The Material Safety Data Sheet (MSDS) is a crucial reference document that demystifies the complexity of chemical safety in the workplace. Whether you’re an employer, an employee, or a safety officer, understanding the relevance and application of MSDS can significantly enhance safety practices and compliance. This blog will delve into the concept of MSDS, breaking down its components, importance, and how it functions as a critical tool in the broader context of occupational health and safety.
We will explore the diverse facets of MSDS to provide you with a comprehensive understanding of its role in ensuring a safer work environment. So, let’s embark on this informational journey into the world of MSDS.
What is a Material Safety Data Sheet (MSDS)?
A Material Safety Data Sheet (MSDS), also known as a Safety Data Sheet (SDS), is a detailed informational document prepared by the manufacturer or importer of a hazardous chemical. It describes the physical and chemical properties of the product. MSDSs contain useful information such as flash points, toxicity, procedures for spills and leaks, and first aid information.
In simple terms, an MSDS is a paper or electronic document that provides detailed information about the risks of a hazardous chemical and advice about safety precautions. It’s about detailed chemical and physical information, hazards, handling and storage procedures, and what to do in an emergency. MSDSs are used not only in the workplace but also for use by environmental health and safety professionals.
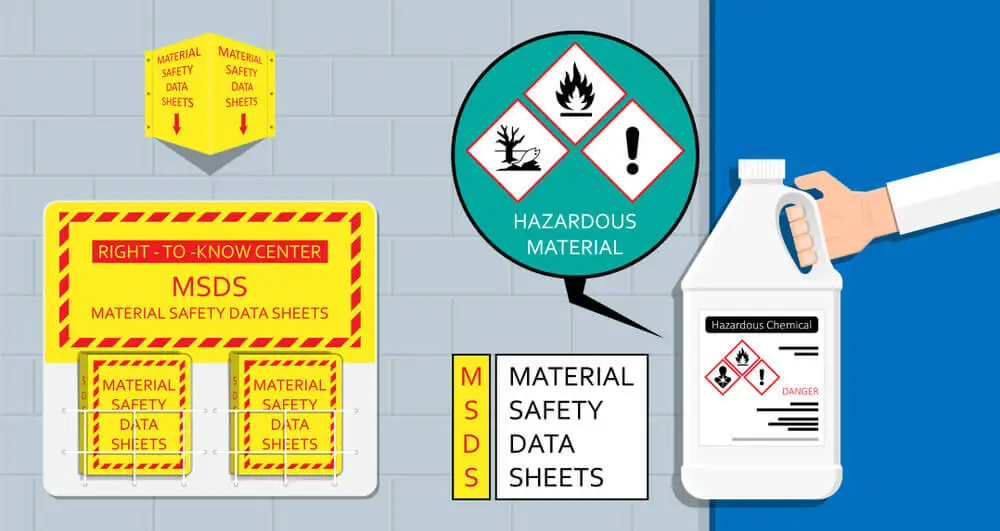
Purpose Of Using Material Safety Data Sheets
The purpose of Material Safety Data Sheets (MSDS), now known as Safety Data Sheets (SDS), is to provide detailed information about a specific hazardous substance. This document is particularly crucial for workplaces where these substances are used or handled. The main objectives of an MSDS are:
- Identifying Hazards: MSDS provides detailed information about the physical and chemical properties of the substance, its hazards, how it can be safely stored, handled, and used, what to do in case of an emergency, and the measures to be taken if someone is exposed to it.
- Protecting Workers: MSDS protects workers from potential harm by providing information about the hazards associated with a chemical or product. They contain detailed first aid measures and recommended personal protective equipment for handling the substance.
- Emergency Preparation: In an emergency involving a substance, such as a spill or fire, the MSDS provides crucial information on handling the situation safely.
- Environmental Safety: MSDS also provides information on the environmental impact of the substance, including details on how to dispose of the substance safely and environmentally friendly.
Benefits of using MSDS
- Worker Safety: When employees know the hazards and understand how to handle a substance safely, the risk of accidents and injuries is significantly reduced.
- Compliance: Providing MSDS helps organizations comply with safety regulations and standards, such as those set by OSHA in the United States. Failure to provide these documents can lead to penalties.
- Efficient Emergency Response: In an accident or emergency, having access to MSDS allows for a quick and efficient response, potentially reducing harm and damage.
- Knowledge and Training: MSDS are valuable resources for training new employees about the potential hazards in the workplace and the safe handling of substances.
In summary, the purpose of MSDS is to inform and protect workers and the environment, and the benefits of using them include increased safety, regulatory compliance, efficient emergency response, and better training.
