In the rapidly evolving landscape of technological advancements, ensuring safety remains paramount, especially regarding electrical appliances we frequently use. Whether it’s a coffee machine in an office or a power tool on a construction site, the importance of their safe operation cannot be overstated. Enter the realm of Portable Appliance Testing, more commonly known by its abbreviation – PAT Testing. This procedure, although straightforward in its execution, plays a vital role in ensuring the safety and functionality of electrical appliances, big and small.
In this comprehensive guide, we’ll delve into the intricacies of PAT testing – from its very definition to its significance, the various types, and the legal framework surrounding it. We’ll also shed light on the recommended frequency of these tests, the individuals responsible for conducting them in the workplace, and the significance of PAT test certificates.
Moreover, we’ll guide you through the meticulous steps involved in the testing process and address the critical question: Is maintaining a record of all your PAT tests essential? Strap in, for you’re about to journey through the essential world of ensuring electrical safety in our day-to-day environments.
What is Portable Appliance Testing (PAT Testing)
Portable Appliance Testing (PAT Testing) is a process used to examine electrical appliances and equipment to ensure they are safe for use. It involves a visual inspection of equipment and any associated cables and plugs and a series of electrical tests. The primary aim of PAT Testing is to prevent electrical accidents in the workplace and other environments, ensuring that appliances adhere to relevant safety standards.
While the term suggests it’s strictly for “portable” devices, PAT Testing encompasses a wide range of equipment, from larger industrial machines to everyday office or household items like computers, microwaves, and extension cords. Regular PAT Testing is crucial for businesses and organizations to comply with safety regulations, ensuring that all electrical equipment remains in safe operating condition and reducing the risk of electrical-related accidents.
Purpose Of Portable Appliance Testing (PAT Testing)
The primary purpose of Portable Appliance Testing (PAT Testing) is to ensure the safety of electrical appliances and equipment, thereby preventing electrical accidents and hazards. By systematically inspecting and testing electrical devices, PAT Testing identifies potential issues that could lead to electric shocks, burns, or even fires. These examinations are vital in the following ways:
- Protecting Users and Bystanders: Regular testing ensures that employees, customers, residents, or anyone exposed to electrical appliances remain safe, reducing the risks associated with faulty equipment.
- Compliance with Legal Obligations: For businesses and organizations, PAT Testing is part of their obligation to adhere to health and safety regulations. Regular testing and maintaining records show due diligence in ensuring a safe environment, potentially shielding entities from legal repercussions in the event of an accident.
- Maintaining Equipment Integrity: Through PAT Testing, minor faults can be detected early, allowing for timely repairs or replacements. This not only ensures safety but can also prolong the lifespan of the equipment and reduce long-term costs.
- Risk Management: By identifying and addressing potential hazards, businesses can manage and mitigate risks associated with electrical failures, which might lead to business interruptions, damage to reputation, or financial liabilities.
In essence, the core purpose of PAT Testing is to create and maintain a safe environment by ensuring that electrical equipment is in a safe operating condition.
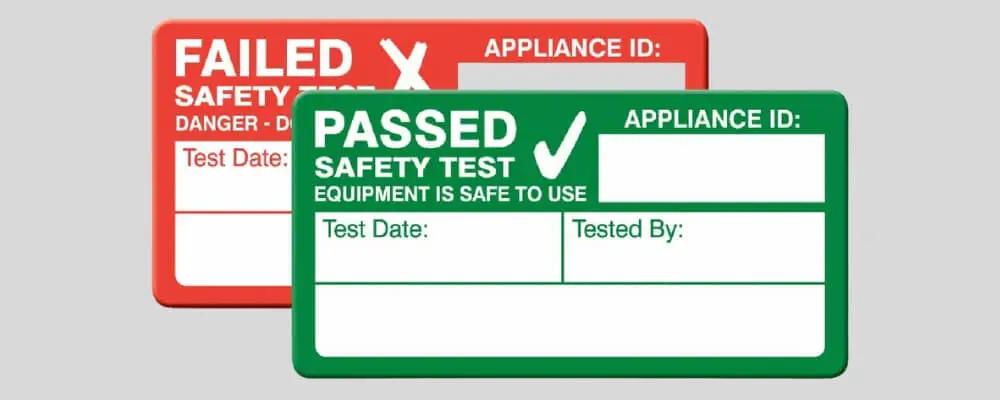
Different Types Of PAT Testing
Portable Appliance Testing (PAT Testing) involves several tests to ascertain the safety of electrical appliances. Various tests can be performed depending on the type of equipment, its usage, and its environment. Here are some of the most common types of PAT testing:
1. Visual Inspection
The very first step in the Portable Appliance Testing (PAT) process is the visual inspection. It is often said that a significant percentage of potential issues can be identified through this inspection. The tester meticulously examines the appliance, focusing on its physical aspects.
