Safety remains paramount in the bustling environment of industrial sites, construction zones, and everyday workspaces. Among the many safety hazards that professionals and workers need to be aware of, pinch point hazards often get overlooked, even though they are pervasive and can result in severe injuries. Pinch points, or nip points, are areas where a person or a part of a person’s body can be caught between moving and stationary parts of equipment or between the material and a piece of equipment.
The injuries from these hazards can range from minor blisters to more severe, life-threatening traumas. This guide aims to provide a comprehensive overview of pinch point hazards – from identifying and understanding them to practical examples, symbols, safety measures, causes of related injuries, and practical identification strategies.
Whether you’re a seasoned industry professional or someone new to environments with machinery, this guide will offer valuable insights into staying safe around pinch points. Dive in to empower yourself with the knowledge to navigate workspaces with heightened awareness and caution.
What’s a Pinch Point Hazard?
A pinch point hazard refers to any point in machinery or equipment where a person or a part of their body can be caught between moving parts or between a moving part and a stationary one. Such points are areas where two or more spaces converge, posing a risk of injury when body parts, clothing, or tools come into contact with the machine. This hazard is particularly common in settings with machinery having moving parts, such as conveyor belts, gears, and pulleys.
Injuries from pinch-point hazards can range from minor abrasions or contusions to more severe outcomes like amputations or even fatalities. Pinch points might not always be immediately apparent, making them especially dangerous in workplaces where individuals may inadvertently get trapped or crushed, leading to severe harm or potential legal ramifications for businesses that fail to mitigate these risks.
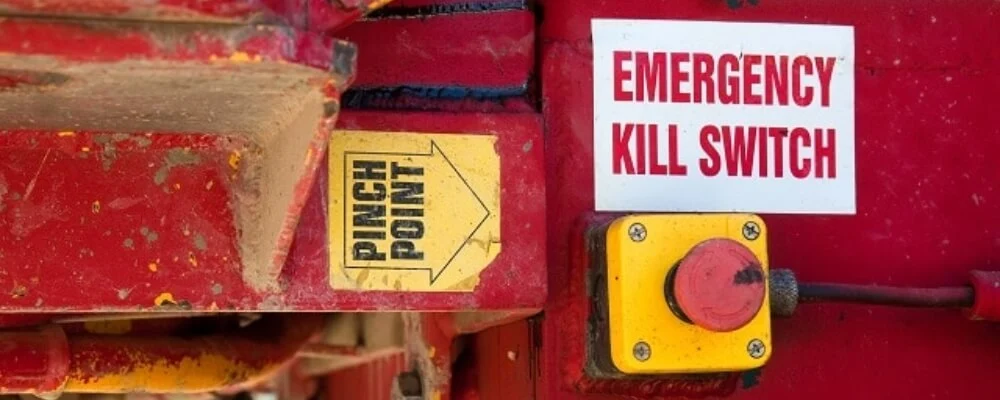
10 Different Examples Of Pinch Point Hazards
Pinch point hazards exist in various settings, ranging from simple household items to complex industrial machinery. Here are 10 different examples of pinch-point hazards:
1. Door Hinges
One of the most common household hazards, the door hinge, presents a risk, particularly to children or those not paying attention. The narrow space between the moving door and the stationary frame can quickly close in on fingers or hands, causing painful injuries. This is especially concerning in heavy doors, where the weight and force can amplify the damage, possibly leading to fractures or severe bruising.
2. Conveyor Belts
In many industrial settings, conveyor belts move objects from one location to another. However, the space where the moving belt meets a stationary part, such as a roller or platform, poses a severe threat. Workers can accidentally get their limbs, fingers, or clothing caught, dragging them into the machinery or resulting in burn injuries due to friction, lacerations, or even amputations.
3. Gears
Machines with interlocking gears are efficient for transmitting motion. Yet, the spaces between these rotating gears can easily trap fingers or other body parts. Given the strength and speed of many gears, especially in industrial machinery, the injuries can be severe, including crushed bones or complete amputations.
4. Pliers and Scissors
Tools like pliers and scissors operate with a pivot point. When used, especially with force or abruptly, the area near the pivot can pinch the skin, leading to painful blisters or cuts. Moreover, the sharp edges can cause more injuries if mishandled or misused.
