The most important step in managing risks involves eliminating them so far as is reasonably practicable, or if that is not possible, minimizing the risks so far as is reasonably practicable. In deciding how to control risks, you must consult your workers and their representatives, who will be directly affected by this decision. Their experience will help you choose appropriate control measures, and their involvement will increase the acceptance of any changes that may be needed to the way they do their job.
There are many ways to control risks. Some control measures are more effective than others. You must consider various control options and choose the control that most effectively eliminates the hazard or minimizes the risk. This may involve a single control measure or a combination of different controls that provide the highest level of reasonably practicable protection.
Some problems can be fixed quickly and immediately, while others need more effort and planning. Of those requiring more effort, you should prioritize areas for action, focusing first on those hazards with the highest level of risk.
The Hierarchy Of Risk Control
The Hierarchy of Risk Control is a framework used to prioritize and implement measures to control or mitigate risks in various industries and workplace settings. It outlines a sequence of steps organizations can take to minimize or eliminate hazards and reduce the risk of accidents or injuries. The five steps in the Hierarchy of Risk Control, in order of priority, are:
You must always aim to eliminate a hazard, which is the most effective control. If this is not reasonably practicable, you must minimize the risk by working through the other alternatives in the hierarchy.
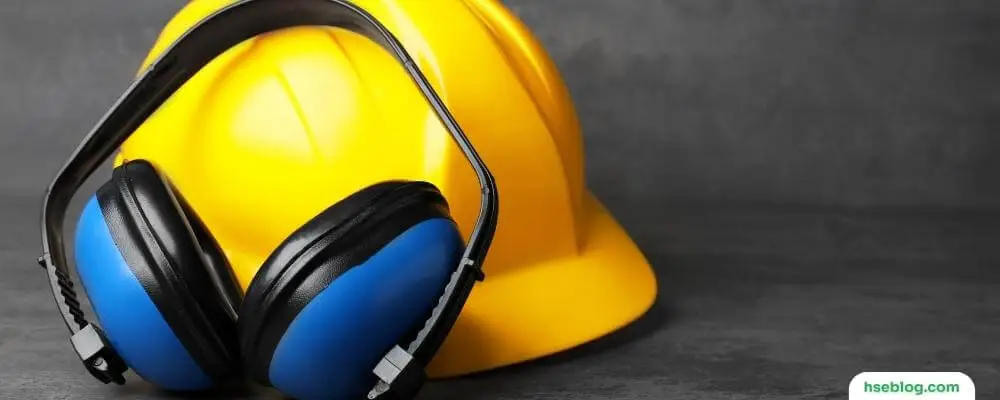
Level 1 Control Measures
The most effective control measure involves eliminating the hazard and associated risk. The best way to do this is by not introducing the hazard into the workplace. For example, you can eliminate the risk of a fall from a height by doing ground-level work.
Eliminating hazards is often cheaper and more practical at the design or planning stage of a product, process, or place used for work. In these early phases, there is greater scope to design hazards or incorporate risk control measures compatible with the original design and functional requirements. For example, a noisy machine could be designed and built to produce as little noise as possible, which is more effective than providing workers with personal hearing protectors.
You can also eliminate risks by obliterating the hazard, such as removing trip hazards on the floor or disposing of unwanted chemicals. It may not be possible to eliminate a hazard if doing so means that you cannot make the end product or deliver the service. If you cannot eliminate the hazard, eliminate as many of the risks associated with the hazard as possible.
Level 2 Control Measures
If it is not reasonably practicable to eliminate the hazards and associated risks, you should minimize the risks using one or more of the following approaches:
Substitute the hazard with something safer
Substituting a hazard with something safer is a key principle in the Hierarchy of Risk Control. It involves identifying a hazardous substance, equipment, or process and replacing it with a safer alternative that does not pose the same level of risk.
- For example, if a company uses a hazardous chemical in its manufacturing process, it may consider substituting it with a less hazardous chemical or a non-hazardous alternative. This could reduce the risk of exposure to the chemical and minimize the potential for accidents or health problems.
