In today’s dynamic industrial environment, ensuring the health and safety of workers is paramount. One of the key aspects of occupational safety involves the management of substances that could be hazardous to health. This is where COSHH, or the Control of Substances Hazardous to Health, comes into play.
COSHH is a regulatory framework in the UK that aims to protect people in the workplace against health risks from hazardous substances. These substances, such as chemicals, fumes, dust, vapours, mists, gases, biological agents, or even asphyxiating gases, could be present in various forms. They may be inherently part of the work process, accidentally produced, or simply exist in the workplace environment.
The range of industries where hazardous substances might be encountered is vast, from healthcare to manufacturing, construction, agriculture, and beyond. Exposure to these hazardous substances can cause various health effects, from mild eye irritation and skin rashes to severe conditions like lung cancer or asthma. In some severe cases, exposure can even be fatal.
Understanding and managing these potential hazards is a moral and ethical obligation for employers and a legal requirement under the COSHH Regulations 2002. This is where COSHH Risk Assessment comes into the picture.
What is COSHH Risk Assessment?
COSHH Risk Assessment is a systematic process designed to identify hazards, assess the associated risks, and determine suitable control measures to mitigate these risks. It forms a crucial part of any health and safety strategy within an organization, helping to protect employees and others who may be exposed to hazardous substances.
The benefits of conducting COSHH Risk Assessments are manifold. It helps prevent work-related illness and injury, reduces absences and sick leave, increases staff morale, and enhances productivity. Moreover, it aids in ensuring that the organization complies with the law and avoids hefty fines and potential reputational damage.
In the upcoming sections, we will delve deeper into the details of COSHH, its legal obligations, the process of conducting a COSHH Risk Assessment, and much more. The ultimate aim is to give you the knowledge and understanding to ensure a safe and healthy workplace environment.

Understanding COSHH
To effectively manage the risks associated with hazardous substances, it is essential to understand the nature of these substances and how they can impact health. This section will discuss the types of substances considered hazardous to health, provide examples of common hazardous substances in different industries, and highlight the implications of exposure to these substances.
Types of Hazardous Substances
Hazardous substances can be categorized based on their physical and chemical properties or the health effects they may cause. Some common types of hazardous substances include:
- Chemicals: These are substances with a specific chemical composition, and they can exist in solid, liquid, or gaseous forms. Examples include solvents, cleaning agents, and adhesives.
- Fumes are tiny solid particles released into the air during high-temperature processes, such as welding or smelting.
- Dust: Dust comprises fine particles of solid materials generated by cutting, grinding, or sanding. Wood dust, silica dust, and flour dust are some examples.
- Vapours: Vapors are gaseous forms of substances that are normally liquid or solid at room temperatures, such as solvents, fuels, or specific chemical reactions.
- Mists: Mists are tiny liquid droplets suspended in the air, often produced during processes like spraying, cutting, or grinding.
- Gases: Gases are substances that exist in the gaseous state at room temperature, like carbon dioxide, oxygen, or natural gas.
- Biological agents: These are microorganisms that can cause harm to human health, including bacteria, viruses, and fungi.
- Asphyxiating gases: These are gases that can displace oxygen in the atmosphere, leading to a life-threatening lack of oxygen, such as nitrogen or carbon dioxide.
Examples of Common Hazardous Substances in Different Industries
Different industries will typically encounter various hazardous substances. Some examples include:
- Manufacturing: Solvents, adhesives, paints, oils, and heavy metals
- Construction: Asbestos, silica dust, cement dust, and welding fumes
- Healthcare: Disinfectants, drugs, anaesthetic gases, and infectious agents
- Agriculture: Pesticides, herbicides, fertilizers, and diesel exhaust
- Food industry: Cleaning agents, flour dust, and refrigerant gases
- Laboratories: Chemicals, solvents, and compressed gases
Implications of Exposure to Hazardous Substances
Exposure to hazardous substances can lead to a range of health effects, depending on the nature of the substance and the extent and duration of exposure. Some of the potential health implications include:
- Acute effects: These are immediate or short-term health effects resulting from exposure, such as skin irritation, eye irritation, headaches, dizziness, or nausea.
