Welding is an essential skill in various industries, from construction and manufacturing to shipbuilding and maintenance. However, welding in confined spaces presents unique challenges and significant safety risks. Confined spaces, such as tanks, boilers, pipes, and tunnels, often lack adequate ventilation and restrict movement, making welding operations more hazardous than in open environments.
This article delves into the hazards associated with welding in confined spaces and outlines best practices to ensure the safety and well-being of welders.
Understanding Confined Spaces
Confined spaces are defined as areas that are typically enclosed by solid walls, lack natural ventilation, have a volume of less than 100 cubic meters of air, and possess at least one dimension (length, width, or height) of less than 2 meters. Common examples include:
- Containers and storage tanks
- Boilers and pressure vessels
- Duct systems and tunnels
- Hollow sections of structures and machinery
- Windowless areas such as basements and crawl spaces
Welding in these environments requires meticulous planning and stringent safety measures due to the inherent limitations and potential hazards.
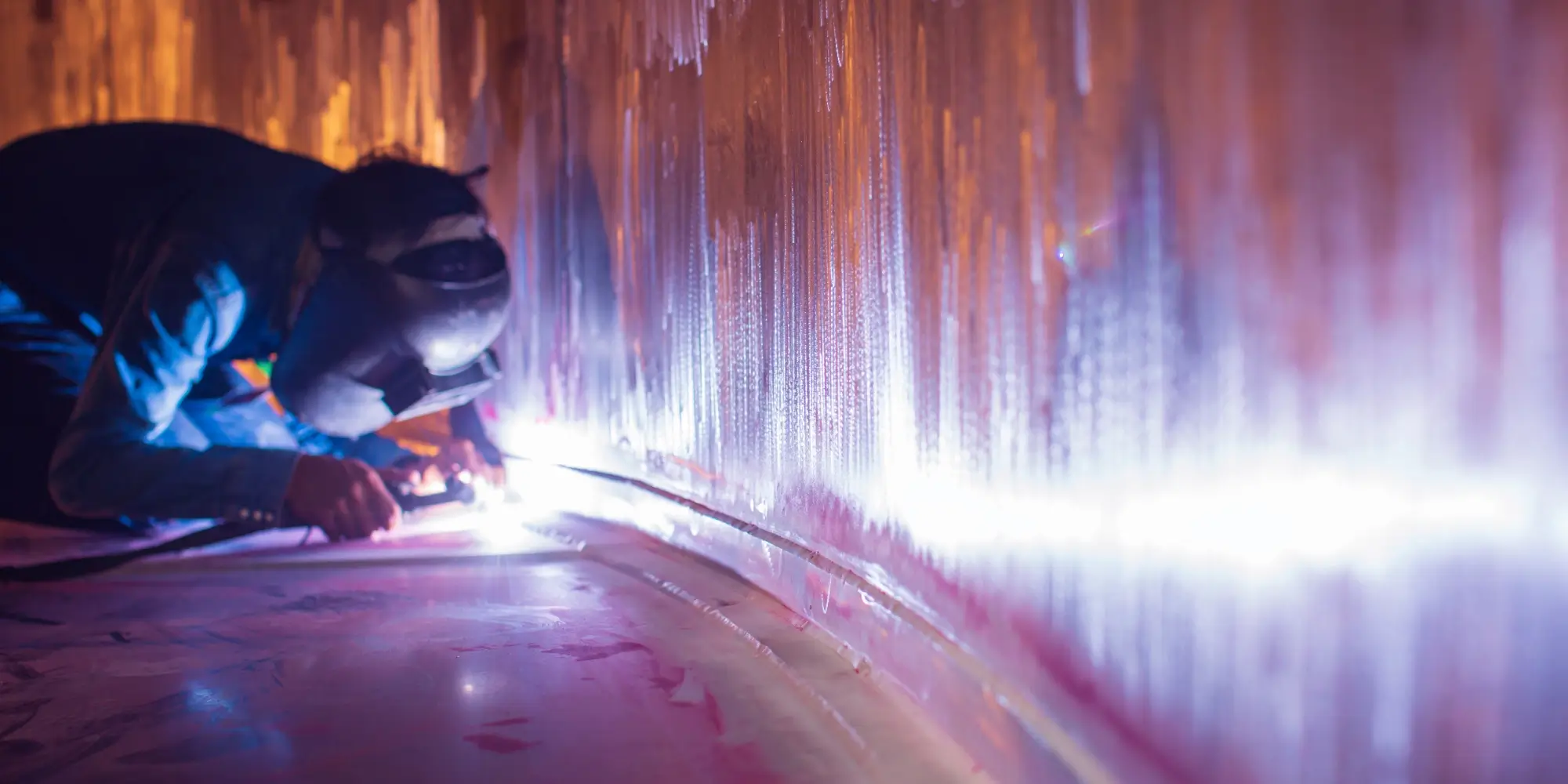
Hazards of Welding in Confined Spaces
Welding in confined spaces introduces a range of hazards that can compromise the safety of welders:
1. Welding Fumes and Gases
Welding processes generate fumes, gases, and dust, including harmful substances like nitrous gases. In confined spaces, these contaminants can quickly accumulate to dangerous levels, posing risks of respiratory issues, fires, deflagrations, or explosions.
