In today’s fast-paced world, where efficiency often takes precedence, it’s vital to remember that safety should never be compromised. Safety protocols play a pivotal role in ensuring our well-being and those around us, whether on the road, in the office, or at a construction site. But why is it that safety often gets overlooked until a mishap occurs? It’s possibly because many see it as common sense or consider precautions as time-consuming. However, as the old adage goes, “Prevention is better than cure.” With this in mind, we’ve compiled a list of 15 Safety Golden Rules.
These guidelines and essential practices have been designed based on years of research, experience, and unfortunate accidents. Adhering to these rules can prevent accidents and save precious lives. Read on to discover these foundational principles that can transform how we approach everyday tasks and specialized jobs.
15 Safety Golden Rules To Prevent Accidents and Save Lives
Golden safety rules are fundamental principles that guide individuals and organizations in preventing accidents and promoting a safe environment. While the specific rules may vary depending on the industry or context, here are 15 general safety golden rules that can help prevent accidents and save lives:
1. Use Tools and Equipment Correctly
Every tool or piece of machinery is designed with specific functions in mind and has its set of operational guidelines. Using tools in ways they weren’t intended or operating machinery without proper training can lead to malfunctions, breakages, or accidents.
Additionally, even if trained, it’s essential to ensure that the tools and machinery are in good condition. Worn-out tools or malfunctioning machinery can be unpredictable and dangerous. Regular maintenance checks and adhering to operational guidelines ensure that tools and equipment function safely and effectively.
2. LOTO (Lock Out-Tag Out)
The Lock Out-Tag Out (LOTO) procedure is crucial when servicing and maintaining equipment and machinery. This procedure ensures that machines are powered down and cannot be started up unexpectedly while maintenance work is in progress. Such unexpected startups can lead to serious injuries.
By locking out the machinery, workers ensure that only they have control over when the machine can be powered back up. The tagging out part involves placing a tag on the locked device to inform others not to power it up. This dual system is a clear communication tool, ensuring everyone’s safety.
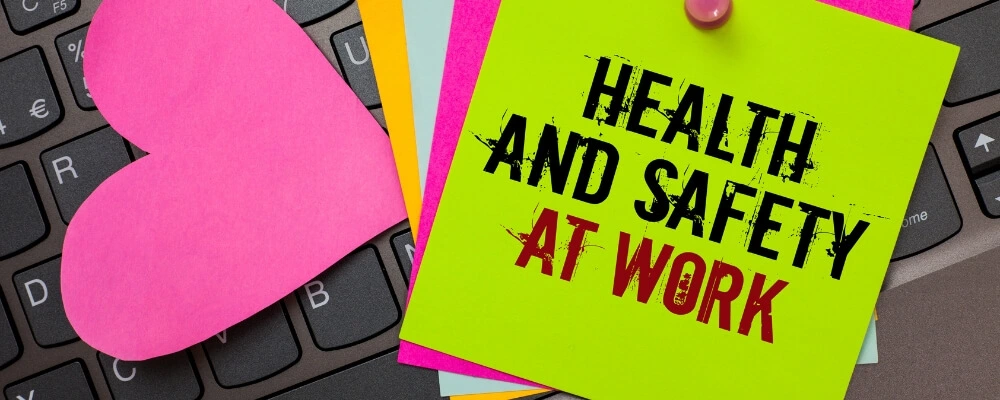
3. No Permit, No Work
A work permit system is a formal written system that outlines how certain work activities should be conducted to ensure the safety of both workers and the surrounding environment. Ensuring a permit is obtained before any task guarantees that all potential risks have been thoroughly assessed.
Obtaining a permit often requires a thorough review of the task, identification of potential hazards, and ensuring adequate safety measures. It’s not just about paper compliance; it’s about creating a culture of safety awareness and diligence.
4. Use Personal Protective Equipment (PPE)
PPE is the last line of defense against workplace hazards. Whether dealing with flying debris, hazardous chemicals, or loud noise, the right PPE can significantly reduce the risk of injury. For example, safety glasses can prevent eye injuries from splashes or flying objects, while gloves can protect hands from chemicals or cuts.
Helmets can shield against falling objects, and earplugs can prevent hearing damage in noisy environments. However, wearing PPE is only part of the solution. Regularly inspecting PPE ensures it remains effective in its protective role. Damaged or worn-out PPE can give a false sense of security while providing minimal protection.
5. Work at Height
Working at heights is inherently risky, given the potential for falls, which can lead to severe injuries or even fatalities. Before initiating any work at an elevated position, it’s crucial to have safety measures like guardrails, nets, and safety harnesses. These measures not only prevent falls but can also protect workers below from falling objects.
Additionally, any equipment used for fall protection, such as harnesses and lanyards, should be inspected regularly. Over time, wear and tear can render these safety tools ineffective, and regular checks ensure their integrity.
