In today’s world, chemicals play a vital role in various industries, from pharmaceuticals and agriculture to manufacturing and research. While these chemicals are essential for progress and innovation, they pose significant risks if they are improperly handled, stored, and disposed of. Chemical safety is crucial in ensuring the well-being of employees, preventing accidents and damage to the environment, and maintaining compliance with regulations.
This blog will discuss the different types of emergency and safety equipment necessary for maintaining a safe and compliant work environment when dealing with hazardous chemicals. We will explore personal protective equipment, safe storage solutions, fire safety equipment, ventilation, and air filtration systems, first aid and emergency response equipment, and the importance of training and education in chemical safety. By understanding and implementing these essential safety measures, organizations can minimize the risk of accidents and create a secure environment for everyone involved.
Importance Of Emergency & Safety Equipment For Chemical Safety
Emergency and safety equipment is paramount for chemical safety in the workplace. Handling, storing, and disposing of hazardous chemicals present numerous risks, including accidents, injuries, fires, explosions, and environmental hazards. By investing in the appropriate emergency and safety equipment, organizations can greatly minimize these risks and create a safer work environment for their employees. Here are some key reasons why emergency and safety equipment is essential for chemical safety:
- Protection of employees: Personal Protective Equipment (PPE) shields workers from exposure to hazardous chemicals, reducing the risk of injury or harm. Proper PPE, such as safety goggles, gloves, protective clothing, and respiratory protection, ensures workers can perform their tasks safely and effectively.
- Prevention of accidents and fires: Proper chemical storage, fire safety equipment, and spill containment materials help to prevent accidents, fires, and explosions that can result from improper handling or storage of hazardous chemicals. This protects employees and safeguards the organization’s assets and reputation.
- Compliance with regulations: Adhering to local and international regulations for chemical safety is crucial for organizations to avoid fines, penalties, and legal liabilities. Implementing appropriate emergency and safety equipment helps businesses maintain compliance with these regulations and demonstrate their commitment to employee safety and environmental protection.
- Improved air quality and ventilation: Proper ventilation and air filtration systems help control the concentration of airborne contaminants, reducing the risk of fire or explosion and preventing the accumulation of toxic fumes. This contributes to a healthier work environment and reduces employees’ risk of long-term health complications.
- Enhanced emergency response: Equipping workplaces with first aid and emergency response equipment, such as eyewash stations, emergency showers, and chemical neutralizers, can significantly minimize the impact of accidents involving hazardous chemicals. Prompt action can reduce the severity of injuries and prevent further harm.
- Fostering a safety culture: Investing in emergency and safety equipment and comprehensive training and education programs helps create a workplace culture. This, in turn, contributes to increased employee morale, reduced absenteeism, and improved overall productivity.
The importance of emergency and safety equipment for chemical safety cannot be overstated. Organizations can protect their employees, assets, and reputation by prioritizing safety measures and investing in the necessary equipment while maintaining regulatory compliance and promoting a safer work environment.