They will look for damaged cables, which could expose the internal wires, bent pins in the plug, which might not make proper contact with the socket, or cracks in the casing, which could expose the internal components. The condition of the plug, the fuse, and the markings or labels on the appliance are also assessed during this phase.
2. Earth Continuity Test (also called Earth Bond Test)
An integral safety feature in electrical appliances is the connection between the appliance’s metal parts and the earth pin on its plug, ensuring any unintended currents have a safe path to the ground. The Earth Continuity Test verifies this connection. This test is crucial for Class I appliances, designed with an essential earth for safety.
A low resistance value during this test indicates a sound connection, ensuring that any fault current would quickly flow to earth, triggering safety measures like fuse blowouts or circuit breakers.
3. Insulation Resistance Test
As appliances age or face wear and tear, there’s a risk that the insulation separating live components from other parts might degrade. The Insulation Resistance Test is designed to ensure that this insulation remains effective.
By applying a high voltage (usually 500V DC) between the live parts and the earthed parts of the appliance and then measuring the resistance, this test can ascertain if any significant leakages might pose a shock risk.
4. Substitute Leakage Test (also called Alternative Leakage Test)
Some electrical appliances, especially more sophisticated or sensitive ones, might be at risk from the high voltages used in the Insulation Resistance Test. In such cases, the Substitute Leakage Test provides a safer alternative.
Instead of measuring insulation directly, this test gauges the actual leakage current from the live parts to the earth under operational conditions. The values obtained help in understanding the safety level of the appliance without subjecting it to potential damage.
5. Differential Leakage Test
Every electrical appliance has a current flow through its live and neutral wires. Ideally, the current entering the appliance should be the same as the current leaving it. The Differential Leakage Test measures this and identifies if there’s a discrepancy.
A significant difference could indicate a leakage in current, possibly because it’s flowing through an unintended path, posing a potential risk.

6. Functional Check
After the above electrical safety tests are conducted, verifying that the appliance still functions as intended is essential. The Functional Check is a basic operational test. It’s not an exhaustive performance test but a simple assurance that the device can power up and operate without immediate issues. This ensures the testing process hasn’t inadvertently affected the appliance’s primary function.
7. Touch Current Test
Imagine touching an appliance and getting a mild shock. The Touch Current Test measures the current that might pass through a user if they touch the appliance. This is especially vital for equipment where the leakage current might be higher but within defined limits. Ensuring this current is within safe parameters minimizes the risk of electric shock upon contact.
8. Load Test
The Load Test provides insights into the appliance’s operational efficiency. This test uses specialized testers to measure the power the appliance draws during its operation. If the appliance draws more or less current than expected, it could indicate underlying issues.
Testers can verify its functioning correctly and efficiently by ensuring the appliance consumes an expected amount of power.
9. RCD (Residual Current Device) Test
RCDs are protective devices designed to swiftly cut off the electricity supply if they detect leakage currents potentially harmful to someone using the appliance. The RCD Test ensures they are responsive and effective for equipment fitted with these devices.
By artificially introducing a fault, testers can confirm if the RCD trips within the correct time and at the right current level, ensuring user protection.