2. Fire and Explosion Risks
The presence of flammable gases, steam, dust, and excess oxygen can create a combustible environment. The ignition sources inherent in welding operations increase the likelihood of fires and explosions.
3. Oxygen Imbalance
Maintaining the right oxygen level is critical. Excess oxygen can fuel fires, while oxygen deficiency can lead to suffocation. Using inert gases for material protection can inadvertently reduce oxygen levels if ventilation is inadequate.
4. Heat Buildup
Confined spaces often trap heat generated from welding, leading to elevated temperatures that can cause heat stress or burns.
5. Electrical Hazards
Welding equipment, including electric hand lamps and power sources, pose risks of electrical shocks, especially in environments where moisture or damaged cables are present.
6. Restricted Movement and Forced Postures
Welders may be required to work in uncomfortable or forced positions, increasing the risk of musculoskeletal injuries and reducing the ability to respond effectively in emergencies.
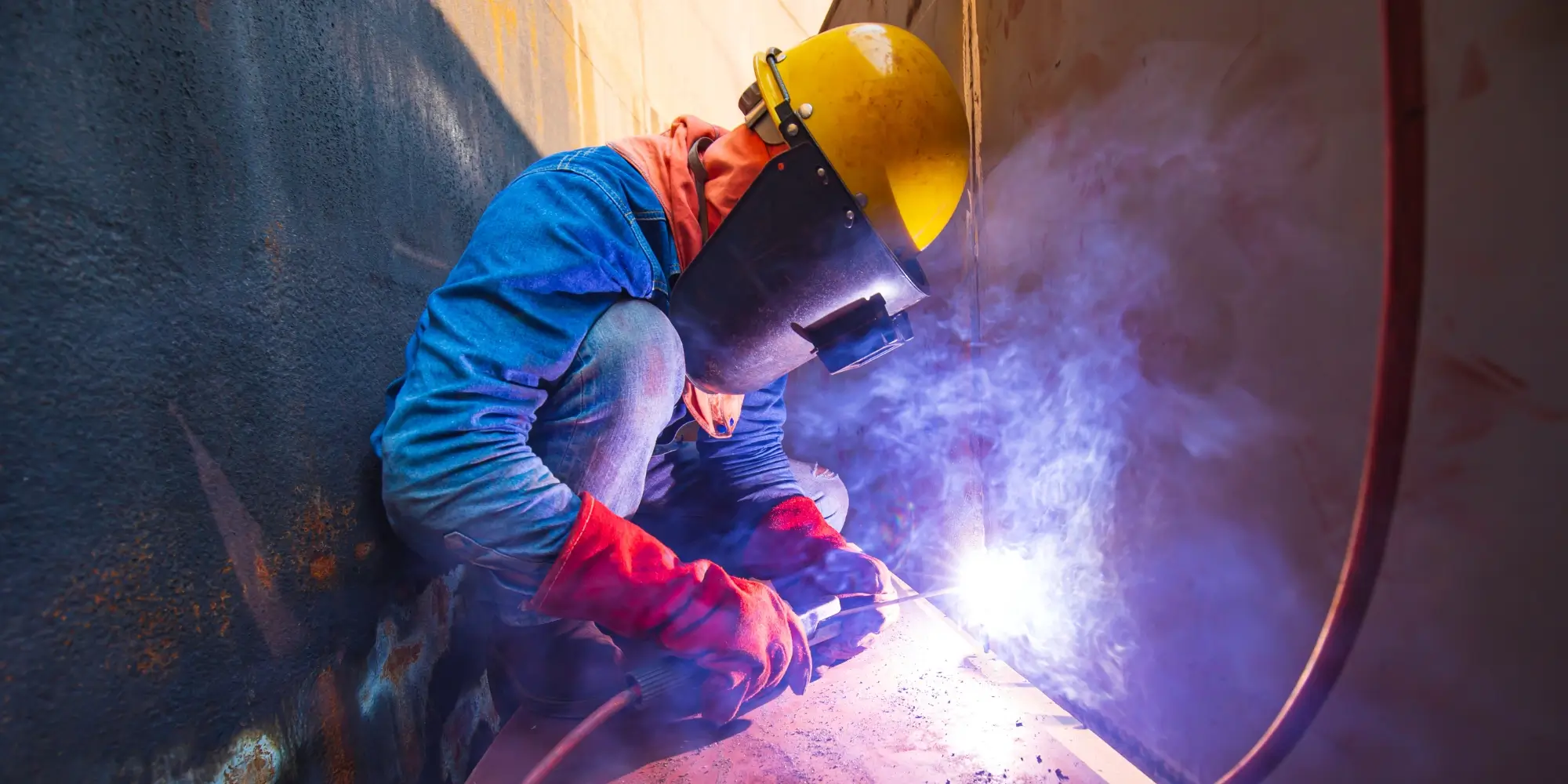
Best Practices for Safe Welding in Confined Spaces
Ensuring safety while welding in confined spaces involves a combination of proper planning, equipment usage, and adherence to safety protocols. Below are essential best practices:
1. Pre-Welding Preparations
- Remove Hazardous Materials: Clear the workspace of any flammable materials, gases, and other potential hazards.
- Inspect Electrical Sources: Ensure that welding power sources are appropriately labeled and identified. Use insulating materials like rubber matting or wooden grating to prevent electrical accidents.