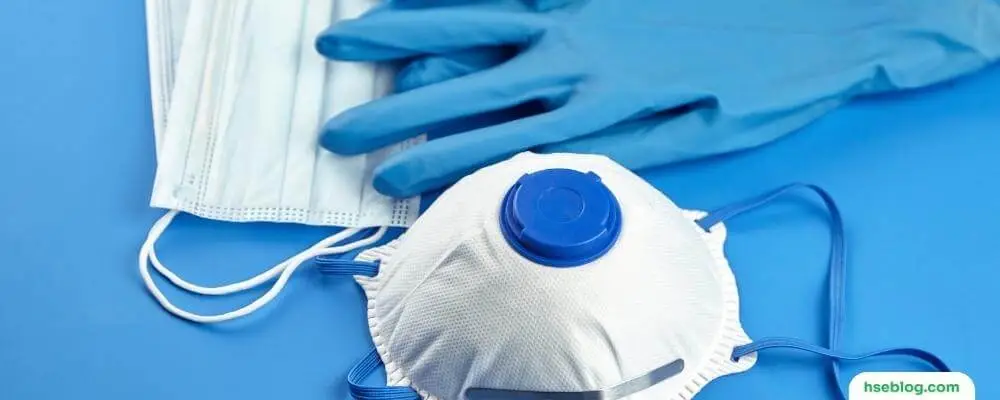
Emergency & Safety Equipment For Chemical Safety
Chemical safety is paramount in any industry or setting where chemicals are used or present. Emergency and safety equipment should be readily available to handle any accidents or spills that may occur. Here are some of the essential emergency and safety equipment for chemical safety:
1. Personal Protective Equipment (PPE)
Personal Protective Equipment (PPE) is essential in maintaining the safety of workers when handling, storing, or disposing of hazardous chemicals. PPE is designed to minimize exposure to hazardous substances, reducing the risk of injury or harm. To select the appropriate PPE for the task, it is crucial to understand the nature of the chemicals, especially different types of chemicals, and the potential hazards involved. Here is a more detailed explanation of the different types of PPE used for chemical safety:
Safety goggles and face shields
Eye and face protection is vital when working with chemicals that can cause splashes, fumes, or airborne particles. Safety goggles protect the eyes from chemical splashes and dust, while face shields offer more extensive coverage, shielding the entire face from potential hazards.
Gloves
Various types of gloves are available for different chemical exposures. Chemical-resistant gloves are designed to resist specific chemicals’ permeation, degradation, and penetration. Cut-resistant gloves are essential when handling sharp objects or materials. Always refer to the chemical compatibility chart to choose the appropriate glove material for the chemicals used.
Protective clothing
Protective clothing includes aprons, coveralls, and lab coats, designed to shield the wearer from chemical splashes, spills, and particulates. Depending on the application, they are often made from materials resistant to specific chemicals and may be disposable or reusable.
Respiratory protection
Chemical fumes, vapors, or dust exposure can lead to respiratory issues or other health complications. Respiratory protection, such as face masks and respirators, helps to filter out hazardous substances in the air, ensuring workers breathe clean air. The selection of the correct type of respirator depends on the nature and concentration of the contaminants.
Foot protection
Chemical-resistant boots and shoe covers provide additional protection from spills, splashes, and slips in areas where hazardous chemicals are used. They can prevent injuries and ensure a safer working environment.
Ear protection
In some cases, chemical exposure can also involve loud noises, such as in manufacturing facilities. Earplugs or earmuffs can protect workers’ hearing in these situations.
Proper use, maintenance, and disposal of PPE are essential in ensuring its effectiveness in protecting workers from chemical hazards. Training on the appropriate PPE selection, use, and limitations should be provided to all employees handling hazardous chemicals.
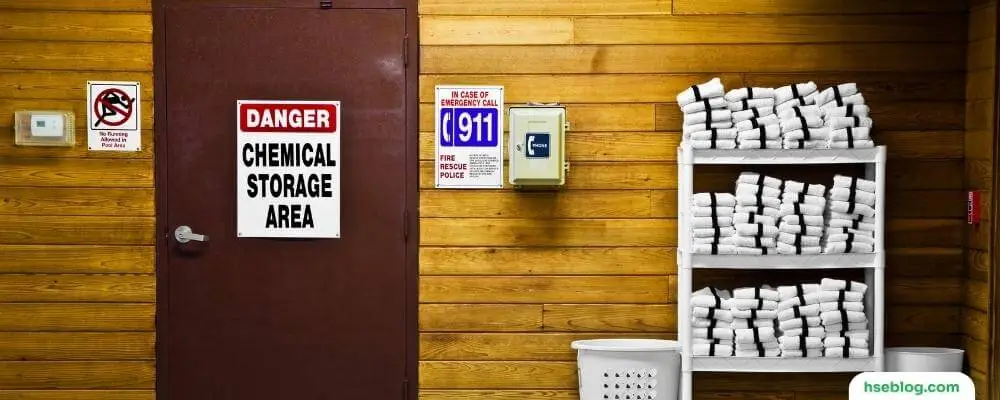
2. Safety Storage Equipment
Proper storage of chemicals is crucial in preventing accidents, fires, and environmental hazards. Safety storage equipment is designed to contain hazardous materials and minimize the risks of improper handling and storage. The following are key types of safety storage equipment used for chemical safety:
Chemical storage cabinets
These cabinets are designed to store and organize various types of chemicals, such as flammable liquids, corrosives, and toxic substances. Depending on the chemicals being stored, they come in different materials, such as metal or polyethylene. These cabinets often have features like self-closing doors, leak-proof sumps, and ventilation to minimize the risks associated with chemical storage.