5. Excavator and Backhoe Buckets
These heavy construction machinery have a moving arm that can pivot or extend. A worker nearby can get caught in the space between this moving part and the main body of the machine, leading to significant trauma, fractures, or more catastrophic injuries, given the machinery’s weight and power.
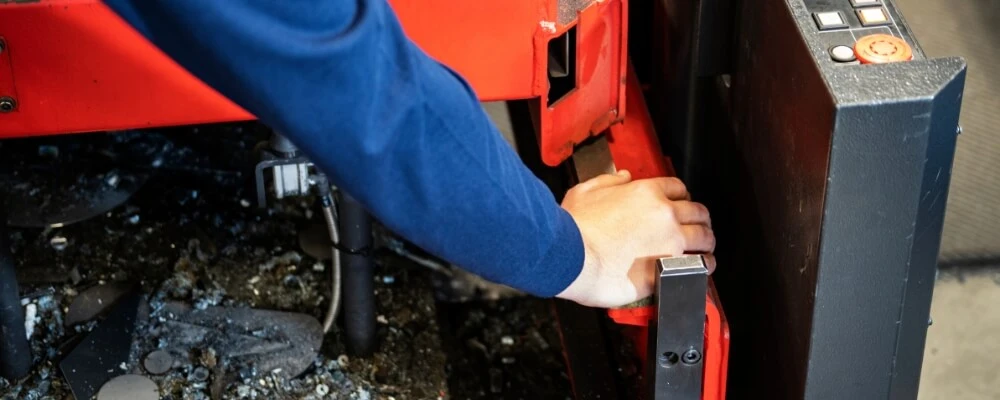
6. Power-driven Rollers
These are critical components in many machines, especially in industries that process materials like paper, metal, or textiles. If hands or fingers get too close, they can be pulled between the rollers. The pressure and force between these rollers can lead to severe crush injuries or entanglement.
7. Truck Doors
Trucks, especially commercial ones, have heavy doors for security and durability. When closing or securing these doors, there’s a risk of hands getting caught between the door and its frame. Given such doors’ weight and solid construction, injuries can range from bruises to broken bones.
8. Elevating Work Platforms
These platforms, often used in construction or maintenance, are designed to lift workers to higher elevations. Workers can be pinched between the platform and any overhead or adjacent structures, like beams or ceilings, if workers are not correctly positioned. Depending on the speed and force, injuries might include compression traumas, fractures, or even more severe injuries if the platform continues its motion.
9. Chain and Sprocket Drives
In many industrial machines, chains transfer motion between parts. These chains can catch fingers, clothing, or hair, especially when moving at high speeds. If a person gets entangled, they could be dragged into the machinery or suffer injuries from the chain, leading to cuts, lacerations, or more severe traumas.
10. Unsecured or Shifting Materials
Construction sites or warehouses often store heavy materials such as concrete blocks, metal sheets, or large equipment. If these are not securely fastened or stacked, they can shift or fall, trapping a worker’s hands or feet between them. Such incidents can lead to crush injuries, fractures, or significant lacerations if the material is sharp-edged.
Each of these examples underscores the importance of being aware of one’s surroundings, especially in environments with machinery or potential moving hazards. Proper training and safety precautions are essential to prevent injuries from these pinch points.
Pinch Point Hazard Sign and Symbol
A Pinch Point Hazard sign typically serves to warn workers and other individuals about areas or machinery where there’s a risk of getting caught between two objects or points, which can lead to severe injuries.
Pinch Point Hazard Sign
The sign usually has a clear, bold warning such as “PINCH POINT” or “WATCH YOUR HANDS” prominently displayed. The text is often white with a black or red background for high visibility. Safety signs also adhere to specific standards, depending on the country and their respective regulatory bodies, so the color and design might vary slightly depending on the jurisdiction.
Pinch Point Hazard Symbol
The symbol often used to represent a pinch point hazard is a simple, graphic representation. This usually consists of a triangular or semi-circular shape depicting a hand or fingers entering a dangerous zone (represented by two converging arrows or objects), suggesting they might get caught or pinched. The hand or fingers are typically shown in black or blue, with red indicating the danger area or the pinching action. This visual representation is immediate and intuitive, providing a quick understanding of the danger even if someone doesn’t take the time to read the warning text.
