In today’s dynamic business environment, organizations constantly seek methodologies to streamline operations, enhance productivity, and create safer workspaces. One approach that has stood the test of time, originating from Japanese manufacturing practices and is now universally adopted across industries, is the 5S Lean methodology. But what exactly is 5S Lean? How can it transform workspaces, and more importantly, how can organizations effectively implement it?
In this blog, we will unravel the principles of 5S Lean, illustrating its impact through real-world examples and guiding you step-by-step on how to seamlessly integrate it into your operations. Whether you’re a seasoned industry professional or a curious novice, this comprehensive exploration of 5S Lean promises insights that can propel your organizational processes to new heights.
What’s 5S Lean?
5S Lean is a systematic approach to workplace organization and standardization based on five Japanese words that start with the letter ‘S’. It’s a part of lean manufacturing and can be applied to any work environment, including offices, labs, and production floors. The goal of 5S is to create a clean, organized, and efficient workspace.
Here’s a brief definition of each of the five S’s:
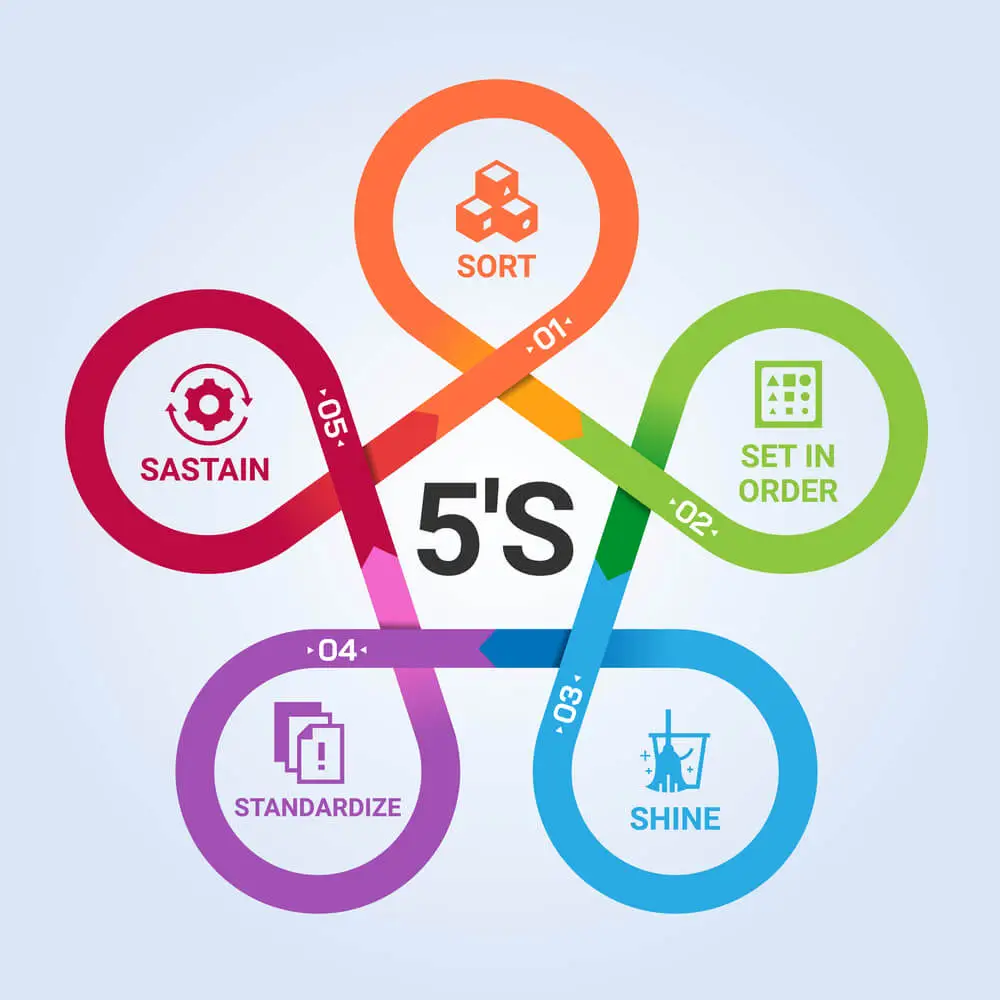
1. Seiri (Sort):
The primary goal of Seiri or “Sort” is to eliminate unnecessary items from the workspace, leaving only the essentials. This process differentiates between what is frequently needed, occasionally required, and what is redundant. Doing this significantly reduces the time wasted searching for items, and potential safety hazards caused by clutter are minimized.