10. Flash Testing (also known as Dielectric Strength or High Potential ‘HiPot’ Testing)
While not a standard in routine PAT testing, Flash Testing is vital in specific scenarios. By applying an exceptionally high voltage between the appliance’s live parts and the earth, this test evaluates the insulation’s capacity to withstand over-voltages, which might arise due to surges or other reasons.
However, given the extreme conditions of this test, it’s reserved for particular situations and is not conducted on sensitive equipment due to the potential risk of damage.
Each test type’s specific purpose and relevance depends on the appliance and environment. Not all tests are applied to every appliance; the appropriate tests are selected based on a risk assessment and the nature of the equipment.
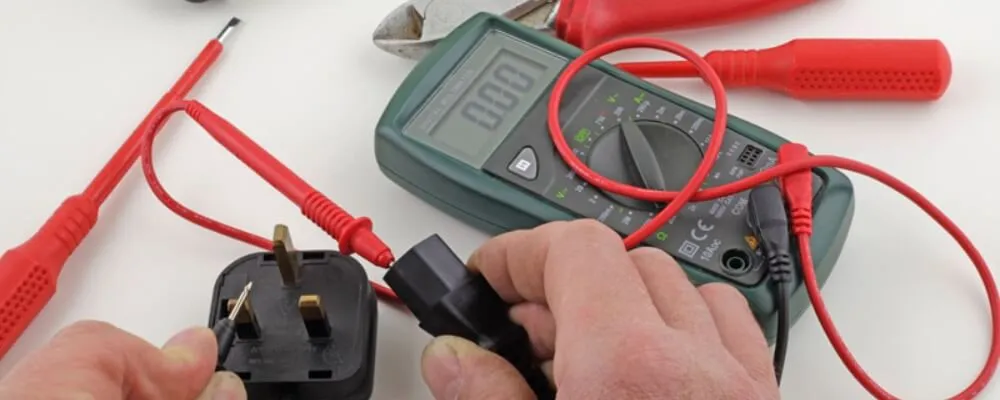
PAT Testing Steps
Portable Appliance Testing (PAT) is a systematic process to ensure that electrical appliances are safe. Here are the typical steps involved in PAT testing:
1. Preparation
Preparation is the foundational step for an effective PAT testing process. This involves accumulating all the essential tools and materials and ensuring the PAT tester is calibrated and in good working condition. Gathering labels is crucial as they communicate the test outcome to users and maintenance staff.
Record-keeping materials, usually in the form of logbooks or digital databases, are pivotal for documentation purposes. Additionally, notifying relevant staff ensures that the testing proceeds smoothly without hampering daily operations. Proper preparation streamlines the entire process and minimizes potential obstacles.
2. Visual Inspection
The initial visual inspection serves as the first defense against potential hazards. Even before diving into electronic evaluations, a cursory glance can reveal glaring issues. Frayed cables, cracked casings, or bent pins can be immediate red flags.
An incorrect fuse rating can jeopardize the appliance’s and its users’ safety. A secure attachment between the plug and the cable is paramount, ensuring no unintended disconnection or short-circuiting.
3. Earth Continuity Test (for Class I appliances)
For appliances that rely on an earth connection (Class I), the Earth Continuity Test is paramount. This assessment ensures that any unintended fault current will have a clear path to the ground, reducing the risk of electric shock.
Professionals use the PAT tester to ensure a robust connection between the plug’s earth pin and the appliance’s metal parts, bolstering safety measures.
4. Insulation Resistance Test
The insulation resistance test delves into the quality of insulation that stands between the live components and the earthed parts of an appliance. By applying a high voltage, typically around 500V DC, testers can determine if the insulation is up to standard.
If the resistance reading is lower than expected, it suggests that the insulation might be damaged or inadequate, thereby increasing the risk of electric shocks or short circuits.
5. Substitute Leakage Test
Some susceptible equipment may be at risk from the high voltages applied during insulation tests. The Substitute Leakage Test circumvents this risk by measuring any current that seeps from the live components to the earth under operational conditions. This indicates the device’s safety without exposing it to potentially damaging voltages.