Gas cylinder storage
Gas cylinders, including leaks, fires, and explosions, can pose significant hazards if not stored properly. Gas cylinder storage solutions include specially designed cabinets, racks, and cages that securely hold cylinders upright, prevent unauthorized access, and ensure proper ventilation.
Safety cans and containers
Safety cans and containers are designed to safely store and dispense flammable, corrosive, or other hazardous liquids. They are made from materials resistant to the stored chemicals and come with features like self-closing lids, flame arresters, and pressure relief mechanisms to minimize the risk of spills, leaks, or explosions.
Eyewash stations and emergency showers
In the event of chemical exposure or accidents, immediate access to eyewash stations and emergency showers is critical to minimize injury. These stations should be located near areas with potential chemical hazards and should be able to provide a continuous flow of water for at least 15 minutes. Regular inspection and maintenance of these stations are essential to ensure their proper functioning.
Spill containment and control materials
Chemical spills can lead to accidents, injuries, and environmental damage. Spill containment and control materials, such as absorbents, pads, and spill kits, are designed to quickly and effectively contain and clean up chemical spills. These materials should be readily available where hazardous chemicals are stored or used.
Proper selection, installation, and maintenance of safety storage equipment are crucial in preventing accidents and ensuring a safe working environment. It is essential to follow local regulations and guidelines when storing hazardous chemicals and regularly inspect and maintain the equipment to ensure its effectiveness. Additionally, training employees on the correct use and handling of these storage solutions can further enhance chemical safety in the workplace.
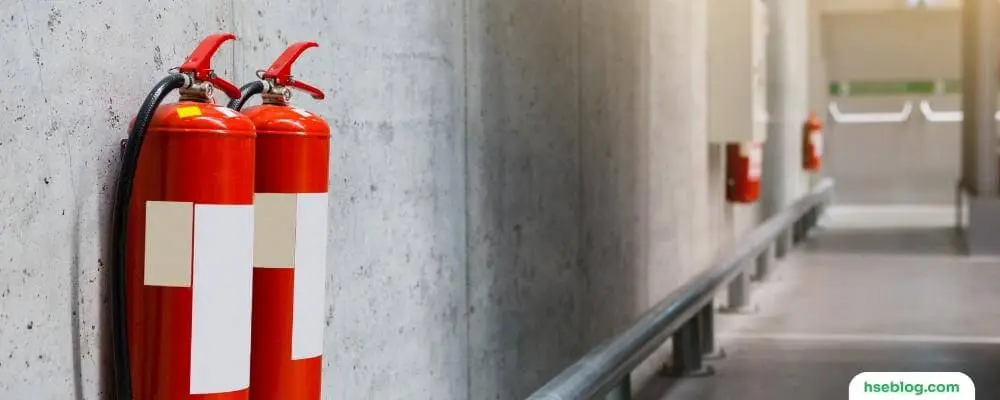
3. Fire Safety Equipment
Chemical fires can be particularly dangerous due to the potential for toxic fumes and the rapid spread of flames. Fire safety equipment is essential in preventing and controlling fires involving hazardous chemicals. Here are the different types of fire safety equipment that play a crucial role in chemical safety:
Fire extinguishers
Not all fire extinguishers are suitable for chemical fires, so it is important to choose the appropriate type based on the specific chemicals in use. For example, Class B extinguishers are designed for flammable liquids and gases, while Class C extinguishers are suitable for electrical fires. Specialized extinguishers may be necessary, such as Class D for combustible metal fires or Class K for kitchen fires. Properly placed and maintained fire extinguishers should be readily available in areas with potential chemical hazards.
