Safety, a cornerstone of organizational success, is more than just a checkbox—an ongoing commitment. As businesses grapple with complex operational landscapes, having a clear compass pointing toward safety excellence is essential. This is where the pivotal role of leading and lagging indicators comes into play. These indicators, much like the dashboard of a car, provide a glimpse into an organization’s safety performance—showcasing where it’s been and hinting at where it’s heading.
This blog will delve deep into the 10 key leading and lagging safety performance indicators. By understanding these metrics, organizations can foster a proactive safety culture, reduce workplace incidents, and ultimately ensure a healthier, more productive environment. So, whether you’re a safety professional aiming to elevate your organization’s safety game or someone keen to understand safety metrics better, this guide will offer valuable insights to steer you in the right direction.
What are the Leading Indicators?
Leading indicators are proactive and predictive measures used in various fields, especially in safety management, to identify and monitor potential risks before they result in negative outcomes. They provide insights into future health and safety performance and allow organizations to take preventive actions to mitigate potential issues.
In essence, leading indicators are a forward-looking metric. They focus on future safety performance and continuous improvement, helping to identify potential risks and allowing for timely intervention.
For example, the frequency of safety training sessions or the number of safety drills conducted in a workplace setting might be used as leading indicators. These metrics suggest the company’s commitment to safety and proactive efforts to prevent accidents. If these numbers were to decrease, it could indicate a potential future increase in safety incidents, even if no such incidents have occurred.
In contrast to lagging indicators, which measure events that have already occurred (e.g., the number of accidents or injuries), leading indicators are all about forecasting and prevention. They offer an early warning sign of potential problems, allowing for corrective actions to be taken before any harm occurs.
What are the Lagging Indicators?
Lagging indicators reflect historical performance by measuring outcomes or events that have already occurred. These are typically output-oriented, easy to measure, and hard to improve or influence. In many contexts, especially in safety and business performance, lagging indicators are used to assess past performance or results based on specific implemented actions or strategies.
For example:
- In workplace safety, lagging indicators might include the number of injuries or accidents over a specific period, the number of worker’s compensation claims filed, or the number of days employees missed due to work-related injuries.
- In business, lagging indicators could refer to end-of-quarter sales figures, total yearly revenue, or customer satisfaction scores from previous periods.
While lagging indicators provide valuable post-event insights and can help organizations identify patterns or trends from past data, they do not inherently offer predictive or proactive insights. Therefore, they are often used with proactive leading indicators that focus on predicting future outcomes or events.
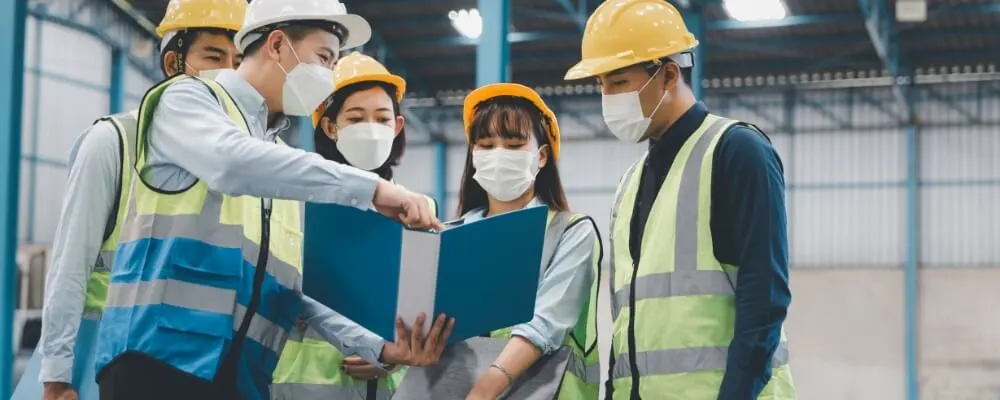
Leading Indicators of Safety Performance
Leading indicators of safety performance are proactive, preventive, and predictive measures that provide information about the effectiveness of a safety management system. They are used to identify potential issues before they result in incidents, injuries, or damages. Monitoring these indicators can help organizations prevent accidents and improve overall safety performance. Here are some leading indicators of safety performance:
1. Safety Training Attendance
Ensuring employees attend workplace safety training sessions is crucial for an organization’s safety culture. Tracking attendance allows management to determine if all personnel receive essential information to perform their tasks safely. When individuals skip or miss safety training, they might lack vital knowledge about risks associated with their roles or the processes to mitigate them.