- Chronic effects: These are long-term health effects that may develop after prolonged or repeated exposure to hazardous substances, such as respiratory diseases, skin conditions, organ damage, or cancer.
- Allergic reactions: Some individuals may develop allergies to specific substances, resulting in symptoms like skin rashes, respiratory irritation, or even anaphylactic shock.
- Asphyxiation: Exposure to asphyxiating gases can lead to oxygen deprivation, causing unconsciousness and, in extreme cases, death.
Understanding the potential health implications of hazardous substances in the workplace is crucial to develop effective strategies to manage and mitigate the associated risks. The next step is to identify these substances and evaluate their risks, which we will discuss in detail in the following sections.
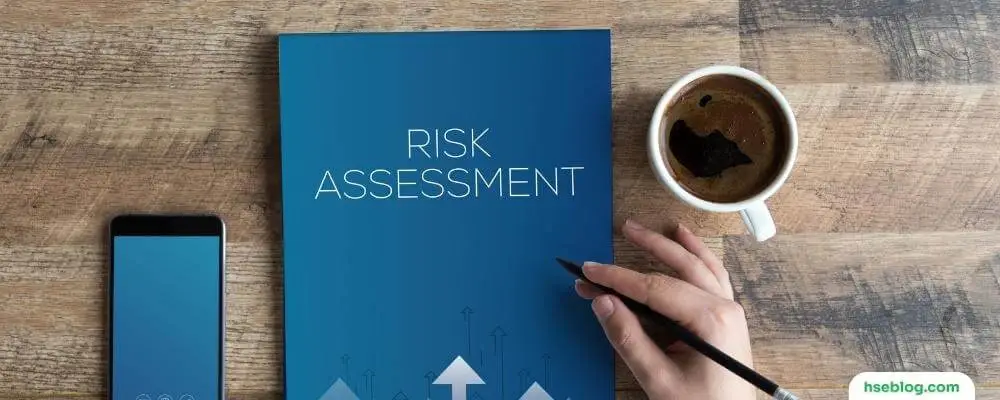
Legal Requirements and COSHH Regulations
To ensure the health and safety of workers, there are legal requirements in place that govern the management of hazardous substances in the workplace. In this section, we will provide an overview of the employer’s legal implications and responsibility, discuss the COSHH regulations in detail, and highlight the penalties for non-compliance.
Responsibility of the Employer
Under the UK’s Health and Safety at Work Act 1974, employers have a legal duty to protect the health, safety, and welfare of their employees and others who may be affected by their work activities. This duty extends to the management of hazardous substances in the workplace. Employers are responsible for the following:
- Identifying hazardous substances present in their workplace.
- Assessing the risks associated with these substances.
- Implementing control measures to prevent or minimize exposure.
- Providing information, instruction, and training to employees.
- Monitoring and reviewing the effectiveness of control measures.
- Keeping records of risk assessments and control measures.
COSHH Regulations
The Control of Substances Hazardous to Health (COSHH) Regulations 2002 specifically focuses on controlling hazardous substances in the workplace. The key requirements of these regulations include:
- Risk Assessment: Employers must conduct a COSHH risk assessment to identify and evaluate the risks associated with hazardous substances. This assessment should consider factors such as the nature of the substance, the level and duration of exposure, and the potential health effects.
- Control Measures: Based on the risk assessment findings, employers must implement appropriate control measures to eliminate or reduce exposure to hazardous substances. These measures may include engineering controls (e.g., ventilation systems), administrative controls (e.g., safe work practices), and the use of personal protective equipment (PPE).
- Monitoring and Health Surveillance: Employers should establish monitoring procedures to ensure that control measures are effective and regularly reviewed. In some cases, health surveillance may be necessary to monitor employees’ health exposed to certain hazardous substances.
- Information and Training: Employers must provide employees with information and training on the hazards associated with hazardous substances, the control measures in place, and the proper use of PPE. Employees should know the risks, understand the control measures, and know how to protect themselves.
- Safety Data Sheets (SDS): Employers must obtain and keep up-to-date Safety Data Sheets for hazardous substances used in the workplace. These sheets provide detailed information about the substances’ properties, hazards, and safe handling.
