A safe and healthy work environment is essential for employee well-being and the overall success of a business. Workplace hazards are any aspect of work that has the potential to cause harm, illness, or injury to employees. These hazards can range from physical dangers, such as slips and falls, to less visible hazards like stress and ergonomic issues. It is crucial for employers and employees to recognize these hazards and take proactive measures to prevent them. By identifying and addressing potential risks, companies can protect their workers, minimize lost productivity, reduce costs associated with workplace accidents, and maintain a positive reputation.
In this article, we will discuss 10 of the most common workplace hazards, their potential consequences, and effective strategies to prevent them. By understanding these hazards and implementing appropriate prevention measures, employers can create a safer, healthier, and more productive work environment for their staff.
Workplace Hazards and How to Prevent Them
Workplace hazards refer to anything in a work environment that can cause harm to employees or pose a risk to their health and safety. Here are 10 common types of workplace hazards and ways to prevent them:
1. Slips, Trips, and Falls
Slips, trips, and falls are among the most common workplace hazards and can lead to severe injuries, including sprains, fractures, and even fatalities. They can occur in any work environment and often result from a variety of causes, including wet or slippery floors, cluttered work areas, loose cables, and poor lighting.
Common causes:
- Wet floors: Spilled liquids or recently mopped surfaces can create slippery conditions that increase the risk of slips and falls.
- Clutter: Obstructed walkways, disorganized storage areas, and random items on the floor can cause employees to trip or lose their balance.
- Loose cables: Unsecured cables or cords running across walkways can easily become a tripping hazard for unsuspecting employees. Wearing protective gear such as slip-resistant shoes and metatarsal guards can provide additional protection against falling objects and reduce the risk of foot injuries.
- Poor lighting: Insufficient lighting can make it difficult for employees to see potential hazards, increasing the risk of slips, trips, and falls.
Prevention strategies:
- Cleaning: Regular cleaning and maintenance can help prevent wet floors, spills, and clutter. Establish a routine cleaning schedule and promptly address spills or wet areas.
- Proper signage: Use clear and visible signs to warn employees of potential hazards, such as wet floors, uneven surfaces, or areas under construction. This can help workers avoid these hazards and take necessary precautions.
- Cable management: Keep cables and cords organized and secure, either by routing them along walls or using cable covers and floor runners to prevent them from becoming a tripping hazard.
- Adequate lighting: Ensure that all work areas have sufficient lighting so employees can easily identify and avoid potential hazards. Regularly check and replace any burned-out or faulty light bulbs.
By addressing these common causes and implementing these prevention strategies, employers can significantly reduce the risk of slips, trips, and falls in the workplace and create a safer environment for their employees.
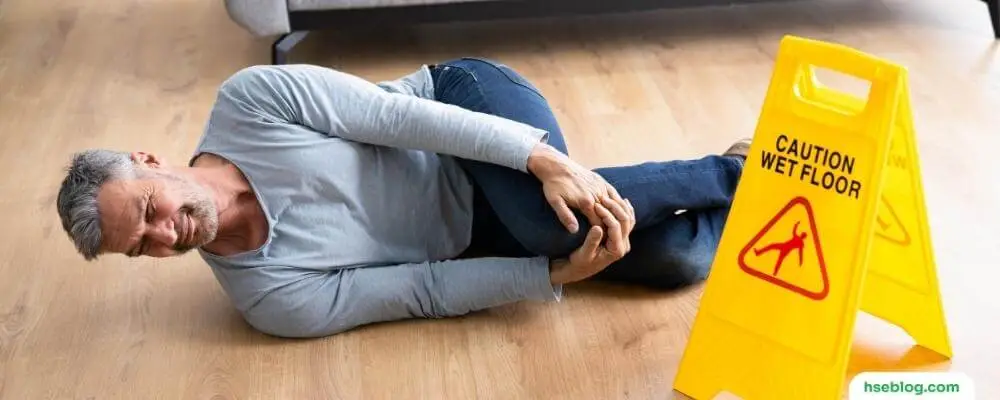
2. Ergonomic Hazards
Ergonomic hazards are physical factors within the work environment that can cause musculoskeletal disorders (MSDs), such as carpal tunnel syndrome, tendonitis, and back pain. These hazards often result from poor workstation design, repetitive motions, awkward postures, and prolonged sitting or standing. By addressing ergonomic hazards, employers can help prevent MSDs and maintain a healthy workforce.