Organizations can identify patterns by maintaining an attendance record, such as specific departments consistently missing training, and take corrective measures. Furthermore, consistent attendance at these trainings can indicate the commitment level from management and employees toward a safe work environment.
2. Near Miss Reports
A near miss is an unplanned event that did not result in injury, illness, or damage but had the potential to do so. Monitoring these incidents is an essential proactive measure for organizations. While it’s fortunate that a near miss didn’t result in harm, it provides invaluable insight into potential weaknesses in safety procedures or equipment.
By analyzing near-miss reports, organizations can identify trends, recognize areas of concern, and develop strategies to prevent similar future incidents. Encouraging employees to report these events fosters a safety awareness and continuous improvement culture.
3. Safety Drills Conducted
Regularly conducting safety drills, such as fire evacuations or earthquake preparedness drills, demonstrates an organization’s commitment to ensuring everyone knows the procedures to follow during emergencies. These drills help familiarize employees with escape routes, assembly points, and other vital protocols, reducing panic and confusion during real events.
Furthermore, by assessing the outcomes of these drills, organizations can pinpoint areas of improvement, ensuring that response times are optimal and that everyone is accounted for during potential emergencies.
4. Safety Audits
Safety audits are systematic evaluations of workplace environments and safety practices. These audits aim to identify potential hazards, non-compliance with safety regulations, and areas where procedures may be improved. Auditors examine various aspects, including machinery, work practices, protective equipment, and even employee behaviors, to maintain safety standards.
Periodic safety audits demonstrate an organization’s commitment to a safe work environment and provide a clear roadmap for addressing and mitigating potential risks before they become problematic.
5. Employee Safety Observations
Employees are often the first to notice unsafe conditions or behaviors in their work environments since they are directly engaged in day-to-day operations. Encouraging them to report these observations empowers them to take an active role in maintaining a safe workplace. Management can get real-time feedback about potential hazards by creating an open channel for these observations.
Recognizing and valuing employee input on safety matters can lead to quicker resolutions, foster a culture of mutual respect and trust, and ensure that the organization benefits from its workforce’s collective experience and insights.
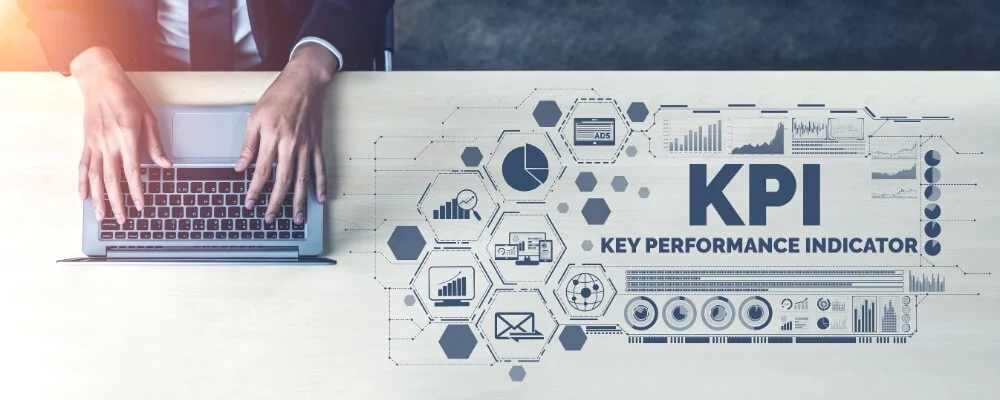
6. Maintenance of Safety Equipment
Safety equipment, ranging from fire extinguishers to safety harnesses, is pivotal in mitigating risks and preventing workplace incidents. Ensuring that these tools and equipment are in optimal working condition is essential. Over time, even the most robust equipment can degrade, malfunction, or become obsolete.