Regular assessments of the workspace identify items that have become obsolete or redundant. A common practice during this phase is using a ‘red tag’ system. Items deemed unnecessary are tagged and moved to a holding area before final disposition.
2. Seiton (Set in Order):
Seiton, or “Set in Order,” focuses on organizing the necessary items to be readily accessible and have a designated place. Tools, materials, and information should be arranged based on frequency of use. This step streamlines operations and minimizes wasted motion, as items are located in strategic positions aligned with their sequence of use in the operational process.
Techniques such as labeling, color-coding, and shadow boards might clarify where items belong, making it intuitive for employees to find and return items to their proper places.
3. Seiso (Shine):
Seiso, meaning “Shine,” goes beyond mere cleanliness. While ensuring the workspace is tidy and conducive to productive work, it emphasizes regular maintenance and inspection of equipment. Daily cleaning becomes integral to operations, fostering a proactive approach to potential issues.
A consistently clean workspace can highlight problems quickly, such as machinery malfunctions evident through leaks on a pristine floor. In essence, cleaning serves as both an aesthetic and functional activity, often acting as an informal equipment inspection.
4. Seiketsu (Standardize):
The objective of Seiketsu, or “Standardize,” is to embed consistent practices ensuring that the standards set in the first three steps are maintained. This involves creating checklists or standard operating procedures that guide and remind employees of their daily tasks and responsibilities. The standards are not static; they undergo regular reviews and updates to align with any changes or improvements.
The aim is to achieve uniformity across different departments or sectors of an organization. Visualization aids, such as charts or schedules, help ensure everyone is on the same page regarding these standards.
5. Shitsuke (Sustain):
Shitsuke, signifying “Sustain,” emphasizes the long-term commitment to the 5S system. This step is not merely about maintaining a system but fostering a culture of continuous improvement within an organization. It involves regularly training employees, reinforcing the importance of the 5S principles, and ensuring their consistent application.
Regular audits check adherence, with successes celebrated and failures constructively addressed. Encouraging feedback is crucial at this stage, as it offers valuable insights and potential areas of improvement from those directly engaged with the processes.
Examples of 5S in Action:
- Sort: An office desk might be cluttered with numerous documents, unused stationery, and redundant equipment. You declutter the space by removing everything and keeping only what’s essential.
- Set in order: After sorting, designate specific locations for each item. For instance, always keeping the stapler on the top right corner of the desk or having a labeled tray for incoming/outgoing documents.
- Shine: Clean the desk daily, ensuring no dust accumulation. Regularly inspect office equipment, like printers, to ensure they’re working properly.
- Standardize: Create a checklist for the daily cleaning routine. Maybe designate a specific day each month for deep cleaning or equipment inspection.
- Sustain: Conduct regular audits to ensure everyone is following the 5S standards. Provide ongoing training sessions and reward compliance.
