Navigating the intricacies of workplace safety, one often encounters the term “Administrative Controls.” A vital layer in the hierarchy of hazard prevention, administrative controls serve as a bridge between human actions and the dynamic environments they interact with. This comprehensive guide delves into these controls’ definitions, benefits, and illustrative examples.
Whether you’re a seasoned safety expert or someone keen on understanding the nuances of hazard management, this exploration offers clarity and actionable insights. Dive in as we demystify administrative controls and underscore their role in fostering safer, more efficient work environments.
What are Administrative Controls? Definition
Administrative controls are strategies or procedures that organizations implement to minimize the risk of exposure to workplace hazards. These controls focus on altering or managing tasks rather than changing physical conditions or relying on protective equipment. They often involve creating policies, procedures, or training programs to ensure a safer environment. For example, implementing a policy to rotate workers through a physically demanding job to prevent repetitive strain injuries is administrative control.
The central principle behind administrative controls is to change human behavior and work patterns to reduce risk. While they do not eliminate hazards, they aim to reduce the probability of hazard exposure. For instance, establishing training sessions on safe handling of chemicals doesn’t remove the chemicals but ensures workers understand the risks and precautions. It’s essential to note that while administrative controls can be more flexible and cheaper to implement initially, they require consistent reinforcement, monitoring, and sometimes retraining to remain effective over time.
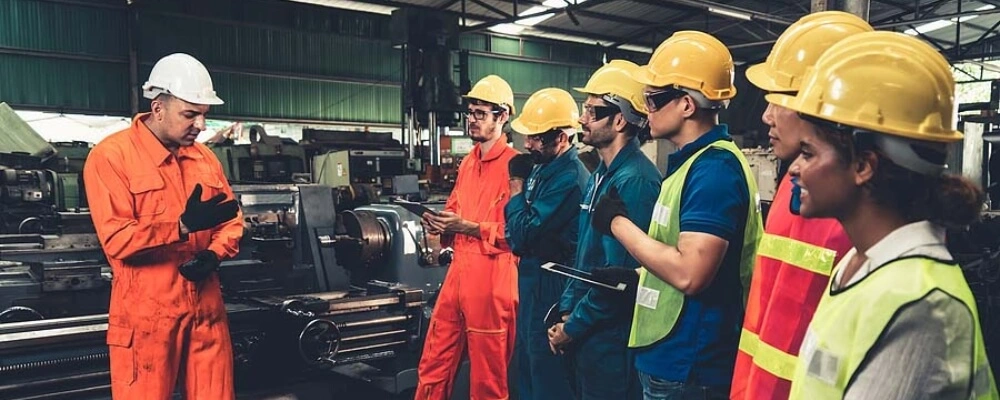
Examples of Administrative Controls
Administrative controls are procedures and policies introduced in the workplace to reduce or prevent exposure to hazards. Here are some examples:
1. Training Programs
Training programs are foundational to workplace safety. They equip employees with the knowledge and skills to execute their tasks without harm. For instance, training sessions may cover proper lifting techniques to avoid back injuries or the correct procedure to handle and store hazardous chemicals. Continuous training ensures that employees remain updated with the latest safety standards and procedures, fostering a safety culture throughout the organization.
2. Work Rotation
Work rotation involves periodically moving employees from one task to another. This minimizes prolonged exposure to specific repetitive tasks or environmental conditions, which can lead to issues like repetitive strain injuries or heat-related illnesses. By rotating duties, workers get a reprieve from repetitive tasks, reducing wear and tear on specific muscle groups or minimizing mental fatigue.
3. Break Policies
Mandated breaks are critical in professions that demand intense physical labor or high concentration. Regular rest intervals can prevent fatigue, which significantly contributes to workplace accidents. Breaks also allow workers to hydrate, rest their eyes, or stretch, promoting overall well-being.
4. Exposure Monitoring
This involves monitoring the amount of hazardous substances or radiation workers are exposed to. Employers can ensure they are within permissible limits by regularly checking and documenting levels. Devices like dosimeters for radiation or air sampling devices for airborne chemicals can help in real-time monitoring.
5. Restricted Access
Not every area within a workplace is safe for all employees. Some areas, especially those housing hazardous materials or machinery, should be accessible only to trained personnel. By restricting access, employers ensure that only those with adequate training and knowledge handle potential hazards, thereby reducing the risk of accidents.
6. Operating Procedures
Having a standardized operating procedure ensures consistency in task execution, reducing errors. For instance, a standardized procedure for operating heavy machinery can guide workers through each step, ensuring they don’t miss any safety precautions.