Regular checks and maintenance routines ensure that any deficiencies are promptly addressed, whether refilling extinguishers, checking the expiration dates on first aid supplies, or ensuring that safety harnesses remain free from wear and tear. When organizations prioritize the upkeep of their safety equipment, it demonstrates their commitment to creating and maintaining a safe working environment for all employees.
7. Safety Meetings and Briefings
Safety meetings and briefings are dedicated forums where safety protocols, concerns, updates, and initiatives are discussed. By holding these meetings regularly, organizations show that safety isn’t just a one-time agenda but an ongoing priority.
These gatherings serve multiple purposes: they keep safety at the forefront of everyone’s minds, provide a platform for discussing new procedures or regulations, and allow for reviewing any recent incidents or near misses. Through these discussions, employees are reminded of the importance of safety and informed of the latest best practices.
8. Employee Engagement in Safety Committees
Safety committees or task forces typically consist of representatives from various organizational departments and levels. Their main goal is to oversee and promote workplace safety. When employees are actively engaged in these committees, it enriches the committee’s perspectives and shows a grassroots commitment to safety.
Employee participation means that the safety culture is not just directed from the top down but is also built and nurtured from the bottom up. Engaged employees can bring unique insights from daily operations, highlight real-world challenges, and collaborate on practical solutions.
9. Hazard Identification and Risk Assessment
Identifying potential hazards and assessing the associated risks is foundational to any proactive safety strategy. By regularly conducting these assessments, organizations can remain one step ahead of possible safety incidents. This process involves spotting potential dangers related to machinery, substances, procedures, or even behaviors and then evaluating their risk level. Once identified, measures can be taken to eliminate the hazard or reduce the associated risk.
This ongoing commitment to identifying and managing hazards underscores the organization’s dedication to ensuring every employee can work in the safest environment possible.
10. Safety Suggestions and Feedback
An organization’s safety culture is greatly enhanced when it values and acts upon employee feedback. Those on the front lines often have firsthand knowledge of potential hazards or areas for improvement. Organizations can tap into a wealth of practical insights by encouraging employees to voice their safety suggestions and concerns.
More importantly, when management takes this feedback seriously and implements suggested changes, it reinforces the idea that everyone has a stake in workplace safety. This collaborative approach leads to a safer work environment and fosters trust, respect, and a sense of collective responsibility among all organization members.
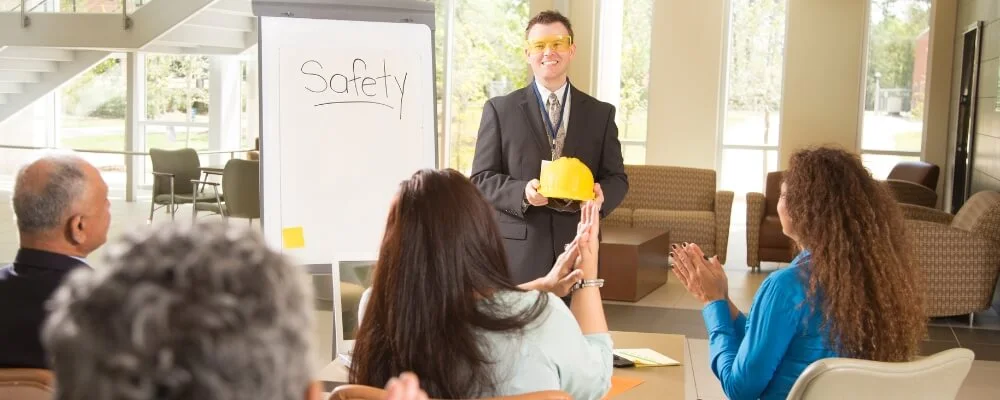
Lagging Indicators of Safety Performance
Lagging indicators are reactive metrics that measure the frequency and severity of incidents that have already occurred. In the context of safety performance, they provide insights into past performance and help organizations identify where things went wrong. Here are 10 commonly used lagging indicators in safety performance:
1. Recordable Injury Rate
Recordable Injury Rate is an essential metric in workplace safety management. It represents the number of work-related injuries in an organization that required medical attention beyond simple first aid relative to a standardized number of work hours (often per 200,000 hours, equivalent to 100 employees working full time for a year).