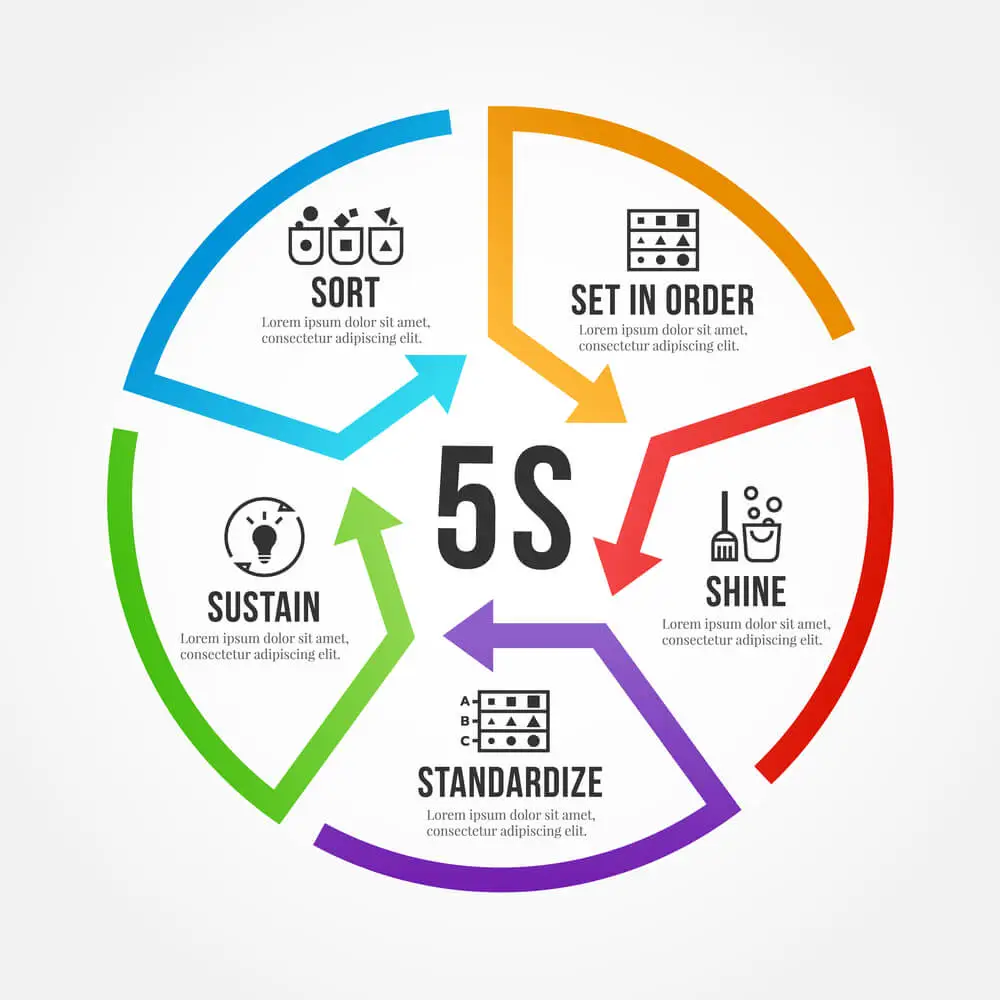
How To Implement 5S Of Lean?
Implementing the 5S methodology is a systematic process that involves everyone in the organization. The following steps can serve as a guideline for a successful 5S implementation:
1. Awareness and Training
The first step in implementing the 5S system is ensuring that everyone in the organization is on board. This requires a comprehensive understanding of the 5S principles and their benefits. Training sessions, workshops, and informational materials should be organized to impart knowledge about 5S. This phase must address the ‘how’ and the ‘why,’ ensuring employees comprehend the importance and value of adopting 5S in their daily routines.
2. Kick-off with a Pilot Area
Before deploying 5S throughout the organization, starting in a specific area or department is wise. This pilot initiative serves as a demonstration of the potential benefits and also as a learning opportunity. By focusing on a limited area first, organizations can refine their approach, identifying what works best and what challenges might arise. It’s also essential to document the process, capturing the methodology and the results. This documentation will be invaluable when expanding the initiative to other parts of the organization.
3. Team Involvement
The success of 5S hinges on active participation from employees at all levels. They are, after all, the ones who interact with the workspace daily. Thus, involving them in every step of the 5S process is crucial. By doing so, the organization can tap into its insights, often grounded in practical experience. Employee involvement ensures that the organization not only imposes changes but collaboratively shapes the workspace. This collaborative approach fosters a sense of ownership among employees, making them more invested in the initiative’s success.
4. Use Visual Aids
A well-organized workspace is further enhanced with clear visual cues. Labels, color codes, and signs guide employees and reinforce the 5S standards. Visual aids streamline operations by making it easier for employees to locate tools or materials, understand workflows, and adhere to designated storage or disposal areas. Moreover, consistent visual cues across the organization can bolster standardization, ensuring everyone is on the same page regardless of their department or role.