6. Differential Leakage Test
The Differential Leakage Test provides insights into potential leakages within the appliance by measuring the current difference between the live and neutral conductors. If the difference is significant, it indicates that some current is escaping the intended circuitry, potentially leading to safety concerns or malfunctioning.
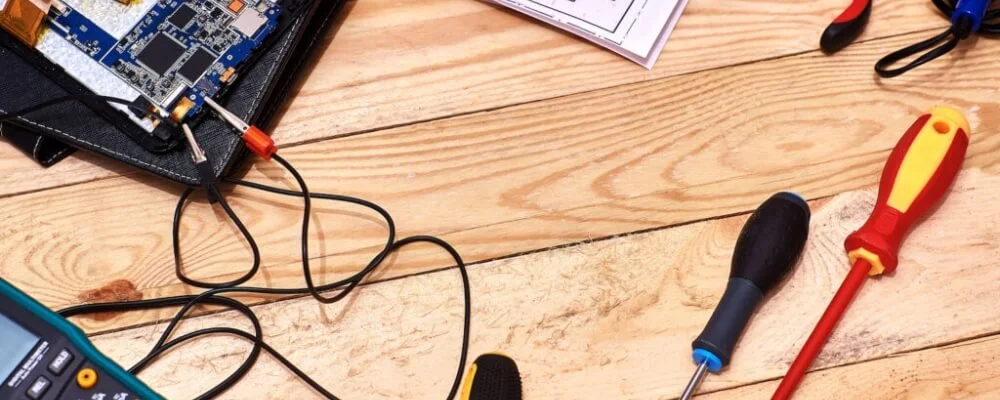
7. Functional Check
Beyond ensuring electrical safety, verifying that the appliance functions as expected is essential. The Functional Check does just that. After all electronic evaluations, the equipment is powered on to ascertain essential operational efficiency. This isn’t a deep dive into the appliance’s full functionality but a rudimentary assessment of its working condition.
8. Additional Tests (if applicable)
Not all appliances require the same set of tests. Supplementary tests such as Touch Current Test, Load Test, RCD Test, or Flash Testing might be warranted depending on the specific nature and environment of the appliance. These specialized tests cater to particular aspects of the device’s safety and functionality.
9. Labeling
Once testing is concluded, clear communication about the results is pivotal. Labels serve this purpose. They are affixed to the tested appliance, conveying vital information like test outcomes, testing dates, and the tester’s identity. This transparency ensures that users and maintenance personnel are always informed about the appliance’s safety status.
10. Record Keeping
Documentation is a crucial aspect of PAT testing. Maintaining records ensures compliance with regulatory standards and aids in future maintenance and troubleshooting. Every test, its result, subsequent actions, appliance details, and location are diligently recorded. This archival process ensures a historical record of the device’s maintenance and safety checks.
11. Reporting and Action
Transparency and prompt action are cornerstones of an effective PAT testing process. Post-testing, a comprehensive report is presented to the concerned personnel. Especially in cases where faults are detected, immediate action, be it repairs or replacements, is vital. Keeping stakeholders in the loop ensures everyone is aligned with the appliance’s safety status.
12. Planning for Retesting
Ensuring appliance safety isn’t a one-off task. Future PAT tests are scheduled based on the nature of the device, its operational environment, and the risk assessment. Regular testing at appropriate intervals guarantees the appliance meets safety standards throughout its lifecycle.
