substitution because it is usually easier and less expensive than redesigning the process or product. For example, a toxic solvent may be replaced with a less toxic solvent or a water-based cleaning solution.
Elimination/Substitution is the most effective level of control because it eliminates the hazard from the workplace altogether, thereby reducing the risk of exposure to workers. However, it can be challenging to implement because it often requires significant changes to the manufacturing process or product design. Employers should consider Elimination/Substitution as the first option for controlling chemical hazards and should only resort to other control measures if it is not possible to eliminate or substitute the hazard.
2. Engineering Controls
Engineering Controls are physical or mechanical controls used to minimize exposure to chemical hazards in the workplace. These controls are the second level of the Hierarchy of Control, and they focus on changing the workplace environment or equipment to reduce the risk of exposure to the hazard.
Examples of Engineering Controls include:
- Ventilation systems: These systems remove or dilute hazardous chemicals from the air, reducing the concentration of the chemical and the risk of exposure. Examples of ventilation systems include local exhaust ventilation, which captures and removes the chemical at the source, and general ventilation, which circulates fresh air throughout the workplace.
- Enclosures and barriers: These physical barriers can prevent workers from coming into contact with hazardous chemicals. Examples include fume hoods, which enclose a chemical process and prevent fumes from escaping into the workplace, and physical barriers, such as walls or shields, which can protect workers from chemical splashes.
- Process isolation: This involves separating the process that produces the chemical hazard from the rest of the workplace. Examples include conducting chemical processes in separate rooms or using sealed containers to transport hazardous chemicals.
- Substitution of hazardous chemicals: This involves replacing a hazardous chemical with a less hazardous alternative. This can be achieved by modifying the chemical process or using a different chemical with similar properties but less risk of harming workers.
Engineering Controls effectively reduce exposure to chemical hazards by removing or reducing the hazard at the source. They also do not rely on worker compliance and are more reliable than Administrative Controls. However, they can be more expensive to implement than Administrative Controls and may require significant workplace environment or equipment changes.
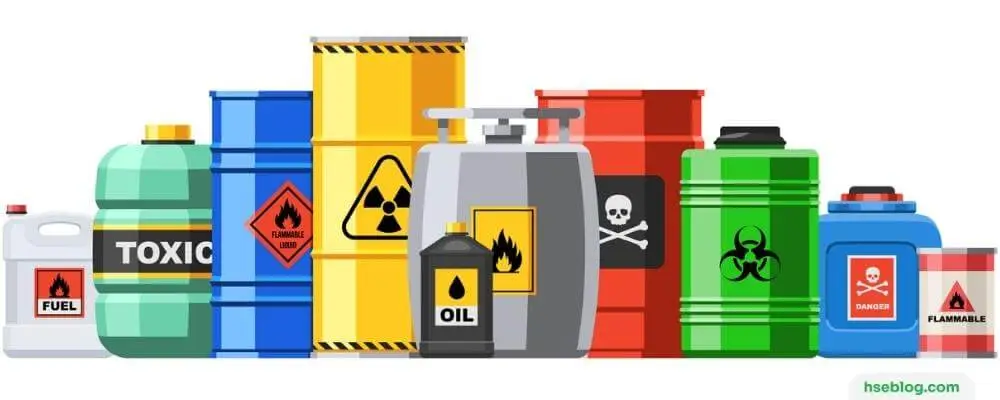
Employers should regularly review and update their Engineering Controls to ensure that they remain effective and relevant to the hazards in their workplace. By implementing effective Engineering Controls, employers can create a safer workplace and protect workers from the harmful effects of chemical hazards.
3. Administrative Controls
Administrative Controls are policies and procedures implemented by an organization to minimize exposure to chemical hazards in the workplace. These controls are the third level of the Hierarchy of Control, and they focus on changing how work is done to reduce the risk of exposure to the hazard.
Examples of Administrative Controls include:
- Work schedule: This involves scheduling work to minimise exposure to chemical hazards. For example, scheduling work that involves the use of hazardous chemicals during times when fewer workers are present in the facility.