5. Regular Audits
To ensure the longevity and efficacy of the 5S implementation, regular audits are essential. These audits assess compliance, evaluate the current system’s efficiency, and identify areas that might require improvement. They serve as a health check, ensuring the organization remains on track. Audits should be carried out by a designated team or individual, with transparent feedback to all stakeholders. This iterative review process ensures the organization always moves toward an optimal workspace environment.
6. Continuous Improvement
Once 5S is implemented, the journey isn’t over. Generally, the essence of 5S, and lean thinking, is Kaizen, or continuous improvement. Organizations should always be on the lookout for ways to further optimize, streamline, and enhance their workspaces and processes. This proactive mindset ensures that the organization doesn’t stagnate but evolves with changing requirements, technologies, and challenges.
7. Celebrate Successes
Recognition plays a crucial role in reinforcing positive behavior and outcomes. Organizations should regularly celebrate and reward teams or individuals who showcase excellence in maintaining and improving their 5S practices. Whether through formal awards, public acknowledgment, or other incentives, celebrating successes fosters a positive organizational culture, encouraging everyone to uphold high standards and seek continual improvement.
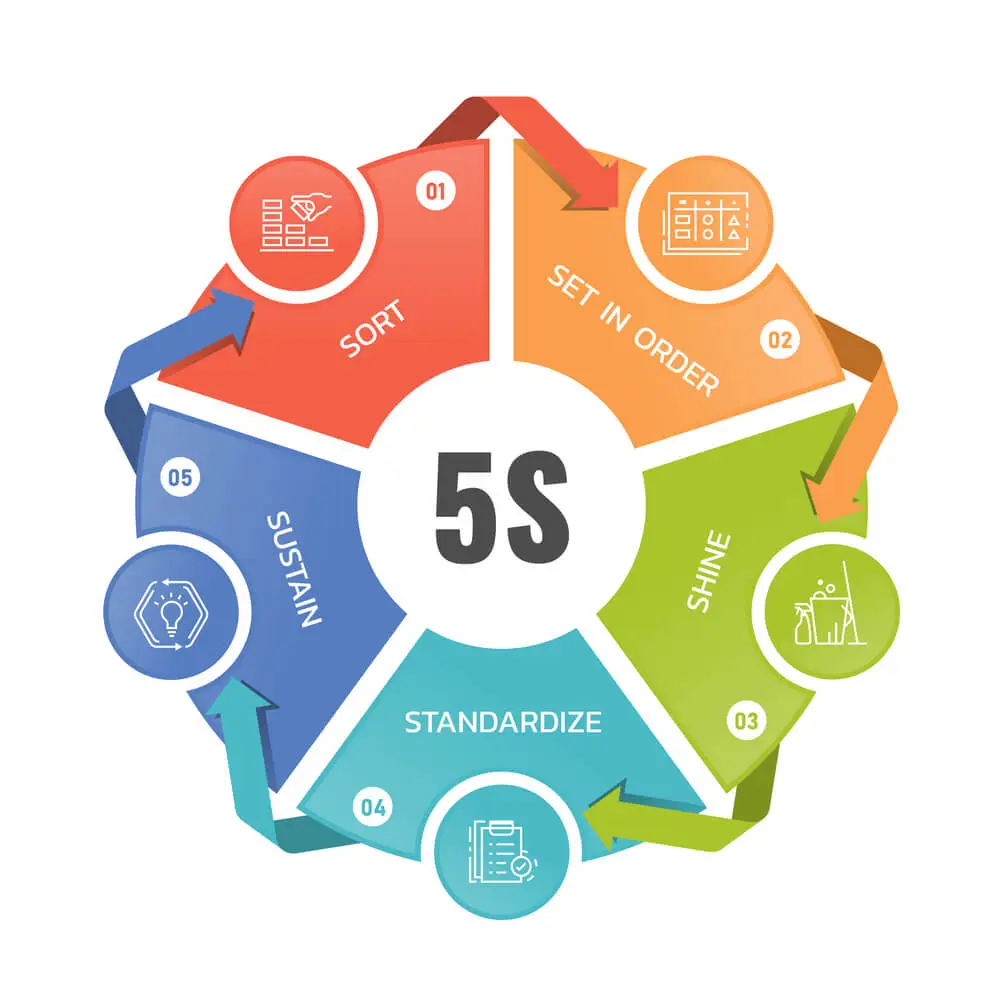
Benefits Of 5S Of Lean
Implementing the 5S system offers a range of benefits, spanning from operational efficiency to employee morale. Here are some of the key advantages of incorporating 5S:
- Improved Efficiency and Productivity: By organizing the workspace and ensuring everything has a designated place, employees can work more efficiently, as they spend less time searching for tools or materials.
