In the realm of industrial machinery and manufacturing processes, the safety of operators and workers is paramount. From colossal hydraulic presses to intricate automated assembly lines, machines can perform tasks that increase productivity exponentially. However, these mechanical marvels can pose significant threats to human safety if improperly handled or malfunctioned. In this context, machine safeguard devices are crucial in protecting workers from potential hazards associated with operating machinery.
This article will explore six essential devices engineered to minimize the risk of accidents and ensure a safer working environment. Whether you are an employer looking to enhance the safety protocols at your facility, or an employee seeking to understand how these devices can protect you on the job, this article serves as an informative guide. Get ready to dive into the world of presence-sensing devices, pullback devices, restraint devices, safety trip controls, two-hand control devices, and two-hand trip devices, and discover how each of these ingenious innovations contributes to making the workplace a safer space for all.
6 Types Of Machine Safeguard Devices
A safety device may perform one of several functions. It may stop the machine if a hand or any part of the body is inadvertently placed in the danger area; restrain or withdraw the operator’s hands from the danger area during operation; require the operator to use both hands on machine controls, thus keeping both hands and body out of danger, or provide a barrier which is synchronized with the operating cycle of the machine to prevent entry to the danger area during the hazardous part of the cycle.
1. Presence-Sensing Devices

The use of presence-sensing devices has become increasingly common in recent years as a way to improve safety in the workplace. These devices use a system of light or radiofrequency sources and controls, which can interrupt the machine’s operating cycle if the light or electric field is broken. This prevents the machine from starting up again until the field is restored, which improves safety for workers who might otherwise be exposed to risks such as moving parts or flying debris. These devices have been shown to reduce the incidence of serious accidents and injuries, making them an important part of any safety program.
Several types of presence-sensing devices are available on the market, each with advantages and disadvantages. One type of device uses an infrared beam to detect the presence of a person or object in the beam’s path. These devices are often used in doorways or other areas where there is a danger of someone being struck by a moving object. Another device uses radiofrequency waves to detect the presence of people or objects. These devices are often used in areas with a danger of electrocution, such as near electrical panels or wet environments.
- Photoelectric presence-sensing device: When the light beam is broken, either the ram will not start to cycle, or, if the cycle has begun, the stopping mechanism will be activated so that the press stops before the operator’s hand can enter the danger zone.
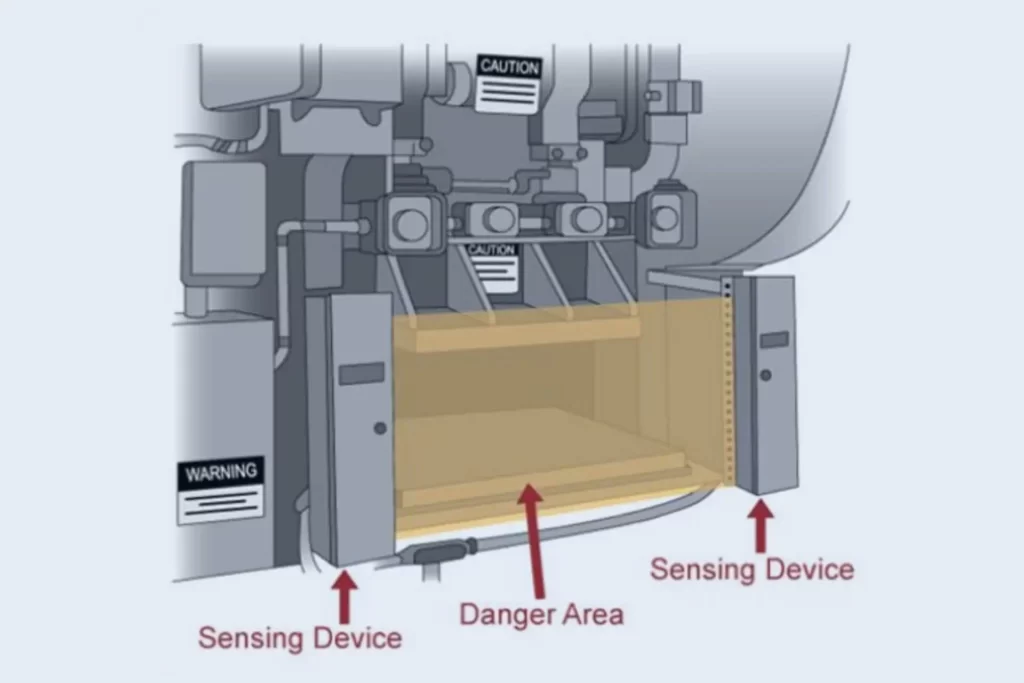
- Electromechanical sensing device: This device has a probe or contact bar which descends to a predetermined distance when the operator initiates the machine cycle. The control circuit does not actuate the machine cycle if an obstruction prevents it from descending its predetermined distance.
