A permit-to-work system is a process used in industrial and manufacturing settings to ensure the safety of employees. This system requires workers to obtain a permit before starting any job that could potentially be hazardous. This blog post will provide you with a checklist for assessing permit-to-work systems. Using this checklist, you can determine if your company’s permit-to-work system is effective and safe!
This checklist aims to help everyone concerned with the preparation of permit-to-work systems to decide whether a permit-to-work system covers all the points considered essential in this guidance. The checklist is intended for use when setting up a new permit-to-work system or auditing an existing one.
Permit To Work Systems Checklist For The Assessment
A Permit to Work (PTW) system is a formal written system used to control certain types of work identified as potentially hazardous. PTW systems are used in various industries, such as construction, manufacturing, and oil and gas.
To assess a PTW system, you can use the following checklist:
Policy
- Is there a clear policy for risk assessment of high-hazard operational and maintenance activities and their control procedures?
- Are the objectives of the permit system clearly defined and understood?
- Is the permit system flexible enough to be applied to other potentially hazardous work apart from that which may have been specifically identified when the system was established?
Organizing Control
- Are responsibilities for the following made clear: management of the permit-to-work system, permit form design and system scope, type of jobs subject to permit and Control of contractors?
- Are the types of work or areas where permits must be used clearly defined and understood by all concerned?
- Is it clearly laid down who may issue permits?
- Is it clearly laid down how permits should be obtained for specific jobs?
- Are people prevented from issuing permits to themselves?
- Is the permit system recognized throughout the site or installation as essential for certain types of work?
- Are copies of permits issued for the same equipment/area kept and displayed together?
- Can all work activities be coordinated to ensure potential interactions are identified?
- Is there a provision on the permit form to cross-reference other relevant certificates and permits?
- Is there a means to ensure other people affected by the proposed work agree before the work (or preparations for it) is started?
- Where there are isolations common to more than one permit, is there a procedure to prevent the isolation from being removed before all the permits have been signed off?
- If an electronic system is in place, is a valid means available to recover the coordination of work activities if the electronic system fails?
Communication
- Does the system provide both for the recipient to retain the permit and for a record of live permits and suspended permits to be maintained at the point of issue?
- Does the system require a copy of the permit to be displayed at the workplace?
- Do permits clearly specify the job to be done?
- Do permits clearly specify to whom they are issued?
- Do permits specify the plant or geographical area to which work must be limited?
- Does the recipient have to sign the permit to show that they have both read and understood the permit’s hazards and control measures detailed in it?
- Do permits clearly specify a time limit for expiry or renewal?
- Does the permit include a handover mechanism for work that extends beyond a shift or other work period, including work that has been suspended?
- Is a hand-back signature required when the job is complete?
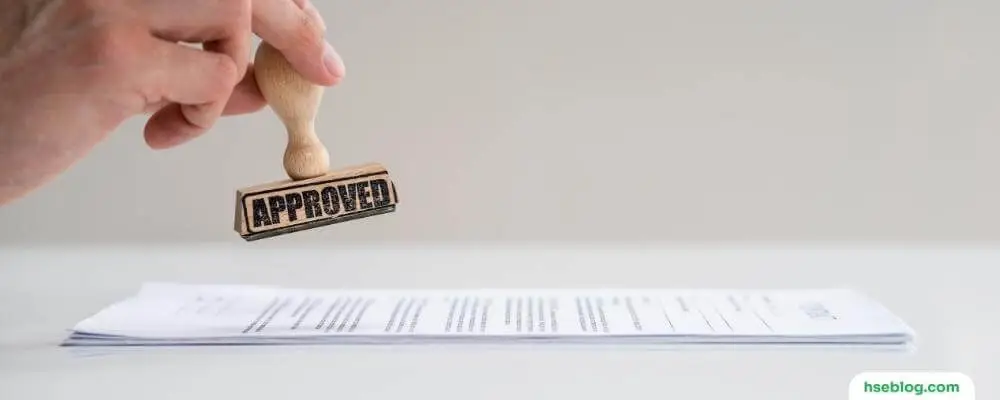
Training and Competence
- Is the permit system thoroughly covered during site or installation safety induction training?
- Are personnel with special responsibilities under the permit system, e.g., issuing and isolating authorities, properly authorized and trained?
- Do these people have sufficient time to carry out their duties properly?
- Does the permit system require a formal assessment of personnel competence before they are given responsibilities under the permit procedure?
- Is a record of training and competence maintained?
- Do training and competence requirements include contractors with responsibilities under the permit-to-work system?
- Are individuals provided with written confirmation of completion of relevant training, and are these documents checked before appointments are made within the permit-to-work system?
- Do authorized issuers have sufficient knowledge about the hazards associated with the relevant plant?
Planning and Implementation
- Does the permit clearly specify the job to be undertaken?
- Are there properly documented isolation procedures for use when working on potentially hazardous plant items, and do they provide for long-term isolation?
- Is there a clear requirement for work being done under a permit to be stopped if site conditions change or any new hazards have arisen?
- Does the permit contain clear rules about how the job should be controlled or abandoned in an emergency?
- Does the permit system require any potential hazards at the work site to be clearly identified and recorded on the permit?
- Does the permit clearly specify the precautions to be taken by permit users and other responsible people?
- Is there a procedure to identify and monitor tasks that require inhibiting safety devices, e.g., fire and gas detectors, to ensure that contingency plans and precautions are in place?
Measuring Performance
- Is there a monitoring procedure or scheduled spot checks to ensure permits are followed?
- Are records of all permits issued, their status, and any associated incidents or near misses?
- Are statistics on permit compliance and safety incidents analyzed regularly to identify trends or areas for improvement?
- Are there key performance indicators (KPIs) in place to measure the effectiveness of the permit-to-work system, such as the number of permits issued, the time taken to issue a permit, and the percentage of completed permits returned?
- Is feedback sought from workers who have used the permit system to identify any issues or areas for improvement?
- Are there regular reviews of the permit system’s performance, and are actions taken to address any identified shortcomings or non-conformances?
Audit and review
- Is there a procedure for reporting incidents arising during work carried out under a permit?
- Is the permit-to-work system audited as appropriate, preferably by people not normally employed at the site or offshore installation?
- Is there a procedure for reviewing the permit system at defined intervals?
Conclusion
In conclusion, a permit-to-work system ensures employees’ safety in industries with potentially hazardous work. The checklist provided in this blog post serves as a guide to assess the effectiveness and safety of a permit-to-work system. Companies can ensure their permit-to-work system is thorough, efficient, and continually improving by addressing policy, organizing control, communication, training and competence, planning and implementation, measuring performance, and auditing and reviewing. Implementing and maintaining an effective permit-to-work system can help prevent accidents, injuries, and potential fatalities in the workplace.