Risk factors:
- Poor posture: Maintaining awkward or uncomfortable postures for extended periods can strain muscles, tendons, and ligaments, leading to discomfort and long-term injury.
- Repetitive motions: Performing the same motion repeatedly without sufficient breaks can cause stress on muscles and joints, potentially leading to chronic pain or injury.
- Prolonged sitting or standing: Remaining in the same position for extended periods can result in muscle fatigue, decreased circulation, and increased risk of MSDs.
Prevention strategies:
- Ergonomic equipment: Provide employees with ergonomically designed workstations and equipment, such as adjustable chairs, sit-stand desks, and properly positioned monitors, to promote a neutral body posture and reduce strain.
- Rest breaks: Encourage employees to take regular breaks to rest, stretch, and change positions. Implementing a policy of short, frequent breaks can help reduce the risk of MSDs and increase productivity.
- Training: Offer training and education on proper ergonomics, body mechanics, and workstation setup. Educate employees on how to identify and report ergonomic hazards and encourage them to take an active role in their own well-being.
By recognizing ergonomic risk factors and implementing appropriate prevention strategies, employers can create a more comfortable and productive work environment that minimizes the risk of injury and promotes overall employee health.
3. Fire and Explosion Hazards
Fires and explosions can have devastating consequences in the workplace, leading to significant property damage, injuries, or even fatalities. These hazards are often the result of improper handling or storage of flammable materials, electrical malfunctions, and inadequate ventilation. To protect employees and assets, it is vital to understand the common causes of fires and explosions and implement effective prevention strategies.
Common causes:
- Flammable materials: Mishandling or improper storage of flammable liquids, gases, or combustible dust can increase the risk of fires or explosions.
- Electrical issues: Overloaded circuits, faulty wiring, or damaged electrical equipment can cause electrical fires, which may lead to explosions if they ignite flammable materials.
- Poor ventilation: Inadequate ventilation can cause the build-up of flammable vapors, gases, or dust, increasing the risk of an explosion if an ignition source is present.
Prevention strategies:
- Fire safety training: Educate employees on fire and explosion hazards, proper handling and storage of flammable materials, and the use of fire extinguishers. Regular training can help ensure that employees are aware of potential risks and know how to respond in case of an emergency.
- Equipment maintenance: Conduct regular inspections and maintenance of electrical systems, machinery, and equipment to identify and correct potential hazards. Implement a preventive maintenance schedule to reduce the risk of equipment malfunction and electrical fires.
- Emergency plans: Develop and communicate a comprehensive emergency plan that includes evacuation procedures, designated assembly areas, and emergency contacts. Conduct regular fire drills to familiarize employees with emergency procedures and ensure that they know how to respond in case of a fire or explosion.
By understanding the common causes of fires and explosions and implementing these prevention strategies, employers can create a safer work environment and minimize the risk of costly and dangerous incidents.
4. Electrical Hazards
Electrical hazards are a significant concern in many workplaces, as they can lead to serious injuries, such as electric shocks, burns, or even electrocution. Electrical hazards can arise from various sources, including faulty wiring, overloaded outlets, and damaged equipment. By understanding the causes of electrical hazards and implementing effective prevention strategies, employers can protect their employees and maintain a safe work environment.
Causes:
- Faulty wiring: Damaged or poorly installed wiring can create a risk of electrical shocks, fires, or short circuits, putting employees in danger.
- Overloaded outlets: Plugging too many devices into a single outlet or using extension cords improperly can overload circuits, increasing the risk of electrical fires or equipment damage.
