In today’s fast-paced business environment, ensuring the safety and well-being of employees is more than just a regulatory requirement—it’s a cornerstone of responsible and sustainable organizational growth. A comprehensive Workplace Safety Program protects workers from potential hazards, boosts productivity, reinforces a company’s reputation, and promotes a culture of continuous improvement.
In this guide, we’ll delve into ten essential tips to help you craft an effective safety program, balancing regulatory compliance and creating an environment where employees feel valued and protected. Whether you’re just starting your safety journey or refining existing protocols, these insights will pave the way for a safer, more harmonious workplace.
Workplace Safety Program
A Workplace Safety Program is a structured plan of action designed to prevent accidents and occupational diseases in the course of work. It encompasses a set of policies, procedures, and practices aimed at identifying and controlling hazards in the workplace, ensuring compliance with local and national safety regulations, and creating a culture that prioritizes the health and well-being of employees. These programs often include elements like training sessions, risk assessments, emergency response plans, equipment maintenance protocols, and reporting mechanisms for potential hazards or incidents.
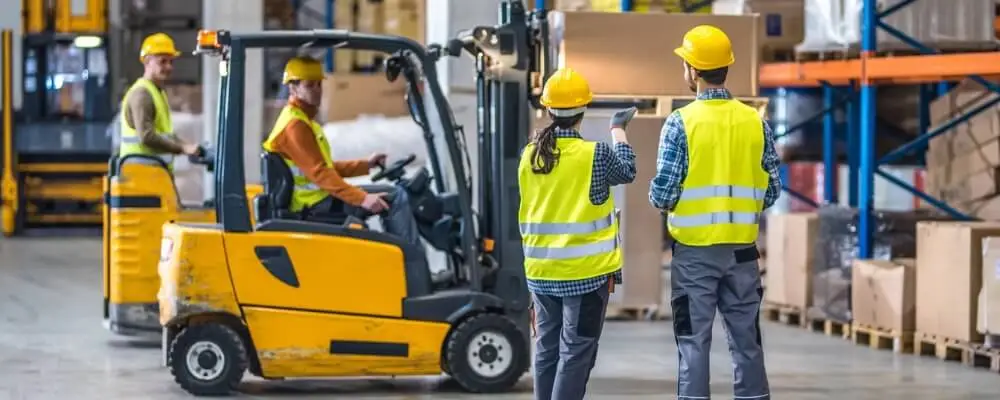
Importance of a Workplace Safety Program
- Employee Protection: The primary aim of any Workplace Safety Program is to safeguard the well-being of employees. A well-implemented program reduces the risk of accidents, illnesses, and fatalities by addressing potential hazards proactively.
- Regulatory Compliance: Many countries have stringent occupational health and safety regulations. A comprehensive safety program ensures businesses adhere to these rules, avoiding legal complications, penalties, or potential shutdowns.
- Economic Savings: Workplace accidents and diseases lead to significant medical expenses, compensation, lost work time, and potential litigation. By preventing such incidents, organizations can avoid these unexpected costs.
- Enhanced Productivity: Employees are more productive in environments where they feel safe. They can focus better on their tasks without worrying about potential risks. Additionally, fewer accidents mean fewer work interruptions, leading to consistent output.
- Reputation Management: Companies known for emphasizing safety are viewed more favorably by clients, partners, and potential employees. A robust safety program can enhance an organization’s reputation, making it a preferred choice for stakeholders.
- Employee Morale and Retention: Knowing their well-being is a priority boosts employee morale. It fosters organizational trust, increasing job satisfaction and better retention rates.
- Continuous Improvement Culture: A dynamic Workplace Safety Program encourages a culture of continuous improvement. Regular evaluations, feedback, and adaptations create an environment where betterment is constantly pursued, benefiting all facets of the business.
A Workplace Safety Program is a regulatory necessity and a cornerstone for an organization’s sustainable and responsible growth. It intertwines the welfare of employees with the broader goals of productivity, growth, and reputation management.
