Falls are one of the leading causes of serious injuries and fatalities in the workplace, especially in high-risk industries like construction, utilities, and maintenance. Preventing these incidents isn’t just a safety measure; it’s a legal and ethical responsibility. That’s where a Fall Protection Plan (FPP) comes into play.
A Fall Protection Plan is more than a checklist—it’s a structured, evolving safety strategy designed to prevent falls and ensure worker safety in elevated or hazardous work environments. Whether you’re a safety officer, site supervisor, or business owner, understanding what an FPP is, when it’s required, and how to implement and maintain it is essential.
In this blog guide, we’ll break down:
- What a Fall Protection Plan is and why it matters
- The key elements of an effective FPP
- Where and when it’s legally required
- How to keep your plan updated and compliant
- Legal obligations and penalties for non-compliance
By the end, you’ll have a clear roadmap for protecting your workforce, reducing liability, and staying ahead of regulatory demands. Let’s get started.
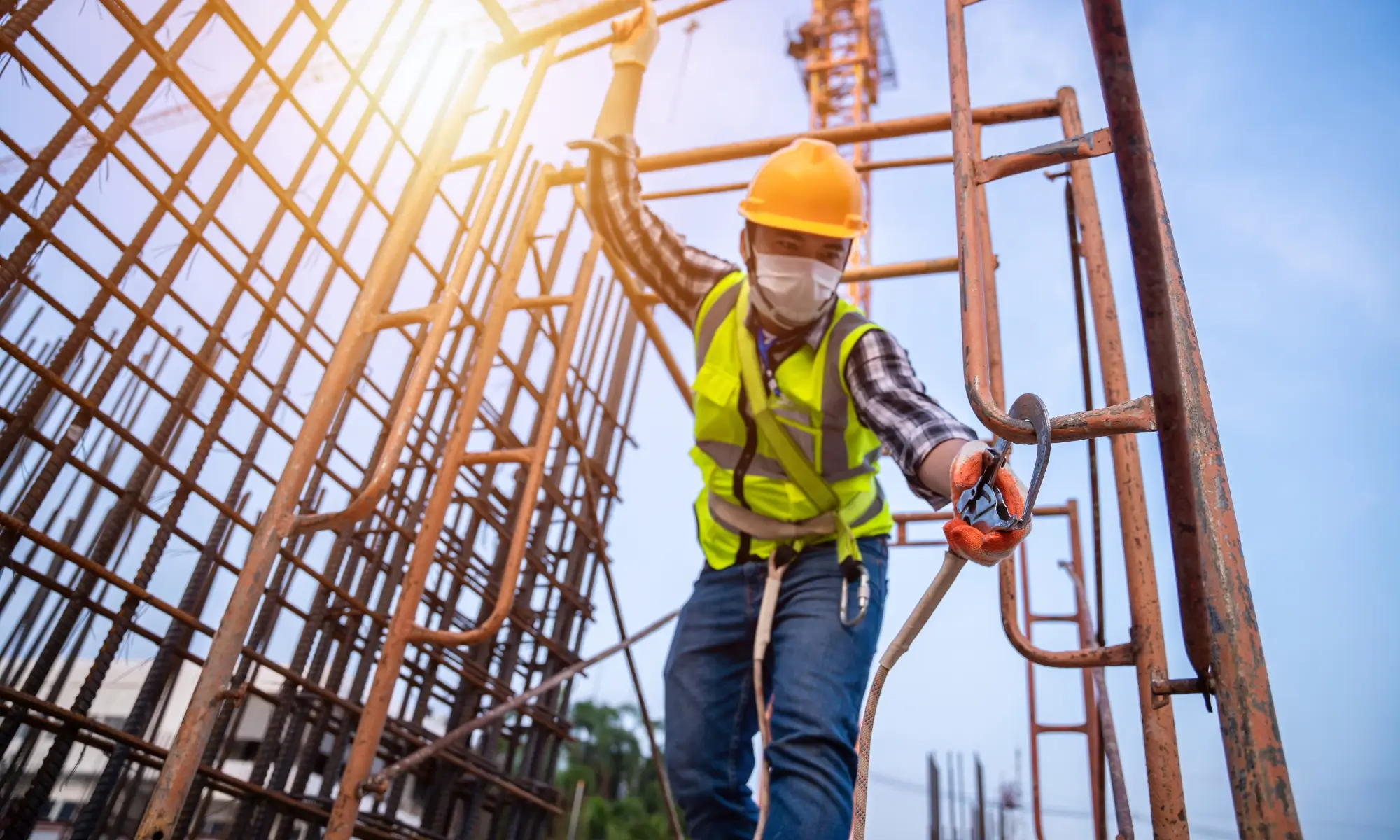
What is a Fall Protection Plan?