2. Pullback Devices
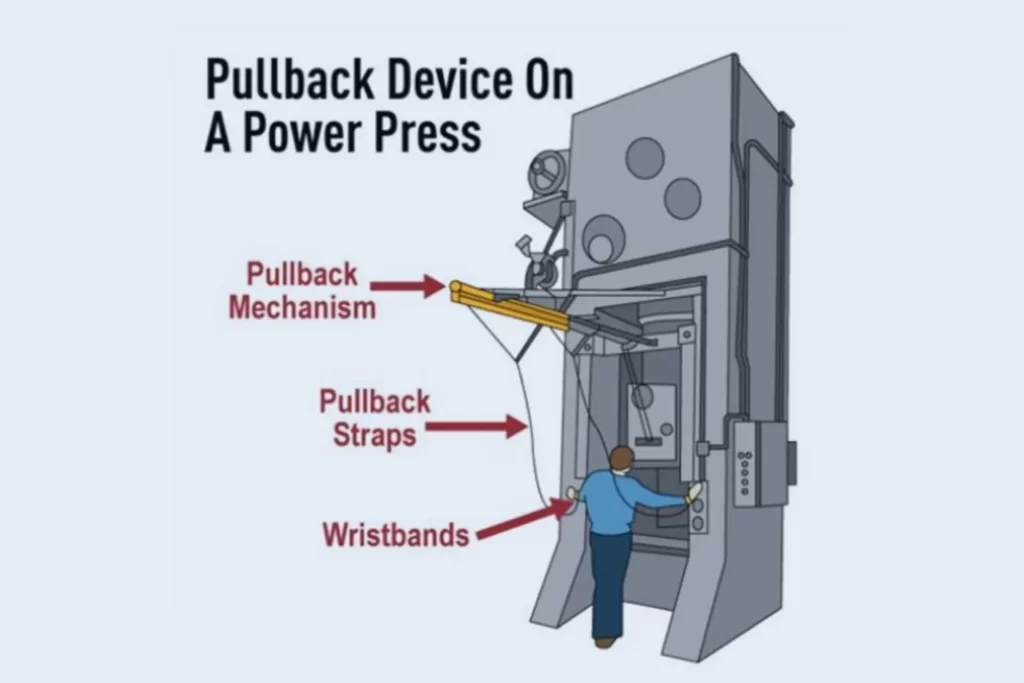
Pullback devices use a series of cables attached to the operator’s hands, wrists, and/or arms. This type of device is primarily used on machines with stroking action. When the slide/ram is up between cycles, the operator is allowed access to the point of operation. When the slide/ram begins to cycle by starting its descent, a mechanical linkage automatically assures the withdrawal of the hands from the point of operation.
3. Restraint Devices
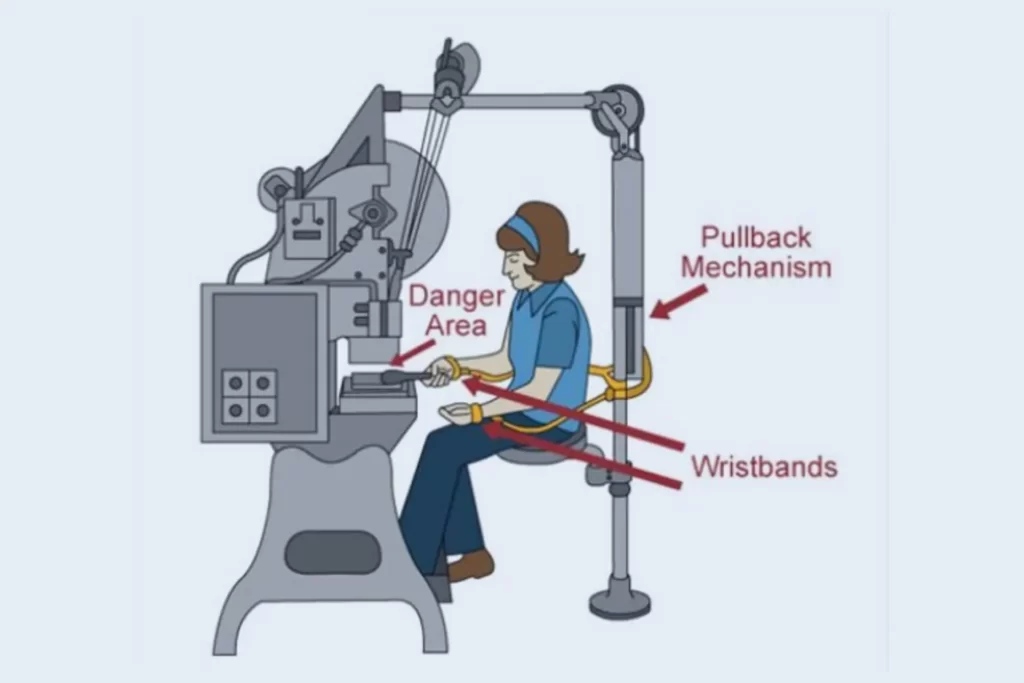
The restraint (holdout) device in the figure to the right uses cables or straps attached to the operator’s hands at a fixed point. The cables or straps must be adjusted to let the operator’s hands travel only within a predetermined safe area. No extending or retracting action is required because the hands are never allowed to extend into the danger area. Consequently, hand-feeding tools are often necessary if the operation involves placing material in a dangerous area.