- Another example is replacing manual labor with automated equipment in a dangerous work environment. For instance, if workers are required to manually lift heavy objects, the company could invest in machinery that can perform the task without human involvement, reducing the risk of back injuries.
Substituting hazards with something safer can be challenging, as finding suitable alternatives often requires significant investment, research, and development. However, it is considered the most effective method of hazard control because it eliminates the risk entirely, rather than simply reducing or managing it.
Isolate the hazard from people
isolating the hazard from people is an important control measure in the Hierarchy of Risk Control. This approach involves physically separating the source of harm from people by distance or using barriers. The goal is to prevent workers from coming into contact with the hazard and reduce the potential for accidents or injuries.
Examples of isolating the hazard from people include:
- Installing guardrails around exposed edges and holes in floors to prevent falls.
- Using remote control systems to operate machinery, so workers are not exposed to moving parts or hazardous materials.
- Storing chemicals in a fume cabinet to prevent exposure to toxic fumes or vapors.
- Constructing soundproof walls or enclosures to protect workers from excessive noise.
Organizations can minimize the risk of accidents and injuries by isolating the hazard, particularly in high-risk environments such as construction sites, manufacturing plants, and laboratories. However, it’s important to note that isolating the hazard is not always possible, and other control measures may be necessary to ensure worker safety.
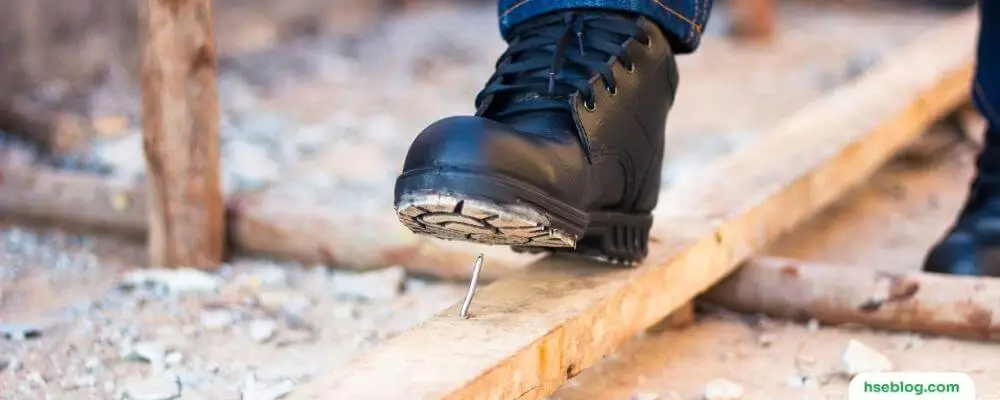
Use engineering controls
Using engineering controls is an important step in the Hierarchy of Risk Control. Engineering controls involve modifying the workplace environment, equipment, or processes to reduce the risk of harm to workers. These control measures are physical in nature and often include mechanical devices or processes.
Examples of engineering controls include:
- Using mechanical devices such as trolleys or hoists to move heavy loads reduces the risk of manual handling injuries.
- Placing guards around moving parts of machinery to prevent workers from coming into contact with them.
- Installing residual current devices (RCDs), also known as electrical safety switches, to protect workers from electric shock.
- Setting work rates on a production line reduces fatigue and prevents repetitive motion injuries.
Engineering controls are often preferred over administrative or personal protective equipment because they provide more reliable and consistent protection. They also tend to be less reliant on individual behavior or compliance, which can be difficult to maintain in fast-paced or high-stress work environments.
However, engineering controls can be expensive and require significant equipment or facility modifications. Therefore, organizations may need to weigh the costs and benefits of different control measures to determine the most effective approach for managing workplace risks.