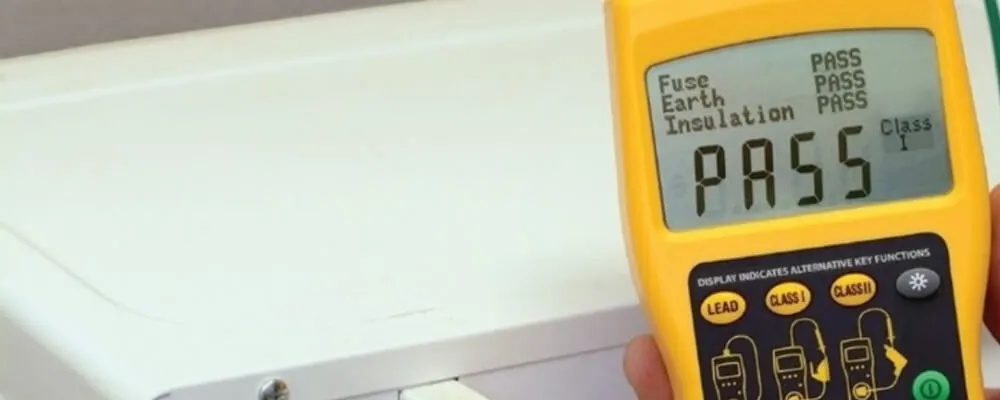
Frequency Of PAT Testing
The frequency of Portable Appliance Testing (PAT) is not universally fixed. It can depend on various factors, including the type of equipment, its use, and the environment in which it operates. Here’s a general guideline on how often different types of equipment should undergo PAT:
- Stationary Equipment or Appliances (e.g., fridges): These items tend to be tested less frequently since they are not moved often. Testing might be done every 12 to 24 months.
- IT Equipment (e.g., computers, printers): Given the relatively low risk posed by such devices, annual testing is typically sufficient for these items in an office setting.
- Moveable Equipment or Portable Appliances (e.g., electric drills, fans): Because these appliances are often moved around, they are more prone to wear and tear. Testing might be done every 6 to 12 months, depending on the usage.
- Hand-held Appliances (e.g., hairdryers, toasters): Due to the higher risk because of their constant handling, these might need testing every 6 to 12 months.
- Construction Site Equipment: Equipment used on construction sites is exposed to a very harsh environment, and thus, the Health and Safety Executive (HSE) in the UK, for instance, recommends that these be tested every three months.
- Equipment Used by the Public: Appliances used in public spaces, such as hotels or gyms, should be tested more frequently because of the high usage and potential risk. Depending on the nature of the appliance, testing might be required every 3 to 12 months.
- Hire Equipment: Items hired out should be tested every time they are returned to ensure they are safe for the next user.
- New Equipment: Newly acquired equipment should be tested before its first use to ensure it meets the necessary safety standards.
The above guidelines serve as general recommendations. The actual frequency of PAT testing should be determined by a risk assessment considering factors like the equipment’s age, its history of faults, the users, and the environment in which it’s used.
Some organizations may also have internal guidelines and policies on PAT testing frequency, which are tailored to their specific needs and the nature of their operations. Always check local regulations and guidelines when setting a testing schedule.
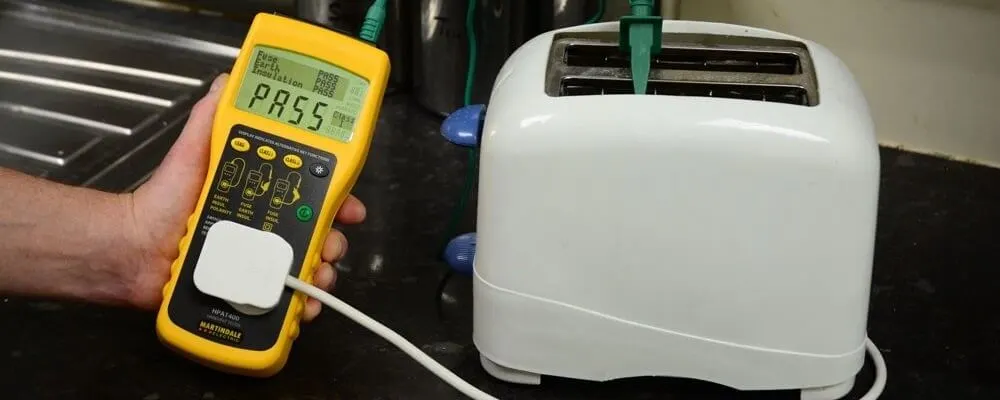
PAT Testing Legal Requirements
In many countries, while Portable Appliance Testing (PAT) itself might not be explicitly required by law, the broader obligation to ensure the safety of electrical equipment is a legal requirement, particularly in work environments. These requirements’ specifics and interpretation can vary depending on the jurisdiction and local regulations. Here’s a look at the legal backdrop concerning PAT testing, primarily focusing on the UK as an example:
1. UK Legal Framework
- Health and Safety at Work Act (1974): This foundational legislation requires employers to ensure the health and safety of their employees and the public. While it doesn’t mandate PAT testing explicitly, it does set the stage for ensuring electrical equipment is safe to use, which PAT can help demonstrate.
