Occupational injuries are a concern that spans across industries, affecting workers and employers alike. Whether you’re working on a bustling construction site, typing away in a quiet office, or maneuvering through the dynamic environment of a hospital, workplace hazards exist everywhere. This blog post will delve into occupational injuries, exploring their definition, various types, causes, and, most importantly, strategies to prevent them.
With this knowledge, employers can create a safer work environment, while employees can be better equipped to protect themselves and their colleagues from potential harm. So, whether you’re an HR professional, a business owner, or a concerned worker, this comprehensive guide is essential for all committed to a safer workspace.
What’s Occupational Injury? Definition
An occupational injury refers to any bodily harm or damage resulting from activities or incidents occurring in the workplace. These injuries can arise from various occupational hazards, such as physical, chemical, biological, or psychosocial factors. They can affect various body parts, including the spine, hands, head, lungs, eyes, skeleton, and skin. Common causes include poor ergonomics, handling of heavy loads, equipment misuse or failure, exposure to hazardous substances or environments, and inadequate safety training.
The repercussions of such injuries can range from temporary incapacitation to permanent disability, significantly impacting an individual’s capacity to perform their job duties. Specific professions, such as construction, mining, fishing, and logging, often have a higher incidence of occupational injuries due to the nature of their tasks. Over time, societal and legal measures have evolved to offer compensation and support to injured workers and to hold employers accountable for ensuring safe working conditions.
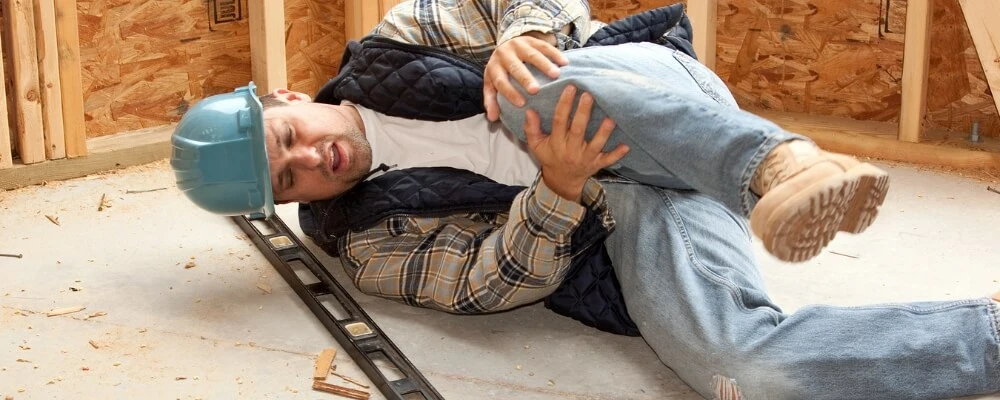
Types Of Occupational Injuries and Causes
Occupational injuries can occur in various settings and industries, resulting from various causes. Understanding the types of occupational injuries and their causes is essential for workplace safety and prevention. Here are some common types of occupational injuries and their associated causes:
1. Musculoskeletal Disorders (MSDs)
MSDs encompass a broad category of physical injuries affecting the body’s structural components. The root causes are often traced back to the workplace environment or the nature of the job. When workers repeatedly perform the same action, like typing on a computer or scanning items at a checkout counter, they exert continuous stress on certain body parts.
Without proper ergonomics, this repetitive motion can exacerbate the issue. For example, a poorly designed workstation or unsuitable chair height can result in sustained poor posture, increasing the risk of conditions such as carpal tunnel syndrome and a painful hand and arm condition.
2. Cuts and Lacerations
The risk of cuts and lacerations is heightened in work environments that involve handling sharp tools, machinery, or materials. The severity of these injuries can vary widely. For instance, in a culinary setting, a chef might accidentally cut themselves due to a brief lapse in concentration.
On the other hand, in manufacturing, an inattentive moment near a machine can lead to severe lacerations, which can sometimes be life-threatening. Training, therefore, is crucial to mitigate these risks.
3. Burns
An array of sources can cause burns that range from first-degree to third-degree burns, depending on their severity. For someone working in a kitchen, accidentally touching a hot pan might lead to a first-degree burn.
Meanwhile, in more industrial settings, workers handle chemicals, and without proper protective equipment, an accidental spill or splash can result in chemical burns that penetrate multiple layers of skin. The aftermath of such burns often requires specialized medical treatment.