A Fall Protection Plan (FPP) is a formal, written document outlining procedures, equipment, training, and emergency protocols to prevent falls and protect workers exposed to fall hazards. More than just a checklist, an FPP is a dynamic framework that evolves with jobsite conditions, new equipment, and updated safety standards.
Why Is a Fall Protection Plan Important?
- Protecting Lives: Falls to a lower level accounted for over 700 worker deaths and more than 120,000 injuries in recent years. A fall protection plan directly addresses this risk with preventative and responsive strategies.
- Legal and Regulatory Compliance: Organizations must implement fall protection under laws like OSHA (in the U.S.) and other international or local standards. Non-compliance can result in hefty fines, legal action, and shutdowns.
- Reducing Organizational Liability: By clearly defining roles, responsibilities, and equipment use, an FPP minimizes legal exposure after incidents and helps organizations demonstrate due diligence.
Core Objectives of a Fall Protection Plan (FPP)
- Identify potential fall hazards
- Implement preventive measures and control systems
- Train all affected employees
- Prepare for emergencies and rescue
- Ensure regular inspection and equipment maintenance
- Stay compliant with legal standards
- Update the plan as conditions change
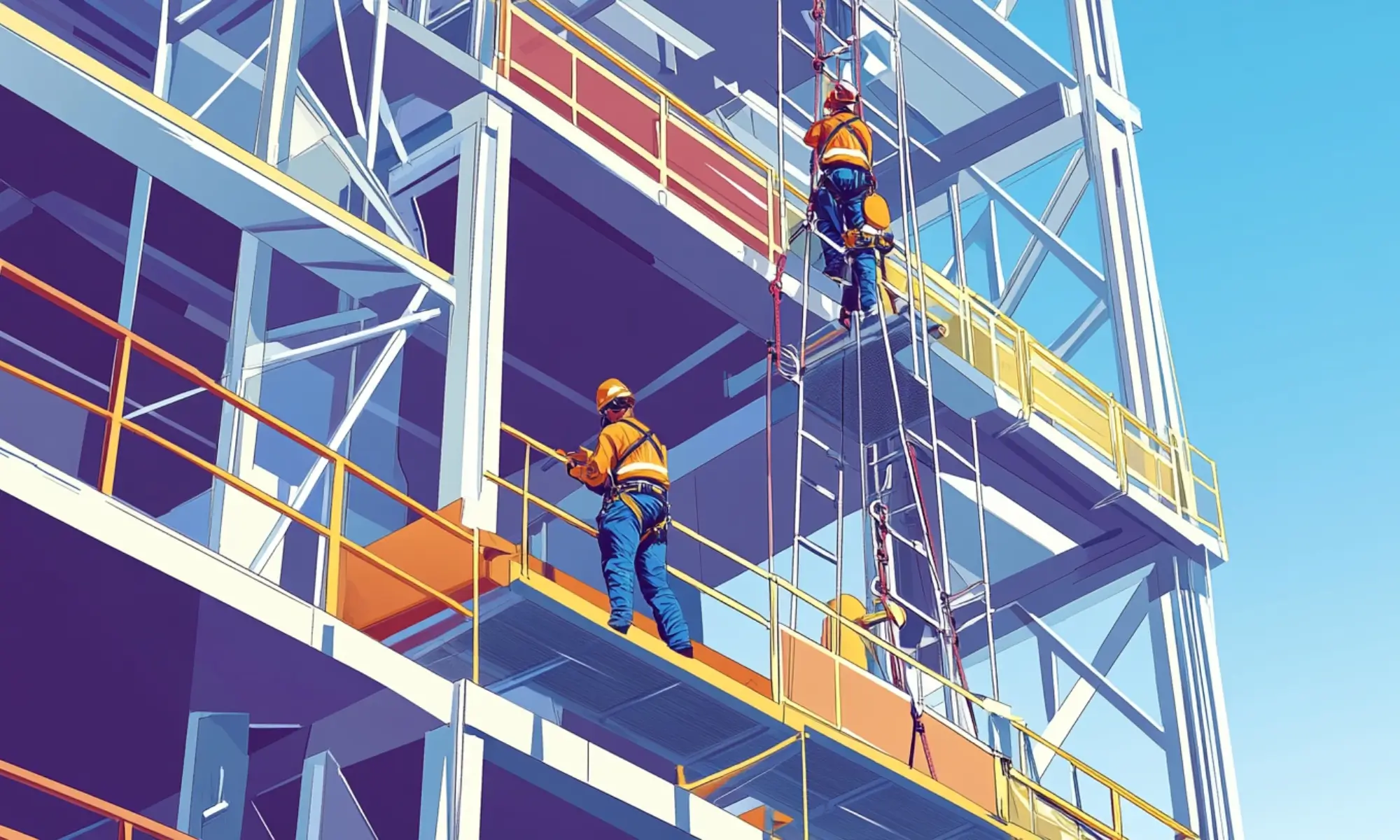
Key Elements of an Effective Fall Protection Plan (FPP)
A strong Fall Protection Plan (FPP) isn’t just about wearing a harness—it’s a comprehensive system designed to prevent falls, reduce risk, and protect lives. To be effective, your FPP must include several essential components that work together to identify hazards, implement controls, and prepare for emergencies. Here are the key elements every Fall Protection Plan should have:
1. Hazard Identification and Risk Assessment
Start by evaluating all areas where workers may be exposed to fall hazards. Identify:
- Unprotected edges
- Roofs, scaffolds, and ladders
- Floor openings or skylights
- Elevated platforms or machinery
Conduct site-specific risk assessments to determine:
- The likelihood of a fall
- The severity of potential injuries
- Which tasks and locations pose the highest risk
2. Preventive and Control Measures
Apply the hierarchy of controls to eliminate or minimize risks:
- Eliminate the hazard (e.g., do the work at ground level if possible)