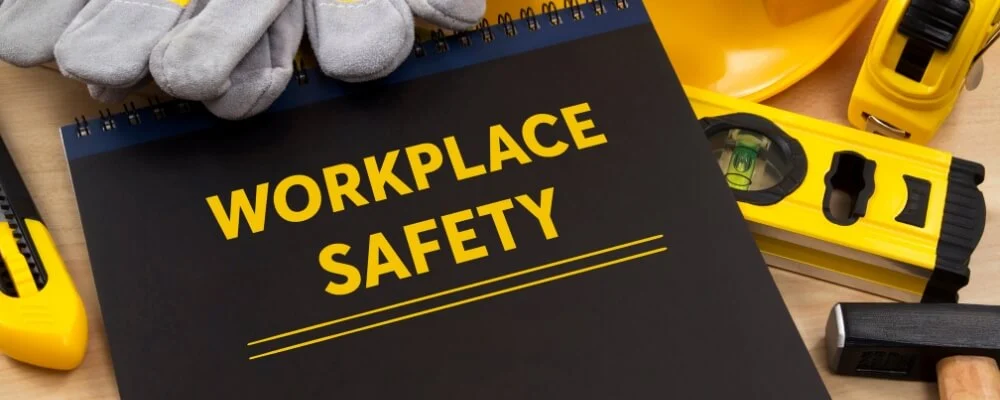
10 Tips For Creating an Effective Workplace Safety Program
Creating an effective workplace safety program is essential for protecting employees, preventing accidents, and ensuring the smooth operation of a business. Here are 10 tips to consider when developing a safety program:
1. Management Commitment
The success of any safety program heavily relies on the dedication of top-level management. Their commitment isn’t just a verbal affirmation; it involves a tangible allocation of resources, time, and capital. For instance, setting aside a budget for safety training or investing in safer machinery sends a clear message throughout the organization about the importance of safety.
When leaders show active involvement in safety initiatives and emphasize it in their regular communications, it creates a culture where every employee understands the value of a safe workplace. This commitment, in turn, results in a more engaged and safety-conscious workforce.
2. Employee Involvement
Safety is everyone’s responsibility. To create a truly effective safety program, it is vital to involve employees from all tiers of the organization. Their day-to-day experiences give them an unparalleled understanding of potential risks and hazards.
When employees have platforms like safety committees to voice their concerns, share experiences, and provide solutions, it fosters a proactive approach to safety. Engaging employees brings to light potential issues management may overlook and instills a sense of ownership and pride in the safety program.
3. Regular Risk Assessments
In the ever-evolving dynamics of workplaces, hazards can change or newly emerge. By conducting regular risk assessments, companies can stay ahead of potential threats. These assessments should be comprehensive, examining the evident physical hazards like malfunctioning equipment and the more subtle behavioral ones like cutting corners during procedures.
After identifying these risks, they should be prioritized based on the severity of potential harm and the chance of them occurring. Such prioritization ensures that resources are allocated efficiently to mitigate the most significant risks first.
4. Training and Education
Knowledge is a critical defense against workplace accidents. Continuous training ensures that employees are well-versed in the best practices related to their roles. However, it’s essential that training isn’t just a box-ticking exercise. The content should be engaging, relevant to the employee’s specific tasks, and regularly updated to reflect changes in equipment, processes, or industry best practices.
Additionally, with new technologies and procedures, training materials should be revised to ensure every employee is equipped with the latest safety knowledge.
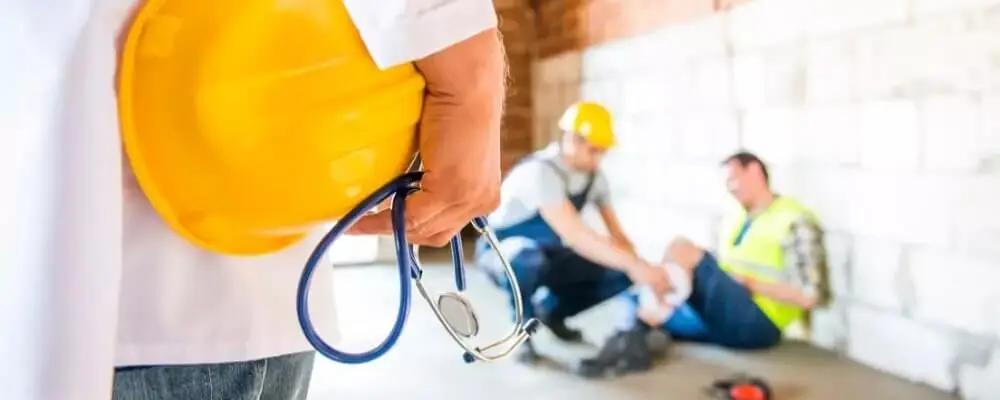
5. Clear Communication
The best safety strategies can fall apart without clear communication. Visual cues, such as signs and posters, can serve as constant reminders of safety protocols, ensuring that procedures are top of mind. Moreover, hosting regular safety meetings creates an open dialogue about safety.