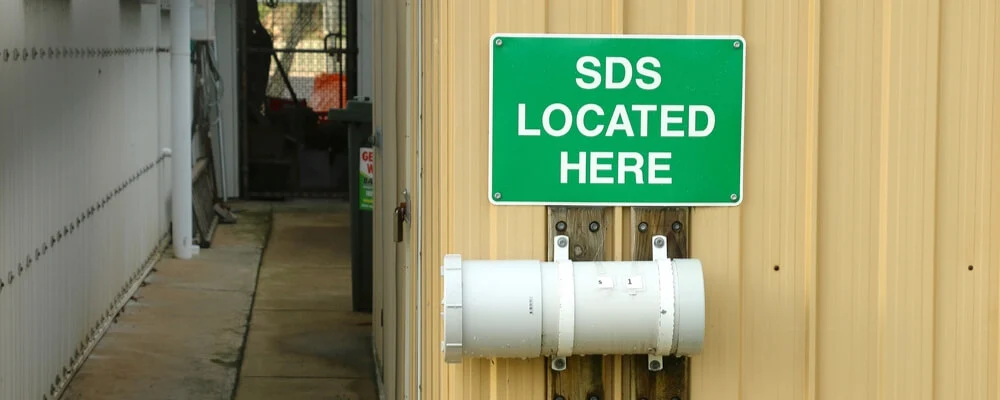
Components of a Material Safety Data Sheet (MSDS)
A Material Safety Data Sheet (MSDS) typically contains various sections that provide essential information about a chemical substance or product. While the specific format may vary depending on regional regulations and industry practices, the following are the common components found in an MSDS:
- Identification: This section provides the product’s name and the manufacturer’s or distributor’s name, address, and contact information. It may also include an emergency phone number for immediate contact in a crisis. Information on recommended use and restrictions on use can also be found in this section.
- Hazard Identification: Here, you’ll find a description of the physical, health, and environmental hazards associated with the substance. This could include whether the material is flammable, corrosive, toxic, or an irritant. The severity of these hazards is often represented using signal words like “warning” or “danger” and hazard statements that describe the nature of the risk.
- Composition/Information on Ingredients: This section lists the substance’s chemical components and relative concentrations. Not all ingredients may be listed for complex mixtures, but those contributing to the product’s hazard level will be.
- First Aid Measures: This area details the actions to take if a person is exposed to the chemical—inhalation, skin or eye contact, or ingestion. It describes symptoms and required treatment; the information should be specific and practical.
- Fire-Fighting Measures: Here, you will find the best methods to extinguish a fire involving the material, any special protective equipment for firefighters, and potential hazards that may arise when the substance is burned.
- Accidental Release Measures: This portion details the steps to follow if the substance spills or leaks, including emergency procedures, protective equipment, and methods for containment and cleanup to prevent environmental damage.
- Handling and Storage: This section offers guidelines for safely handling the substance to minimize exposure and instructions for properly storing the substance to prevent accidents, like fire or exposure to hazardous fumes.
- Exposure Controls/Personal Protection: This area includes measures to limit workers’ exposure to the substance, such as recommendations on specific types of ventilation, personal protective equipment like gloves or respirators, and what type of eye protection should be worn.
- Physical and Chemical Properties: This section provides technical data about the substance, such as its appearance, odor, boiling and melting points, flash point (the temperature at which it can ignite), solubility in water, and other relevant characteristics.
- Stability and Reactivity: Here, you’ll find information on the substance’s stability under normal conditions, as well as any materials it might react with, creating a hazardous situation. This might include light, heat, or other chemicals.
- Toxicological Information: This part describes the health effects of exposure to the substance, including immediate effects and any long-term health problems it could cause.
- Ecological Information: This section provides information on the substance’s environmental impact, including toxicity to aquatic organisms, persistence and degradability, and its bio-accumulation potential.
- Disposal Considerations: It includes recommendations for appropriate disposal practices, recycling or reclamation of the chemical or its container, and safe handling practices.
- Transport Information: This section provides guidance on how to safely transport the substance, including any special precautions that should be taken.
- Regulatory Information: This area offers additional details about the substance as required by specific regulations. This could include regulations from various jurisdictions, such as international, federal, state or local.
By having an in-depth understanding of these sections, users of these substances can mitigate risks and ensure safe handling and storage, ensuring the safety of individuals and the environment.