- Use engineering controls like guardrails or safety nets
- Implement administrative controls like work rotation and safety signage
- Provide personal protective equipment (PPE) such as harnesses and lifelines when hazards can’t be removed
3. Selection and Use of Fall Protection Systems
Choose appropriate systems based on the task, location, and environment. These may include:
- Guardrails (passive protection)
- Fall restraint systems are used to prevent reaching a hazard
- Fall arrest systems are used to stop a fall in progress
- Safety nets under elevated work areas
- Positioning systems for vertical or sloped surfaces
Ensure all equipment meets national safety standards and is installed by qualified personnel.
4. Training Requirements
Workers must be trained by a competent person in:
- Recognizing fall hazards
- Using fall protection systems and equipment correctly
- Inspecting gear before use
- Responding to emergencies
Refresher training should be conducted regularly or when:
- New equipment is introduced
- There’s a change in jobsite conditions
- An employee demonstrates unsafe practices
5. Equipment Inspection and Maintenance
Establish protocols for:
- Pre-use inspections by workers
- Scheduled inspections by trained personnel
- Record-keeping of inspection dates and findings
Immediately remove any damaged or expired equipment from service and replace as needed. Equipment must also be stored properly to maintain its integrity.
6. Emergency Response and Rescue Plan
If a fall occurs, time is critical. Your plan should outline:
- Rescue procedures for retrieving suspended workers
- Designated rescue personnel and their training
- Necessary rescue equipment on-site
- Communication protocols with emergency services
Practice rescue drills regularly to ensure everyone knows their role.
7. Documentation and Record-Keeping
Maintain detailed records of:
- Fall hazard assessments
- Safety meetings and toolbox talks
- Training and certification
- Equipment inspections and maintenance
- Incidents and near-miss reports
Proper documentation demonstrates due diligence and is essential for audits and investigations.
An effective Fall Protection Plan is a living document—it should be reviewed regularly, updated as conditions change, and tailored to your specific worksite. When these key elements are fully integrated, you protect your team and create a safer, more accountable workplace.