- Electricity at Work Regulations (1989): This is more specific to electrical safety. Regulation 4(2) states that all systems shall be maintained to prevent danger. Again, while PAT testing itself isn’t directly mandated, carrying out such tests is a recognized and effective way of ensuring equipment safety and compliance with these regulations.
- Provision and Use of Work Equipment Regulations (1998) (PUWER): Under PUWER, work equipment must be maintained in an efficient state, in efficient working order, and in good repair. Electrical appliances fall under the definition of work equipment, making regular inspections and maintenance (which can include PAT testing) a part of ensuring compliance.
2. Clarifications
- PAT testing is one way to meet these legal obligations, but it’s not the only way. However, it is a widely recognized and thorough method of ensuring electrical safety.
- The legislation has no fixed interval about how frequently PAT testing must be done. Instead, factors like the type of equipment, the environment in which it’s used, and the frequency of its use can determine the testing frequency. Employers often rely on risk assessments to decide on this.
- The legal obligation isn’t about conducting the test but ensuring safety. So, if an employer or organization can demonstrate that their electrical equipment is safe without PAT testing, they would still be in compliance with the law.
- While not strictly necessary, keeping records of PAT tests can be beneficial. These records indicate a proactive approach to equipment safety if there were ever legal inquiries or insurance claims.
3. Outside the UK
It’s crucial to remember that legal requirements can vary by country. If you’re concerned about the requirements outside of the UK, it’s essential to consult local regulations or seek advice from professionals familiar with the regional rules and standards.
While PAT testing might not be a legal mandate, the obligation to ensure electrical safety in work environments is most certainly. PAT testing is a widely recognized means of fulfilling this responsibility in many jurisdictions.
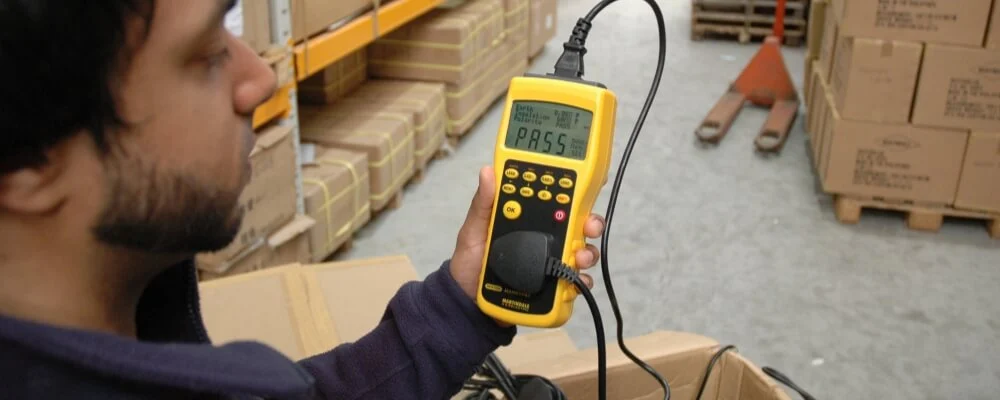
Who Should Be Responsible For PAT Testing In The Workplace?
In the workplace, the responsibility for ensuring Portable Appliance Testing (PAT) is carried out appropriately typically falls on several key parties:
1. Employers
At the broadest level, employers have a duty of care to ensure the safety of their employees and anyone else affected by their operations, as stipulated in health and safety regulations in many countries. This means employers should ensure that all electrical equipment is safe to use and is maintained in a safe condition. As such, they should either ensure they have competent staff in-house to conduct PAT or hire qualified external contractors.