- Damaged equipment: Frayed cords, loose connections, or malfunctioning equipment can create electrical hazards that may result in injury or damage to property.
Prevention strategies:
- Regular inspections: Conduct periodic inspections of electrical systems, wiring, and equipment to identify and address potential hazards. Schedule maintenance and repairs as needed to ensure the safe operation of all electrical components.
- Proper training: Provide training for employees on electrical safety, including the identification of electrical hazards, the use of personal protective equipment (PPE), and safe work practices. Ensure that employees who work with or around electrical systems have the necessary skills and knowledge to perform their tasks safely.
- Lockout/tagout procedures: Implement and enforce lockout/tagout (LOTO) procedures to ensure that electrical equipment is properly shut down and secured before maintenance or repair work is performed. LOTO procedures help prevent accidental energizing of equipment, protecting workers from electrical injuries.
By addressing the causes of electrical hazards and implementing these prevention strategies, employers can significantly reduce the risk of electrical accidents and create a safer work environment for their employees.
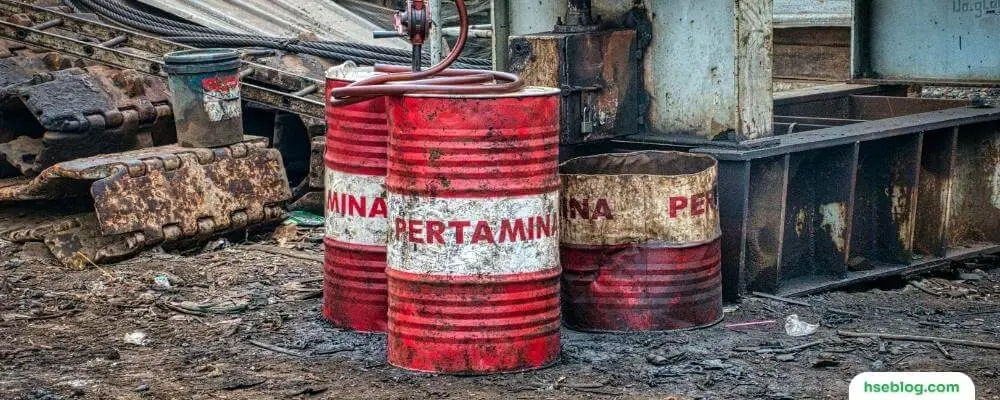
5. Chemical Hazards
Chemical hazards pose a significant risk to employees in various industries, from manufacturing and construction to laboratories and healthcare. Exposure to hazardous chemicals can cause acute or chronic health effects, including skin irritation, respiratory problems, and poisoning. Understanding the different types of exposure and implementing effective prevention strategies can help employers protect their employees from harmful chemical exposure.
Types of exposure:
- Inhalation: Breathing in airborne contaminants such as dust, vapors, or gases can cause respiratory irritation, asthma, or other serious lung conditions.
- Skin contact: Direct contact between chemicals and the skin can lead to irritation, burns, or the absorption of harmful substances into the bloodstream.
- Ingestion: Accidental swallowing of hazardous chemicals can result in poisoning, internal burns, or other severe health issues.
Prevention strategies:
- Proper storage: Store chemicals according to the manufacturer’s guidelines and regulatory requirements, using appropriate containers and labels. Segregate incompatible chemicals to prevent reactions, leaks, or spills.
- Ventilation: Ensure adequate ventilation in work areas where chemicals are used or stored. Proper ventilation can help control airborne concentrations of hazardous substances, reducing the risk of inhalation exposure.
- Personal protective equipment (PPE): Provide employees with appropriate PPE, such as gloves, goggles, and respirators, to protect them from chemical exposure. Ensure that employees are trained on the correct use, maintenance, and disposal of PPE.
By recognizing the types of chemical exposure and implementing these prevention strategies, employers can minimize the risk of hazardous chemical exposure and create a safer work environment for their employees.