By tracking this rate, organizations can get a clearer picture of the frequency of more severe injuries. A higher rate can indicate potential issues in workplace safety procedures, whereas a lower rate suggests that safety protocols are effectively preventing severe injuries.
2. Lost Time Injury Frequency Rate (LTIFR)
LTIFR is a key performance indicator in occupational health and safety. It quantifies the frequency at which work-related injuries result in an employee being unable to return to work for a scheduled shift or longer. This means the injury was significant enough to warrant time off, affecting both the employee’s well-being and the organization’s operational capacity.
By monitoring LTIFR, organizations can gauge the effectiveness of their safety programs and interventions. A decreasing LTIFR over time can indicate improved safety measures and a more secure working environment.
3. Severity Rate
Severity Rate measures the gravity of injuries sustained within the workplace. Instead of simply looking at the number of injuries, it focuses on the duration or the number of lost days resulting from them. It is calculated by taking the total number of lost days due to injuries in a given period and relating it to a standardized number of work hours.
This metric is essential because two workplaces might have the same injuries. Still, if one has more extended absences resulting from those injuries, it suggests that the nature of the injuries is more severe.
4. Fatality Rate
The Fatality Rate is, understandably, one of the most sobering indicators of workplace safety. It measures the fatalities from work-related incidents relative to a standardized number of work hours. Even a single fatality can have profound implications from a human perspective and in terms of regulatory, reputational, and financial consequences for an organization. Regularly tracking and aiming to reduce the fatality rate is paramount for any organization, as it directly pertains to the lives of its employees.
5. Property Damage Incidents
While human safety is always the paramount concern, property damage incidents provide another lens through which an organization’s safety can be assessed. These incidents encompass any event that damages the company’s equipment, infrastructure, or other assets. Such damages can lead to operational disruptions, financial costs for repair or replacement, and potential secondary safety risks.
By monitoring the frequency and severity of property damage incidents, organizations can identify areas where safety improvements or additional training might be necessary to prevent future damages and the associated costs.
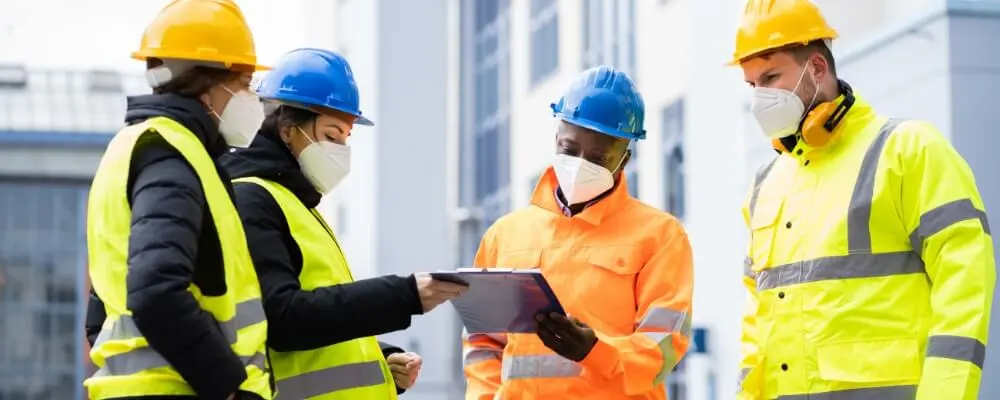
6. Workers’ Compensation Claims
Workers’ compensation is a form of insurance that provides wage replacement and medical benefits to employees injured during employment. When an employee files a claim, it signifies that they have suffered a work-related injury or illness that warrants compensation. Monitoring the number of these claims can offer insights into workplace safety.