6. Confined Space Entry
Confined spaces, like tanks, vessels, silos, and pits, pose unique risks due to their limited access and egress points, potential for hazardous atmospheres, and the possibility of engulfment. Entering a confined space without proper precautions can be fatal.
Critical safety protocols include testing and monitoring the atmosphere for toxic gases, ensuring sufficient ventilation, and having a standby person outside the confined space. This standby person monitors the worker’s safety and is ready to call for help or initiate rescue procedures if anything goes wrong.
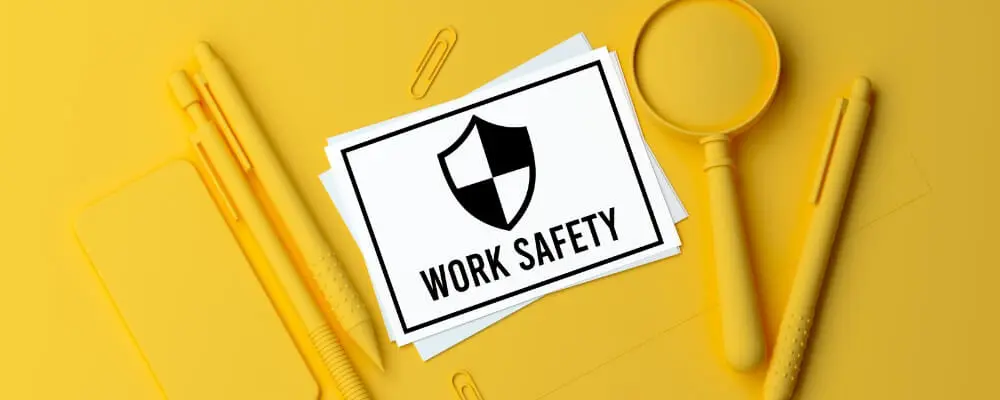
7. Lifting Operations
Lifting, whether manual or using machinery, poses risks like strains, sprains, and, in the case of equipment like cranes, the potential for catastrophic accidents if loads are dropped or if the machinery tips over. Proper lifting techniques should be employed to protect the back and other muscles. For heavier loads requiring equipment, machinery should be in good working condition, and operators should be adequately trained.
Spotters are vital in guiding the operator, especially in areas with limited visibility or requiring precision. Their role is to ensure the path is clear and to communicate any potential hazards to the operator in real-time.
8. Never Bypass Safety Devices
Safety devices, such as machine guards, interlock systems, and emergency stop buttons, are integrated into systems and machinery to prevent injuries and mishaps. These devices have been designed based on historical accidents, risks identified during design and engineering processes, or regulatory requirements.
When someone chooses to bypass or tamper with these devices, they not only put themselves at risk but also jeopardize the safety of others around them. A machine operating without its safety devices is like driving a car without brakes—an accident waiting to happen.
9. Safe Driving
The act of driving is a complex task that requires full attention and adherence to traffic rules. Speed limits are set based on various factors, including road conditions, traffic flow, and the type of area (residential, commercial, etc.). Exceeding these limits increases the risk of accidents due to reduced reaction time and longer stopping distances.
Distractions from phone usage, eating, or other activities divert attention from the road and can result in fatal accidents. Driving under the influence of alcohol or drugs severely impairs judgment and reaction times, making it a significant cause of traffic fatalities. Additionally, ensuring your vehicle is in good condition through regular maintenance reduces the risk of malfunctions that can lead to accidents.
10. Follow Safety Procedures
Every task or job has associated risks. Safety procedures are developed based on a thorough understanding of these risks and are designed to mitigate them. Whether it’s the correct way to operate a machine, the safe method to mix chemicals, or the right way to lock out equipment, these procedures are the blueprint for safe operations. Ignoring or deviating from these procedures can lead to unforeseen consequences, endangering the individual and those around them.
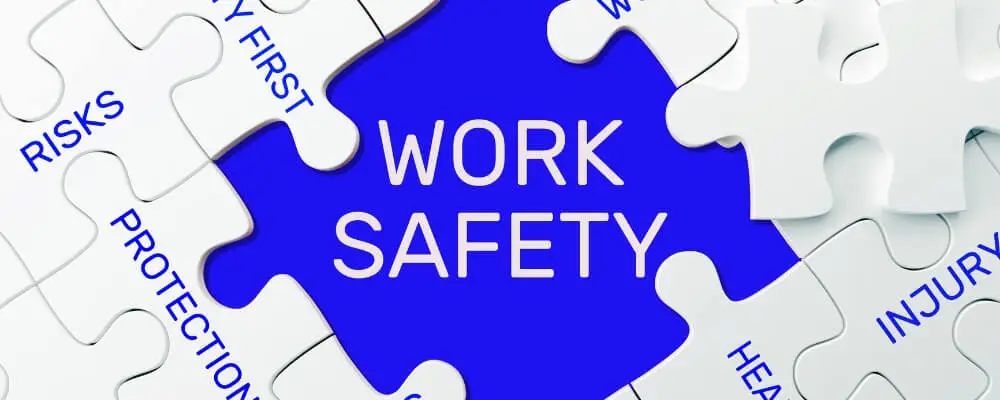
11. Report Accidents/Incidents
While the primary aim is always to prevent accidents or incidents, it’s crucial to report them promptly when they do occur. Immediate reporting allows swift action, whether medical attention for an injured colleague or corrective action to prevent further incidents. Beyond the immediate response, reporting also plays a vital role in an organization’s long-term safety strategy.