Level 3 Control Measures
These control measures do not control the hazard at the source. They rely on human behavior and supervision and, used on their own, tend to be least effective in minimizing risks. Two approaches to reducing risk in this way are:
Use administrative controls
Administrative controls are a type of risk management strategy that focuses on reducing the risk of exposure to hazards in the workplace through the implementation of work procedures, policies, and practices. These controls rely on human behavior and actions to minimize the risks associated with workplace hazards.
Examples of administrative controls include:
- Developing procedures for operating machinery safely: This may include guidelines for proper use, regular maintenance, and inspection of the equipment, as well as training and certification requirements for operators.
- Limiting exposure time to hazardous tasks: Employers may implement policies limiting workers’ exposure time to a particular hazard. For example, workers may be required to take breaks or rotate job tasks to minimize their exposure to a particular hazard.
- Using signs to warn people of a hazard: Employers can use signage to alert workers and visitors to the presence of a hazard, such as a wet floor, hazardous chemicals, or construction zones.
Overall, administrative controls can be an effective tool for managing workplace hazards. Still, they should be used with other risk management strategies, such as engineering controls and personal protective equipment (PPE), to provide comprehensive protection to workers.
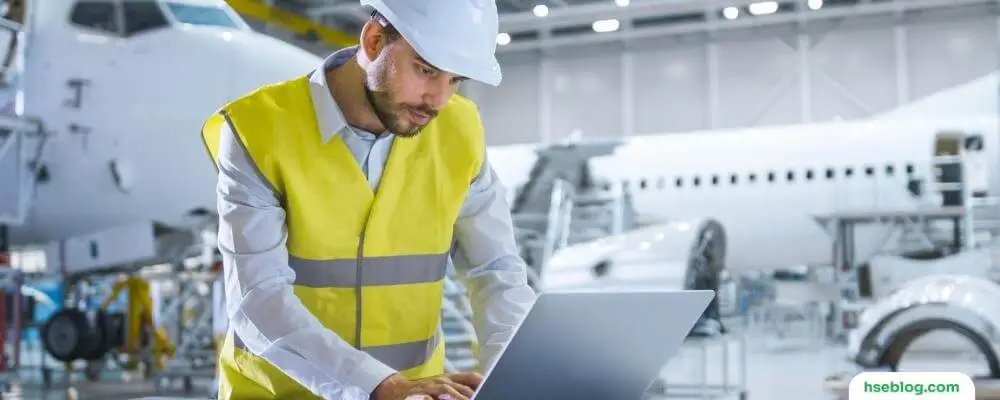
Use personal protective equipment (PPE)
Personal Protective Equipment (PPE) is a type of protective gear that is designed to minimize exposure to hazards that can cause injury or illness. It is an essential component of a comprehensive safety program in many industries, such as construction, manufacturing, healthcare, and agriculture.
PPE can include a range of items, such as:
- Hard hats: Designed to protect the head from impact and penetration hazards, such as falling objects or electrical hazards.
- Respirators: Used to filter out harmful particles, gases, or vapors from the air that workers breathe in, protecting the respiratory system.
- Gloves: Designed to protect the hands from cuts, burns, and other hazards that can cause injury.
- Safety glasses and goggles: Designed to protect the eyes from impact, dust, chemicals, and other hazards that can cause eye injury.
It is important to note that PPE is only effective if workers wear and use it correctly. Employers are responsible for providing appropriate PPE to their employees, training them on using it correctly, and ensuring that it is maintained and replaced as necessary. Workers are also responsible for wearing and using PPE as directed and reporting any problems or concerns with their PPE to their employer.
Administrative controls and PPE should only be used:
Administrative controls and PPE should not be considered the first defense against workplace hazards. Instead, they should only be used:
- As a last resort: Administrative controls and PPE should be used when all other practical control measures have been considered and found impractical or ineffective.
- As an interim measure: Administrative controls and PPE can be used as interim measures while higher-level control measures, such as engineering controls, are being developed and implemented.
- To supplement higher-level control measures: Administrative controls and PPE should be used with other control measures to provide comprehensive protection to workers. They should not be relied upon as the sole means of protecting workers from hazards.
