In modern work environments, the protection and welfare of workers are of utmost importance. Companies, regardless of their industry or size, acknowledge the vital significance of Occupational Health and Safety (OHS) in cultivating a productive, safe, and optimistic workplace. However, what are the specifics of these OHS measures, and why are they so essential?
In this blog, we will delve deep into 10 different OHS procedures, shedding light on their importance and offering insights into their implementation. Whether you’re an employer aiming to enhance your workspace safety or an employee curious about best practices, this guide will equip you with valuable knowledge to navigate the intricate landscape of workplace safety. Join us as we embark on this enlightening journey into the heart of occupational health and safety.
Occupational Health And Safety Procedures
Occupational Health and Safety (OHS) Procedures refer to the rules, guidelines, and protocols established by organizations to ensure their employees’ safety, health, and well-being while at work. These procedures are developed to prevent workplace injuries, illnesses, and fatalities, and they encompass a range of practices, from equipment usage guidelines and ergonomic considerations to emergency response plans.
Importance of Occupational Health and Safety Procedures:
- Employee Well-being: At the core of OHS procedures is the concern for the well-being of employees. A safe working environment ensures that workers are protected from potential harm, whether from machinery, chemicals, or workplace stress.
- Legal and Regulatory Compliance: Many countries have strict regulations concerning workplace safety. Adhering to OHS procedures ensures that organizations remain compliant with these laws, thereby avoiding potential legal penalties, fines, or lawsuits.
- Reduction in Costs: Injuries and illnesses result in medical expenses, potential compensation claims, and lost workdays, which can be costly for businesses. Implementing and adhering to OHS procedures can significantly reduce these costs.
- Enhanced Productivity: A safe workplace tends to be a more efficient one. Employees not worried about potential hazards can focus better on their tasks. Moreover, reduced injury rates mean fewer work disruptions.
- Improved Reputation: Organizations known for stringent safety standards are viewed more favorably by clients, partners, and potential employees. A strong OHS track record can be a competitive advantage in many industries.
- Employee Morale and Retention: Knowing their safety is a priority can boost employee morale. Satisfied and secure employees are likelier to stay with the company, reducing turnover rates and associated recruitment costs.
- Proactive Risk Management: OHS procedures regularly identify potential risks and hazards. This proactive approach can help preemptively address issues before they become significant problems.
Occupational Health and Safety Procedures are not just about compliance or reducing costs. They represent an organization’s commitment to the well-being of its employees, creating an environment where individuals can work effectively and securely.
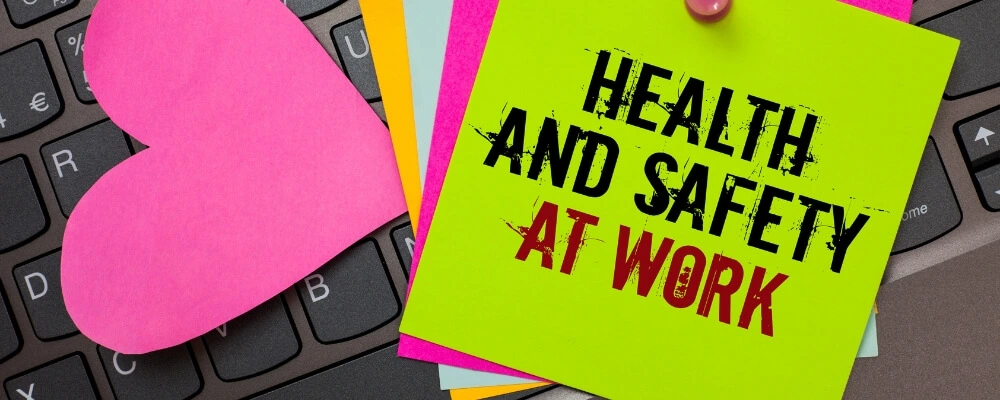
10 Different Occupational Health And Safety Procedures
Occupational Health and Safety (OHS) procedures are essential for ensuring a safe and healthy working environment. Here are 10 different OHS procedures:
1. Risk Assessment
Risk assessment is a systematic process of evaluating potential hazards before they can cause harm. It begins with identifying potential dangers inherent in a task or using specific equipment. This could range from slippery floors to the use of sharp objects or exposure to harmful chemicals. After identifying these hazards, the next step involves gauging the risk level. This level depends on factors like the severity of potential harm and the frequency of exposure to the hazard. For instance, a machine used daily and can cause severe injury if mishandled would have a high-risk level.