A high frequency of claims might suggest potential systemic issues with workplace safety. Conversely, fewer claims may indicate effective safety protocols and a healthier work environment. Additionally, high compensation claims can lead to increased insurance premiums for the employer, making it a significant financial consideration.
7. Safety Violation Fines
Safety violation fines are penalties imposed by regulatory bodies on organizations that fail to comply with established safety standards and regulations. These fines serve as a financial deterrent against neglecting safety practices. An increase in the number or amount of these fines can indicate a decline in an organization’s adherence to safety regulations.
Consistently incurring these fines affects an organization’s bottom line and can tarnish its reputation, potentially leading to lost business opportunities and diminished trust among employees and stakeholders.
8. Occupational Illness Rate
The Occupational Illness Rate represents the number of reported work-related illnesses over a specific period, typically standardized per a set number of work hours. It provides insight into the longer-term health impacts of working conditions. While injuries might be immediate and apparent, occupational illnesses can develop over time due to prolonged exposure to harmful conditions or substances.
Examples include respiratory diseases from inhaling harmful particles or repetitive strain injuries from consistent ergonomic issues. Tracking this rate helps organizations identify and address chronic health hazards in the workplace.
9. Incidents of Non-compliance
Incidents of non-compliance refer to situations where established safety regulations, standards, or company-specific policies were not adhered to. These incidents can range from not wearing the proper PPE to failing to follow machine safety protocols.
Regularly monitoring these incidents can help organizations identify areas for further training or intervention. A high non-compliance rate suggests a lack of awareness, insufficient training, or a cultural issue where safety guidelines are not taken seriously.
10. Number of Safety Corrective Actions
After a safety incident occurs, it’s crucial to understand its cause and take steps to prevent similar events in the future. The number of safety corrective actions refers to the measures taken in response to identified safety issues. This can include revising procedures, implementing new training programs, or making physical modifications to the work environment.
Tracking the number and effectiveness of these corrective actions allows organizations to assess their responsiveness to safety concerns. An organization that consistently implements corrective actions demonstrates a proactive approach to safety, emphasizing continuous improvement.
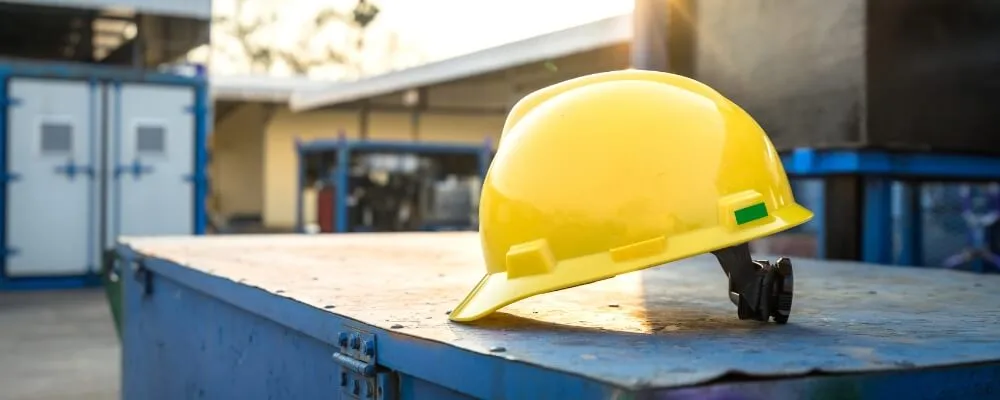
Best Practices For Using Leading and Lagging Indicators For a Better Workplace
Utilizing leading and lagging indicators is a strategic way for organizations to enhance workplace safety and overall efficiency. When effectively implemented, these indicators can significantly transform an organization’s approach to safety, productivity, and performance. Here are best practices for using leading and lagging indicators to foster a better workplace:
- Establish Clear Objectives: Determine the specific goals you aim to achieve with your safety program. Knowing your objectives helps select the most relevant indicators to track and monitor.