- Manage Gas Emissions: During breaks or when welding is not in progress, disconnect or secure oxy-acetylene cutters and hoses to prevent accidental gas leaks.
- Obtain Written Approvals: Secure necessary permits and approvals from the operating company, outlining specific safety measures for the task.
2. Supervision and Communication
- Designate a Supervisor: Assign a dedicated supervisor responsible for enforcing safety measures and monitoring the welding operations.
- Establish a Safety Post: Appoint a reliable safety attendant outside the confined space to maintain visual or verbal communication with the welder. This person should be trained in safety and rescue operations and ready to seek help if needed.
3. Ventilation and Air Quality Management
- Ensure Adequate Ventilation: Maintain a breathable atmosphere by ensuring an oxygen content of at least 19.5%. Implement effective fume extraction systems, such as spot extraction burners or hoods near the welding site.
- Use Mechanical Ventilators: For spaces where spot extraction is insufficient, employ mechanical ventilators to supply and exhaust air from different locations, ensuring continuous air flow.
- Deploy Respiratory Protection: When ventilation cannot adequately remove contaminants, provide welders with self-contained respirator devices, such as Powered Air-Purifying Respirators (PAPR), which filter out harmful fumes and particles.
4. Personal Protective Equipment (PPE)
- Essential PPE: Equip welders with appropriate PPE, including flame-retardant clothing, gloves, footwear, and respiratory protection.
- Advanced Respiratory Gear: In environments with low oxygen levels or high contamination, use welding helmets with PAPR systems to enhance breathability and reduce heat stress.