Penalties for Non-Compliance
Non-compliance with COSHH regulations can have serious consequences. Penalties for failing to meet the legal requirements can include fines, imprisonment, or both. The severity of the penalties depends on the nature and extent of the breach, as well as any harm caused or potential harm that could have resulted from the non-compliance.
Employers must understand and adhere to COSHH regulations to fulfil their legal obligations and ensure the health and safety of their employees. Compliance not only avoids legal repercussions but also creates a safer work environment and promotes the well-being of workers.
The Need for COSHH Risk Assessment
COSHH risk assessment is a fundamental process in managing the risks associated with hazardous substances in the workplace. This section will explain why COSHH risk assessment is necessary, discuss its role in health and safety management, and highlight the benefits of conducting regular COSHH risk assessments.
Why is COSHH Risk Assessment Necessary?
COSHH risk assessment is necessary for several reasons:
- Identification of Hazards: It helps identify and recognize the hazardous substances present in the workplace, allowing employers to understand the potential risks associated with them.
- Evaluation of Risks: Employers can determine the likelihood and severity of harm from exposure to hazardous substances by assessing the risks. This enables the prioritization of control measures and resources.
- Prevention and Control: COSHH risk assessment is crucial in preventing and controlling exposure to hazardous substances. It helps select and implement effective control measures to minimize the risks to an acceptable level.
- Legal Compliance: Conducting COSHH risk assessments is a legal requirement under the COSHH regulations. Compliance with the regulations ensures that employers fulfil their legal obligations and avoid penalties for non-compliance.
Role of COSHH Risk Assessment in Health and Safety Management
COSHH risk assessment is integral to an effective health and safety management system. It serves several important roles:
- Proactive Hazard Management: COSHH risk assessment allows employers to proactively identify and manage hazards associated with hazardous substances. Taking appropriate control measures helps prevent work-related illnesses, injuries, and accidents.
- Decision-Making: By systematically evaluating risks, COSHH risk assessment supports informed decision-making. It assists employers in determining the most suitable control measures and allocating resources effectively.
- Continuous Improvement: COSHH risk assessments are not one-time activities. They encourage a culture of continuous improvement by regularly reviewing and updating control measures based on new information, technological advancements, or changes in work processes.
- Communication and Collaboration: COSHH risk assessments facilitate effective communication and collaboration between employers, employees, and relevant stakeholders. They ensure everyone understands the risks, control measures, and their respective roles in maintaining a safe and healthy work environment.
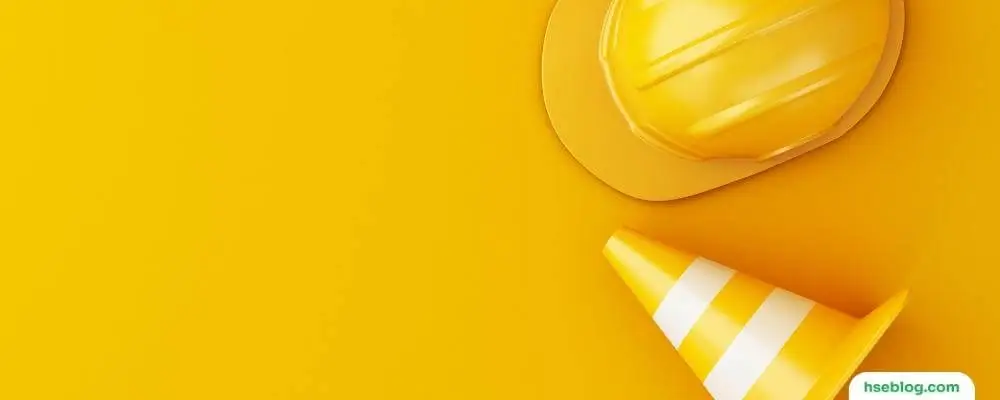
Benefits of Conducting Regular COSHH Risk Assessments
Regular COSHH risk assessments provide numerous benefits, including:
- Risk Reduction: COSHH risk assessments help reduce the risks associated with hazardous substances by identifying and controlling hazards. This leads to a safer work environment and protects the health and well-being of employees.