Analyzing accidents and near-misses provides valuable insights into potential system weaknesses or areas of concern. This information can be used to refine safety procedures, enhance training, and ensure a safer work environment for everyone.
12. Stay Informed
Safety is an evolving discipline, with new research, technologies, and methodologies continuously emerging. Staying informed through regular safety training is crucial. Training sessions can introduce workers to new equipment, teach them about updated regulations, or refresh their memories on essential safety practices.
Furthermore, their risks and hazards may evolve as industries grow and change. By keeping abreast of the latest safety standards and best practices, workers and organizations can ensure they’re always ahead of potential dangers, minimizing the risk of accidents.
13. Avoid Distractions
Distractions can significantly impair a person’s ability to focus, leading to mistakes or oversights that can have severe consequences. For instance, using a mobile phone while driving or operating machinery divides one’s attention and slows reaction times, making it harder to respond to sudden hazards.
In many work environments, a momentary lapse in concentration can lead to significant accidents. Therefore, maintaining focus and minimizing interruptions or distractions is pivotal in ensuring personal safety and the safety of those around.
14. Communicate
Communication is the linchpin of safety in team environments. Whether it’s a change in plans, a newly spotted hazard, or feedback on a particular process, sharing information ensures everyone is on the same page. When workers openly communicate, they create an environment where risks are spotted and addressed more rapidly.
For instance, if a worker identifies a potential hazard, communicating it ensures that others are aware and can take precautions. Likewise, if there are environmental changes, such as a wet floor or malfunctioning equipment, letting others know prevents potential accidents.
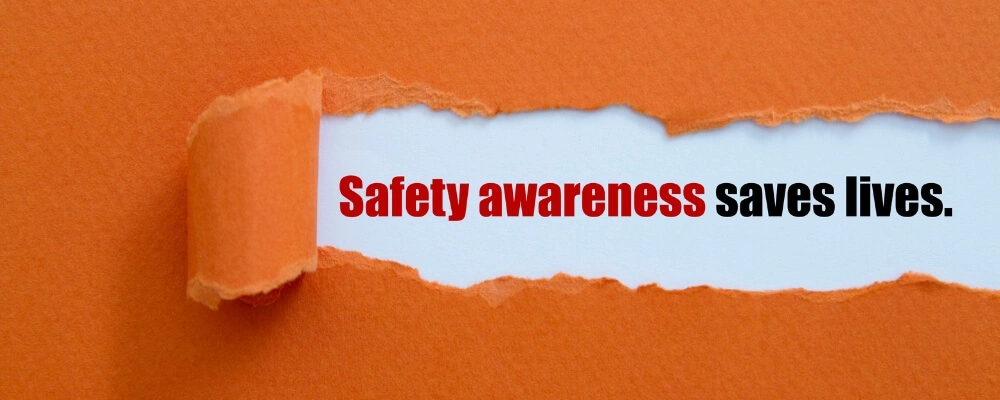
15. Plan Ahead
Proper planning is one of the most effective ways to prevent accidents. Before undertaking any task, a thorough risk assessment should be conducted to identify potential hazards. Once these hazards are known, steps can be taken to mitigate them. Additionally, preparedness goes beyond just the immediate task. Knowing the location of first aid kits ensures rapid response in case of minor injuries.
Similarly, being aware of emergency exits ensures that everyone can evacuate swiftly and safely in the event of an emergency like a fire or chemical spill. By planning ahead, workers and organizations can anticipate and counteract many risks they might face.
Conclusion
Safety is not just a protocol; it’s a mindset, a commitment to preserving the well-being of ourselves and those around us. The 15 Safety Golden Rules we’ve discussed are not mere recommendations; they represent the collective wisdom drawn from countless experiences, some of which had regrettable consequences.
By embedding these rules into our daily routines and work processes, we fortify our environments against accidents and foster a culture where safety becomes second nature. Remember, it’s not about navigating a checklist but about creating an environment where every life is valued, every hazard is addressed, and every accident is too many. As we progress, let these golden rules serve as our compass, guiding us toward safer choices, actions, and outcomes.
Also Read: Workplace Accident Report | Which Key Information To Include