Once these risks are clearly understood, appropriate measures are taken to mitigate (reduce the potential impact or likelihood) or eliminate the risks. For some hazards, elimination might be possible, like replacing a toxic substance with a non-toxic one. For others, mitigation measures might be more appropriate, like using protective gear or improving ventilation.
2. Personal Protective Equipment (PPE) Usage
PPE is the final barrier between a worker and potential hazards. Depending on the nature of the job, the required PPE can vary. For instance, construction workers might need helmets to protect against falling objects, while lab technicians might require safety goggles to shield their eyes from chemical splashes. Beyond just providing PPE, workers must know how to wear and maintain them correctly.
A safety mask worn improperly might not offer any protection against inhaled toxins. Moreover, some PPEs, like gloves or filters, have wear-and-tear limits and need regular replacement. Thus, regular training sessions should emphasize the importance of correct usage and maintenance of PPE.
3. Emergency Response Planning
Unforeseen events can happen in any workplace, from fires to chemical spills or natural disasters. An effective emergency response plan outlines the steps to be taken immediately after such an incident.
Essential components of this plan include marked evacuation routes, designated assembly points outside the danger zone, and a list of emergency contact numbers, including local authorities and medical facilities. Regular drills are pivotal in familiarizing all employees with the plan, ensuring that panic doesn’t set in in the face of a real emergency and everyone knows their roles and responsibilities.
4. Machine Safety
The machinery, if misused or malfunctioning, can be a significant source of workplace injuries. Safety guards, which might be physical barriers or sensor-based systems, ensure that the moving parts of a machine don’t pose a direct threat to the workers. However, safety guards are just the first step.
Comprehensive training ensures that workers know how to operate the machines and are aware of potential risks and the signs of malfunction. Furthermore, regular maintenance checks prolong the machine’s life and ensure that wear and tear haven’t made the machine unsafe to use.
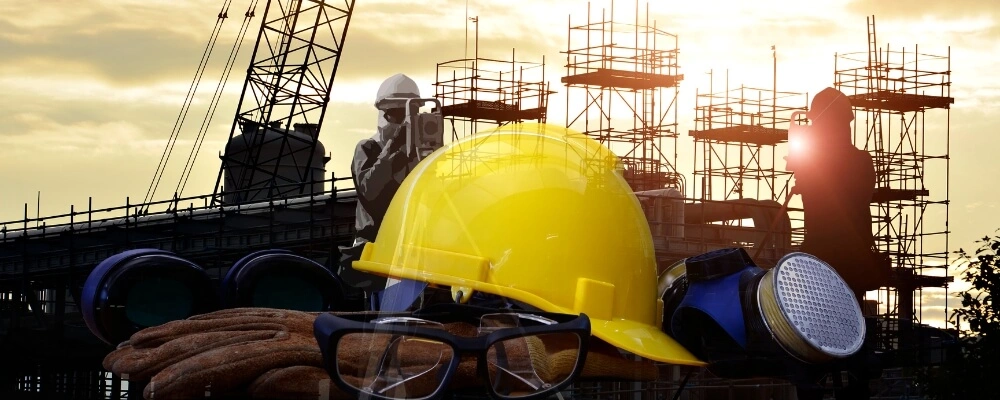
5. Chemical Handling and Storage
Many workplaces use chemicals, some of which can be hazardous if inhaled, ingested, or even touched. Proper labeling ensures that everyone is aware of what a container holds. This labeling is usually complemented by Material Safety Data Sheets (MSDS). These documents provide detailed information about the chemical’s properties, potential hazards, required PPE, and first aid measures in case of exposure.
A designated storage area ensures that chemicals are stored in controlled conditions, minimizing the risk of spillage or unwanted reactions. Employees, especially those directly handling these chemicals, need rigorous training on safe handling procedures, which includes the correct method of transferring chemicals between containers, the importance of using fume hoods, and steps to take in case of accidental exposure.
6. Ergonomics
Ergonomics involves designing and arranging a workplace to optimize it for human use, ensuring that tasks, equipment, and the environment support the user’s ability to work efficiently and safely. An ergonomic workspace not only prevents injuries but also boosts productivity. Consider a desk job scenario: chairs and tables must be of appropriate height so that a worker does not slouch or strain their neck looking at a computer screen.
