Machinery is an important part of any business. It helps to automate tasks and increase efficiency. However, it can also be dangerous if proper safety precautions are not taken. That’s why it’s important to have machine guards in place to protect workers from potential injuries. This blog post will discuss the different types of machine guards and how they can help keep your employees safe!
What is Machine Guarding?
Machine guarding is the installation of physical barriers and safety devices to protect workers from injuries caused by exposure to moving parts on machinery. Machine guarding can also protect against other hazards, such as flying debris or toxic chemicals.
Moving machine parts can cause severe workplace injuries, such as crushed fingers or hands, amputations, burns, or blindness. Safeguards are essential for protecting workers from these preventable injuries. Any machine part, function, or process that may cause injury must be safeguarded. When a machine or accidental contact operation injures the operator or others nearby, the hazards must be eliminated or controlled.
Various machine-guarding products are available on the market, including barrier guards, safety light curtains, safety switches, and emergency stop buttons. The type of product selected will depend on the specific hazards present in the work environment.
Each piece of machinery has its own unique mechanical and non-mechanical hazards. Machine guarding provides a means to protect humans from injury while working nearby or while operating equipment. It is often the first line of defence to protect operators from injury while working on or around industrial machinery during normal operation.
Benefits of Machine Guarding
Implementing machine guarding offers multiple safety, operational, and legal advantages. Here are the key benefits:
- Protects Workers from Injury: Machine guards act as a physical barrier between workers and moving parts, preventing serious injuries like amputations, lacerations, burns, and even fatalities.
- Enhances Workplace Safety Culture: Visible safety measures demonstrate a company’s commitment to employee well-being, promoting a proactive and responsible safety culture.
- Reduces Downtime and Costs: Fewer accidents mean fewer disruptions, lower medical costs, and reduced workers’ compensation claims, which directly impact operational efficiency and profitability.
- Ensures Regulatory Compliance: Machine guarding helps companies comply with safety regulations such as OSHA, PUWER, and ISO standards, avoiding legal penalties and inspections-related delays.
- Boosts Employee Confidence and Morale: Workers are more confident and productive when they feel safe, leading to increased morale, lower turnover, and higher job satisfaction.
- Protects Against Mechanical Failures: Guards not only protect people but also prevent foreign objects or debris from damaging the machine, thereby extending equipment life and performance.
