In the ever-evolving landscape of workplace safety, one term consistently stands out as a cornerstone for hazard mitigation: Engineering Controls. These are not just technical jargon thrown around by safety professionals; they represent a proactive approach to ensuring that workers remain protected from potential dangers inherent in their tasks. Rooted in design and innovation, engineering controls target hazards at their source, aiming for elimination or significant reduction.
This blog will delve deep into engineering controls, offering clear definitions, exploring their manifold benefits, and illuminating through real-world examples. Whether you’re a seasoned safety professional or just beginning to navigate the intricacies of workplace health, this guide will provide valuable insights to enhance your understanding and application of engineering controls. Join us on this journey to make workplaces safer and more efficient.
Engineering Controls
Engineering Controls refer to modifications or interventions in the work environment designed to reduce or eliminate workers’ exposure to hazards. These controls focus on addressing the hazard at its source rather than relying on workers to reduce their exposure. They are part of a broader approach to workplace safety, fitting within the Hierarchy of Control Measures.
Examples of engineering controls include the installation of ventilation systems to remove harmful airborne contaminants, placing barriers or shields around moving machinery parts to prevent physical contact, and redesigning workstations to be more ergonomic. Such controls are preferred because they offer direct measures to safeguard workers and often provide more permanent solutions than administrative controls or personal protective equipment (PPE).
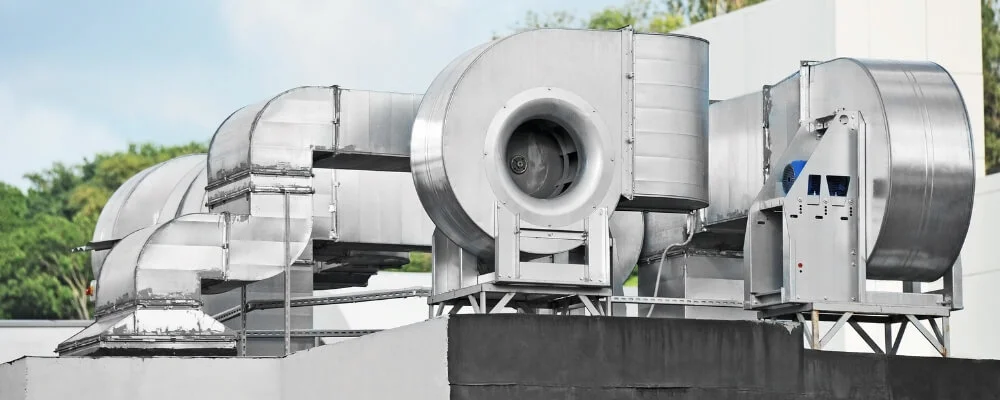
Different Examples Of Engineering Controls
Engineering controls are designed to mitigate or eliminate worker exposure to workplace hazards. Here are different examples of engineering controls:
1. Ventilation Systems
Ventilation systems are crucial in environments where airborne contaminants are present. Local Exhaust Ventilation (LEV), for instance, is designed to capture and remove these contaminants directly from their point of origin. A familiar application of this is the fume hood in laboratories, which actively draws and expels hazardous fumes away from the user.
On the other hand, General/Dilution Ventilation operates on the principle of dilution. It doesn’t remove contaminants at the source but reduces their concentration by mixing them with clean air. Many commercial buildings employ such systems as part of their HVAC to ensure that indoor air remains safe and breathable.
2. Machine Guarding
In industries where machinery operates with moving parts, workers are always injured by coming into direct contact with these parts. Machine guards serve as a protective barrier or enclosure, ensuring that workers are shielded from parts like gears, belts, and chains. Such barriers are instrumental in preventing severe injuries, including cuts or amputations.
3. Ergonomic Design
Ergonomics revolves around designing the workplace environment tailored to human capacities and limitations. By redesigning workstations, tools, or equipment to suit the user better, the risk of musculoskeletal disorders significantly diminishes. For example, introducing adjustable height tables or chairs can prevent back strain and other postural issues, ensuring that workers remain comfortable and health risks are minimized.
4. Isolation
Some hazards are best managed by completely separating them from the workers. This separation can be achieved by constructing soundproof rooms for operations that generate excessive noise. Similarly, processes that involve highly toxic substances or pose severe risks might be isolated in a designated room or building, ensuring that general worker populations are not exposed.
5. Enclosures
Similar to isolation, enclosures involve physical barriers to completely contain a hazard. A robotic assembly line might be fully enclosed to ensure humans don’t accidentally enter its operational space. Another example is glove boxes, often used in labs for handling hazardous materials, where the operator can manipulate the substance inside without direct contact.