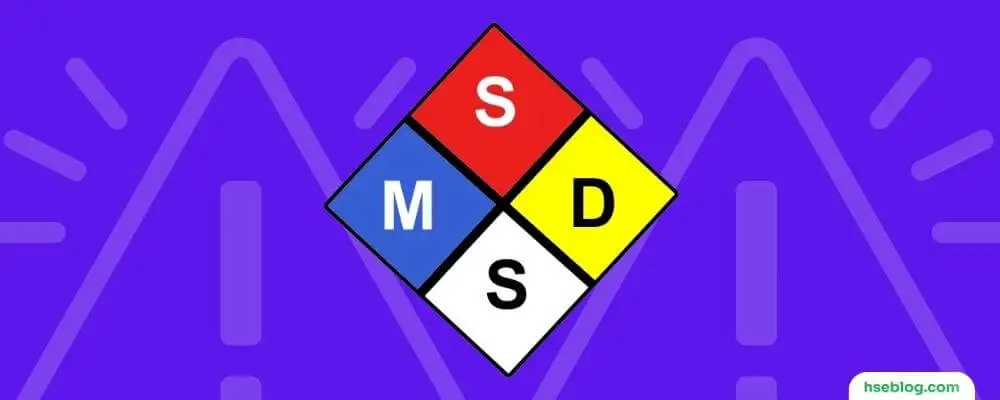
Tips For Using Material Safety Data Sheets
Using Material Safety Data Sheets (MSDS), now called Safety Data Sheets (SDS), can be crucial in maintaining a safe working environment. Here are some tips for using these documents:
- Accessibility: Ensure the SDS for each substance in your workplace is readily available and easily accessible to all employees. This could be in a physical binder or a digital database, but the employees must know where to find it.
- Reading and Understanding: All employees who handle hazardous substances should read and understand the SDS for each substance they use. The document should not just be skimmed over but read in detail.
- Training: Employers should provide training to their employees on how to read and understand an SDS. Employees need to know what information is available and how to use that information.
- Stay Updated: SDS should be kept up to date. Manufacturers will update their SDS when new information becomes available, and it’s important to ensure that you’re using the most recent version.
- Emergency Procedures: The SDS contains valuable information about what to do in an emergency, such as a spill or exposure. Make sure that everyone who uses the chemical knows these procedures.
- Personal Protective Equipment (PPE): The SDS specifies what PPE is required when handling the substance. Ensure this equipment is available and everyone knows how to use it correctly.
- First Aid Information: Know where to find the first aid information on the SDS. In case of exposure, it’s important to act quickly, and knowing where to find this information can save precious time.
- Proper Storage and Disposal: The SDS will provide information on properly storing and disposing of the chemical. Ensure these guidelines are followed to prevent accidents.
- Regular Review: Regularly review SDS for all chemicals in your workplace. Regulations and recommended safety measures can evolve even if the chemical composition doesn’t change.
- Communication: Any changes or updates to SDS should be communicated to all employees handling the chemical.
By using these tips, companies and employees can ensure they’re handling, storing, and disposing of hazardous substances safely and prepared in an emergency.
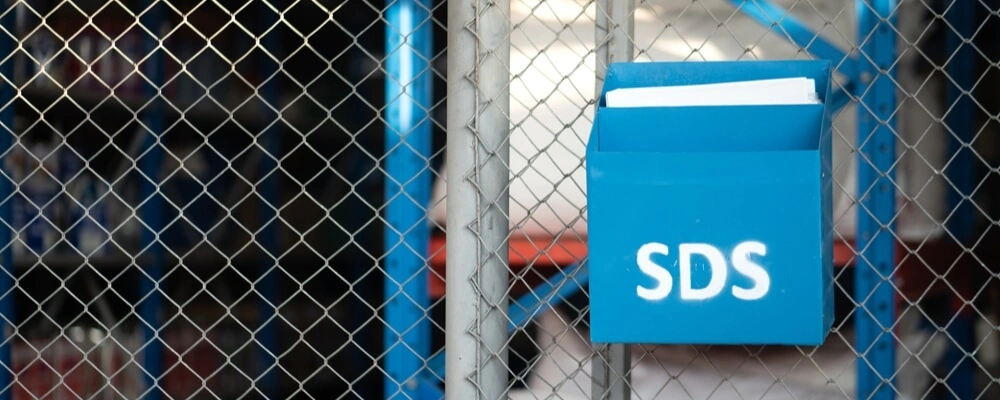
How to Access Material Safety Data Sheets (MSDS)?
Material Safety Data Sheets (MSDS), now known as Safety Data Sheets (SDS), are typically provided by the manufacturer or supplier of a product. Here are a few ways you can access them:
- Directly from the manufacturer or supplier: Manufacturers and suppliers of hazardous chemicals must provide an MSDS with their products. If you can’t find an MSDS that was supposed to come with a product, contact the manufacturer or supplier directly to ask for it.
- Manufacturer or supplier website: Many manufacturers and suppliers provide MSDS for their products on their websites. Look for a link to “MSDS,” “Safety Data Sheets,” or “Product Safety” on the company’s website.
- Online databases: Several online databases collect and provide access to MSDS from various manufacturers and suppliers. These include databases run by private companies, industry associations, and government agencies. Examples include the SIRI MSDS Index, MSDSonline, and the National Library of Medicine’s PubChem database in the United States. While these databases can be useful, they may not always have the most recent version of an MSDS. If possible, always get the most up-to-date information directly from the manufacturer or supplier.