- Simplifies Training and Supervision: Clear, visible safeguards make it easier to train new employees on safe work practices and ensure consistent enforcement by supervisors.
Types Of Machine Guards
Several types of machine guards can be used to protect workers from injuries. Some of the most common types of machine guards include:
1. Fixed Guards
A fixed guard is a physical barrier that prevents a person from coming into contact with dangerous moving parts. The guard may be shaped to fit the machine quite closely (enclosing guard) or more like a fence around the machine (perimeter guard). It may have openings (e.g., to allow raw material to be fed into a machine), but these must be designed so that it is impossible to reach in and contact dangerous parts (distance guard).
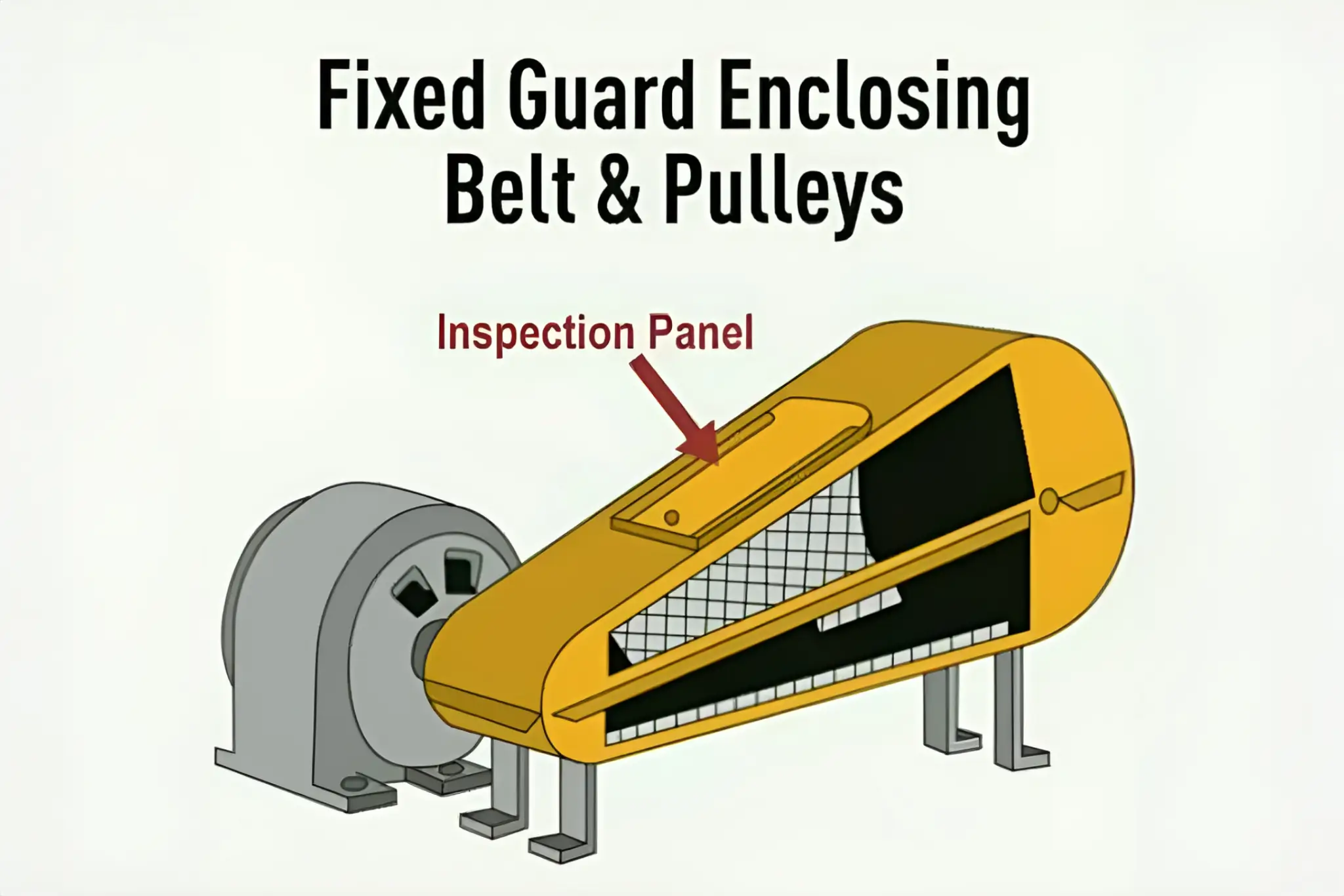
A fixed guard has no moving parts and should, by its design, prevent access to the dangerous parts of the machinery. It must be of robust construction and sufficient to withstand the stresses of the process and environmental conditions. If visibility or free airflow (e.g., for cooling) is necessary, this must be allowed for in the design and construction of the guard. If the guard can be opened or removed, this must only be possible with the aid of a tool.
An alternative fixed guard is the distance fixed guard, which does not completely enclose a hazard but reduces access by its dimensions and distance from the hazard. Where perimeter fence guards are used, the guard must follow the contours of the machinery as far as possible, thus minimizing the space between the guard and the machinery. With this type of guard, the safety devices and operating systems must prevent the machinery from being operated with the guards closed and someone inside the guard in the danger area.
Both fixed guards must be firmly attached to the machine so they cannot be removed easily. They should also be designed to not present a new hazard (e.g., by entrapment) and can be cleaned easily.
The main disadvantage of a fixed guard is that it does not always properly prevent access. It is often left off by maintenance staff and can create difficulties in the operation of the machine. Another disadvantage is that they are not always visible, which can make people unaware of the hazard.
It is important to note that a fixed guard will not be effective if it does not cover the entire hazard. It is also important to ensure that the guard is made of a material that cannot be easily breached. Finally, the guard must be firmly attached to the machine so that unauthorised personnel cannot easily remove it.
2. Adjustable Guards
Adjustable and self-adjusting guards are used when it is impossible to completely prevent access to dangerous parts. They are commonly used to safeguard woodworking and metalworking machinery, where a workpiece must be fed into or manipulated during machine use.