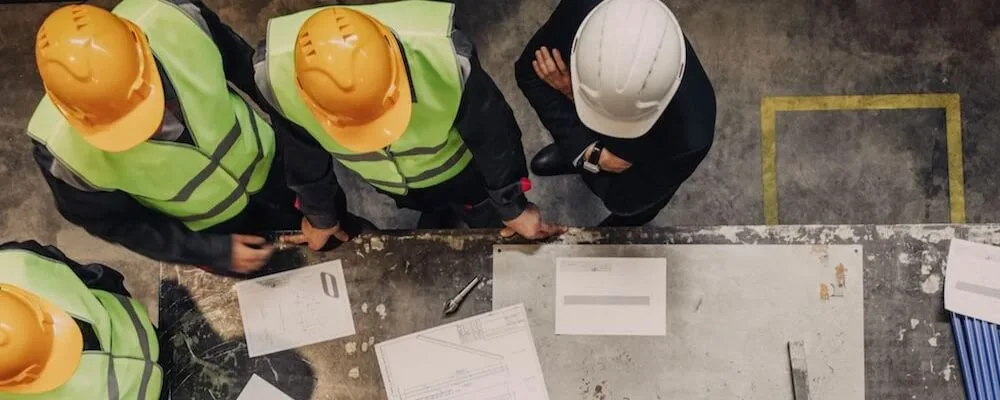
7. Emergency Protocols
Emergencies, such as fires or chemical spills, require swift and organized action. Pre-established emergency protocols offer clear guidelines for taking steps, minimizing panic and chaos. Regular drills can help employees familiarize themselves with these protocols.
8. Preventive Maintenance
Machinery and equipment, if not maintained, can malfunction, leading to accidents. Scheduled maintenance checks ensure everything is in working order, reducing the risk of unexpected breakdowns or hazards.
9. Housekeeping Policies
A clean workspace is a safe workspace. Regular cleaning, organizing, and decluttering can prevent accidents like trips or falls. Moreover, proper disposal of waste, especially hazardous waste, can prevent fires or exposure to toxic substances.
10. Shift Design
Designing shifts thoughtfully can significantly impact worker health and safety. Long, continuous shifts can lead to fatigue, reducing alertness. Additionally, working during extreme temperatures, either hot or cold, can pose health risks. Adjusting shift timings or durations can mitigate these risks.
11. Communication Protocols
Effective communication is key in any workplace. Whether it’s about a new hazard, a change in procedure, or employee feedback, having a clear communication protocol ensures everyone is on the same page, reducing misunderstandings and potential risks.
12. Safety Signage
Visual cues, like signs, can act as instant reminders for workers. Signs indicating high noise levels, areas requiring protective gear, or directions during emergencies can provide quick guidance, enhancing overall safety.
In essence, these administrative controls, when implemented effectively, contribute significantly to a safer and more efficient workplace. They focus on the human aspect of operations, ensuring that every individual is protected, informed, and trained to face workplace challenges.
In essence, administrative controls are about changing the way people work rather than modifying the physical work environment or providing protective equipment. They play a crucial role in a holistic approach to workplace safety.
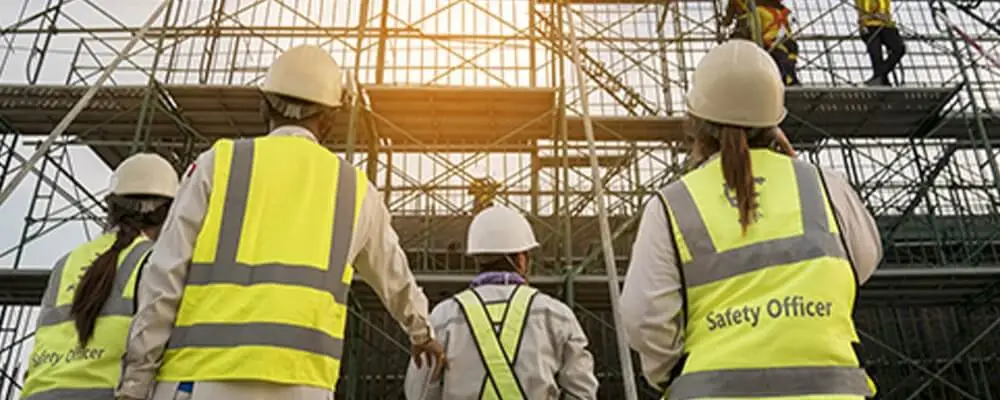
Benefits and Limitations Of Administrative Controls
Benefits of Administrative Controls:
- Flexibility: Administrative controls can quickly adapt to different situations and environments. They offer solutions that can be tailored to the specific needs of a workplace or task.
- Engagement: These controls often involve worker participation in developing and implementing policies and procedures. This involvement can lead to increased buy-in and commitment from employees.
- Cost-effective: In many cases, administrative controls can be implemented with little to no capital outlay, especially compared to engineering controls.
- Comprehensive: Administrative controls often take a holistic approach to safety, addressing multiple facets of a potential hazard, from training and education to work practices and emergency response.
- Promotes Safety Culture: Regular training sessions, safety meetings, and other administrative measures foster a culture of safety awareness and continuous improvement within an organization.
Limitations of Administrative Controls:
- Reliance on Human Behavior: These controls depend on workers consistently following established procedures and practices. Human error, non-compliance, or misunderstanding can compromise their effectiveness.