2. Facility or Maintenance Managers
In larger organizations or those with specific departments for building maintenance, the facility or maintenance manager may be responsible for organizing and overseeing PAT testing. This role involves coordinating testing schedules, maintaining records, and rectifying any faults found during testing.
3. Qualified PAT Testers
The actual testing process should be conducted by competent individuals in PAT testing. This doesn’t necessarily mean they need a formal qualification, although training and certification are beneficial. They should, however, understand the types of equipment they’re testing, the potential hazards, and the necessary precautions. This could be an employee who has undergone appropriate training or an external contractor.
4. Employees
While they may not be responsible for the testing, all employees have a role in electrical safety. They should be encouraged to report any damaged equipment or irregularities they notice. They should also cooperate with PAT schedules, ensuring their equipment is available for testing.
5. Health and Safety Representatives
In organizations with dedicated health and safety departments or representatives, these individuals may play a role in ensuring PAT testing is conducted. They could set policies, ensure compliance with local regulations, and review testing records.
In summary, while the actual testing should be conducted by those with the necessary competence, the overarching responsibility lies with the employer. Employers need to ensure regular PAT testing is part of their overall health and safety strategy and that it’s carried out by knowledgeable individuals, whether in-house or externally contracted.
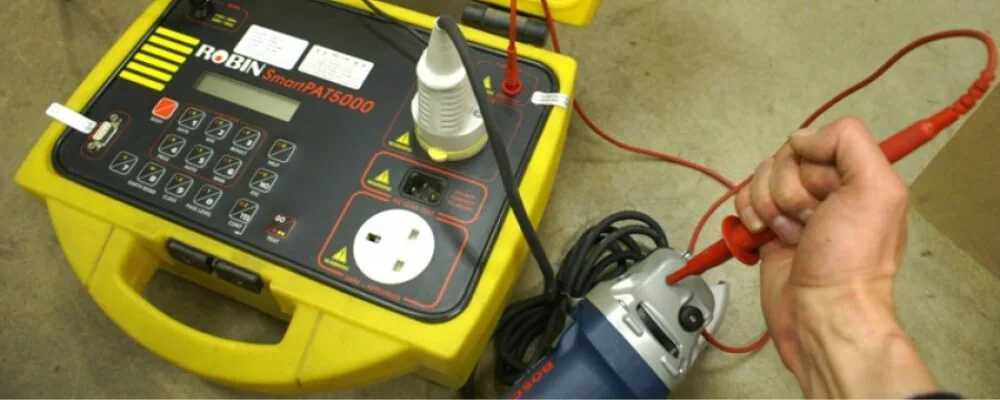
What Is A PAT Test Certificate?
A PAT (Portable Appliance Testing) Test Certificate is a document that provides evidence that an electrical appliance has been tested for safety. The certificate confirms that the appliance has undergone various tests to ensure it is safe and meets the required standards. The main components of a PAT Test Certificate include:
- Details of the Tester: This includes the name, company, and qualifications of the person who conducted the PAT test.
- Date of Test: This indicates when the test was conducted, which can be crucial for determining when the next test is due based on the recommended testing intervals for the type of equipment and its use.
- Appliance Information: Each item tested will have its details listed. This typically includes an identification number or code, the appliance’s description, make, model, and location within the premises.
- Test Results: For each appliance tested, the results for the various tests performed (e.g., earth continuity, insulation resistance, etc.) will be documented. It will clearly state whether the appliance passed or failed each test.
- Overall Status: Based on the individual test results, each appliance will be labeled “PASS” or “FAIL.”
- Comments/Recommendations: If there are any specific concerns or recommendations regarding a tested item, they’ll be noted here. For instance, an appliance might pass the tests but still have a recommendation for a minor repair or preventive measure.
- Signature: The person responsible for conducting the PAT test will typically sign the certificate, verifying its authenticity and the accuracy of the information.
A PAT Test Certificate serves as a record for businesses and organizations, ensuring they maintain a safe environment for employees, customers, and visitors. It’s also a vital document for compliance, as it can be required by insurance companies, regulatory bodies, or during health and safety audits.