Using a clear sign and a universally recognized symbol ensures that the warning is understood by many people, regardless of language or literacy barriers. If you want to procure or create such signs, adhering to your country’s or specific industry’s safety standards is essential.
10 Important Safety Tips to Avoid Pinch Point Hazards
Pinch point hazards can pose serious risks in various work environments, especially in industries that involve heavy machinery, equipment, or manual labor. To avoid pinch point accidents and ensure workplace safety, consider these 10 essential safety tips:
1. Proper Training
Training is the foundation of safety. When employees are trained on machinery, it’s not just about knowing which button to press. They need to understand the inner workings, the reasons behind safety protocols, and potential risks. For example, a worker may know how to start a machine, but if they’re unaware of where pinch points occur, they’re at risk every time they operate it. Comprehensive training should simulate real-world scenarios, showcasing the possible dangers of incorrect operation and emphasizing the importance of caution around identified pinch points.
2. Regular Inspections
Just like a car needs regular check-ups, machinery, and workplace equipment need consistent inspections. Over time, wear and tear can cause parts to malfunction or create unforeseen pinch points. Scheduled inspections conducted by qualified personnel ensure that the equipment functions as intended and that no new hazards have emerged. These inspections not only prolong the life of the machinery but also safeguard the lives of those operating them.
3. Use Machine Guards
Machine guards are like the safety barriers on a roller coaster — designed to keep you safe from moving parts that could harm you. These barriers, whether made of metal, plastic, or other durable materials, are specifically designed to shield or block the most hazardous parts of machinery. Without them, the risk of contact with pinch points or moving parts increases exponentially. Their presence is crucial and, in many jurisdictions, mandated by law.
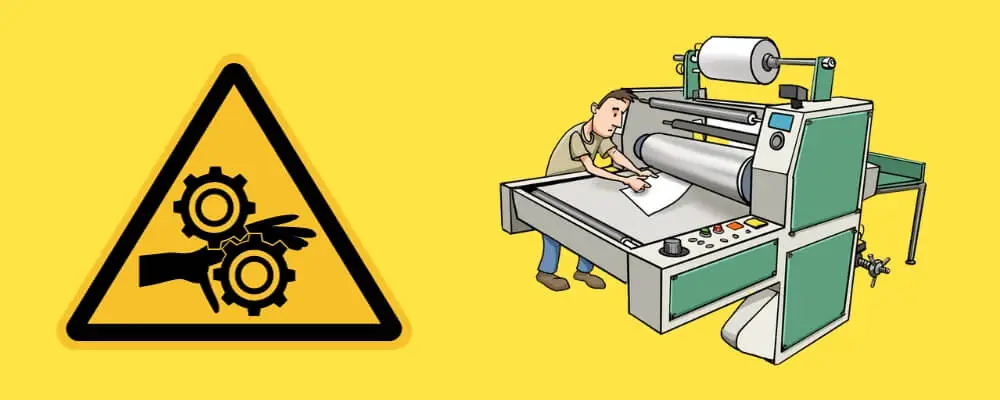
4. Maintain Situational Awareness
Picture a worker engrossed in a conversation or daydreaming near a running machine. The lack of focus can be deadly. Workplaces, especially those with heavy machinery, require undivided attention. Every beep, clang, or unexpected movement can signal something amiss. By being fully present and attuned to their environment, workers can react swiftly to potential threats, reducing the chances of accidents.
5. Wear Appropriate PPE
Personal Protective Equipment (PPE) is the final line of defense against workplace hazards. While training and safety measures aim to prevent accidents, PPE minimizes injury when accidents happen. Gloves can prevent or lessen abrasions, safety footwear can protect against crushing injuries, and snug-fitting clothing ensures nothing gets caught in machinery. Conversely, jewelry or loose attire can become entanglement hazards in themselves.
6. Lockout/Tagout Procedures
Imagine trying to repair a machine, and someone unknowingly turns it on. Lockout/tagout procedures ensure machines are properly shut off and cannot be started again without the knowledge of the person working on them. This is often done using locks and warning tags. It’s a vital step in ensuring that maintenance or repair work on machinery is done safely.