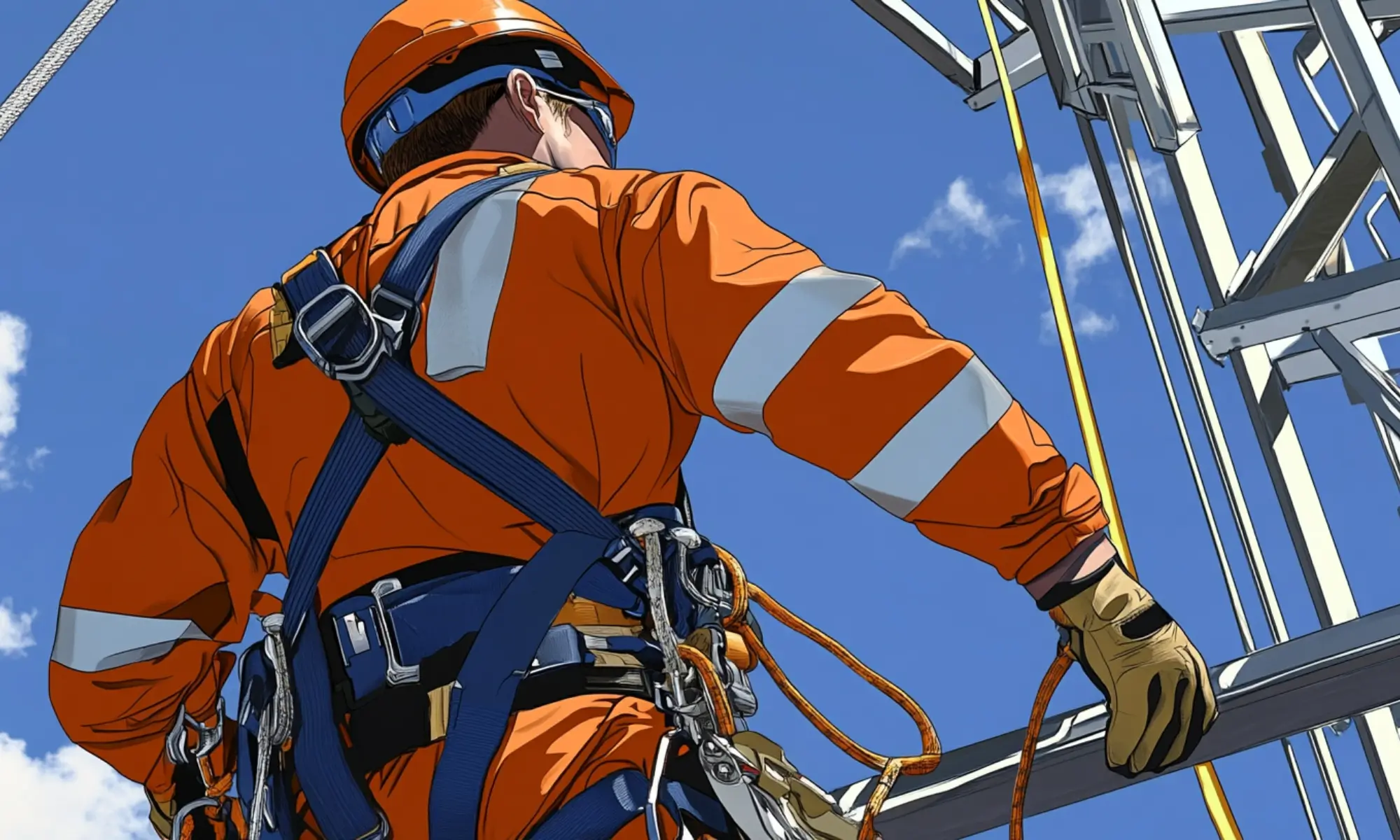
When and Where Is a Fall Protection Plan (FPP) Required?
A Fall Protection Plan (FPP) is legally required when workers are exposed to fall hazards that could result in injury or death. The specific requirements vary by jurisdiction, but here are the most common situations where an FPP becomes mandatory:
When is it required?
Fall protection is required when workers are exposed to a fall height threshold, which varies depending on the type of work:
- 4 feet (1.2 meters) in general industry settings (according to OSHA).