Employers are legally responsible for assessing workplace hazards and implementing appropriate control measures to protect their workers. The hierarchy of controls should be followed, starting with eliminating the hazard if possible, then implementing engineering controls, administrative controls, and finally, using PPE as a last resort.
How to Develop and Implement Control Options
Information about suitable controls for many common hazards and risks can be obtained from the following:
- Codes of practice and guidance material
- Manufacturers and suppliers of plant, substances, and equipment used in your workplace
- Industry associations and
In some cases, published information will guide the whole work process. In other cases, the guidance may relate to using specific substances safely to individual plant items. You may use the recommended control options if they suit your situation and eliminate or minimize the risk.
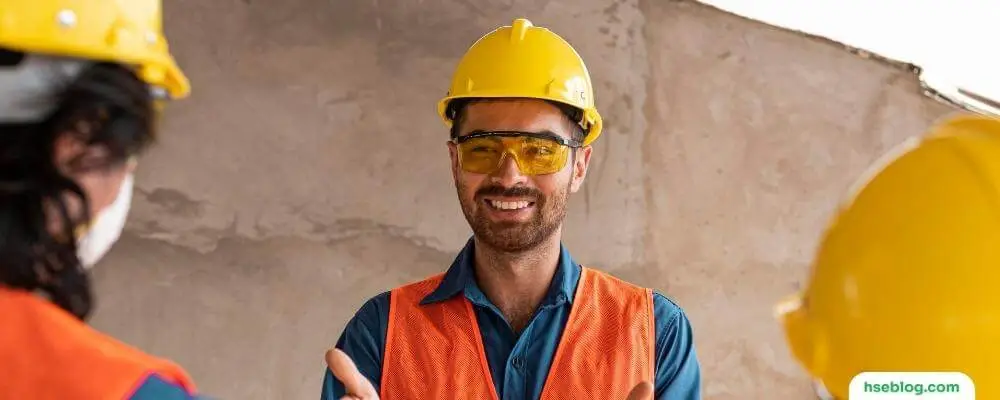
Developing Specific Control Measures
You may need to develop specific control measures if the information is irrelevant to your workplace’s hazards, risks, or circumstances. This can be done by referring to the events recorded during the risk assessment.
For each event in the sequence, ask: “What can be done to stop or change the event?”
Working through the events in the sequence will give you ideas about all possible ways to eliminate or minimize the risk. There may be more than one solution for each of the events. The control option you choose should be:
- One that provides the highest level of protection for people and is the most reliable – that is, controls located toward the top of the hierarchy
- Available – that is, it can be purchased, made to suit, or be put in Suitable for the circumstance in your
- Workplace – that is, it will work appropriately given the workplace conditions and work process, and where the hazard or risk has the potential to cause death, severe injury, or illness, more emphasis should be given to those controls that eliminate or reduce the level of harm, than those that reduce the likelihood of harm occurring.
Make sure that your chosen solution does not introduce new hazards.
Cost Of Control Measures
All risks can be controlled, and it is always possible to do something, such as stopping the activity or providing instructions to those exposed. There will normally be several different options between these two extremes. Cost (time, effort, and money) is one factor to consider when determining the best control option. The cost of controlling a risk may be considered in determining what is reasonably practicable but cannot be used as a reason for doing nothing.
The greater the likelihood of a hazard occurring and/or the greater the harm that would result if the hazard or risk did occur, the less weight should be given to the cost of controlling the hazard or risk. If two control measures provide the same levels of protection and are equally reliable, you can adopt the least expensive option.
Cost cannot be used as a reason for adopting controls that rely exclusively on changing people’s behavior or actions when more effective controls are available that can change the risk through substitution, engineering, or isolation.
Implementing Controls
The control measures you implement will usually require changes to how work is carried out due to new or modified equipment or processes, new or different chemicals, or new personal protective equipment. In these situations, it is usually necessary to support the control measures with the following:
1. Work procedures
Develop a safe work procedure that describes the task, identifies the hazards, and documents how the task will be performed to minimize the risks.