7. Keep Work Areas Clean
A stray tool or an out-of-place object can spell disaster in a workspace. Clutter isn’t just an eyesore; it’s a hazard. Clean, organized workspaces ensure that nothing unintentionally comes into contact with machinery. It also ensures that workers have clear paths to move, reducing the likelihood of bumps or stumbles that could place them in harm’s way.
8. Use Tools When Necessary
Hands are irreplaceable. If there’s an option to use a tool rather than placing one’s hand near a potential pinch point, the tool should always be the choice. Whether it’s a long wrench, a stick, or specialized equipment, using tools can provide an additional layer of separation from dangerous machinery parts.
9. Post Warning Signs
Visual cues are powerful reminders. Warning signs act as constant reminders of the dangers lurking in machinery. Whether it’s a symbol of a hand near gears or a simple “Caution!” text, these signs catch the attention, reminding workers to be cautious, especially if they’re new or unfamiliar with the machinery.
10. Encourage Reporting
A culture of safety is one where every individual feels responsible. Encouraging reporting means fostering an environment where employees aren’t afraid to voice concerns or point out potential hazards. It ensures that issues are promptly addressed and everyone learns from near misses or oversights, making the workplace safer.
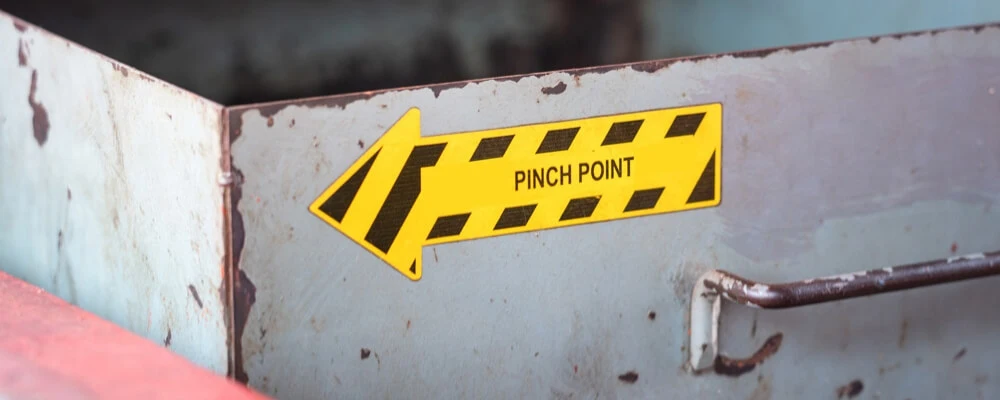
Common Causes Of Injuries From Pinch Points
Unfortunately, injuries from pinch points are common in many industries, particularly where machinery and moving equipment are involved. Understanding the root causes of such injuries can help in formulating preventive measures. Here are some common causes of injuries from pinch points:
- Lack of Awareness: Not being aware of the locations of pinch points or underestimating their potential danger often leads workers to inadvertently place their hands or other body parts in harm’s way.
- Absence of Machine Guards: Machine guards are specifically designed to cover dangerous parts of a machine. Workers are exposed to pinch-point hazards if absent, damaged, or improperly installed.
- Inadequate Training: Workers who aren’t adequately trained on the use of equipment might not be aware of the locations of pinch points or how to safely operate the machinery.
- Faulty or Malfunctioning Equipment: Equipment that isn’t maintained or malfunctions can lead to unexpected movements, creating unforeseen pinch points or suddenly exposing existing ones.
- Distractions: Distracted workers might not pay full attention to their tasks. This inattention can result in their hands or other body parts accidentally entering pinch points.
- Improper Hand Placement: Placing hands-on machinery without knowing where the pinch points are can lead to injuries, especially during machine startup or operation.
- Loose Clothing or Jewelry: These can get caught in machinery, pulling the wearer into a pinch point.
- Bypassing Safety Protocols: Sometimes, workers might feel that safety measures slow them down and choose to bypass them, putting themselves at direct risk.
- Not Using Personal Protective Equipment (PPE): While PPE-like gloves can’t always prevent a pinch point injury, they can often reduce the severity. Failing to use PPE increases the risk of more severe injuries.
- Failure to Lockout/Tagout: Not following lockout/tagout procedures can result in machinery being turned on unexpectedly while someone is working on or near it.
- Complacency: Over time, workers can become too comfortable or complacent around machinery, leading them to let their guard down and not treat pinch points with the respect and caution they require.