4. Fractures and Broken Bones
Unexpected accidents that lead to sudden impacts, such as falls or being struck by an object, are common causes of fractures or broken bones. For instance, a construction worker on a scaffold without proper safety measures could fall and break a limb. Similarly, workers in warehouses might be at risk if heavy objects are not securely stored and end up falling onto them.
5. Sprains and Strains
These are among the more common workplace injuries. Even a seemingly benign task, such as lifting a box, can lead to an injury if not done correctly. Sprains involve the stretching or tearing of ligaments, while strains involve the same for muscles or tendons. For instance, lifting a heavy object with improper technique can put undue stress on the back, leading to strains that can be debilitating if not addressed.

6. Repetitive Strain Injuries (RSIs)
Over time, performing the same physical activity repeatedly can lead to injuries. These are termed RSIs, and they often develop slowly, presenting as mild discomfort initially but can progress to severe pain or dysfunction. For instance, an assembly line worker might develop a tennis elbow through continuously fitting parts, where the outer elbow becomes sore and tender.
7. Eye Injuries
The eyes are particularly vulnerable in many work settings. A simple task, like grinding metal without safety goggles, can lead to sparks or debris injuring the eye. Similarly, chemical splashes can cause irreversible eye damage in a laboratory if safety goggles aren’t worn.
In more specialized professions like welding, the intense light produced can cause what’s known as ‘welder’s flash,’ a painful condition where the cornea is burned. Protecting the eyes is paramount in such professions, given their vulnerability and importance.
8. Hearing Loss
In many industrial environments, the persistent roar of machinery or equipment can be loud. Over prolonged exposure, this constant barrage of noise can impair an individual’s hearing. For example, a factory worker operating next to a loud machine daily without ear protection might not notice the gradual decrease in their hearing ability until it becomes a significant issue.
Unfortunately, this noise-induced hearing loss is irreversible and can substantially impact a person’s quality of life.
9. Chemical Exposures
Hazardous chemicals pose a series of threats in the workplace. Beyond immediate dangers like chemical burns or explosions, prolonged exposure or accidental inhalation can lead to serious internal health issues. Consider a lab technician working with toxic substances.
If they don’t use fume hoods or wear masks, they might inhale dangerous fumes, leading to internal burns, poisoning, or long-term ailments. Proper handling, storage, and protection are essential to prevent such scenarios.
10. Respiratory Disorders
Many jobs expose workers to airborne contaminants. Over time, inhaling these pollutants can lead to respiratory diseases. For instance, construction sites often produce a lot of dust, including fine particles like silica.
When inhaled, this silica dust can settle in the lungs, leading to conditions such as silicosis, a lung disease that can be debilitating and even fatal. Regularly using masks and ensuring proper ventilation can help mitigate this risk.
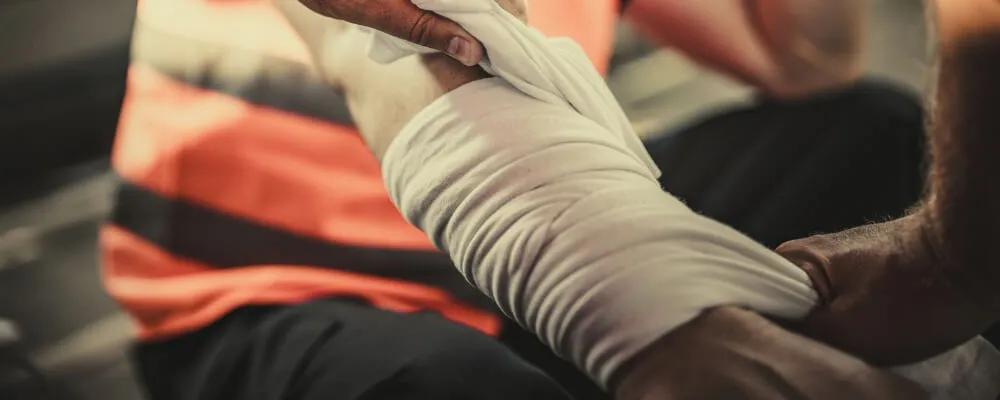
11. Falls
Falling accidents are prevalent in many work settings and can result from various causes. An office worker, for instance, might not notice a coffee spill on the floor, and a slip can lead to broken bones or concussions.
Working at heights amplifies the risk in more specialized professions, like roofing or window washing. A simple misstep can result in a devastating fall without appropriate harnesses or safety measures, leading to severe injuries or fatalities.
12. Struck by/Against Injuries
These injuries are common in dynamic environments where objects are in motion or space is constrained. In construction or warehouse settings, there’s always a risk of objects falling or being propelled accidentally. Imagine a construction site where bricks are hoisted upwards; if one gets dislodged, it could fall and injure a worker below.