- Legal Compliance: Conducting regular COSHH risk assessments ensures compliance with legal obligations under the COSHH regulations. This helps avoid penalties, legal actions, and reputational damage associated with non-compliance.
- Improved Productivity: Effective management of hazardous substances enhances productivity by minimizing work-related illnesses and absences. Employees feel safer and more motivated when working in an environment where their health is prioritized.
- Cost Savings: Proactive risk management through COSHH risk assessments can result in cost savings in the long run. Employers can reduce healthcare costs, compensation claims, and potential legal expenses by preventing accidents, injuries, and illnesses.
- Enhanced Reputation: Demonstrating a commitment to the health and safety of employees through regular COSHH risk assessments enhances the organization’s reputation. It fosters trust among employees, clients, and stakeholders, contributing to long-term success.
In summary, COSHH risk assessment is necessary for identifying hazards, evaluating risks, and implementing control measures to manage the risks associated with hazardous substances. It plays a crucial role in health and safety management by preventing harm, ensuring legal compliance, and promoting a culture of continuous improvement.
The COSHH Risk Assessment Process
A COSHH risk assessment is a systematic approach to identifying and managing the risks associated with hazardous substances in the workplace. This section will provide a step-by-step guide to carrying out a COSHH risk assessment and discuss important considerations during the process.
Step-by-Step Guide to Carrying Out a COSHH Risk Assessment:
- Identifying Hazardous Substances
- Evaluating and Controlling Risks
- COSHH Risk Assessment Documentation
1. Identifying Hazardous Substances
Identifying potentially hazardous substances is crucial in the COSHH risk assessment process. This section will discuss how to identify hazardous substances in your workplace, use of Safety Data Sheets (SDS) for identification, and classify and label hazardous substances.
How to Identify Potentially Hazardous Substances in Your Workplace:
- Review Inventory and Material Safety Data Sheets (MSDS): Examine the inventory of substances used in the workplace and review the associated MSDS or SDS, which provides information on the hazardous properties, handling, and storage requirements of the substances.
- Conduct Workplace Inspections: Inspect the workplace to identify substances present, such as chemicals, solvents, gases, or dust. Look for warning signs, labels, or colour-coding indicating the presence of hazardous substances.
- Consult with Suppliers and Manufacturers: Reach out to suppliers or manufacturers of the substances used in the workplace to obtain information about their hazardous properties and associated risks.
Using Safety Data Sheets (SDS) for Identification:
SDS, formerly known as Material Safety Data Sheets (MSDS), are essential sources of information for identifying hazardous substances in the workplace. When reviewing SDS, pay attention to the following information:
- Hazard Identification: SDS details the specific hazards associated with the substance, including its classification, toxicity, flammability, and reactivity.
- Composition and Ingredients: The SDS lists the chemical composition and ingredients of the substance, allowing you to determine its potential hazards.
- Handling and Storage: SDS provides guidelines on safe handling, storage, and disposal of the substance, including information on necessary precautions and protective measures.
- First Aid Measures: The SDS outlines recommended first aid measures in case of substance exposure or accidents.
- Exposure Controls and Personal Protection: SDS provides information on recommended exposure limits, engineering controls, and personal protective equipment (PPE) required for working with the substance.
Classification and Labelling of Hazardous Substances:
Hazardous substances are typically classified and labelled based on internationally recognized systems, such as the Globally Harmonized System (GHS). The GHS uses standardized symbols, pictograms, and hazard statements to indicate the nature of the hazards associated with a substance. Pay attention to container labels and markings to identify hazardous substances and understand their risks.
It is crucial to have a comprehensive understanding of the hazardous substances present in the workplace to effectively assess the associated risks and implement appropriate control measures. The identification process should consider information from SDS, workplace inspections, and consultations with suppliers or manufacturers.
2. Evaluating and Controlling Risks
Once hazardous substances are identified, it is necessary to evaluate their risks and implement control measures to mitigate them. This section will evaluate the risks associated with identified hazardous substances and different control methods.
How to Evaluate the Risks Associated with Hazardous Substances:
- Exposure Assessment: Assess the level and duration of exposure to hazardous substances. Consider factors such as the concentration of the substance, frequency and duration of exposure, and the route of exposure (e.g., inhalation, skin contact).