Ergonomic keyboards and mice can reduce the risk of repetitive strain injuries like carpal tunnel syndrome. Moreover, the arrangement of daily tasks plays a role too. Intermittently changing tasks or taking short breaks can prevent muscle fatigue and cognitive burnout, ensuring the employee’s well-being.
7. First Aid
First aid, in the context of the workplace, is the immediate care given to an injured person before professional medical care is available. A crucial element of first aid preparedness is having a kit with essentials like bandages, antiseptics, and pain relievers, which can address minor injuries or stabilize more severe ones. But merely having a kit is not enough. Workers should have basic knowledge of first aid practices.
For instance, they should be able to perform CPR or know how to address chemical burns. Moreover, every workplace should have designated individuals who have undergone more comprehensive first aid training, acting as primary responders during an emergency.
8. Housekeeping
A clean and organized workplace is not just aesthetically pleasing but also critical for safety. Regular cleaning ensures that potential hazards, like spills that can cause slips, are immediately addressed.
Organized walkways without obstructions can prevent tripping hazards and are especially vital during emergencies for swift evacuations. Proper storage of tools and equipment is another key element. Tools left haphazardly can pose risks of injuries, while certain equipment might malfunction or degrade if not stored under appropriate conditions.
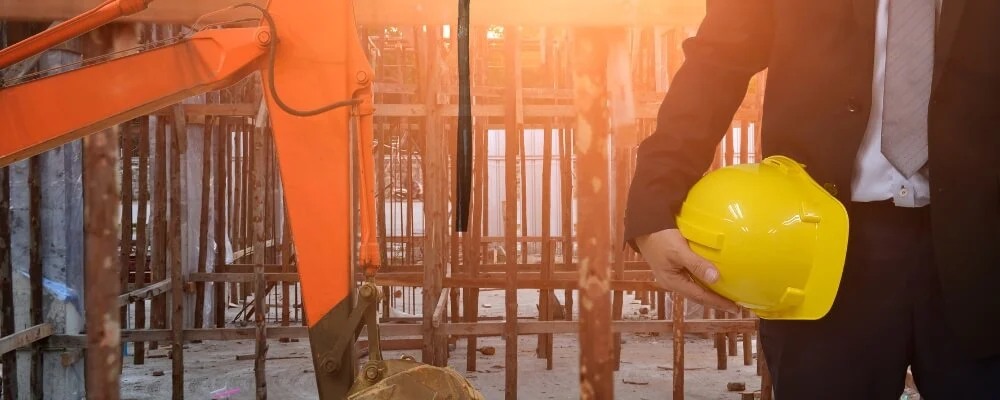
9. Fire Safety
Fires are among the most common and destructive hazards in a workplace. Preparedness for such an eventuality begins with having fire extinguishers readily available. But it’s equally important for employees to know how to use them. Different fires (electrical, chemical, or paper-based) require specific types of extinguishers, and using the wrong one can exacerbate the situation.
Modern workplaces also use smoke detectors and sprinkler systems as early warning and response systems. These devices need regular testing to ensure they are always functional. The objective is to detect a fire early, suppress it if possible, and allow safe evacuation.
10. Training and Education
Knowledge is the first line of defense in any safety protocol. Regular training sessions ensure employees are well-equipped to handle their roles’ specific challenges and risks. For new employees, an introduction to OHS procedures is essential. At the same time, refresher courses ensure that veterans are not complacent and are updated on new safety protocols or equipment.
Specific training sessions should be conducted whenever new machinery or procedures are introduced. This holistic approach to training ensures that the entire workforce is prepared, aware, and actively participating in maintaining a safe work environment.
Conclusion
Occupational Health and Safety (OHS) is vast, multifaceted, and crucial in every professional setting. As we’ve journeyed through these 10 different OHS procedures, it’s evident that they aren’t just checkboxes on a compliance form; they represent a deep-seated commitment to the health, safety, and overall well-being of every individual in a workplace.
By understanding and implementing these procedures, organizations uphold their legal and ethical responsibilities and foster a culture of care and respect. Such environments invariably lead to increased morale, efficiency, and productivity. In a world where change is the only constant, prioritizing the safety and health of employees remains a timeless tenet of good business and humane leadership.
No matter how advanced or basic its operations are, every organization would do well to embed these OHS procedures into its fabric. After all, a safe workplace is not just a right; it’s a cornerstone of sustainable success.