- Balance Your Metrics: Don’t rely solely on leading or lagging indicators. Use a mix of both to get a comprehensive view of safety performance. While lagging indicators help understand past performance, leading indicators are predictive and preventive.
- Involve Employees: Encourage workers to participate in selecting, reporting, and reviewing indicators. Their hands-on experience can offer valuable insights and increase buy-in for safety initiatives.
- Frequent Review & Analysis: Regularly assess your indicators. Continuous evaluation helps identify trends, understand root causes, and make timely interventions.
- Prioritize Communication: Ensure that everyone in the organization, from top management to front-line employees, understands the significance of the indicators, their purpose, and how they relate to the overall safety and productivity goals.
- Benchmarking: Compare your organization’s indicators with industry standards or similar organizations. This can provide perspective on how you’re doing and where improvements can be made.
- Act on the Data: Data alone doesn’t improve safety or performance. The organization must act on the insights derived from the indicators. Develop action plans, assign responsibilities, and set timelines for improvements.
- Feedback Loop: Create a system where feedback from leading and lagging indicators can refine processes and strategies. This will establish a cycle of continuous improvement.
- Keep Indicators Relevant: As the organization grows and changes, so will its safety and performance priorities. Review and update your indicators periodically to ensure they remain relevant to your current operational context.
- Invest in Training: Regularly train employees on safety protocols, the importance of reporting, and how to utilize the data from leading and lagging indicators for their tasks. Empower them with the necessary knowledge to contribute effectively to the organization’s safety goals.
- Celebrate Successes: Recognize and celebrate when positive results are achieved, whether it’s a decrease in injury rates (lagging indicator) or an increase in safety training sessions (leading indicator). This boosts morale and reinforces the importance of safety.
- Transparency is Key: Ensure that positive or negative data is transparently shared across the organization. This fosters trust, promotes accountability, and encourages collective responsibility for safety.
- Avoid Punitive Measures: Avoid using leading indicators, especially those like near-miss reports, as a tool for punitive measures. Employees should feel safe reporting issues without fear of repercussions.
- Leverage Technology: Use modern tools and software to track, analyze, and present data. Technology can automate data collection, provide real-time insights, and simplify reporting.
- Continuous Monitoring: Don’t just set indicators and forget them. Monitor them constantly to ensure the organization is moving in the desired direction, and be ready to make course corrections as needed.
When organizations effectively integrate leading and lagging indicators into their strategies, they can proactively manage risks, understand past challenges, and foster a culture of continuous improvement and safety. The key is to be systematic, collaborative, and action-oriented.
Conclusion
Navigating workplace safety requires more than good intentions; it demands a systematic approach informed by reliable metrics. The 10 key leading and lagging indicators of safety performance highlighted in this guide offer organizations a comprehensive framework to evaluate, improve, and sustain their safety initiatives. By closely monitoring and acting upon these indicators, businesses can mitigate potential risks and foster a culture where safety is inherently woven into the fabric of daily operations.
Remember, a safe workplace is not merely a destination but an ongoing journey. These indicators serve as milestones, helping organizations stay on track, celebrate their progress, and remain vigilant against complacency. By prioritizing these metrics, we can ensure that every worker returns home safely at the end of the day, making our workplaces a beacon of safety, productivity, and well-being.