- Health Effects Assessment: Evaluate the potential health effects of exposure to hazardous substances. Review available data, such as toxicity information, exposure limits, and occupational exposure standards.
- Risk Determination: Combine the exposure and health effects assessments to determine the risk level associated with each hazardous substance. Assess whether the risks are acceptable or if further control measures are necessary.
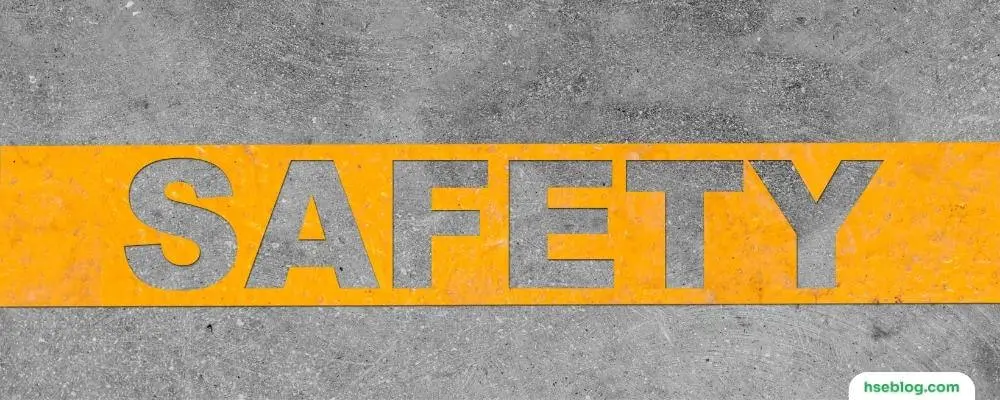
Methods of Controlling the Risks:
There are various methods of controlling the risks associated with hazardous substances:
- Elimination: Where possible, eliminate hazardous substances by finding safer alternatives or modifying work processes to remove the need for the substances.
- Substitution: Replace hazardous substances with less hazardous alternatives. Consider using less toxic chemicals, adopting alternative technologies, or implementing process changes.
- Engineering Controls: Implement engineering controls to minimize exposure. This may include improving ventilation systems, enclosing or isolating the process, or implementing automated systems.
- Administrative Controls: Establish safe work practices and procedures, such as proper handling and storage protocols, regular maintenance, and training programs. Ensure employees know the risks, understand the control measures, and follow established procedures.
- Personal Protective Equipment (PPE): As a last resort, provide appropriate personal protective equipment, such as gloves, respiratory protection, or protective clothing, to individuals who may be exposed to hazardous substances. PPE should be used with other control measures and selected based on the specific hazards and exposure levels.
The selection of control measures should be based on the hierarchy of controls, prioritizing elimination or substitution whenever possible. However, in some cases, a combination of control measures may be necessary to adequately mitigate the risks associated with hazardous substances.
Regular monitoring and review of the effectiveness of the implemented control measures are essential to ensure their ongoing efficiency. This includes periodic inspections, air monitoring, and employee feedback to identify deficiencies or improvement areas.
3. COSHH Risk Assessment Documentation
Accurate documentation of the COSHH risk assessment process is crucial for demonstrating compliance with legal requirements, tracking the effectiveness of control measures, and facilitating ongoing review and improvement. This section will discuss the importance of keeping records, what to include in the COSHH Risk Assessment documentation and the need for regular review and updates.
The Importance of Keeping Records:
Keeping records of the COSHH risk assessment process is essential for several reasons:
- Legal Compliance: Maintaining accurate and up-to-date records ensures compliance with legal obligations under the COSHH regulations. These records indicate due diligence in managing hazardous substances and can be requested during inspections or audits.
- Tracking Control Measures: Records allow employers to track the implementation and effectiveness of control measures over time. This includes information on selecting and implementing control measures, maintenance activities, and employee training.
- Communication and Collaboration: Well-documented COSHH risk assessments facilitate effective communication and collaboration within the workplace. Records provide a reference point for sharing information with employees, contractors, or regulatory authorities, ensuring everyone knows the identified hazards and control measures in place.
