Ensuring the safety of employees within a workspace remains a paramount concern for any thriving organization. With the rise in workplace accidents, stakeholders are urged to prioritize and improve workplace safety measures. The incorporation of a safer work environment not only abolishes potential hazards but also significantly boosts employees’ productivity, morale, and overall job satisfaction.
Adopting safety protocols, providing safety training, and installing safety equipment are a necessity. This article underlines the importance of workplace safety and offers resourceful strategies for enhancing the efficiency of safety protocols for a guaranteed safer working environment.

10 Effective Strategies/Ideas to Improve Workplace Safety
Creating a safe work environment is not just a legal duty; it’s a critical component in the long-term success of any business. Improving workplace safety is an ongoing process that requires commitment and proactive strategies. Here are ten steps to enhance safety in the workplace and foster a robust safety culture.
1. Establish a Safety-First Culture
An effective safety culture is the foundation of a safe workplace. This means that every aspect of the work environment, from management to the newest employee, prioritizes safety above all else. To cultivate this culture, businesses must ensure that all employees understand the importance of safety and are trained to follow safety protocols. Regular meetings to review safety rules and discuss prevention can keep workplace safety top of mind.
2. Conduct Regular Risk Evaluations
Regular risk evaluations are crucial in identifying potential hazards. Appoint or nominate a safety captain who is empowered to communicate concerns identified by employees to leadership. This proactive approach ensures that risks are assessed and appropriate measures are taken to mitigate them.
3. Implement Comprehensive Safety Training
Safety training for their positions is essential for all employees. Training should be ongoing and evolve with new safety protocols and technologies. Employees who follow safety policies help keep everyone safe and can prevent work injuries by visiting areas where there’s a high risk for employee injury and ensuring that appropriate safety measures are in place.
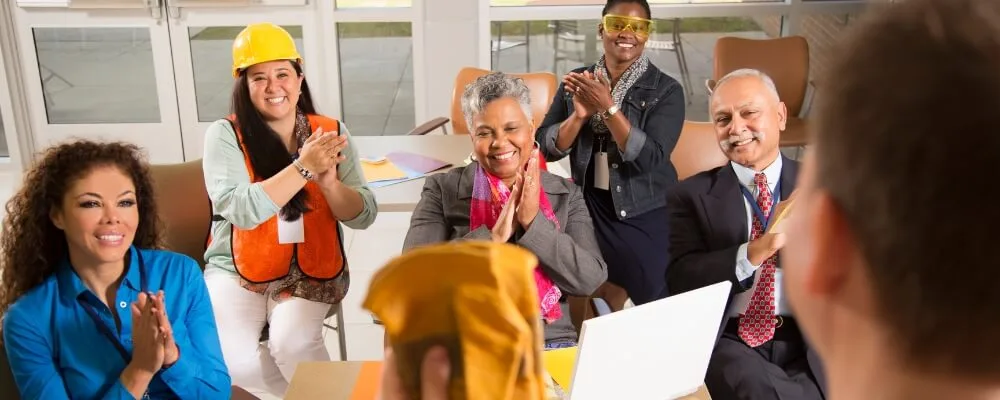
4. Improve Workplace Ergonomics
Ergonomics plays a significant role in preventing workplace injuries, especially repetitive motion injuries. Improve workplace ergonomics and develop human performance by consulting with physical and occupational therapists. These professionals can help you screen candidates for physically demanding roles and aid in the return-to-work process for those recovering from injuries.
5. Keep the Workplace Clean and Organized
A messy workplace can lead to accidents and reduce productivity. Ensure that walkways are clear of clutter, cords are securely fastened, and tools are stored properly. Labels and signs can help maintain organization and remind employees of safety practices.
6. Use Labels and Signs Effectively
Labels and signs are simple steps to improve workplace safety. They provide quick, visual reminders of potential hazards and safety procedures. Ensure that these are up to-date and clearly visible in all necessary areas.
7. Provide the Right Tools and Equipment
A safe workplace has the right tools for the job. This includes personal protective equipment (PPE), ergonomic furniture, and safety guards on machinery. Regular maintenance and updates of equipment can also reduce workplace hazards.

8. Encourage Open Communication
It’s your responsibility to create an environment where employees feel comfortable reporting hazards right away and identifying potential areas of concern they may not have noticed. An open-door policy can help facilitate this communication.
9. Prepare for Emergencies
Have emergency plans in place, including evacuation routes, emergency contacts, and access to first aid. Regular drills can help ensure that, in the event of an emergency, everyone knows what to do.
10. Reward Safe Behavior
A way to encourage a strong workplace safety culture is to reward safe behavior. Recognize and reward employees and teams that exemplify safety protocols and contribute to preventing workplace accidents. This positive reinforcement can help keep safety processes at the forefront of everyone’s mind.
By implementing these strategies, businesses can end up not only protecting their employees but also improving overall morale and productivity. Remember, a safe workplace is a productive one, and the steps to improve workplace safety are usually simple and cost-effective. Take five minutes to stretch, report hazards right away, and always keep your workplace safe.