- Training: This involves educating workers about the hazards associated with their work and how to work safely with chemicals. Training can include information on the safe handling, storage, and disposal of chemicals.
- Signs and labels: This involves using signs and labels to communicate the hazards associated with chemicals and the precautions workers need to take when working with them.
- Work procedures: This involves developing and implementing standard operating procedures (SOPs) for hazardous chemical tasks. These procedures can help ensure that workers perform tasks safely and consistently.
- Exposure monitoring: This involves regularly monitoring the levels of exposure to chemicals in the workplace to identify areas where exposure can be reduced.
Administrative Controls are often used with other measures, such as Engineering Controls and Personal Protective Equipment (PPE), to provide additional protection against chemical hazards. They are effective in reducing exposure to hazards and can be relatively inexpensive to implement compared to other control measures.
However, it is important to note that Administrative Controls rely on worker compliance and may not be as reliable as other control measures, such as Engineering Controls. They should be used with other control measures to provide comprehensive protection against chemical hazards. Employers should regularly review and update their Administrative Controls to ensure that they remain effective and relevant to the hazards in their workplace.
4. Personal Protective Equipment (PPE)
Personal Protective Equipment (PPE) is the fourth level of the Hierarchy of Control, and it involves providing workers with equipment to protect them from chemical hazards. PPE is used when the first three levels of control (Elimination/Substitution, Engineering Controls, and Administrative Controls) are not feasible or effective in controlling the hazard.
Examples of PPE include:
- Gloves: Gloves protect the hands and arms from chemical exposure. Different types of gloves are available depending on the chemical being used, and it is important to select gloves appropriate for the specific chemical hazard.
- Respirators: Respirators are used to protect the lungs from inhaling hazardous chemicals. Different types of respirators are available depending on the chemical used and the protection level required.
- Protective clothing: Protective clothing, such as lab coats or coveralls, can protect workers’ skin and clothing from chemical exposure.
- Eye and face protection: Eye and face protection, such as goggles or face shields, can protect workers’ eyes and face from chemical splashes or vapours.
PPE is effective in reducing exposure to chemical hazards. Still, it should be considered a last resort because it relies on worker compliance and may not be as effective as the previous levels of control. Workers must be trained on properly using and maintaining PPE, and employers must ensure that the PPE fits properly and is appropriate for the specific hazard.
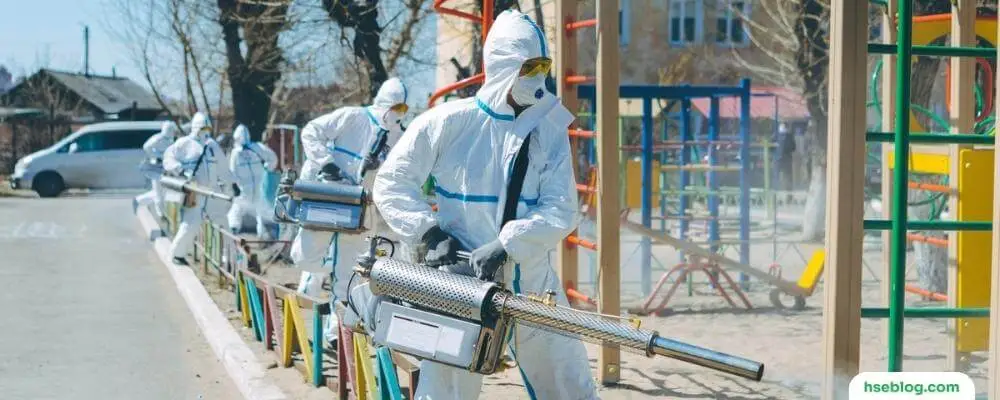
It is also important to note that PPE only protects the individual worker and does not control the hazard at the source. Therefore, PPE should be used with other control measures to protect against chemical hazards comprehensively.