- 6 feet (1.8 meters) in the construction industry.
- 10 feet (3 meters) or more when working on scaffolding.
- Regardless of height if working over dangerous equipment or materials (e.g., machinery, sharp objects, toxic substances).
Trigger points for requiring a Fall Protection Plan include:
- Elevated platforms or unprotected edges
- Ladders or scaffolding work
- Roof work (especially sloped or wet surfaces)
- Leading-edge construction
- Bridge or tower maintenance
- Openings like skylights or floor holes
Where is it required?
A Fall Protection Plan must be in place wherever fall risks exist, including:
- Construction sites: The most common environment, especially for roofers, framers, or steelworkers.
- Manufacturing plants and warehouses: Elevated storage platforms, loading docks, or catwalks.
- Telecommunication and utility sectors: Tower climbing and pole work.
- Oil and gas facilities: Rig platforms, derricks, and confined space entry points.
- Mining and tunneling: Shaft openings and vertical ladders.
- Maintenance operations: Window cleaning, HVAC service on rooftops, etc.
Legal Backing
Regulatory bodies like OSHA (U.S.), HSE (UK), or CCOHS (Canada) legally enforce fall protection standards. Employers are responsible for:
- Assessing fall risks in all work environments
- Providing a written fall protection plan
- Ensuring workers are trained and equipped
Failure to comply can result in citations, penalties, and serious legal consequences if an incident occurs.
In short, if there’s a risk of falling and getting injured, a Fall Protection Plan isn’t just best practice—it’s mandatory. It’s your blueprint for protecting workers, complying with the law, and maintaining a safe, productive workplace.
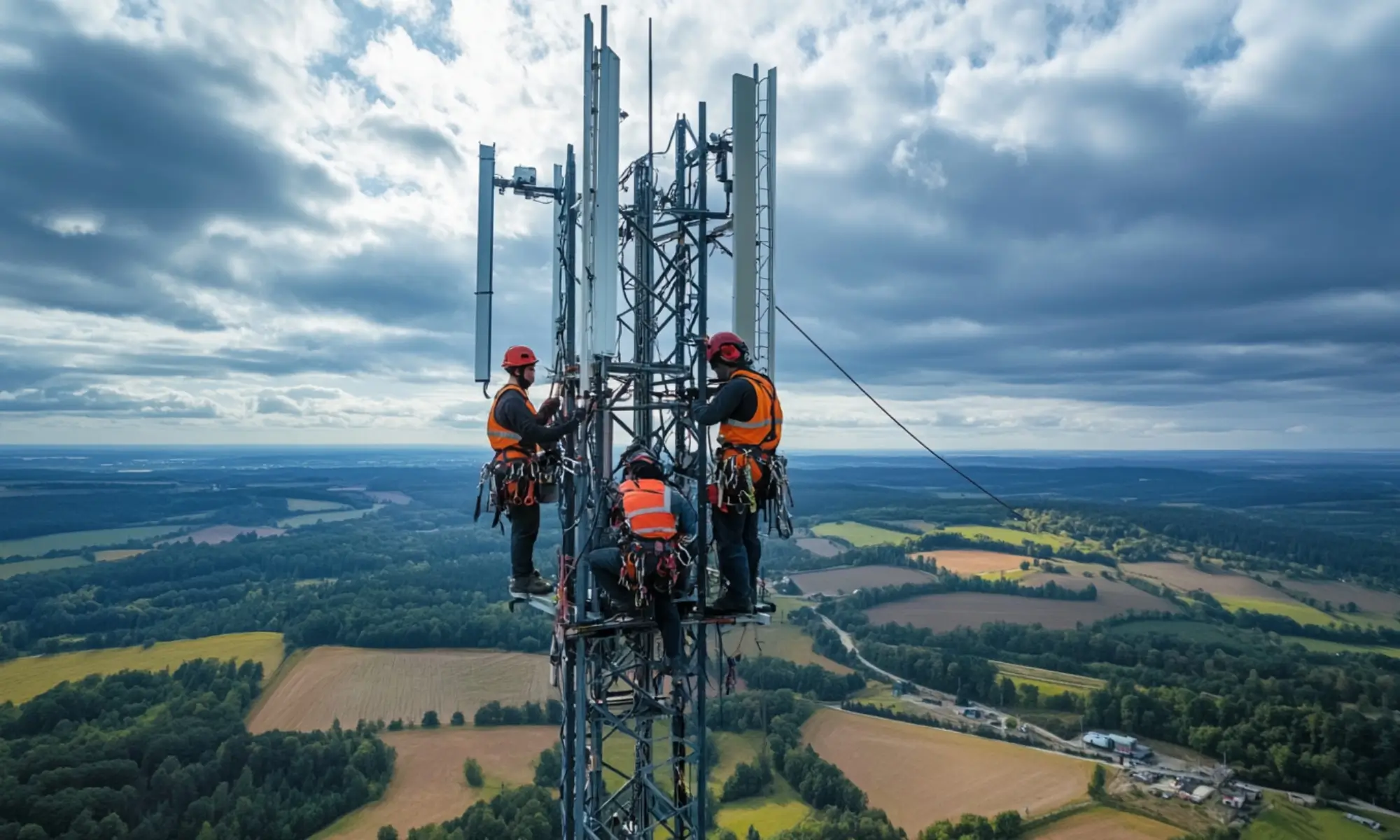
How to Keep Your Fall Protection Plan Updated
A Fall Protection Plan (FPP) is not a “set-it-and-forget-it” document—it must evolve with your workplace to remain effective and compliant. Keeping it up to date ensures you’re prepared for new hazards, meet regulatory requirements, and continuously improve safety performance.
Here’s how to keep your Fall Protection Plan current and effective:
1. Conduct Regular Plan Reviews