Addressing these causes through training, equipment maintenance, and fostering a safety culture can significantly reduce pinch point-related injuries.
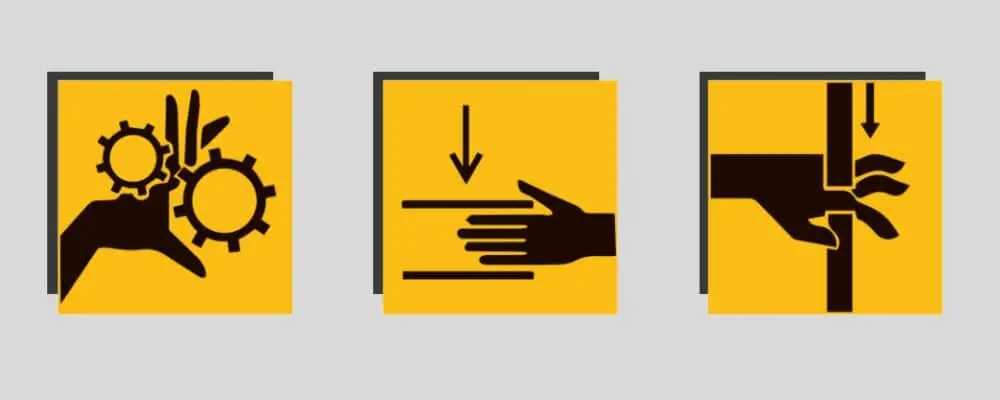
Practical Tips On How To Identify Pinch Points
Identifying pinch points is crucial to preventing related injuries. Here are some tips to help you identify pinch points in various settings:
- Understand Machine Operation: Familiarize yourself with how machinery operates. Knowing the moving parts and their functions will help spot potential pinch points.
- Review Manufacturer’s Manual: Most machinery has detailed manuals highlighting safety features and potential hazards. Always consult these manuals when setting up or operating new equipment.
- Visual Inspection: Regularly inspect machinery and equipment. Look for areas where moving parts come close to each other or to stationary parts.
- Look for Previous Injury Reports: Past incidents can indicate risk areas. Regularly review injury logs or reports to determine if there have been any pinch point-related injuries and take measures to prevent future occurrences.
- Consult Experienced Workers: Those working with a particular piece of equipment for a long time can often pinpoint its hazards. Always ask experienced operators for their insights.
- Conduct Risk Assessments: Regular risk assessments can identify hazards in machinery and processes. Use structured methodologies to assess and rank potential risks.
- Watch for Near Misses: Near misses are incidents that could have resulted in injuries but didn’t. Monitoring and analyzing near misses can help identify and rectify potential pinch points before they cause harm.
- Training and Workshops: Regular training sessions can educate workers about known hazards and act as brainstorming sessions where they can discuss potential pinch points they’ve noticed.
- Labeling and Signage: While this is more of a preventive measure if you see warning signs or labels about moving parts, these often indicate the presence of pinch points. Consider adding such signage as a reminder once pinch points are identified.
- Monitor Maintenance and Repairs: Machines being repaired or undergoing maintenance can exhibit different behaviors or have protective covers removed. Treat such equipment with added caution and look for new potential pinch points.
- Stay Updated with Industry Best Practices: Join industry groups, attend seminars, and participate in workshops. Connecting with industry peers can provide insights into everyday problems and solutions related to pinch points.
Remember, the key to identifying pinch points is a combination of knowledge, vigilance, and a proactive approach. Encouraging a culture of safety and open communication can significantly aid in the early identification and mitigation of pinch-point hazards.
Conclusion
Awareness, vigilance, and proactive measures form the foundation of safety in any environment, especially when navigating the potential risks associated with pinch-point hazards. As we’ve delved into the intricacies of pinch points throughout this guide, it’s evident that understanding their presence and potential danger is half the battle. The other half lies in consistent action—regular inspections, proper training, and fostering a safety-conscious culture.
It’s essential to remember that while machinery and equipment play a significant role in advancing our industries, human lives and well-being are irreplaceable. By prioritizing safety and ensuring that everyone is equipped with the knowledge and tools to identify and avoid pinch points, we pave the way for a more productive and safer workspace. Stay alert, stay informed, and always prioritize safety above all.