Safety should always be the top priority in any workplace where hazardous chemicals are used or stored. A significant aspect of maintaining a safe environment involves effective communication about these hazards. The Occupational Safety and Health Administration (OSHA) has a Hazard Communication Standard (HCS), 29 CFR 1910.1200, that mandates all employers to develop and implement a hazard communication program. This program plays a vital role in ensuring that everyone in the workplace understands the risks they face and how to protect themselves.
Creating an effective hazard communication program can seem daunting, but it is entirely achievable with careful planning and systematic implementation. This blog post is designed to guide you through this process step by step. From learning the standard and identifying responsible staff to preparing a written hazard communication plan, labeling containers, maintaining Safety Data Sheets (SDSs), training employees, and evaluating and reassessing your program—each step plays a crucial role in fostering a safe, informed, and prepared working environment.
Follow these six steps to build an effective hazard communication program, ensuring compliance with OSHA’s standards and, most importantly, keeping your employees safe. Let’s explore each of these steps in more detail.
Steps To An Effective Hazard Communication Program
Creating a safe workplace is paramount, particularly in industries where hazardous chemicals are used or stored. Clear communication regarding these hazards is an integral part of this safety protocol. Employers can implement an effective hazard communication program by following these six steps:
Step 1: Learn the Standard/Identify Responsible Staff
The initial step towards an effective hazard communication program involves an in-depth understanding of OSHA’s Hazard Communication Standard and assigning roles to responsible staff.
Understanding the Hazard Communication Standard
First, you need to obtain a copy of OSHA’s Hazard Communication Standard, accessed from OSHA’s hazard communication webpage at www.osha.gov/hazcom. This document is vital as it outlines the workplace’s guidelines for handling hazardous materials. To effectively implement the program, it is crucial to fully comprehend the provisions and rules laid out in this standard.
The most relevant sections to the employers dealing with chemicals in their workplaces are primarily contained in paragraphs (e), (f), (g), and (h) of the document. These paragraphs encompass the written hazard communication program, labels and other forms of warnings, safety data sheets, and employee information and training, respectively. By thoroughly studying these sections, you can determine the requirements for compliance in your workplace.
Identifying Responsible Staff
Once you’ve grasped the requirements of the Hazard Communication Standard, the next step is to identify and assign a person or a team who will be primarily responsible for coordinating the implementation of the hazard communication program. This individual or team will oversee the whole process, ensuring all parts of the program are properly carried out.
The coordinator should have a comprehensive understanding of the Hazard Communication Standard and must be able to make crucial decisions about the program’s execution. They must be able to identify and delegate roles to staff members for different activities such as training. This might involve determining who best suits certain roles, assigning them, and ensuring the assigned individuals know their responsibilities.
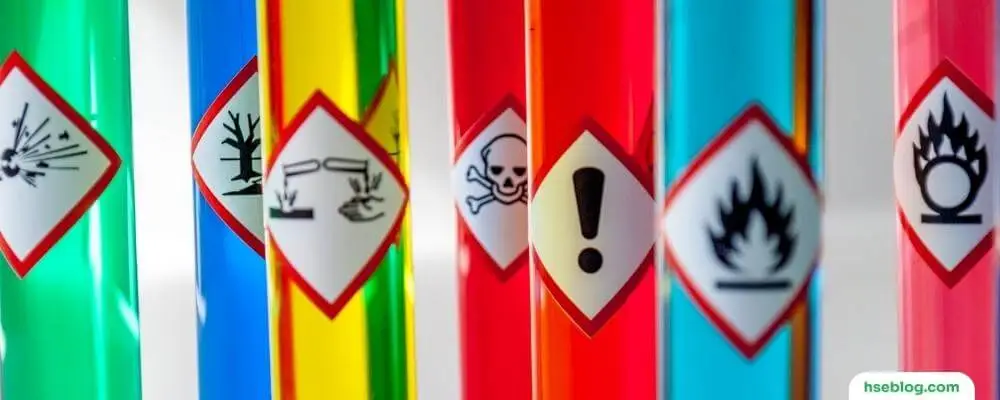
Step 2: Prepare and Implement a Written Hazard Communication Program
The second step towards crafting an effective hazard communication program involves preparing a detailed written plan and a comprehensive list of all hazardous chemicals in your workplace.
Drafting a Written Hazard Communication Plan
This plan serves as a roadmap, outlining how you will handle hazard communication in your facility. This must be detailed and systematic documentation demonstrating how you will meet the requirements as specified by OSHA in paragraphs (f), (g), and (h) of the Hazard Communication Standard, covering labels and other forms of warning, safety data sheets (SDSs), and employee information and training respectively.
This written program aims to ensure that your approach to hazard communication is organized and coordinated. It should describe the methods you will use for labeling, how you will manage and disseminate Safety Data Sheets, and the approach to providing information and training to employees. These elements must be described in detail, demonstrating how your organization will comply with the Hazard Communication Standard.