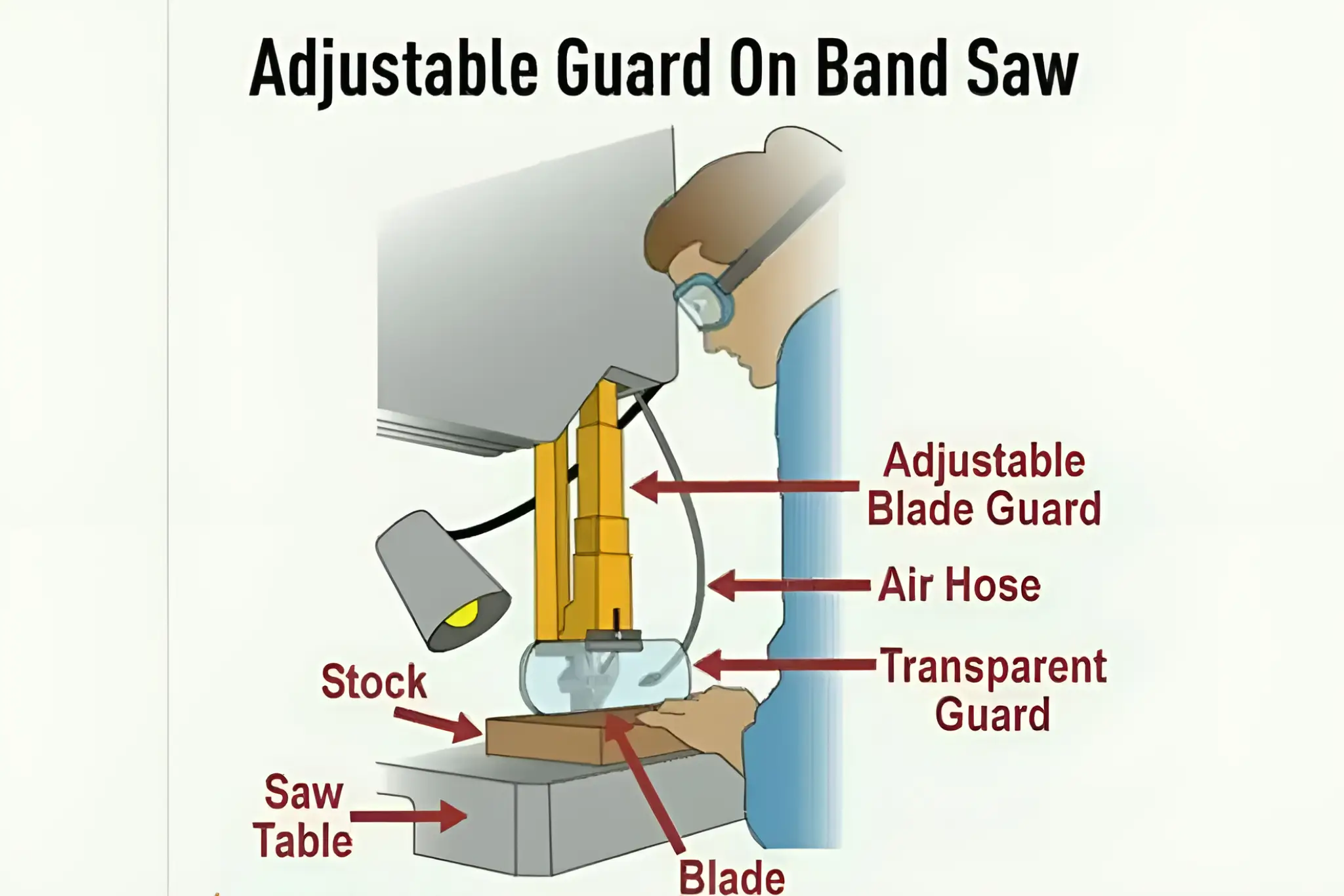
User Adjusted Guard
These are fixed or movable guards, which are adjustable for a particular operation during which they remain fixed. They are particularly used with machine tools where some access to the dangerous part is required (e.g., drills, circular saws, milling machines; and where the clearance required will vary (e.g., with the size of the cutter in use on a horizontal milling machine or with the size of the timber being sawn on a circular saw bench).
Adjustable guards may be the only option with cutting tools, which are otherwise very difficult to guard, but they have the disadvantage of requiring frequent readjustment. By the nature of the machines on which they are most frequently used, there will still be some access to the dangerous parts, so these machines must only be used by suitably trained operators. Jigs, push sticks, and false tables must be used to minimize hazards while feeding the workpiece. The working area should be well-lit and free of anything that might cause the operator to slip or trip.