What to Include in the COSHH Risk Assessment Documentation:
The COSHH risk assessment documentation should include the following information:
- Details of the Hazardous Substances: Clearly identify the hazardous substances, including their names, chemical compositions, associated hazards, and relevant reference numbers or codes.
- Risk Assessment Findings: Document the findings of the risk assessment, including the identified hazards, evaluation of risks, and conclusions regarding the level of risk associated with each substance.
- Control Measures: Describe the control measures implemented to mitigate the risks associated with hazardous substances. This should include details of engineering controls, administrative controls, and the use of personal protective equipment (PPE).
- Monitoring and Review: Document any monitoring activities conducted, such as air sampling results or inspections. Include records of reviews and updates to the risk assessment, indicating any changes to control measures or procedures.
- Training and Awareness: Record details of the training provided to employees regarding COSHH and the risks associated with hazardous substances. This includes records of training sessions, attendance, and any feedback or questions raised.
Reviewing and Updating the Assessment:
COSHH risk assessments should not be static documents. Regular review and updates are necessary to ensure control measures remain effective and relevant. Factors triggering a review include substance changes, work processes, equipment, or regulations. Reviews should also be conducted if there are incidents or near-misses related to hazardous substances or new findings from scientific research or industry best practices.
By regularly reviewing and updating the COSHH risk assessment, employers can ensure that control measures remain adequate, employees are protected, and compliance with legal requirements is maintained.
Training and Awareness
Proper training of staff on COSHH and the risk assessment process is essential to ensure a safe and healthy workplace. This section will discuss the importance of training employees and strategies for raising awareness about COSHH in the workplace.
The Importance of Training Staff on COSHH and the Risk Assessment Process:
- Knowledge and Understanding: Training employees on COSHH and the risk assessment process gives them the knowledge and understanding to recognize hazards, follow safe work practices, and use control measures effectively.
- Risk Awareness: By educating employees about the risks associated with hazardous substances, they become more aware of the potential hazards in their work environment. This awareness helps foster a proactive safety culture and empowers employees to take necessary precautions to protect themselves and others.
- Correct Use of Control Measures: Proper training ensures employees understand how to use and maintain control measures, such as personal protective equipment (PPE) or engineering controls. This reduces the likelihood of accidents or incidents due to incorrect or ineffective use of control measures.
- Compliance with Procedures: Training helps employees understand and comply with established procedures for handling hazardous substances, thereby minimizing the risk of exposure and ensuring consistent adherence to safety protocols.
- Empowerment and Confidence: Training instils confidence in employees, knowing they have the knowledge and skills to safely handle hazardous substances. This empowers them to actively participate in maintaining a safe working environment and contributes to overall job satisfaction.
How to Raise Awareness about COSHH in Your Workplace:
- Training Programs: Develop comprehensive training programs that cover COSHH regulations, risk assessment methodologies, and specific control measures relevant to your workplace. Provide regular training sessions for new employees and refresher courses for existing staff.
- Information Sharing: Regularly communicate information about hazardous substances, risk assessment findings, and control measures to all employees. Use multiple channels, such as notice boards, newsletters, or email updates, to ensure widespread dissemination of relevant information.
- Safety Meetings and Toolbox Talks: Organize safety meetings or toolbox talks dedicated to discussing COSHH and related topics. Encourage open dialogue, address questions or concerns, and promote a culture of active participation in maintaining a safe work environment.
- Signage and Labels: Use clear and prominent signage and labels to identify hazardous substances, designated areas, and the required control measures. Ensure that labels are accurate, easy to understand, and comply with relevant regulations.
- Employee Engagement: Involve employees in risk assessment and control measures decision-making. Encourage them to actively contribute their knowledge, observations, and suggestions for improvement. This involvement increases ownership and commitment to workplace safety.
- Continuous Education: Stay updated with the latest developments in COSHH regulations, best practices, and emerging hazards. Share this knowledge with employees through regular training updates or informational sessions.
By prioritizing training and raising awareness about COSHH, organizations can create a safety-conscious work culture where employees are equipped with the knowledge and skills to identify, assess, and manage the risks associated with hazardous substances.