6. Biological Hazards
Biological hazards refer to living organisms or substances derived from them that can pose a threat to human health. These hazards can be found in various workplaces, such as healthcare settings, laboratories, agriculture, and food service. Exposure to biological hazards can lead to infections, allergies, and other adverse health effects. By understanding the sources of these hazards and implementing effective prevention strategies, employers can protect their employees and maintain a safe work environment.
Sources:
- Bacteria: Pathogenic bacteria can cause infections and illnesses, such as foodborne diseases or respiratory infections.
- Viruses: Viruses, such as the flu or COVID-19, can spread rapidly in the workplace, causing outbreaks and impacting employee health.
- Mold: Mold growth in damp or humid environments can cause allergic reactions, respiratory issues, or other health problems.
- Animal waste: Exposure to animal waste or contaminated materials in agricultural or veterinary settings can lead to infections or parasitic diseases.
Prevention strategies:
- Sanitation: Maintain a clean and sanitary work environment by regularly cleaning and disinfecting surfaces, equipment, and common areas. Dispose of waste materials properly to prevent the spread of pathogens.
- Personal hygiene: Encourage employees to practice good personal hygiene, such as regular hand washing, using hand sanitizer, and covering their mouth and nose when coughing or sneezing. Provide appropriate facilities and supplies to support good hygiene practices.
- Vaccinations: Encourage employees to stay up-to-date on recommended vaccinations, including those for seasonal flu or other relevant diseases. Consider offering vaccination programs or providing information on where employees can receive vaccinations.
By recognizing the sources of biological hazards and implementing these prevention strategies, employers can minimize the risk of illness and infection in the workplace, contributing to a safer and healthier work environment for all employees.
7. Noise Hazards
Exposure to excessive noise levels in the workplace can have detrimental effects on employees’ health and well-being. Prolonged exposure to high noise levels can lead to hearing loss, increased stress, and sleep disruption, among other issues. Industries such as manufacturing, construction, and transportation are particularly susceptible to noise hazards. By understanding the dangers of prolonged exposure and implementing effective prevention strategies, employers can protect their employees from the harmful effects of noise.
Dangers of prolonged exposure:
- Hearing loss: Long-term exposure to loud noises can cause permanent hearing loss or tinnitus (ringing in the ears), impacting an individual’s quality of life and ability to perform work tasks effectively.
- Stress: High noise levels can contribute to increased stress levels, which can, in turn, negatively affect an employee’s mental health, job satisfaction, and productivity.
- Sleep disruption: Employees who are exposed to excessive noise levels during their work hours may experience difficulty sleeping, leading to fatigue, decreased concentration, and increased risk of accidents or errors at work.
Prevention strategies:
- Hearing protection: Provide employees with appropriate hearing protection devices, such as earplugs or earmuffs, and ensure that they are trained on their proper use and maintenance. Regularly assess the effectiveness of hearing protection and replace worn or damaged devices as needed.
- Noise barriers: Implement noise barriers or enclosures around loud equipment to reduce noise levels in the work environment. These barriers can be made of materials such as foam, acoustic panels, or curtains that help absorb or block sound.
- Equipment maintenance: Regularly inspect and maintain machinery and equipment to ensure that it operates as quietly and efficiently as possible. Upgrading to newer, quieter equipment or implementing noise reduction features can also help minimize noise hazards.
By understanding the dangers of prolonged noise exposure and implementing these prevention strategies, employers can create a healthier and more comfortable work environment for their employees while reducing the risk of noise-related health issues.