- In the workplace: Employers must keep a copy of the MSDS for every hazardous chemical used and make them readily accessible to employees. They can be kept in a binder in a central location or stored electronically as long as employees know how to access them and there is a backup system in case of computer or power failures.
Remember, it’s important to ensure that the MSDS you are referring to is the most recent version as manufacturers and suppliers must update their MSDS whenever new significant information about a product’s health, safety, or environmental hazards becomes available.
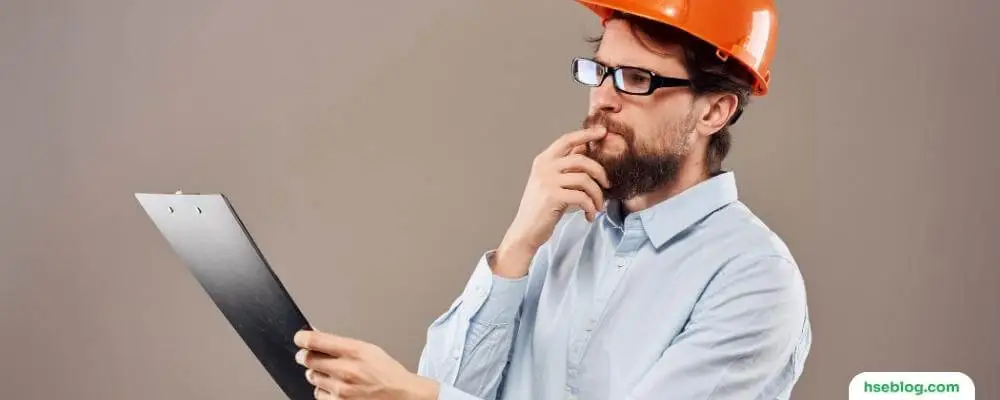
Historical Background And Evolution Of MSDS
The concept of Material Safety Data Sheets (MSDS), now known as Safety Data Sheets (SDS), traces its roots back to the late 20th century when workplace safety emerged as a significant concern. Here’s a brief look at the history and evolution of MSDS:
- 1970s – OSHA Formation and the Hazard Communication Standard: In the United States, the Occupational Safety and Health Administration (OSHA) was established in 1970 to ensure workers’ safe and healthy working conditions. One of the regulations OSHA enforced was the Hazard Communication Standard (HCS), originally promulgated in 1983. This standard required chemical manufacturers and importers to evaluate the hazards of the chemicals they produce or import and provide information about them through labels on shipped containers and more detailed information sheets called MSDS.
- 1994 – Standardization of MSDS: In 1994, OSHA revised the HCS to include a standardized 16-section format for MSDS. This format was voluntary but recommended to help users find pertinent information quickly and easily. It included information such as product and company identification, hazard identification, first-aid measures, fire-fighting measures, accidental release measures, handling and storage, exposure controls/personal protection, physical and chemical properties, stability and reactivity, toxicological information, and ecological information.
- 2002 – Introduction of the Globally Harmonized System (GHS): 2002 the United Nations adopted the Globally Harmonized System of Classification and Labeling of Chemicals (GHS). This system aimed to standardize and harmonize hazard classification and communication globally, including standardizing the format and content of safety data sheets.
- 2012 – OSHA Adopts GHS: In 2012, OSHA revised its HCS to align with the GHS. As part of this update, “Material Safety Data Sheets” was replaced with “Safety Data Sheets,” and the standardized 16-section format was made mandatory. Adopting the GHS helped ensure that the same set of labels, pictograms, and safety data sheets could be used for hazardous chemicals worldwide, making it easier for workers to understand the hazards, especially for those who work with chemicals from multiple sources.
Over the years, the MSDS (now SDS) has evolved significantly, with a primary goal of improving workplace safety by providing clear, concise, and standardized information on the hazards of chemicals and how to handle them safely.
Note:
Please note that while we strive to provide accurate and timely information, laws and regulations regarding MSDS can change. So, it’s always a good idea to consult with a local authority or expert in your area if you have specific questions.
Conclusion
In conclusion, the Material Safety Data Sheet (MSDS) is a fundamental resource in occupational safety. It’s a comprehensive document that provides vital information about the nature of chemicals used in the workplace, their risks, and the precautions necessary for safe handling and use. Beyond its role in everyday operations, the MSDS is instrumental in training employees, preparing for emergencies, and ensuring regulatory compliance.
This guide provides a complete overview of an MSDS, its components, purpose, and use. By understanding and effectively utilizing MSDS, companies can ensure a safer work environment and foster an informed and alert workforce, which is the bedrock of any successful safety program.