Imagine a factory where big machines are working non-stop. These machines have parts that move and sometimes come very close to each other. Where these parts come close, a small space can be dangerous. This small space is called a “Nip Point.” It might not look like much, but it can be risky for people working around these machines.
In this blog post, we will talk about what nip points are, why they can be dangerous, and the three main types of nip point you should know about. This is super important for anyone who works with machines or wants to know how to stay safe in places with big machines. Let’s dive in and learn more about these sneaky little spaces that need our attention.
What are Nip Points?
Nip points are areas in machinery where two rotating or moving parts come close together, creating a small opening or point of contact. These points pose a significant hazard because they can catch or trap body parts like fingers, hands, arms, clothing, and hair. When a person’s body part or material gets caught in a nip point, the force of the moving machinery can cause severe injuries, including crushing, shearing, or amputation. Nip points can occur in various types of machinery and are a common cause of workplace injuries. Workers must be aware of these hazards and take appropriate safety measures.
In-running nip points are one of the most common causes of workplace injuries involving machinery. These pinch points occur when the material is pulled into a gradually narrowing opening between two rolls. The force of the moving material can be strong enough to trap and crush body parts, such as fingers, hands, arms, and even hair. Nip point injuries can be extremely serious and even fatal in some cases. Workers who operate or maintain machinery must be aware of the dangers of nip points and take precautions to protect themselves. Some simple safety measures include using guards or shields to block access to nip points and ensuring that loose clothing and long hair are securely tied back before operating machinery.
U.S. Department of Labor, Occupational Safety & Health Administration (OSHA) Dangerous nip points also occur in machinery parts, not in direct contact with the material, such as near pulleys, gears, and spindles—where the linear or rotary motion of the moving equipment occurs through narrowing openings between components. Frequently the machine is running too fast or is too powerful to allow stopping before significant injury occurs.
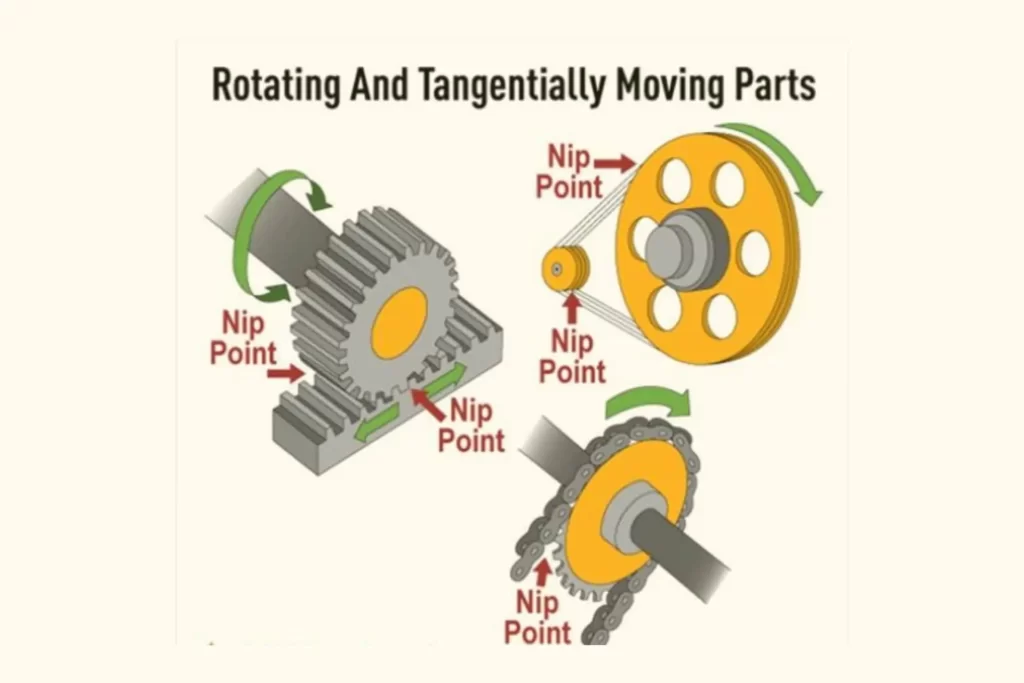
3 Main Types Of In-Running Nips
Anyone who has worked with machinery knows that there are a lot of potential hazards. One of the most common hazards is the in-running nip point caused by rotating machinery parts. This can be a very serious hazard, as it can cause amputation or entrapment. In-running nip points can be found anywhere on the machine but are most commonly found on belts, pulleys, and gears. The best way to prevent this type of hazard is to ensure that all workers are properly trained on the risks and how to avoid them. Additionally, all workers should wear proper safety gear when working with machinery. There are three main types of in-running nips.
1. Parallel rotating parts
Parts can rotate in opposite directions while their axes are parallel. These parts may be in contact, producing nip points. Stock fed between the rolls may also produce nip points. This danger is common on machines with intermeshing gears, rolling mills, and calenders.