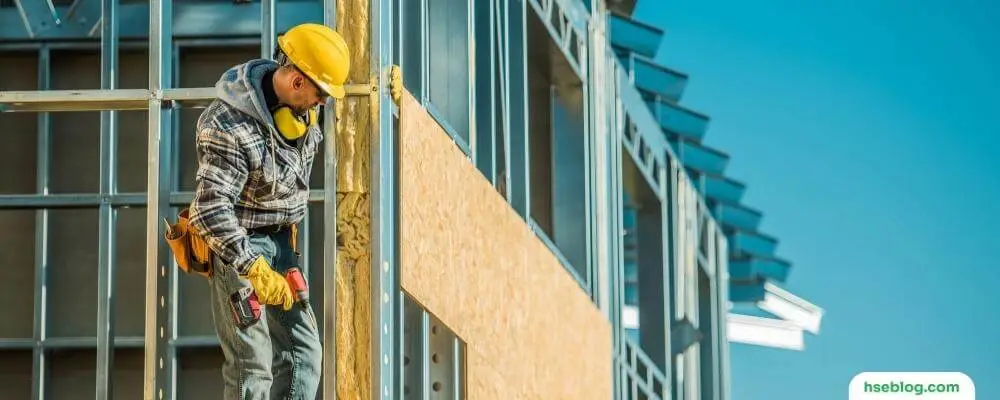
8. Working at Heights
Working at heights is a common risk factor in various industries, such as construction, maintenance, and telecommunications. Falls from elevated surfaces, like ladders, scaffolding, or roofs, can lead to severe injuries or even fatalities. By understanding the risk factors associated with working at heights and implementing effective prevention strategies, employers can protect their employees and maintain a safe work environment.
Risk factors:
- Falls from ladders: Improper use, incorrect ladder selection, or poorly maintained ladders can result in falls, leading to injuries or fatalities.
- Falls from scaffolding: Inadequate scaffolding setup, lack of guardrails, or failure to follow safety protocols can contribute to fall accidents.
- Falls from roofs: Slippery or uneven surfaces, inadequate fall protection, or lack of training can increase the risk of falls from roofs.
Prevention strategies:
- Fall protection: Provide appropriate fall protection equipment, such as guardrails, safety nets, and personal fall arrest systems, to minimize the risk of falls. Ensure that employees are trained in the proper use and maintenance of fall protection equipment.
- Proper training: Offer comprehensive training on working at heights, including the correct setup and use of ladders, scaffolding, and fall protection equipment. Regularly reinforce safety protocols and encourage employees to report any unsafe conditions or practices.
- Equipment inspections: Conduct regular inspections of ladders, scaffolding, and fall protection equipment to ensure they are in good working condition. Remove damaged or faulty equipment from service and replace it as necessary.
By addressing the risk factors associated with working at heights and implementing these prevention strategies, employers can significantly reduce the risk of falls and create a safer work environment for their employees.
9. Workplace Violence
Workplace violence encompasses a wide range of aggressive behaviors, including physical, verbal, emotional, and psychological abuse. It can affect employees across all industries and can lead to serious consequences, such as injuries, decreased productivity, and a negative work environment. By understanding the different types of workplace violence and implementing effective prevention strategies, employers can protect their employees and maintain a safe and supportive work environment.
Types:
- Physical: Physical violence includes acts such as hitting, pushing, or other forms of assault that can result in injury or harm.
- Verbal: Verbal violence involves the use of threatening, intimidating, or offensive language that can create a hostile work environment.
- Emotional or psychological: Emotional or psychological abuse includes behaviors such as bullying, harassment, or manipulation, which can have a significant impact on an employee’s mental health and well-being.
Prevention strategies:
- Zero-tolerance policy: Implement a zero-tolerance policy for workplace violence, clearly outlining the behaviors that are considered unacceptable and the consequences for those who engage in such conduct. Ensure that this policy is communicated to all employees and consistently enforced.
- Training: Provide training for employees on how to recognize, report, and respond to workplace violence. Training should include information on conflict resolution, de-escalation techniques, and how to seek support when faced with violent situations.
- Security measures: Implement security measures, such as access control systems, surveillance cameras, and on-site security personnel, to help deter and manage incidents of workplace violence. Encourage employees to report any security concerns or incidents promptly.
By understanding the different types of workplace violence and implementing these prevention strategies, employers can create a safer and more positive work environment for all employees, reducing the risk of violence and its associated consequences.