Preparing a Hazardous Chemicals Inventory
The second part of this step is preparing a comprehensive list of all hazardous chemicals known to be present in your workplace. This inventory’s purpose is to clearly understand what hazardous materials you have, where they are, and what risks they pose.
While preparing this list, it is recommended to use the product identifier. This name is used to identify the hazardous chemical, such as the product name, common name, or chemical name. Your product identifier should match the name on the corresponding label and Safety Data Sheet for each hazardous chemical. This makes tracking the status of each chemical’s SDS and labels much more straightforward.
Step 3: Ensure Containers are Labeled
The third step in implementing an effective hazard communication program revolves around properly labeling all containers that house hazardous chemicals in your workplace.
Maintaining Labels on Shipped Containers
All containers shipped by chemical manufacturers and importers should come with labels that provide critical information about the hazardous chemicals they contain. This information includes the product identifier, a signal word (like “Warning” or “Danger”), pictograms (symbols to quickly convey specific hazards), hazard statements (descriptions of the nature and degree of hazard), precautionary statements (recommended measures to prevent or reduce adverse effects), and the name, address, and phone number of the responsible party.
When you, as an employer, receive a container of hazardous chemicals from a supplier, you must ensure that this information is clearly visible, intact, and not tampered with.
Labeling Workplace Containers
Not only do shipped containers need to be labeled, but also any containers of hazardous chemicals used within your workplace. As an employer, you have the responsibility to label these containers adequately.
You can use the same labeling system the supplier provided or alternative systems like those provided by third parties. Examples of third-party systems include the National Fire Protection Association (NFPA) system or the Hazardous Materials Identification System (HMIS). However, these third-party systems should be used with other necessary information rather than as a replacement for supplier-provided labels.
At the very least, labels on workplace containers must include the product identifier and general information about the hazards posed by the chemical. Regardless of the labeling system used, ensuring that all workers can access complete hazard information to work safely with these chemicals is essential.
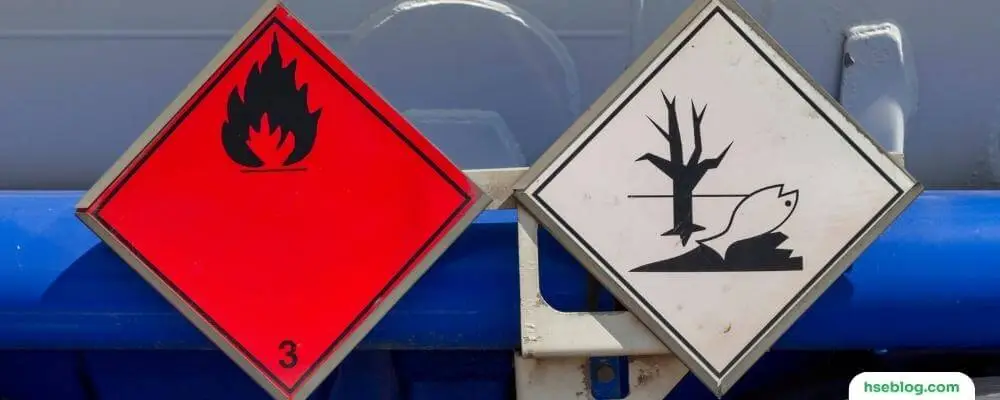
Step 4. Maintain Safety Data Sheets (SDSs)
The fourth step to creating a comprehensive hazard communication program involves careful management of Safety Data Sheets or SDSs for every hazardous chemical in the workplace.
Keeping Safety Data Sheets
An SDS is a detailed document that provides information about a specific hazardous chemical, including its properties, potential hazards, protective measures, and safety precautions. As an employer, you must maintain an up-to-date SDS for each hazardous chemical in your workplace. If an SDS does not accompany the delivery of a hazardous chemical from your supplier, it’s important to request one promptly. Maintaining an organized, current collection of SDSs is crucial for keeping your workplace safe.
Ensuring Accessibility of SDSs
Just having SDSs isn’t enough; they need to be readily accessible to all employees in their work areas during their work shifts. This is crucial as it ensures that employees can quickly reference these documents to understand the risks and safety precautions related to the chemicals they are handling.
The method of making SDSs accessible can vary based on the specific circumstances of your workplace. Some employers might opt to keep SDSs in a central location, such as a safety office or a binder at a job site. This can be a practical solution for workplaces with a moderate number of hazardous chemicals.
In workplaces with many chemicals, electronic access might be more practical. If you choose this route, it’s crucial to have a reliable backup system in case of a power outage, equipment failure, or other emergency that might disrupt access to the primary electronic system.
Regardless of the method used to store and access SDSs, employers must ensure that employees are adequately trained to access and use these documents. Employees should be able to obtain hard copies of the SDSs if an electronic system is in use. In the case of a medical emergency, hard copy SDSs must be immediately available to medical personnel to ensure they have all the information they need to respond appropriately.