4. Safety Trip Controls
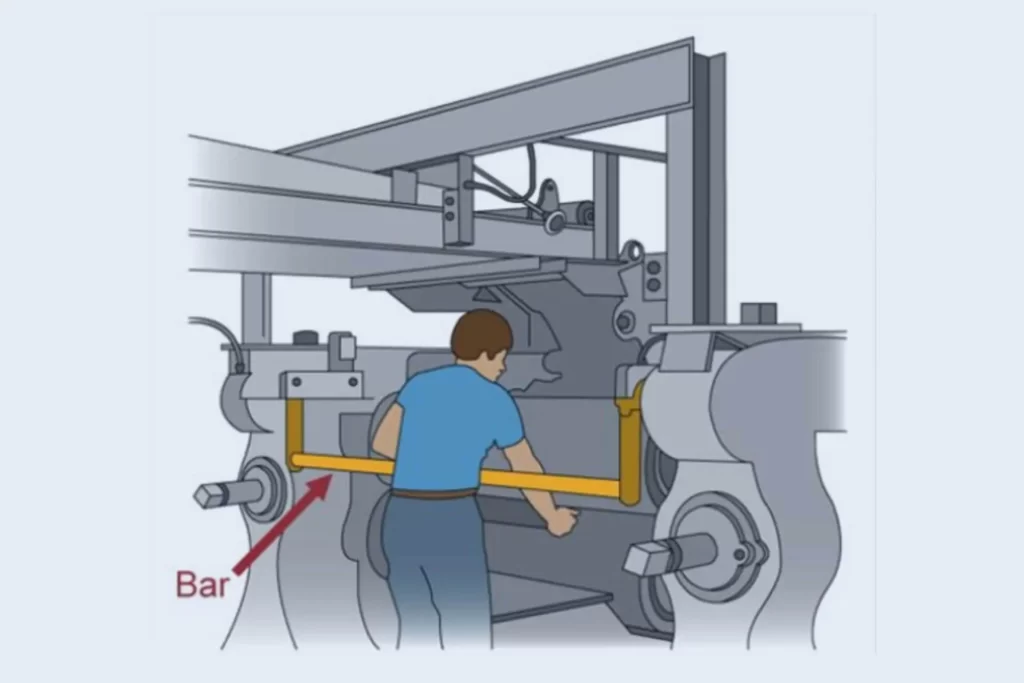
Safety trip controls provide a quick means for deactivating the machine in an emergency. A pressure-sensitive body bar, when depressed, will deactivate the machine. If the operator or anyone trips loses balance, or is drawn toward the machine, applying pressure to the bar will stop the operation. The positioning of the bar, therefore, is critical. It must stop the machine before a part of the employee’s body reaches the dangerous area.
Unfortunately, it may be easy to defeat the body bar by going under it into the danger zone. The figure here shows a pressure-sensitive body bar on the front of a rubber mill.