2. Tangentially moving parts
Tangentially moving nip points are also created between rotating and tangentially moving parts. Some examples would be the point of contact between a power transmission belt and its pulley, a chain, and a sprocket, and a rack and pinion.
3. Rotating and fixed parts
Nip points can occur between rotating and fixed parts, creating a shearing, crushing, or abrading action. Examples are spoked handwheels or flywheels, screw conveyors, the periphery of an abrasive wheel, and an incorrectly adjusted work rest.
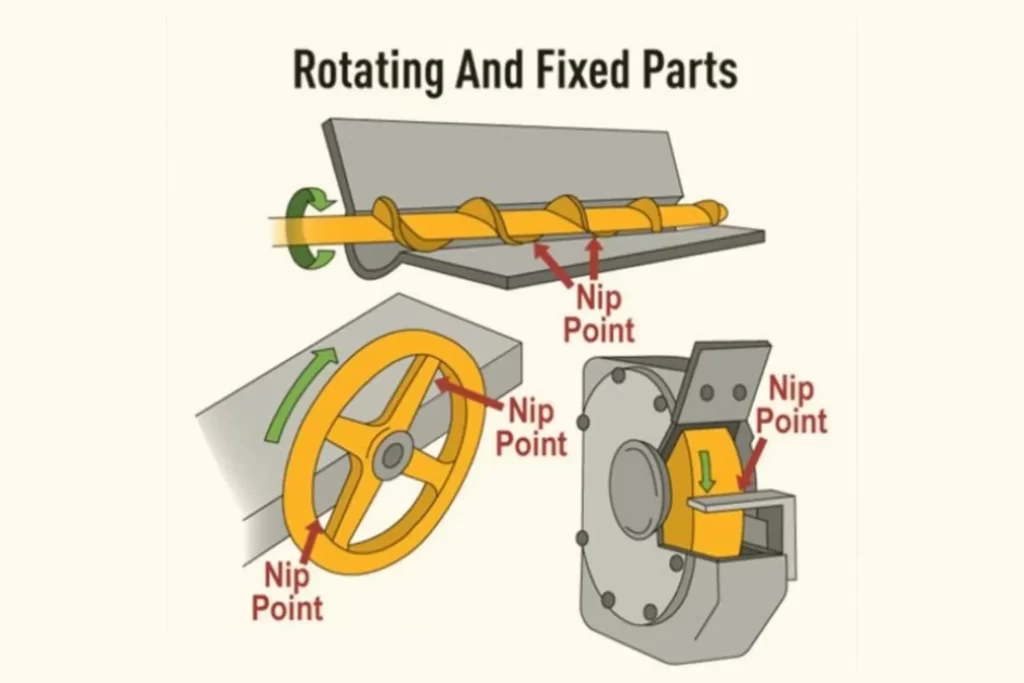
Safety Measures to Prevent Injuries from Nip Points:
Understanding the different types of in-running nips is important, but it is equally important to know how to prevent injuries associated with them. Here are some safety measures that should be taken to minimize the risk of nip point accidents:
- Machine Guarding: Guards should be installed to prevent access to nip points. These guards can be fixed, interlocked, adjustable, or self-adjusting depending on the requirements of the machinery. They should be designed in a way that does not obstruct the operator’s view or impede the operation of the machinery.
- Training and Awareness: Workers should be trained to understand the dangers of nip points and the importance of safety procedures. Training programs should include information about the specific types of in-running nips, how they are created, and the types of guards or devices that can protect against them.
- Signage and Labeling: Clear and conspicuous signs should be placed on or near machinery to warn of the presence of nip points. Labels can also remind workers of specific precautions when operating the machinery.
- Regular Inspection and Maintenance: Machinery should be regularly inspected for worn or damaged parts that might create new nip points. Proper maintenance should ensure that all components are in good working order and that guards are securely in place.
- Emergency Stop Devices: Machines should be equipped with emergency stop devices that can be easily accessed and operated to immediately stop the machine in an emergency.
- Personal Protective Equipment (PPE): Workers should wear appropriate personal protective equipment, such as gloves, safety glasses, and protective clothing. Loose clothing, jewelry, and long hair should be secured or covered to avoid getting caught in the machinery.
- Safe Work Practices: Establish and enforce safe work practices such as not reaching into areas where nip points may be present, ensuring machinery is turned off and de-energized before performing maintenance, and not bypassing or removing guards.
- Safe Design Principles: When purchasing or modifying new machinery, ensure it has been designed safely. Look for machines that have nip points eliminated or guarded by design.
- Monitoring and Supervision: Regular monitoring of the work area and supervision can ensure that employees follow safety protocols and use machinery correctly.
In summary, nip points are hazardous areas in machinery where there is the potential for body parts or clothing to be caught between moving parts. Three main types of in-running nips exist: parallel rotating parts, tangentially moving parts, and rotating and fixed parts. Implementing safety measures, including machine guarding, training, proper maintenance, and personal protective equipment, is critical in preventing injuries and accidents associated with nip points.