Fire blankets
Fire blankets are made from fire-resistant materials and can smother small fires or wrap around a person whose clothes have caught fire. They can be particularly useful in laboratories or other areas where hazardous chemicals are used, as they can quickly extinguish small fires before they spread.
Fire alarms and detectors
Early detection of fires is crucial in minimizing damage and ensuring the safety of employees. Fire alarms and detectors, such as smoke and heat sensors, should be installed throughout the facility, especially where hazardous chemicals are stored or used. Regular testing and maintenance of these devices are essential to ensure they remain in proper working order.
Emergency exit signs and lighting
Clear and visible emergency exit signs and lighting are critical for guiding employees to safety in a fire or other emergency. These signs and lights should be installed along escape routes and near exit doors, and they should be regularly inspected and maintained to ensure their functionality during an emergency.
Proper selection, placement, and maintenance of fire safety equipment are essential in preventing and controlling fires involving hazardous chemicals. In addition to installing the appropriate equipment, regular training and drills should be conducted to ensure that employees know how to use fire safety equipment and follow emergency evacuation procedures. Establishing and enforcing fire safety guidelines and practices can greatly reduce the risk of fires and ensure a safer working environment when dealing with hazardous chemicals.
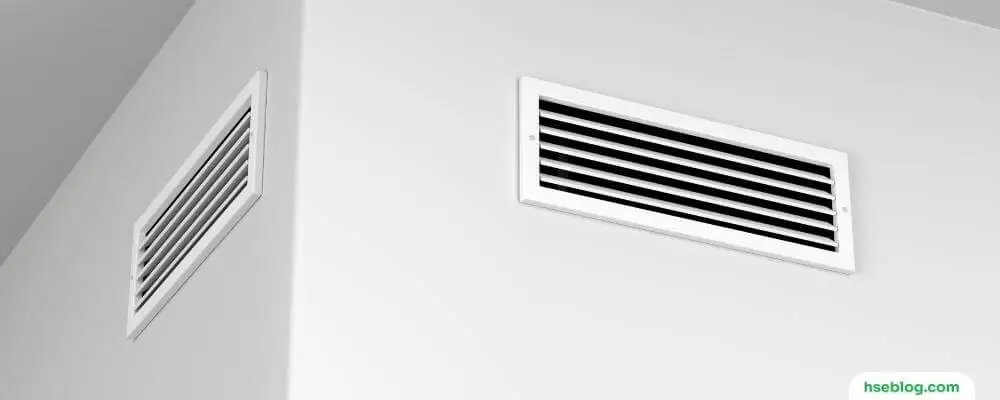
4. Ventilation and Air Filtration Systems
A well-designed ventilation and air filtration system is critical in maintaining a safe and healthy work environment when dealing with hazardous chemicals. Proper ventilation can help control the concentration of airborne contaminants, reduce the risk of fire or explosion, and prevent the accumulation of toxic fumes. The following are the key components of effective ventilation and air filtration systems for chemical safety:
Laboratory fume hoods
Fume hoods are essential in laboratories and other workspaces where hazardous chemicals are used. They are designed to capture and exhaust fumes, vapors, and particulates generated during chemical processes, preventing worker exposure. A well-functioning fume hood should provide adequate face velocity, sash height, and appropriate exhaust ducting. Regular inspection, maintenance, and testing of fume hoods are necessary to ensure their effectiveness.
Exhaust fans and ducts
Exhaust fans and ducts remove contaminated air from workspaces and replace it with fresh, clean air. These systems should be designed and installed according to industry standards and local regulations to ensure adequate air exchange and contaminant removal. Regular inspection and cleaning of exhaust fans and ducts are essential to maintain efficiency and prevent hazardous substances buildup.
Air purifiers and filters
In some situations, air purifiers and filters can supplement ventilation systems or provide additional air cleaning in areas where hazardous chemicals are used. These devices may use HEPA filters, activated carbon filters, or other technologies to remove particles and contaminants from the air. Regular maintenance and filter replacement is crucial to ensure their effectiveness.