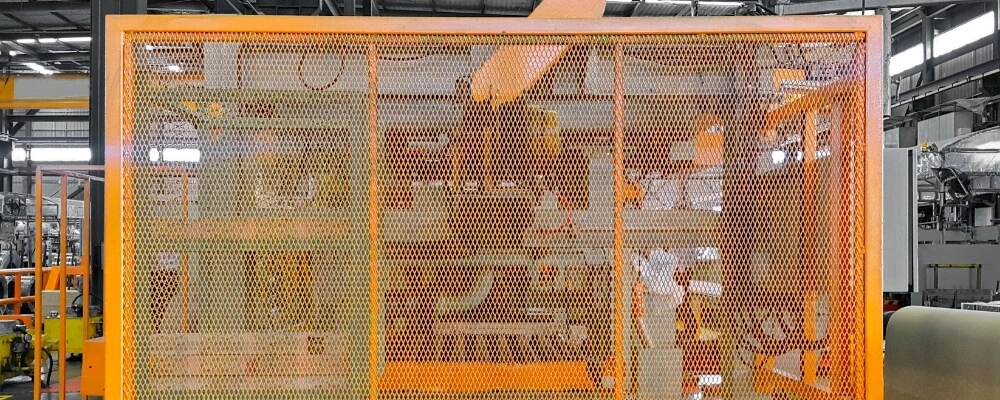
6. Wet Methods
Certain operations, like cutting or grinding, release dust that can pose inhalation risks. Wet methods involve using water or other liquid solutions to suppress the release of such dust. This keeps the air cleaner and significantly reduces the health risks of inhaling harmful particles.
7. Automated Systems
Automation serves a dual purpose – it increases operational efficiency and reduces human exposure to hazards. Robotic systems in automotive industries, which might handle tasks like painting cars, ensure that humans are not exposed to harmful chemicals or the risks of repetitive tasks.
8. Process Modifications
Sometimes, the best way to mitigate risks is by altering how a job or process is executed. This could involve changing task sequences, reducing process temperatures, or adopting a different work method to minimize or eliminate hazards.
9. Interlock Systems
Safety is paramount, and interlock systems are a testament to that. These systems prevent machinery or equipment from operating unless certain safety conditions are met. A household example is a microwave, which will not function unless its door is securely closed.
10. Alarms and Sensors
Proactive safety measures like alarms and sensors are pivotal in warning workers of impending dangers. Devices such as carbon monoxide detectors continuously monitor environments and sound alerts if hazardous gas levels are detected, allowing timely evacuations or interventions.
11. Vibration Control
Prolonged exposure to vibrations, especially in heavy machinery industries, can lead to health issues. Implementing anti-vibration gloves or specialized padding significantly reduces the risk of vibration-induced injuries, ensuring workers’ well-being.
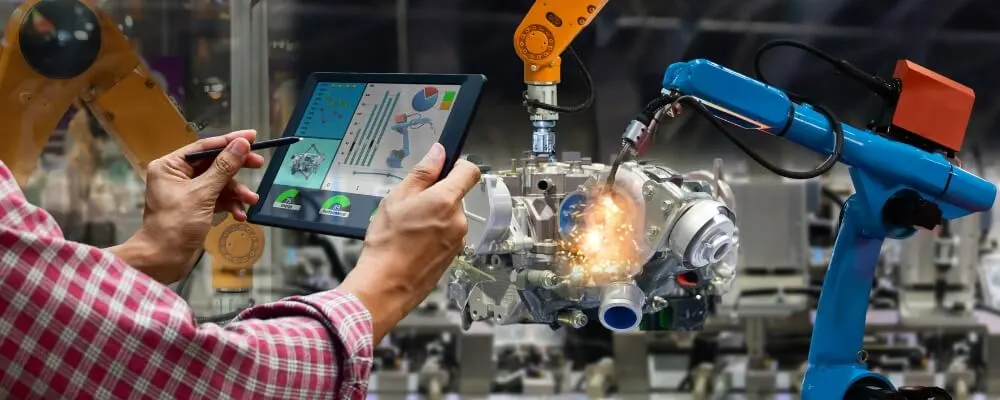
Benefits And Limitations Of Engineering Controls
Benefits of Engineering Controls
- Direct Intervention: Engineering controls address hazards at their source rather than just protecting workers from them. This often leads to a more effective and long-lasting solution.
- Permanent Solutions: Unlike administrative controls or personal protective equipment (PPE), which may need to be repeatedly enforced or worn, engineering controls usually offer more permanent solutions once installed.
- Reduced Dependency on Worker Behavior: Unlike PPE, which requires workers to consistently wear and use it properly, engineering controls function continuously without worker intervention.
- Potential for Increased Productivity: A safer, more ergonomically designed workspace can increase worker productivity and morale.
- Cost Savings in the Long Run: Although the upfront cost can be high, in the long run, the reduction in workplace injuries, illnesses, and associated costs can result in overall savings.
- Enhanced Compliance: Meeting regulatory standards becomes more straightforward when hazards are eliminated or reduced at the source.
Limitations of Engineering Controls
- Upfront Costs: The initial investment required for engineering controls can be high. This includes costs for design, purchase, and installation.