Employers should regularly review and update their PPE program to ensure that it remains effective and relevant to the hazards in their workplace. By implementing effective PPE, employers can create a safer workplace and protect workers from the harmful effects of chemical hazards.
5. Emergency Preparedness
Emergency Preparedness is the fifth and final level of the Hierarchy of Control, and it involves preparing for and responding to chemical hazards in emergency situations. This level of control is critical because even with the best control measures in place, there is still a risk of an unexpected release of hazardous chemicals. Therefore, it is important to have emergency preparedness measures in place to minimize harm in these situations.
Emergency Preparedness measures can include a variety of strategies and procedures, including:
- Evacuation plans: These plans ensure that workers can safely and quickly evacuate the facility in a chemical emergency. This may include designating evacuation routes and exits, training workers on the evacuation procedures, and conducting regular drills to ensure workers are familiar with the procedures.
- Emergency response teams: These teams are made up of trained individuals responsible for responding to chemical emergencies. The team may include individuals with specialized training in handling hazardous chemicals and first responders trained in providing medical assistance.
- Communication protocols: Effective communication is critical in a chemical emergency. Communication protocols may include alarms, sirens, or other signalling devices to alert workers of the emergency and established procedures for notifying emergency responders and communicating with workers.
- First aid: It is important to have basic first aid supplies and trained personnel on hand in case of injury due to a chemical hazard. Workers should be trained in basic first aid techniques, and kits should be available in the workplace.
Emergency Preparedness measures are critical to minimizing harm during a chemical emergency. Employers should regularly review and update their Emergency Preparedness plans to ensure that they remain effective and relevant to the hazards in their workplace. Employers can create a safer workplace and minimize harm in a chemical emergency by implementing effective Emergency Preparedness measures.
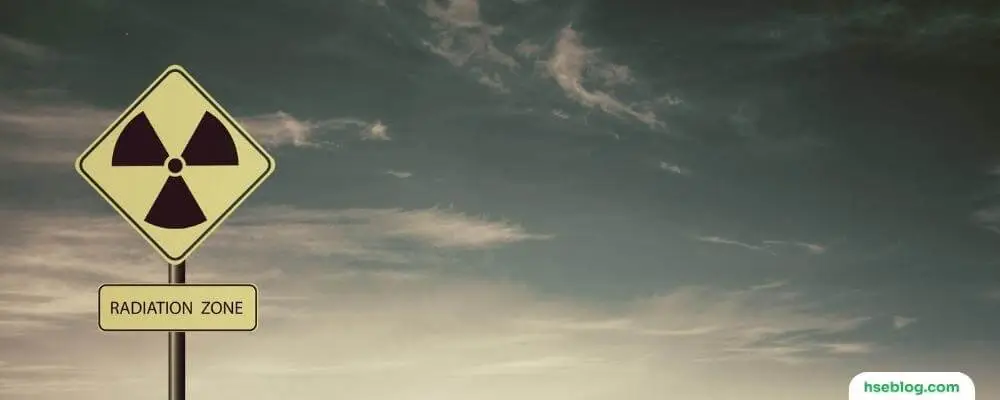
Conclusion
Implementing measures to control chemical hazards is crucial for protecting workers from harm and creating a safe workplace environment. Taking a comprehensive and integrated approach to control chemical hazards is important, using the Hierarchy of Control as a guide. This approach emphasizes eliminating or substituting hazardous chemicals before relying on less effective control measures, such as engineering controls, administrative controls, personal protective equipment, and emergency preparedness measures.
By implementing effective control measures and regularly reviewing and updating them, employers can create a safer workplace and protect workers from the harmful effects of chemical hazards. It is also important to provide workers with the necessary training and equipment to work safely with hazardous chemicals and to ensure that emergency preparedness measures are in place in the event of an unexpected release of hazardous chemicals.
In summary, the Hierarchy of Control provides a framework for implementing comprehensive and effective measures to control chemical hazards in the workplace. By following this framework and prioritizing the most effective control measures, employers can create a safer workplace and protect workers from the harmful effects of chemical hazards.