- Enhanced Safety: Reducing clutter and ensuring proper organization can minimize the risk of accidents and injuries. Clear walkways, labeled hazardous areas, and organized storage reduce the likelihood of trips, spills, and other hazards.
- Reduced Waste: By sorting out unnecessary items and streamlining work processes, there’s a reduction in waste of materials, time, and effort.
- Increased Quality: A clean and well-organized workspace often leads to better product quality because employees have what they need and can focus more on their tasks.
- Higher Employee Morale: A clean and organized environment often boosts employee morale. They can take pride in their workplace, leading to increased job satisfaction and reduced turnover.
- Easier Problem Identification: When a workspace is organized, deviations or anomalies are easier to spot. For instance, a leak or equipment malfunction can be quickly noticed and rectified.
- Standardized Operations: The standardization phase ensures that best practices are defined and followed across the board, leading to consistent performance and outcomes.
- Flexibility and Scalability: With a standardized and organized environment, it’s easier to train new employees, scale operations, or adapt to changes.
- Cost Savings: By reducing waste, improving efficiency, and minimizing defects or errors, the organization can realize significant cost savings.
- Improved Image: Visitors, whether clients, vendors, or potential hires, will have a better impression of an organization that looks tidy, organized, and efficient.
- Cultural Shift: Over time, maintaining 5S principles can instill a culture of discipline, responsibility, and continuous improvement within the organization.
While the benefits of 5S are substantial, it’s essential to remember that successful implementation requires sustained effort, regular reviews, and adjustments based on feedback and changing requirements.
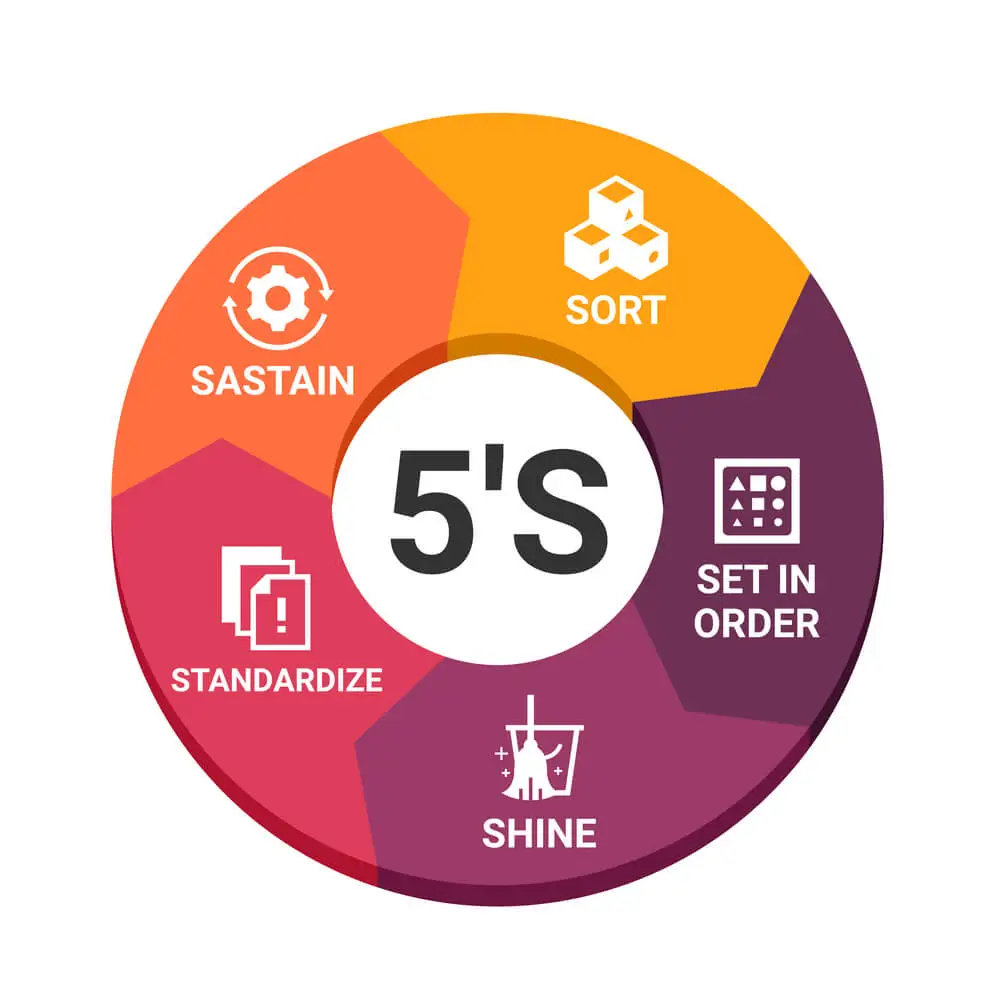
5S and Workplace Safety
Implementing the 5S system in an organization isn’t just about efficiency and productivity; it’s also inherently tied to improving workplace safety. Let’s delve into how each principle of the 5S system contributes to a safer work environment:
Seiri (Sort)
The workplace becomes less cluttered by distinguishing between necessary and unnecessary items and eliminating the latter. A decluttered workspace minimizes potential tripping hazards and ensures that essential safety tools and equipment are more easily accessible. With fewer items in the way, there’s a reduced risk of accidents related to stumbling over or colliding with misplaced objects.
Seiton (Set in Order)