Discussing incidents or near misses in these forums can provide valuable learning opportunities and underscore the importance of adhering to safety guidelines. Through open communication channels, employees can stay informed about any changes to safety procedures, ensuring everyone is aligned in their efforts to maintain a safe working environment.
6. Emergency Preparedness
Every organization should anticipate and prepare for emergencies. This involves crafting a comprehensive emergency response plan detailing the steps to be taken in various scenarios, such as fires, chemical spills, and natural disasters.
The key to an effective response is familiarity with the plan, so conducting regular drills is crucial. These drills ensure that, in the heat of the moment, every individual knows their role and can act swiftly, reducing the potential for harm or damage.
7. Maintain Equipment
The state of machinery, equipment, and tools can significantly influence workplace safety. Neglected or poorly maintained equipment is a ticking time bomb, as it can malfunction without warning, leading to potential injuries.
Hence, it is imperative that regular inspections are conducted and any signs of wear, damage, or malfunction are addressed promptly. Proper maintenance doesn’t just extend the lifespan of the equipment but, more importantly, ensures that those using them are always safe.
8. Implement Reporting Systems
Transparency and open communication form the bedrock of a successful safety program. The organization can gather invaluable data by creating a user-friendly system for employees to report potential hazards, near misses, or actual incidents. This data not only helps rectify immediate concerns but also aids in refining safety protocols.
Additionally, it’s vital to create a culture where employees feel safe to report without fear of retribution. This non-punitive approach encourages honesty, allowing the organization to address issues before they escalate.
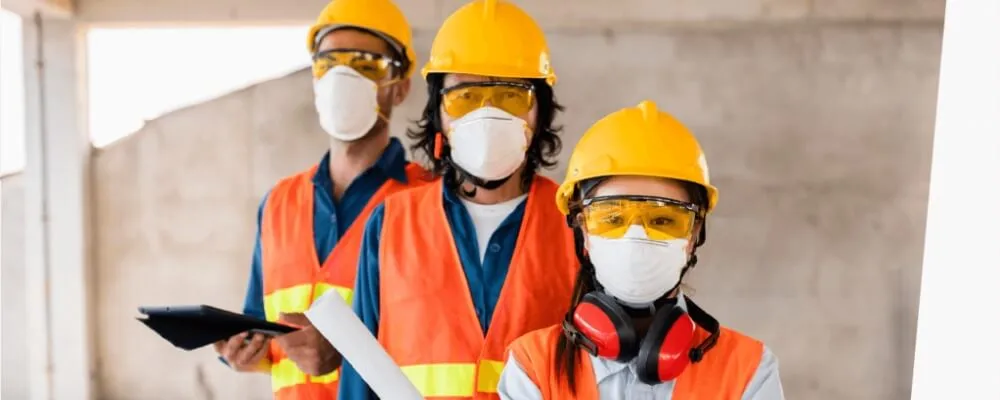
9. Continuous Improvement
The pursuit of safety is a continuous journey. As industries evolve, so do their associated risks. Therefore, organizations must regularly review and update their safety protocols. This should be based on employee feedback, learnings from incident reports, and staying abreast of new industry standards or regulations.
By cultivating a mindset of continuous improvement, organizations can adapt to changing circumstances, ensuring they always prioritize the safety of their employees.
10. Celebrate Successes
Positive reinforcement can be a powerful motivator. Recognizing and celebrating safety milestones serves a dual purpose. Firstly, it boosts the workforce’s morale, making them feel appreciated for maintaining a safe environment.
Whether acknowledging a certain duration without incidents or the successful execution of a new safety measure, these celebrations instill pride in the workforce. Secondly, it underscores the importance of safety, reminding everyone of its centrality to the organization’s ethos.
Conclusion
In a world where business dynamics are ever-evolving, the consistent thread that binds successful organizations is an unwavering commitment to workplace safety. Establishing a robust Workplace Safety Program is not merely about compliance; it’s about creating an environment where employees can thrive without fear, where risks are preemptively managed, and where the company’s reputation shines as a beacon of responsibility.
The ten tips we’ve explored are foundational pillars in building this sanctuary of safety. By prioritizing the well-being of every individual, businesses not only foster trust and loyalty among their workforce but also set themselves up for sustainable growth and success. As you chart your organization’s safety journey, remember that the ultimate goal is a harmonious blend of care, compliance, and continuous improvement.