Similarly, workers might inadvertently walk into or be struck by moving equipment in tight corridors or busy workshops, leading to bruises, fractures, or more severe injuries. Safety protocols and awareness are vital in preventing such accidents.
13. Caught In/Between
Industrial settings, particularly complex machinery, can pose unique risks to workers. These machines’ intricacies and fast-moving parts can be hazardous if safety protocols are not strictly followed. For example, workers not vigilant in a manufacturing line could find a piece of their clothing or a limb caught in the machinery.
Such incidents can result in severe injuries, amputations, or even fatalities. Regular maintenance, training, and safety checks are vital in preventing these unfortunate events.
14. Electrocution
Working with electricity is inherently risky, requiring a deep understanding and respect for its power. While highly trained, electricians can still face dangers, especially when dealing with high-voltage systems or when unexpected issues arise.
For instance, if an electrician were to accidentally touch a live wire without having properly turned off the circuit or if the wire’s insulation was compromised, the resulting shock could lead to severe injuries, burns, or even death. Safe practices, regular equipment checks, and ensuring circuits are off before working on them are critical for electrical safety.
15. Vehicular Accidents
Driving or operating any vehicle comes with its set of risks. Occupational drivers, whether truckers hauling cargo or delivery personnel in city environments, are constantly exposed to the hazards of the road. Conditions such as adverse weather, vehicle malfunctions, or driver fatigue can significantly increase the risk of accidents.
For example, a delivery driver working long hours might be more prone to mistakes due to fatigue, leading to potential road accidents. Regular vehicle maintenance and ensuring drivers take adequate breaks can help mitigate these risks.
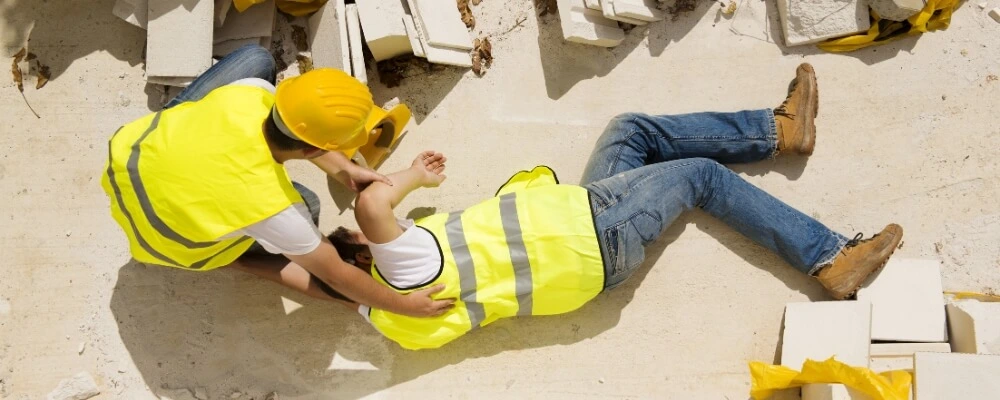
16. Exertion and Bodily Reaction
Everyday activities in the workplace, often considered benign, can accumulate stress on the body over time. Continuous actions can lead to chronic injuries, especially with incorrect posture or without proper ergonomic equipment.
A warehouse worker who spends hours every day bending down to lift boxes without using proper lifting techniques might develop chronic back pain or other musculoskeletal problems. Training on correct postures and ergonomic tools can help reduce such injuries.
17. Exposure to Harmful Substances or Environments
Certain jobs entail working under extreme conditions or with materials that can be harmful if proper precautions aren’t taken. Miners, for example, delve deep underground where the risk of exposure to toxic gases or cave-ins is high.
Without adequate ventilation or protective equipment, a miner could be at risk of inhaling toxic gases, leading to immediate health crises or long-term respiratory issues. Proper equipment, regular air quality monitoring, and emergency protocols are essential in such environments.
18. Violence and Assaults
While ideally, every workplace would be free from threats and conflicts, the reality is that tensions can sometimes escalate, or external threats can manifest. Security personnel are at the forefront of these risks. Still, even retail employees or office workers can find themselves in situations where they face threats from aggrieved individuals, be they coworkers or external actors.
For instance, a retail employee working late might be vulnerable to robberies or confrontations. Proactive conflict resolution training, security measures, and situational awareness can help minimize these risks.
This list is by no means exhaustive. Specific risks may lead to other unique injury types depending on the occupation. It’s also worth noting that prevention and safety measures can significantly reduce the risk of these injuries.