Organizing tools and equipment ensures that everything has a specific place, reducing the need for workers to hunt around or reach awkwardly for them, potentially causing strain or injury. Proper organization also means that emergency equipment, such as fire extinguishers or first-aid kits, can be accessed quickly in a crisis, potentially saving lives.
Seiso (Shine)
Regular cleaning and maintenance, as emphasized in the Seiso phase, are critical for safety. A clean workspace means fewer hazards like oil spills which can lead to slips and falls. By regularly maintaining and inspecting equipment, potential malfunctions that could result in accidents are identified and rectified early on. This proactive approach ensures that issues are addressed before they become major safety concerns.
Seiketsu (Standardize)
By developing standardized task procedures, the chances of errors or deviations that could result in accidents are minimized. A standardized approach ensures everyone knows the safest way to perform a task, reducing the risk of injury due to unfamiliarity or process inconsistency. Regularly revisiting and updating these standards ensures they align with the latest safety protocols.
Shitsuke (Sustain)
Sustaining the gains made through the first four steps is vital for long-term safety. Continuous training and reinforcement ensure that employees don’t become complacent. Instead, they remain committed to upholding safety standards. The discipline and commitment ingrained by Shitsuke ensure that safety becomes a deeply embedded aspect of the organizational culture.
In essence, the 5S system promotes a proactive rather than reactive approach to workplace safety. By creating a tidy, organized, and standardized work environment, potential hazards are identified and eliminated early on, fostering a culture where safety and efficiency go hand in hand.
Conclusion
The 5S Lean methodology, rooted in Japanese manufacturing, presents a holistic approach to optimizing and enhancing workspaces across varied industries. By adopting its principles, organizations can achieve streamlined operations and foster a culture of safety and continuous improvement. Through tangible examples, we’ve seen its transformative power in action, highlighting the tangible benefits that can be reaped when effectively implemented. However, the journey with 5S Lean isn’t a one-time endeavor but a continuous commitment to excellence.
As we’ve explored its facets and delved into implementation strategies, it’s evident that when embraced wholeheartedly, 5S Lean has the potential to serve as a cornerstone for organizational success, driving both efficiency and safety in harmony.