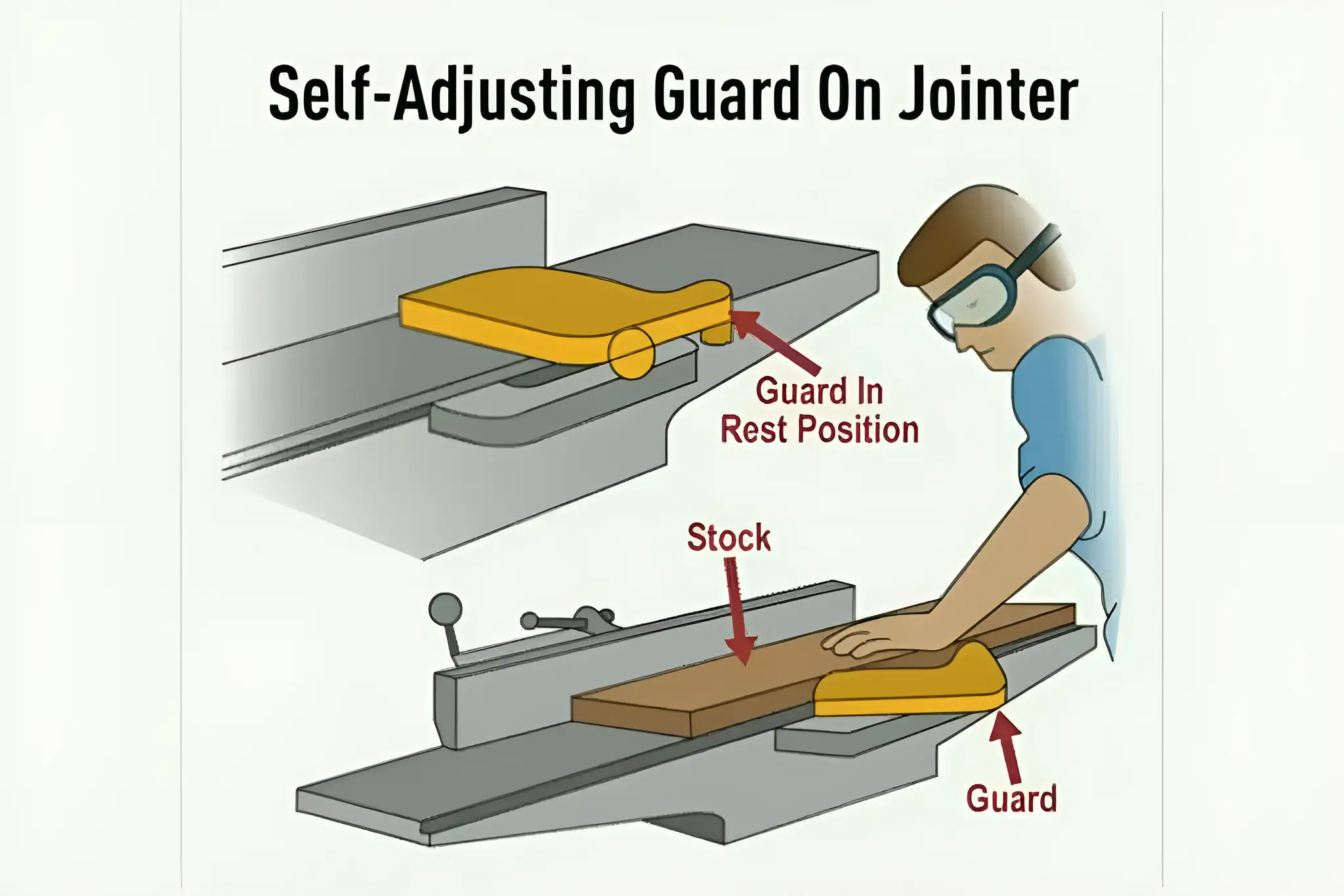
Self Adjusting Guard
A self-adjusting guard adjusts itself to accommodate, for example, the passage of material. A good example is a spring-loaded guard fitted to many portable circular saws.
As with adjustable guards, they only provide a partial solution in that they may still allow access to the dangerous part of the machinery. They require careful maintenance to ensure they work to the best advantage. It is important to remember that both adjustable and self-adjusting guards rely on the operator for their effectiveness. They should not be considered a perfect solution to the problem of access to dangerous machinery parts.
Operators must be properly trained in their use and, where necessary, authorized by their employer. Adjustable and self-adjusting guards should be regularly inspected and, where necessary, adjusted or repaired. Where possible, jigs, push sticks, and false tables should be used to minimize hazards while feeding the workpiece. The working area should be well-lit and free of anything that might cause the operator to slip or trip.