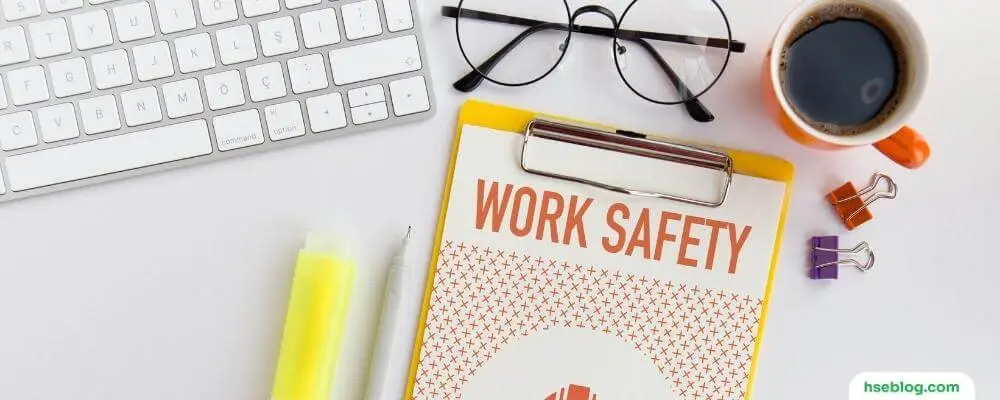
Case Studies
Real-life case studies provide valuable insights into the importance of COSHH risk assessment and how it could have prevented incidents involving hazardous substances. This section will present a few examples of such incidents and discuss how proper COSHH risk assessment could have mitigated or prevented them.
Case Study 1: Chemical Exposure in a Manufacturing Plant
In a manufacturing plant, workers were exposed to a hazardous chemical during a mixing process due to inadequate ventilation and improper use of personal protective equipment (PPE). Several workers experienced symptoms of chemical poisoning, including respiratory distress and skin irritation.
How proper COSHH risk assessment could have prevented the incident:
- Identification of Hazard: A thorough COSHH risk assessment would have identified the hazardous nature of the chemical, highlighting the need for appropriate control measures.
- Evaluation of Risks: The risk assessment would have evaluated the risks associated with the chemical exposure, considering factors such as concentration, duration of exposure, and potential health effects.
- Control Measures: Based on the risk assessment findings, appropriate control measures could have been implemented. This could include ensuring adequate ventilation systems, providing proper PPE, and implementing safe work practices.
- Training and Awareness: Proper training on the risks associated with the chemical and the correct use of control measures would have educated workers on protecting themselves.
By conducting a comprehensive COSHH risk assessment, the manufacturing plant could have identified the risks associated with the hazardous chemical and implemented control measures to prevent the incident and protect the health and safety of the workers.
Case Study 2: Dust Explosion in a Woodworking Facility
In a woodworking facility, a dust explosion occurred, causing significant damage to the facility and injuring several workers. The explosion resulted from the accumulation of combustible wood dust in the workshop, combined with a spark from a piece of machinery.
How proper COSHH risk assessment could have prevented the incident:
- Identification of Hazard: A COSHH risk assessment would have recognized the potential hazards of wood dust, particularly its combustibility.
- Evaluation of Risks: The risk assessment would have assessed the risks of dust explosion, considering factors such as dust accumulation, ignition sources, and ventilation systems.
- Control Measures: The risk assessment would have led to the implementation of control measures to mitigate the risk of dust explosion, such as implementing dust collection systems, regular cleaning procedures, and proper maintenance of equipment to eliminate potential ignition sources.
- Training and Awareness: Proper training on the hazards of wood dust and the importance of maintaining a clean and safe work environment would have raised awareness among workers, promoting proactive measures to prevent dust accumulations and potential explosions.
By conducting a COSHH risk assessment focused on the hazards of wood dust and implementing appropriate control measures, the woodworking facility could have minimized the risk of a dust explosion and ensured the safety of workers and the facility.
These case studies illustrate how proper COSHH risk assessment is crucial in identifying hazards, evaluating risks, and implementing control measures to prevent hazardous substance incidents. Conducting comprehensive assessments and taking proactive measures based on the assessment findings can significantly reduce the likelihood of accidents, injuries, and long-term health effects associated with hazardous substances.