2. Training, instruction, and information
Train your workers in the work procedure to ensure they can perform the task safely. Training should require workers to demonstrate competence in performing the task according to the procedure. It is insufficient to simply give a worker the procedure and ask them to acknowledge that they understand and can perform it. Training, instruction, and information must be provided in a form that can be understood by all workers.
Information and instruction may also need to be provided to others who enter the workplace, such as customers or visitors.
3. Supervision
The level of supervision required will depend on the level of risk and the experience of the workers involved. High levels of supervision are necessary where inexperienced workers are expected to follow new procedures or carry out complex and critical tasks.
You may prepare a risk register that identifies the hazards, what action needs to be taken, who will be responsible for taking action, and when.
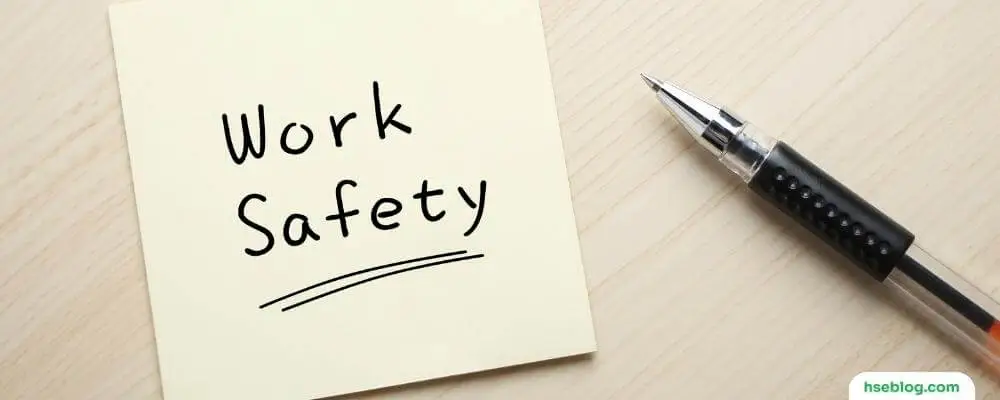
How to ensure that controls remain effective
The following actions may help you monitor the control measures you have implemented and ensure that they remain effective:
- Accountability for health and safety – Accountability should be clearly allocated to ensure procedures are followed and maintained. Managers and supervisors should have the authority and resources to implement and maintain control measures.
- Maintenance of plant and equipment will involve regular inspection and testing, repair, or replacement of damaged or worn plant and equipment. It includes checking that any control measures are suitable for the nature and duration of work set up and used.
- Up-to-date training and competency – Control measures, notably lower-level controls, depend on all workers and supervisors having the appropriate competencies to do the job Training should be provided to maintain competencies and ensure new workers are capable of working safely.
- Up-to-date hazard information – Information about hazards, such as plants and substances, may be updated by manufacturers and suppliers and should be checked to ensure controls are still relevant. New technology may provide more effective solutions than were previously available. Changes to operating conditions or the way activities are carried out may also mean that control measures need to be
- Regular review and consultation – Control measures are more effective where there is a regular review of work procedures and consultation with your workers and their representatives.
Conclusion
Controlling risk is crucial in preventing accidents and injuries in any environment. The hierarchy of risk control provides a structured approach to identifying and prioritizing risk controls based on their effectiveness. The five levels of the hierarchy, from most effective to least effective, are elimination, substitution, engineering controls, administrative controls, and personal protective equipment.
Elimination and substitution are the most effective ways to control risk, as they eliminate or substitute the hazard with a less hazardous one. However, if elimination or substitution is not possible, engineering controls should be implemented to isolate people from the hazard. Administrative controls can change how people work, while personal protective equipment should be used as a last resort.
It is essential to note that the hierarchy of risk control is not a one-time process, and it should be continually reviewed and updated to ensure its effectiveness. By following the hierarchy of risk control, organizations can reduce the risk of accidents and injuries, improve the safety and health of their employees, and create a safer work environment.