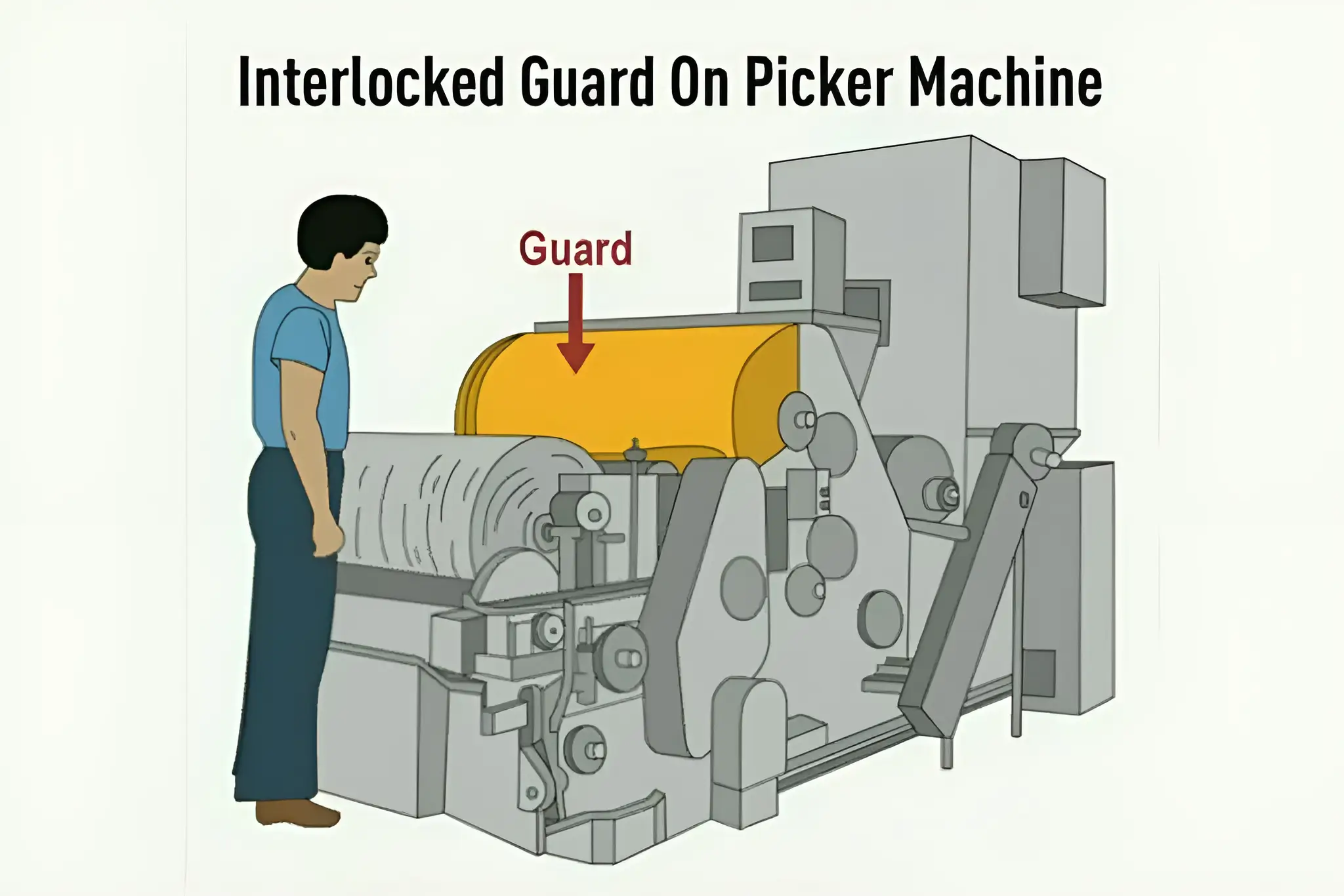
3. Interlocked Guards
An interlocked guard is designed to be removed or opened as a normal part of routine machine operation. When the guard is removed, a safety interlock system prevents machine operation. For example, a microwave oven has a hinged door on the front to allow easy access; this door is interlocked so that power to the microwave generator is shut off when it is open.
The basic principles of an interlocked guard are:
- Power to the machine is disabled, and the machine will not operate until the guard is in place.
- Either the guard is locked shut until it is safe to open, or opening the guard stops the dangerous parts and disables power.
The advantages of interlocked guards are that they allow safe access to operate and maintain the machine without dismantling the safety devices. Their disadvantage stems from the constant need to ensure that they are operating correctly and designed to be failsafe. Maintenance and inspection procedures must be very strict.