Review your FPP at least once a year—more often for high-risk industries like construction or roofing. During each review:
- Reassess fall hazards based on recent job activities
- Confirm that control measures are still effective
- Check if the safety responsibilities and contact personnel are still accurate
These periodic reviews ensure the plan reflects your current work environment.
2. Update After Changes to the Worksite or Equipment
Any modification to the physical layout of your site, work processes, or introduction of new equipment may introduce new fall risks. Your FPP should be updated to:
- Address new or altered hazards
- Include training on newly introduced equipment
- Adjust rescue procedures if work locations or access routes have changed
Always treat site changes as a trigger to review and revise the plan.
3. Analyze Incidents and Near Misses
If a fall, close call, or safety violation occurs, investigate the root cause thoroughly. Use the findings to:
- Modify hazard assessments
- Improve fall protection methods
- Strengthen training or emergency response protocols
This proactive approach helps prevent repeat incidents and strengthens your safety culture.
4. Stay Aligned with Regulations and Standards
Safety regulations evolve. Regularly check updates from:
- OSHA (or your country’s safety authority)
- ANSI/CSA standards
- Industry best practices
When a new regulation comes into effect—such as a change in minimum fall distance or equipment certification—your FPP should be revised immediately to stay compliant.
5. Include Worker Feedback and Field Observations
Encourage open communication with your workers. They often spot issues before they become incidents. Use feedback from:
- Toolbox talks
- Safety meetings
- On-site observations
This keeps your plan grounded in reality and relevant to actual working conditions.
Keeping your Fall Protection Plan updated is about staying proactive. Regular reviews, responsiveness to change, learning from experience, and compliance tracking are all essential to ensure your plan protects lives and meets legal expectations. A well-maintained FPP is the foundation of a safe, responsible, and resilient workplace.