- Potentially High Maintenance: Administrative controls may require ongoing training, re-certification, and monitoring, which can be time-consuming and costly in the long run.
- May Not Eliminate the Hazard: While they can reduce the risk, administrative controls often do not eliminate the source of the hazard, unlike some engineering controls or elimination methods.
- Inconsistency: Due to variations in understanding, interpretation, or implementation, there might be inconsistencies in how different workers or departments apply the controls.
- Temporary Solutions: In some cases, administrative controls can be considered band-aid solutions. They might address the immediate risk but not provide long-term solutions to root causes.
- Complexity: As workplaces grow and evolve, administrative measures might become complex, potentially leading to confusion or lack of clarity among workers.
In conclusion, while administrative controls are crucial in managing workplace hazards, they are most effective when used with other control measures. An integrated approach that includes elimination, engineering, personal protective equipment, and administrative controls ensures a comprehensive and effective safety strategy.
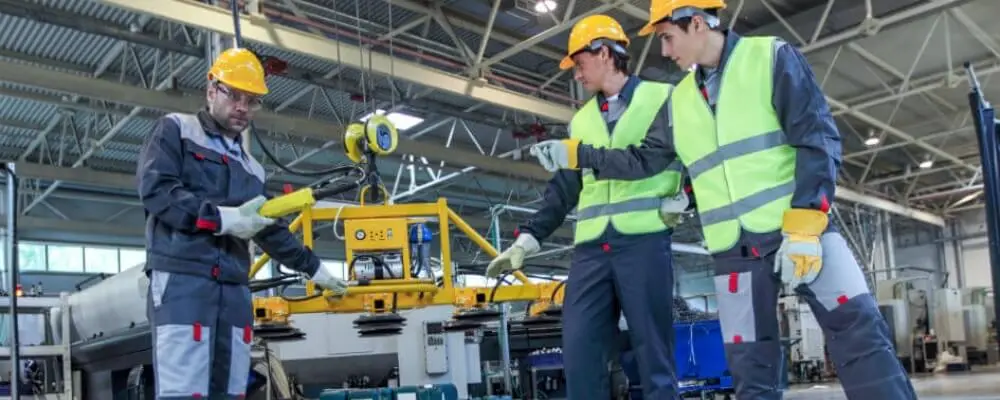
Effectiveness Of Administrative Controls
The effectiveness of administrative controls in managing workplace hazards varies based on several factors. Here’s an overview:
- Nature of the Hazard: Some hazards are more suitably addressed through administrative controls than others. For example, limiting exposure to repetitive tasks through work rotation can reduce the risk of repetitive strain injuries. However, relying solely on administrative controls may be inadequate for more direct hazards, such as exposure to toxic substances.
- Implementation and Compliance: The effectiveness of administrative controls hinges largely on proper implementation and consistent compliance. If workers are not adequately trained or there’s a lack of enforcement, these controls can become ineffective.
- Integration with Other Controls: Administrative controls are often more effective when used with other types of controls, such as engineering controls or personal protective equipment. For instance, training workers on the safe use of machinery (an administrative control) is more effective when the machinery has safety features (engineering control) and workers use the required protective gear.
- Flexibility and Adaptability: One strength of administrative controls is their flexibility. They can be rapidly adapted to changing conditions or new information. This adaptability can make them particularly effective in dynamic environments or when facing novel hazards.
- Frequency of Review and Update: To remain effective, administrative controls need regular review and updating. As work conditions change, technologies evolve, or new research emerges, controls should be revised to maintain or enhance their effectiveness.
- Cultural Fit: Workplace culture can influence administrative controls’ effectiveness. Administrative controls will likely be more successful in a culture prioritizing safety and where employees feel empowered to voice concerns or provide feedback.
- Feedback Mechanisms: Effective administrative controls often include feedback mechanisms allowing continuous improvement. Regular safety audits, incident reports, and worker feedback can highlight areas where controls might fail, or enhancements are needed.
- Clarity and Communication: For administrative controls to be effective, they must be clearly communicated to all involved. This means that instructions, guidelines, and protocols must be easily understandable and accessible.
In summary, the effectiveness of administrative controls is multifaceted and dependent on various factors. While they play a vital role in the hierarchy of controls, their success is influenced by how they are implemented, maintained, and integrated within a broader safety strategy.
Conclusion
In the multifaceted realm of workplace safety, administrative controls stand out as a pivotal component. Through our exploration of their definitions, benefits, and examples, it becomes evident that these controls play an indispensable role in shaping safer work environments. They offer a dynamic approach to hazard management by focusing on human behaviors and procedures and highlight the importance of continuous training, evaluation, and adaptability.
While they are just one layer in the comprehensive hierarchy of hazard controls, administrative controls undeniably hold significant sway in mitigating risks and promoting a safety culture. As we venture into an era where work environments continue to evolve, understanding and effectively implementing these controls will ensure a harmonious balance between productivity and safety.