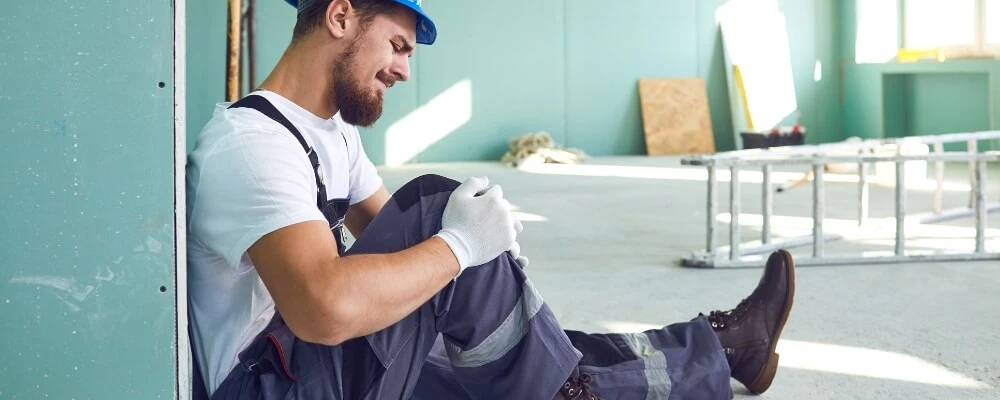
Prevention Strategies For Occupational Injuries
Preventing occupational injuries is vital for maintaining a safe and productive work environment. Here are several strategies that employers can implement to reduce the risk of injuries in the workplace:
- Risk Assessment: Begin with a thorough workplace assessment to identify potential hazards. This includes understanding the dangers associated with machinery, tools, chemicals, and the overall work environment.
- Regular Training: Ensure all employees receive comprehensive training on safety protocols, proper equipment usage, and best practices tailored to their roles. Refresher courses should also be held periodically.
- Provide Protective Equipment: Depending on the nature of the job, supply workers with necessary protective gear such as helmets, goggles, gloves, earplugs, and safety shoes. Ensure that the equipment is well-maintained and replaced when needed.
- Ergonomic Workstations: Design workstations to suit the ergonomic needs of workers. Adjustable chairs, proper lighting, keyboard setups, and other modifications can prevent strain injuries, especially in office settings.
- Maintain Equipment: Regularly inspect and maintain machinery, tools, and vehicles to ensure they’re in good working condition. Faulty equipment is a significant cause of workplace injuries.
- Clear Communication: Encourage an open dialogue about safety concerns. Workers should feel comfortable reporting potential hazards and near misses or suggesting improvements.
- Emergency Protocols: Have clear emergency response plans and ensure employees are familiar with them. This includes fire evacuation procedures, first-aid response, and reporting incidents.
- Good Housekeeping: Regularly clean and organize workspaces to prevent slip-and-fall hazards. Ensure pathways are clear, spills are cleaned promptly, and waste is disposed of correctly.
- Limit Work Hours: Overworking employees can lead to fatigue, decreased attention, and a higher risk of accidents. Ensure workers have adequate breaks and aren’t pushed beyond safe working hours.
- Health and Wellness Programs: Encourage overall health and wellness among employees. Fit employees are less likely to incur injuries as they generally have better strength, flexibility, and stamina.
- Continuous Monitoring: Establish a system to continuously monitor and evaluate workplace safety. This might include routine inspections, safety audits, or feedback sessions.
- Safety Culture: Cultivate a culture that prioritizes safety. When safety becomes a core value, employees at all levels become more proactive in preventing accidents and injuries.
- Stay Updated: Regulations, industry standards, and best practices evolve. Stay informed about the latest safety research and updates to ensure the workplace meets current standards.
By implementing these strategies, employers can create a safer work environment, reduce the risk of injuries, and promote the well-being of their employees.
Conclusion
In the complex landscape of the modern workplace, understanding occupational injuries is paramount for ensuring the safety and well-being of all employees. We’ve traversed the nuances of what defines an occupational injury, explored its various types, and delved into the root causes that lead to such incidents. But knowledge is most potent when paired with action.
By implementing robust prevention strategies, employers can dramatically reduce the incidence of injuries, ensuring compliance with regulations and fostering a safety culture. As we conclude our deep dive into occupational injuries, let it remind us that every workplace accident is one too many. With awareness, commitment, and proactive measures, we can collectively usher in an era where occupational safety is not just a priority but a norm.