This is a movable guard (or which has a movable part) whose movement is connected to the power or control system of the machine.
An interlocking guard must be connected to the machine controls such that:
- Until the guard is closed, the interlock prevents the machinery from operating by interrupting the power medium;
- Either the guard remains locked until the risk of injury from the hazard has passed, or opening the guard causes the hazard to be eliminated before access is possible.
A passenger lift or hoist is a good illustration of these principles: the lift will not move unless the doors are closed, and the doors remain locked until the lift is stationary and in such a position that it is safe to open.
Special care is needed with systems that have stored energy. This might be the momentum of a heavy moving part, stored pressure in a hydraulic or pneumatic system, or even the simple fact of a part being able to move under gravity even though the power is disconnected. In these situations, dangerous movement may continue or be possible with the guard open, and these factors need to be considered in the overall design.
Braking devices (to arrest movement when the guard is opened) or delay devices (to prevent the guard from opening until the machinery is safe) may be needed. All interlocking systems must be designed to minimize failure-to-danger risk and should not be easy to defeat.
An interlocked guard should:
- be made of a material that cannot be easily breached or removed;
- be firmly attached to the machine;
- have smooth edges to prevent clothing from being snagged;
- be as large as possible while still allowing access to the hazard;
- if it is necessary to reach past the guard to operate the controls, these should be recessed or located on the side away from the hazard;
- be designed so that it cannot be left in an unsafe position; and
- have a positive locking device to prevent it from being opened accidentally.
In summary, an interlocked guard is a movable barrier connected to a machine’s power or control system so that the machine cannot operate unless the guard is in place. Interlocked guards are used to protect people from hazards that could cause serious injury, so they must be designed carefully to ensure that they are fit for their purpose.
4. Light Curtains and Screens
A light curtain or screen is a device that emits a series of infrared or laser beams across the access point of a machine. If beams are interrupted (for instance, by a worker’s hand), the machine’s power or control system is interrupted, instantly stopping operation.
Light curtains and screens are especially useful in applications where frequent access is needed, and hard guarding would hinder productivity. They can also cover large areas and irregular shapes, where physical guards may not be practical. Common applications for light curtains are automated assembly lines and robotic work cells.
However, they require careful positioning to prevent reaching or walking under the beams without detection. They also require a safe machine stop time, as a hand or other object can move quickly through the beams and potentially contact the hazard before the machine stops.
5. Safety Mats, Edges, and Bumpers
Safety mats, edges, and bumpers are devices that sense the presence of people or objects. A safety mat is a floor mat which senses the weight of a person standing on it and will deactivate the machine. Safety edges and bumpers are used to guard hazards and are typically found on machine doors or barriers. The machine will be deactivated if pressure is applied to the safety edge or bumper (for example, if a person were to become trapped).
These devices are good for areas with heavy pedestrian traffic, where light curtains may not be feasible due to space restrictions or the risk of accidental machine stoppage. However, like light curtains, they depend on safe machine stop times.
6. Two-Hand Controls and Trips
Two-hand controls require the operator to use both hands to operate the machine, ensuring that the operator’s hands are not near the hazard when the machine cycles. These are often used on machines such as press brakes or punches.
Two-hand trips are similar but require the operator to simultaneously activate the machine using two separate controls. This can help ensure the operator’s hands are away from the danger area when the machine cycles. However, these controls do not protect other people in the hazard area and are unsuitable for all machines.
In conclusion, many types of machine guards are available to protect workers from hazards. The best type of guard will depend on the specific machine, the operation being performed, and the potential hazards. Remember, no matter what type of guard is used, it must be maintained properly to ensure it continues to provide protection. Workers should be trained to understand the purpose and function of guards and should be involved in the selection, installation, and review of guarding systems. Safety should always be a top priority in every workplace.
Conclusion
Machine guarding is a vital component of workplace safety, especially in environments where machinery poses a risk of serious injury. By implementing the appropriate type of guard—whether fixed, adjustable, interlocked, or sensor-based—businesses can significantly reduce the risk of accidents and ensure compliance with safety regulations. Beyond physical protection, effective machine guarding promotes a safety-first culture, boosts worker confidence, and enhances overall operational efficiency.
Ultimately, the goal of machine guarding is not just to comply with standards but to proactively safeguard human life. Every employer must prioritize regular inspection, maintenance, and training to ensure that machine guards function effectively and remain in place. With the right systems and mindset, machine guarding can help create a safer, more productive workplace for everyone.