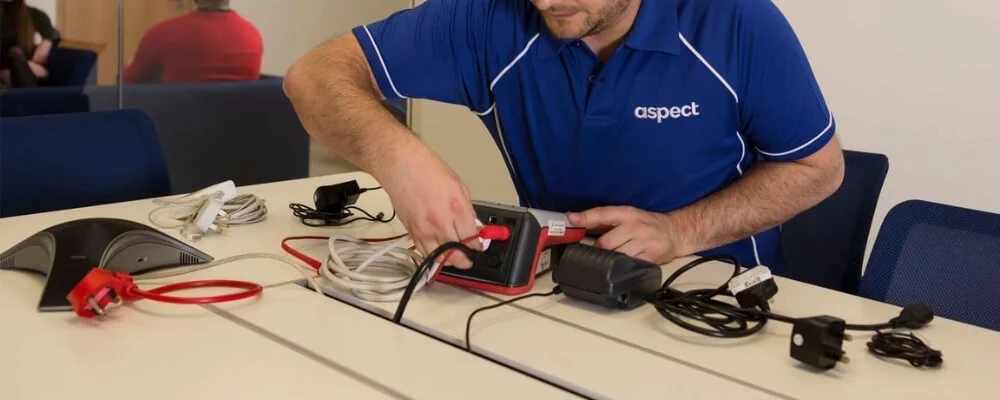
Do I Need To Keep A Record Of PAT Tests?
It is advisable to keep a record of PAT (Portable Appliance Testing) tests. While the specific legal requirements can vary depending on your jurisdiction, keeping a record of PAT tests offers several benefits:
- Proof of Compliance: A documented record provides evidence that you’ve met health and safety obligations related to electrical safety in the workplace. This can be crucial if you’re subject to inspections or audits by regulatory authorities.
- Liability Protection: In the unfortunate event of an electrical accident, having a record of regular PAT tests can demonstrate due diligence on your part, potentially limiting legal liabilities.
- Maintenance Tracking: Keeping records can help you track the condition of your electrical appliances and maintenance needs over time. This can be especially useful for identifying recurring problems or determining when equipment may need to be replaced.
- Scheduling Future Tests: You can determine when the next PAT test is due by referring to past records. This helps ensure that testing is done at the appropriate intervals based on the type of equipment and its use.
- Insurance Requirements: Some insurance companies may require evidence of regular PAT testing as a condition for coverage or to validate a claim. Maintaining records can assist in meeting these requirements.
- Employee Safety: Records can also act as a reference, showing employees that equipment has been tested and is safe to use, thereby promoting a culture of safety in the workplace.
Typically, the records should include details about the tested appliances, test results, any faults found and actions taken, and the name and qualifications of the person who conducted the tests. These records and the PAT Test Certificate offer comprehensive documentation of your organization’s commitment to electrical safety.
Conclusion
Electrical safety is an undebatable priority in both residential and professional environments. Overlooking the importance of ensuring our devices’ safe and efficient operation not only poses a threat to the equipment but, more critically, to human lives. Through Portable Appliance Testing or PAT Testing, we harness a systematic approach to evaluating and certifying the safety of electrical appliances. As we’ve explored in this guide, PAT Testing is more than just a technical procedure; it’s a commitment to safety, a legal obligation, and an integral part of responsible equipment management.
Understanding the different facets of PAT—from the types of tests to the frequency, from who should conduct them to the essential documentation—offers a clear roadmap for businesses, institutions, and even households to stay compliant and safe. At the heart of it all is the realization that safety is not a one-time checkbox but an ongoing responsibility. As technology continues evolving and our reliance on electrical appliances grows, the need for regular PAT Testing becomes even more pronounced.
Whether you’re an employer, an employee, a homeowner, or simply someone keen to understand the workings of the electrical world, we hope this guide serves as a valuable resource. Remember, in electricity, knowledge paired with action can be the difference between safety and catastrophe. Embrace PAT Testing, stay informed, and, most importantly, stay safe.