Gas detection monitors
Gas detection monitors continuously monitor the air for hazardous gases or vapors. These devices can provide early warning of leaks or spills, allowing for prompt action to mitigate the risk of exposure or other hazards. Gas detection monitors should be installed in strategic locations, such as near chemical storage areas or where gas cylinders are used, and should be regularly calibrated and maintained.
Proper design, installation, and maintenance of ventilation and air filtration systems are essential for maintaining a safe working environment when handling hazardous chemicals. In addition to using the appropriate equipment, it is crucial to provide training for employees on the importance of ventilation and air filtration and how to recognize signs of inadequate ventilation or air quality issues. By prioritizing air quality and safety, organizations can reduce the risk of accidents and create a healthier work environment for their employees.
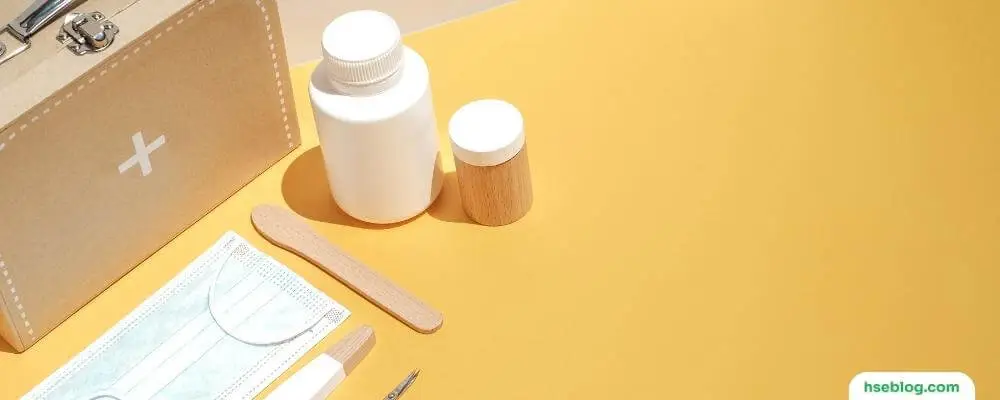
5. First Aid and Emergency Response Equipment
Having the right first aid and emergency response equipment on hand is essential for minimizing the impact of accidents involving hazardous chemicals. Quick action can significantly reduce the severity of injuries and prevent further harm. The following are key components of first aid and emergency response equipment for chemical safety:
First aid kits
First aid kits should be tailored to the specific chemical hazards present in the workplace. These kits should include essential items such as bandages, gauze, adhesive tape, burn dressings, and antiseptic wipes. In addition, kits should contain specialized supplies for treating chemical injuries, such as eyewash solutions, burn gel, and neutralizing agents for specific chemicals. First aid kits should be easily accessible, clearly marked, and regularly inspected to ensure their contents are up to date-and in good condition.
Emergency eyewash stations
Chemical exposure to the eyes can cause severe and permanent damage if not treated promptly. Emergency eyewash stations provide immediate access to a continuous water or eyewash solution flow, allowing for quick and effective eye flushing. These stations should be located near areas with potential chemical hazards and regularly inspected, maintained, and tested to ensure proper functionality.
Emergency showers
In the event of chemical spills or splashes on the skin, emergency showers can quickly flush away contaminants and minimize the risk of injury. These showers should be located near areas with potential chemical hazards and should be able to provide a continuous flow of water for at least 15 minutes. Regular inspection and maintenance of emergency showers are necessary to ensure proper functioning.
Chemical neutralizers and treatments
Some hazardous chemicals may require specialized neutralizers or treatments to mitigate their effects. For example, calcium gluconate gel can treat hydrofluoric acid burns, while sodium bicarbonate or other neutralizing agents can neutralize chemical spills. It is crucial to have the appropriate neutralizers and treatments readily available in areas where hazardous chemicals are used.
Communication devices
In an emergency, effective communication is vital for coordinating response efforts and ensuring the safety of all employees. Communication devices like phones, radios, or alarm systems should be readily available and functional to facilitate quick communication with emergency responders and other team members.