Step 5. Inform and Train Employees
The fifth step in setting up an effective hazard communication program is training and educating your employees about the hazardous chemicals they may encounter in their work area.
Timing and Scope of Training
Employee training should occur before their initial assignment to a work area and whenever new hazards are introduced. Employees must receive updated training whenever a new hazardous chemical is brought into the workplace. This keeps them informed about the potential risks and ensures they know how to handle these chemicals safely and responsibly.
Training must be conducted in a language and manner that all employees can understand. This might mean offering training materials in multiple languages or using visual aids or hands-on demonstrations for those with difficulty reading.
Content of Training
The training should cover the requirements of the Hazard Communication Standard (HCS), the specific hazards of the chemicals in the work area, appropriate protective measures to mitigate these hazards, and where and how to obtain additional information.
Employees should be fully aware of their exposure to hazardous chemicals and understand their associated risks. They should be trained to read and understand labels and Safety Data Sheets (SDSs) as these documents provide crucial information about chemical hazards, precautions for use, protective equipment, first-aid instructions, and more.
In addition, the training should provide a detailed overview of the protective measures available in the workplace. This could include personal protective equipment (PPE), safe handling procedures, and emergency procedures. Employees should also be trained on how to use or implement these measures effectively.
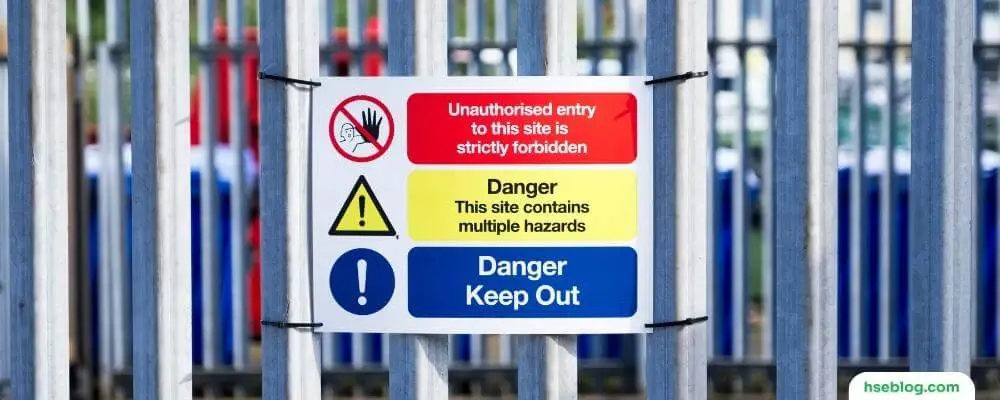
Step 6. Evaluate and Reassess Your Program
The sixth and final step in creating a comprehensive hazard communication program involves regularly evaluating and reassessing your program to ensure it remains effective and relevant.
Regular Review of Your Program
Over time, workplaces evolve and change, and so should your hazard communication program. Regularly reviewing your program is crucial to ensure it continues functioning as intended and meets its objectives. This could mean assessing whether your employees still understand the information they’ve been provided, if they can successfully locate and interpret Safety Data Sheets (SDSs), or if they use the correct protective measures when handling hazardous chemicals.
You might conduct these reviews annually, biannually, or more frequently if there are significant changes in your workplace. These reviews aim to identify any gaps or weaknesses in your program that may have developed over time.
Revision of Your Program
Based on your reviews, revisions to your program may be necessary to address changes in your workplace. This could include the introduction of new chemicals, the discovery of new hazards, changes in safety regulations or best practices, or changes in the way work is conducted.
Revisions could take many forms. For example, if new hazardous chemicals have been introduced into your workplace, you might need to update your inventory of hazardous chemicals, obtain new SDSs, and conduct additional employee training. You might need to change your labeling system or update safety procedures if new hazards are identified.
Conclusion
Implementing a thorough and effective hazard communication program is a vital responsibility for employers dealing with hazardous chemicals in their workplace. Adherence to OSHA’s Hazard Communication Standard ensures regulatory compliance and, more importantly, safeguards the health and well-being of your employees.
As we’ve discussed in this guide, an effective program consists of six key steps: learning the standard and identifying responsible staff, preparing a written hazard communication plan, ensuring proper labeling of containers, maintaining Safety Data Sheets, providing comprehensive training to employees, and continually evaluating and reassessing the program.
Each of these steps plays an integral role in constructing a comprehensive program that fosters a culture of safety and awareness within your organization. A well-executed program promotes transparency, prepares your team to handle hazardous situations, and makes your workplace safer for everyone involved.
Remember, creating and maintaining a hazard communication program is not a one-time effort; it requires consistent monitoring, evaluation, and adaptation to the ever-changing circumstances of your workplace. By investing in these steps, you invest in your business’s long-term safety, productivity, and most valuable asset—your employees.