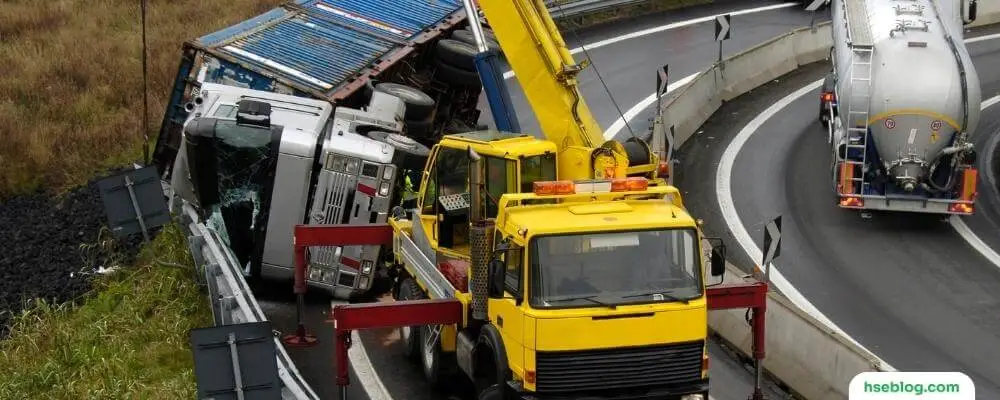
10. Vehicle Accidents
Vehicle accidents are a significant concern for workplaces that involve the operation of vehicles, such as transportation, delivery, or construction. These accidents can result in severe injuries, fatalities, and property damage. Common causes of vehicle accidents include distracted driving, speeding, and inadequate training. By understanding these causes and implementing effective prevention strategies, employers can protect their employees and minimize the risk of vehicle accidents.
Common causes:
- Distracted driving: Operating a vehicle while engaging in other activities, such as texting or talking on the phone, can significantly increase the risk of accidents.
- Speeding: Driving at excessive speeds or failing to adjust speed for road and weather conditions can lead to collisions and other incidents.
- Inadequate training: Drivers who are not properly trained in vehicle operation or safety procedures are more likely to be involved in accidents due to errors or poor judgment.
Prevention strategies:
- Safe driving training: Provide comprehensive training for employees who operate vehicles as part of their job duties. Training should include defensive driving techniques, hazard recognition, and proper vehicle handling. Regularly reinforce safety procedures and provide refresher courses as needed.
- Vehicle maintenance: Implement a routine maintenance schedule for all company vehicles to ensure they are in good working condition. Regular inspections and repairs can help identify and address potential safety issues before they lead to accidents.
- Safety policies: Establish and enforce safety policies that promote responsible driving, such as prohibiting the use of mobile devices while driving, requiring the use of seat belts, and setting appropriate speed limits for different road conditions. Encourage employees to report any unsafe driving behaviors or incidents promptly.
By understanding the common causes of vehicle accidents and implementing these prevention strategies, employers can reduce the risk of accidents, protect their employees, and promote a culture of safety within the workplace.
Conclusion
Proactive hazard management is essential for creating and maintaining a safe work environment for employees across all industries. By identifying and addressing potential hazards before they lead to accidents or injuries, employers can significantly reduce the risks associated with various workplace activities. Implementing effective prevention strategies for the top workplace hazards, as outlined in this article, can help protect employees from harm and minimize the costs associated with accidents, injuries, and lost productivity.
It is crucial for employers to prioritize safety in the workplace by fostering a culture where employees feel encouraged to report hazards, participate in safety training, and follow established safety procedures. By doing so, businesses can not only protect their workforce but also improve overall employee satisfaction, productivity, and company reputation.
In conclusion, recognizing and preventing workplace hazards is an ongoing responsibility for employers and employees alike. By working together to identify, address, and mitigate potential risks, we can create a safer, healthier, and more productive work environment for everyone.