Proper selection, placement, and maintenance of first aid and emergency response equipment are essential for minimizing the impact of accidents involving hazardous chemicals. Regular training on using this equipment and emergency response procedures can further enhance chemical safety in the workplace. By being prepared for emergencies and providing the necessary resources, organizations can significantly reduce the risk of serious injuries and create a safer work environment for their employees.
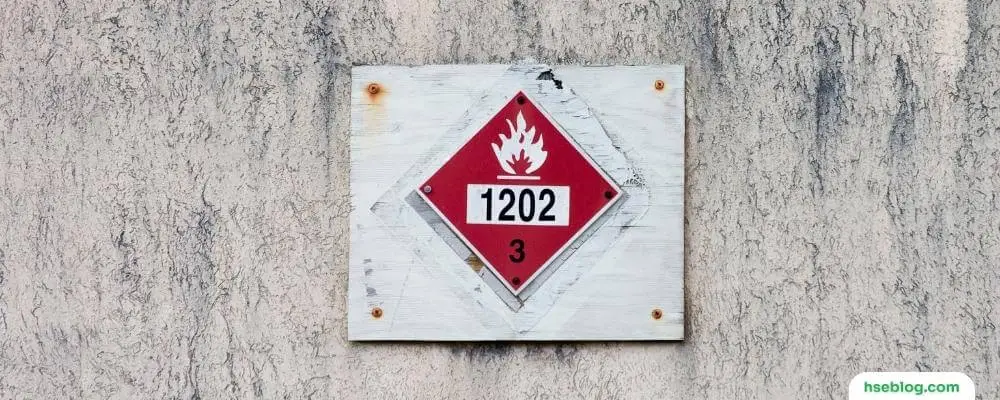
6. Training and Education
Training and education are critical in ensuring employees’ safety with hazardous chemicals. Proper training helps workers understand the risks associated with chemicals, how to handle them safely, and what to do in emergencies. The following are essential aspects of training and education for chemical safety:
Importance of proper training in handling and storage of chemicals
Employees should be trained to understand the dangers associated with the chemicals they work with and the precautions necessary to prevent accidents. This includes proper handling techniques, storage requirements, and disposal methods. Training should be tailored to the specific chemicals and hazards present in the workplace.
Regular safety drills and simulations
Regular safety drills and simulations help employees practice their skills and knowledge in a controlled environment, reinforcing their training and preparing them for real-life emergencies. These drills should cover various scenarios, such as chemical spills, fires, or exposure incidents, and involve using safety equipment and emergency response procedures.
Hazard communication and labeling
Workers should be trained to understand hazard communication standards, such as the Globally Harmonized System (GHS) for the Classification and Labeling of Chemicals. This includes recognizing hazard pictograms, understanding safety data sheets (SDS), and interpreting chemical labels. Proper hazard communication helps employees identify and understand the chemical risks and take appropriate precautions.
MSDS (Material Safety Data Sheets) and SDS (Safety Data Sheets) management
Employees should be trained to access, read, and understand Material Safety Data Sheets (MSDS) and Safety Data Sheets (SDS) for the chemicals they work with. These documents provide information about specific chemicals’ properties, hazards, and safety precautions. Regular training on MSDS and SDS management ensures employees are always updated with the latest safety information.
Comprehensive training and education programs are vital in fostering a workplace safety culture dealing with hazardous chemicals. By ensuring that employees are knowledgeable about the chemicals they work with, how to handle them safely, and what to do in emergencies, organizations can significantly reduce the risk of accidents and create a safer work environment for everyone. Regular training sessions, safety drills, and ongoing education can help maintain a high safety awareness and preparedness level among the workforce.
Conclusion
Ensuring chemical safety in the workplace requires effective emergency and safety equipment, proper training, and a strong safety culture. This includes using Personal Protective Equipment (PPE), appropriate storage solutions, fire safety equipment, ventilation, and air filtration systems, first aid and emergency response equipment, and comprehensive training and education programs.
By investing in these essential components and fostering a culture of safety awareness, organizations can significantly reduce the risk of accidents, injuries, and environmental hazards associated with hazardous chemicals. By prioritizing employee safety and adhering to industry best practices and regulations, businesses can create a safer work environment for everyone while enhancing productivity and maintaining regulatory compliance.