5. Emergency Preparedness
- Develop Exit Strategies: Establish clear and accessible exit routes to ensure quick evacuation in case of an emergency.
- Maintain Clear Escape Routes: Keep all escape paths unobstructed and well-marked.
- Provide Safety Equipment: Supply safety belts, lifelines, and other necessary gear to prevent accidents and facilitate rescue operations.
6. Ongoing Monitoring and Maintenance
- Continuous Air Monitoring: Use gas detection instruments to regularly check for hazardous gas levels before and during welding.
- Regular Equipment Checks: Inspect all welding tools and ventilation systems to ensure they are functioning correctly and safely.
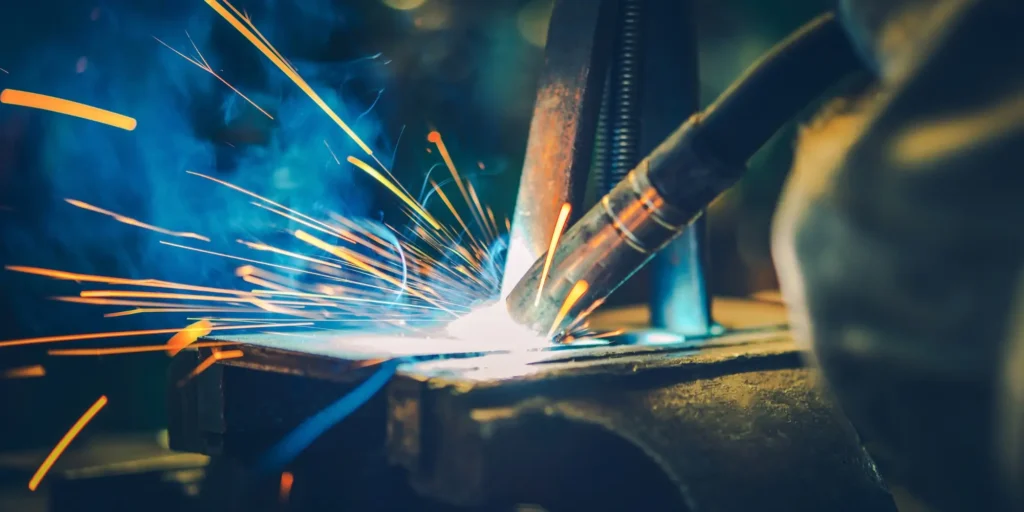
Implementing Ventilation Solutions
Effective ventilation is paramount in maintaining air quality within confined spaces. Here are some strategies:
Spot Extraction vs. General Ventilation
- Spot Extraction: Involves using extraction burners or hoods positioned near the welding site to capture and remove fumes directly.
- General Ventilation: Involves supplying clean air into the confined space while simultaneously exhausting contaminated air from a different location. This method ensures a continuous refresh of the air, typically at a rate of seven air changes per hour.
Ventilation Equipment
Products like the ECKO K2025 Confined Space Blower, Ducting, and Canister offer robust solutions for ventilating confined spaces. These units are designed to withstand harsh environments, providing durable and effective airflow management to prevent oxygen displacement and fume accumulation.
Specific Procedures During Welding
Adhering to specific operational procedures can significantly enhance safety:
- Handling Equipment During Breaks: Disconnect welding machines and secure electrodes and torch valves when not in use to prevent accidental gas leaks or electrical hazards.
- Managing Gas Cylinders: Keep gas cylinders and heavy equipment outside the confined space to minimize clutter and potential hazards inside.
Conclusion
Welding in confined spaces is fraught with challenges that require diligent attention to safety protocols and best practices. By understanding the inherent hazards and implementing comprehensive safety measures—ranging from proper ventilation and PPE usage to effective supervision and emergency preparedness—employers can protect their welders from life-threatening risks. Continuous training, regular equipment maintenance, and a culture of safety are essential to ensure that welding operations in confined spaces are conducted safely and efficiently.
Stay Safe, Stay Informed: Welding in confined spaces demands respect for the environment and adherence to stringent safety standards. Equip your team with the knowledge, tools, and support they need to perform their duties safely, ensuring both their well-being and the success of your projects.