5. Two-Hand Control Devices
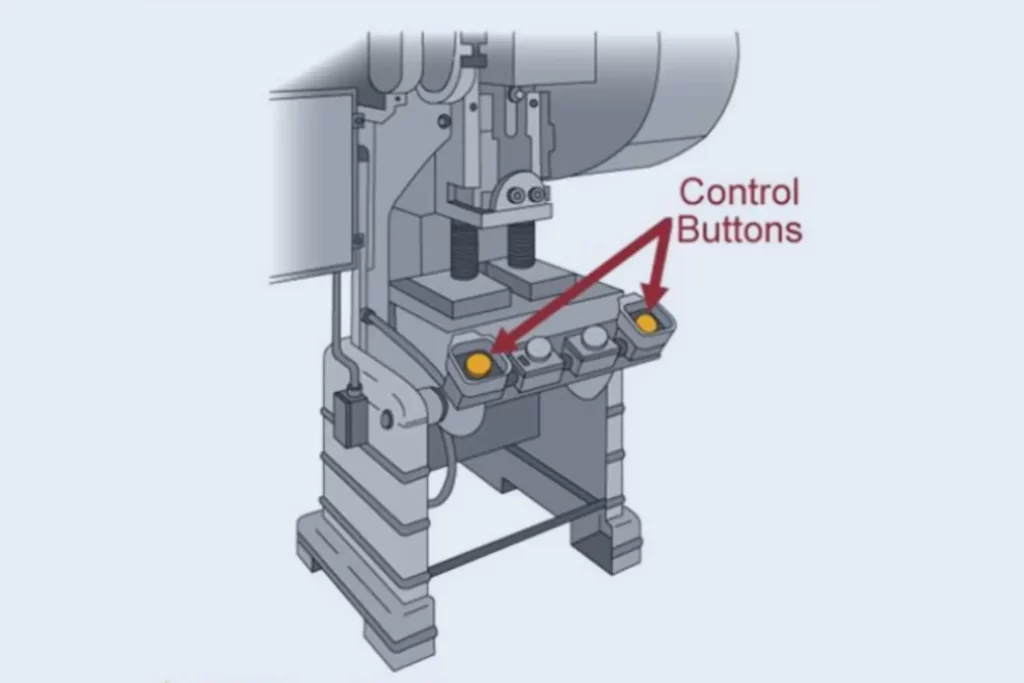
The two-hand control device requires constant, concurrent pressure by the operator to activate the machine. If used on a power press, this control requires a part-revolution clutch, brake, and brake monitor. With this device, the operator’s hands must be safe (on control buttons) and safe from danger while the machine completes its closing cycle.
6. Two-Hand Trip Devices
The two-hand trip device requires concurrent application of the operator’s control buttons to activate the machine cycle, after which the hands are free. This device requires the joint operation of two trigger buttons away from the “danger zone” of the press. To be effective, both two-hand controls and trips must be located so that the operator cannot use two hands or one hand and another part of his/her body to trip the machine.
What Do Safeguarding Devices Do To Protect The Worker?
Safeguarding devices are designed to protect workers by mitigating the risks associated with operating machinery. Here’s what they do to ensure protection:
- Prevent Access to Hazardous Areas: Some safeguarding devices, like barriers or shields, physically prevent the operator’s body or limbs from entering areas where they could be injured by moving parts.
- Detect Presence: Presence-sensing devices like light curtains or radiofrequency sensors can detect when a person or object is too close to the machine. Upon detection, these devices will either halt the machine’s operation or prevent it from starting up.
- Emergency Stops: Devices like safety trip controls allow for quick deactivation of the machine in emergencies. For example, a pressure-sensitive bar can halt machine operation if someone stumbles into it.
- Restrict Movements: Restraint devices, like cables or straps, are designed to limit the movement of the operator’s hands, ensuring that they cannot reach hazardous areas.
- Automatic Withdrawal: Pullback devices are attached to the operator’s hands and automatically pull them away from the danger zone when the machine is in motion.
- Require Two-Hand Operation: Two-hand control and two-hand trip devices require the operator to use both hands to operate the machine. This ensures that the operator’s hands are engaged with the controls and away from the danger zone when the machine operates.
- Create Safe Work Procedures: By incorporating safeguarding devices, the work procedure becomes safer, ensuring that certain safety protocols are followed before the machine operates.
- Educate and Train Workers: While not a physical device, an essential aspect of safeguarding is training workers to understand the purpose and function of these devices, ensuring proper usage and maintenance.
By employing these functions, safeguarding devices significantly reduce the likelihood of accidents, injuries, and fatalities in environments where machinery is operated, promoting a safer and more productive workplace.
Conclusion
In conclusion, the importance of machine safeguard devices in ensuring the safety of machine operators cannot be overstated. These six types of safety devices – presence-sensing devices, pullback devices, restraint devices, safety trip controls, two-hand control devices, and two-hand trip devices – all play a vital role in safeguarding against potential hazards and minimizing the risk of accidents. By creating safer environments, these devices protect employees and enhance productivity by minimizing downtime caused by accidents.
Whether stopping the machine operation in case of an intrusion or ensuring an operator’s hands remain clear of the danger zone, each device contributes to safety in different yet crucial ways. Both employers and employees must understand these devices and their operation to foster a safety culture and maintain a hazard-free workplace.