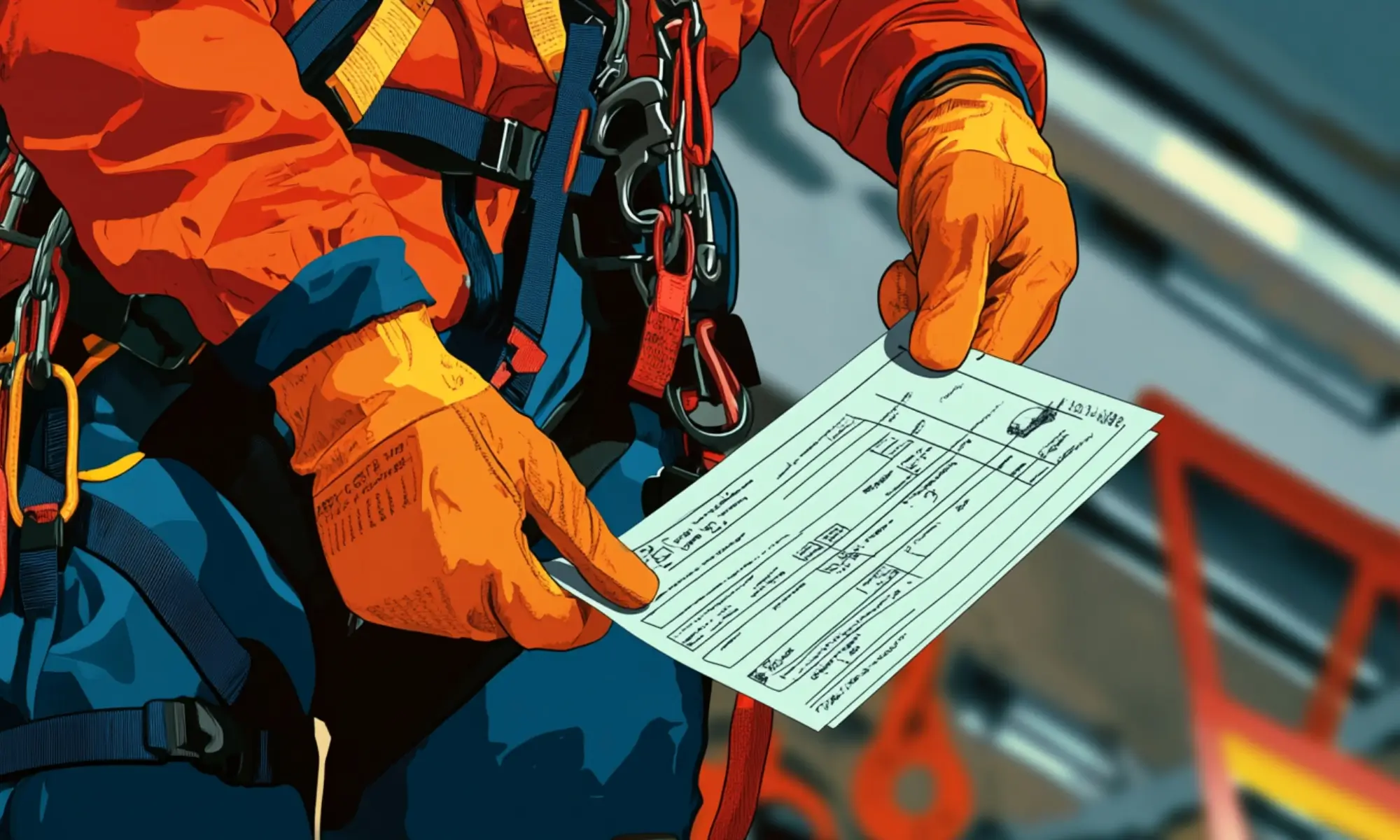
Compliance and Legal Considerations
OSHA and Beyond
In the U.S., OSHA mandates fall protection under Standard 1926.501. Other countries have their own safety agencies with similar expectations.
Ensuring Your Plan Meets Legal Requirements
- Use competent and qualified persons for system design and training
- Update plans regularly
- Keep training and inspection records
- Follow the manufacturer and legal guidelines for equipment
Penalties for Non-Compliance
Fines for failing to meet fall protection requirements can exceed $15,000 per violation, and in some fatality cases, criminal charges may apply.
Conclusion
A well-developed Fall Protection Plan (FPP) is more than a regulatory requirement—it’s a life-saving strategy that reflects your commitment to workplace safety. By identifying hazards, selecting the right protection systems, ensuring proper training, and preparing for emergencies, an FPP creates a structured approach to preventing falls and reducing risk.
Keeping your plan updated, compliant, and responsive to changing worksite conditions is essential. From routine reviews to incorporating lessons from near misses, a proactive FPP supports a culture of safety, minimizes liability, and ensures your workforce can operate with confidence.
Whether managing a construction site, maintaining elevated equipment, or operating in any environment where fall hazards exist, your Fall Protection Plan should be your blueprint for protecting people and preventing tragedies.
Make fall protection a priority—because safety from the top down saves lives.