- Maintenance Requirements: Engineering controls require regular maintenance to ensure they remain effective. Over time, without proper maintenance, their efficiency can degrade.
- Potential for New Hazards: Implementing an engineering control could inadvertently introduce new hazards. For example, installing a machine guard might reduce the risk of contact injuries but could lead to overheating if not designed properly.
- Not Always Feasible: In some cases, it might not be possible to implement engineering controls due to space, structural, or operational constraints.
- May Not Address All Risks: While engineering controls can significantly reduce many hazards, they might not eliminate all potential risks, especially if multiple hazards exist.
- Change Management: Implementing engineering controls often requires changes to established processes. Employees need to be trained on the new processes, and resistance to change might occur.
- Time-Consuming Implementation: Designing, procuring, and installing engineering controls can be a lengthy process, especially for complex systems.
In summary, while engineering controls play a pivotal role in hazard mitigation and offer several benefits, it’s essential to recognize their limitations. An effective workplace safety strategy often combines engineering controls with administrative controls and personal protective equipment to comprehensively address all potential hazards.
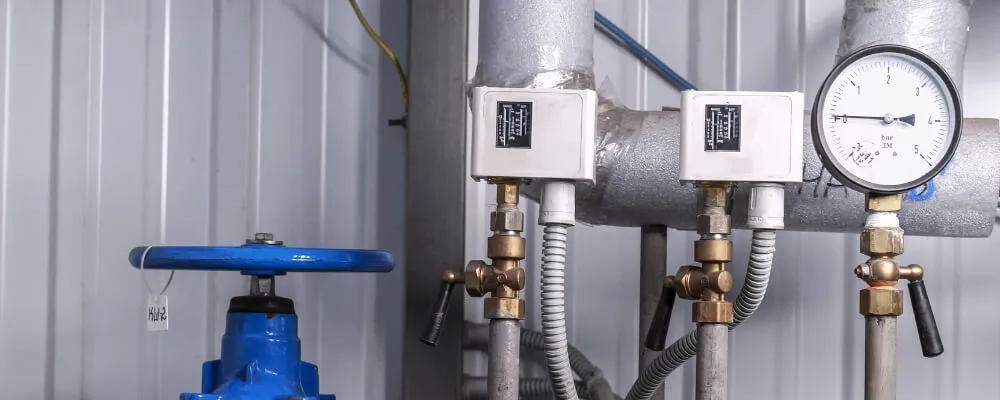
Effectiveness Of Engineering Controls
Engineering controls are widely recognized as one of the most effective means of protecting workers from occupational hazards. Their effectiveness arises from their ability to target the source of the hazard rather than merely addressing its consequences or depending on worker behaviour. Let’s delve into the aspects that highlight the effectiveness of engineering controls:
- Source Elimination or Reduction: Engineering controls aim to eliminate the hazard at its source or significantly reduce its potential for harm. For instance, redesigning equipment to operate without producing harmful emissions eliminates the need for workers to rely on respirators.
- Consistency: Once in place, engineering controls operate continuously without depending on human intervention or behaviour. Unlike PPE, which requires consistent and correct usage by every worker, engineering controls remain consistently effective.
- Broad Protection: While PPE only protects the individual wearing it, engineering controls, such as ventilation systems, can protect all nearby workers.
- Enhanced Work Environment: By addressing ergonomic hazards, engineering controls can lead to more comfortable work environments, reducing fatigue and the potential for musculoskeletal disorders.
- Reduced Long-Term Costs: Despite initial investments, effective engineering controls can reduce medical expenses, compensation claims, and lost workdays in the long run.
- Reliability: High-quality engineering controls, especially when maintained regularly, offer a reliable solution, reducing the likelihood of system failures that could expose workers to hazards.
- Compliance and Regulatory Approval: Implementing engineering controls can make it easier for organizations to meet occupational safety and health standards, as many regulations prioritize or mandate engineering controls over other protective measures.
However, the effectiveness of engineering controls can be compromised if:
- They are not adequately maintained or inspected regularly.
- There is poor initial design or incorrect installation.
- Changes in the work environment or process render them obsolete.
- Workers bypass them, assuming they slow down the work process.
Engineering controls are highly effective because they target hazards at their source and operate consistently. Regular maintenance, periodic reviews, and employee training are essential to ensure they remain effective.
Conclusion
Engineering controls are a testament to the power of proactive design and innovation in workplace safety. Through their strategic application, we can transform hazardous environments into safe havens for workers, mitigating risks right at their inception. As we’ve explored in this blog, the range of these controls is vast, from the complexities of ventilation systems to the simplicity of ergonomic designs. Their benefits, both immediate and long-term, underscore the vital role they play in health and safety strategies across industries.
By understanding and embracing these tools, organizations can ensure compliance with regulations and foster a culture where the well-being of every worker is paramount. As we move forward in an increasingly industrialized world, the importance of engineering controls will only magnify. Let’s continue championing their use, learning from real-world examples, and striving for safer, more efficient work environments.