Personal Protective Equipment, or PPE as it is more commonly known, serves a vital function in the world of work, particularly in industries where workers are exposed to various hazards such as chemicals, noise, dust, and heavy machinery. The main purpose of PPE is to safeguard the health and safety of workers by reducing their exposure to these hazards, therefore minimizing the likelihood of occupational illnesses and injuries.
PPE ranges from gloves and hard hats to goggles, masks, earplugs, and safety shoes, each designed to protect a specific body part against a specific hazard. The significance of PPE cannot be understated, as it forms a critical line of defence that protects millions of workers across the globe every day.
In this detailed blog post, we will explore six types of Personal Protective Equipment: eye and face protection, respiratory protection, head protection, hand protection, foot protection, and hearing protection. We aim to give you a thorough understanding of the different types of PPE, their features, how they are used, and the specific dangers they are designed to guard against.
What is PPE? Meaning and Full Form
PPE stands for Personal Protective Equipment, which refers to specialized gear designed to safeguard individuals from various workplace hazards. This equipment includes items such as helmets, gloves, eye protection, high-visibility clothing, and respiratory devices. PPE is essential in environments where risks cannot be entirely eliminated through other means, providing a critical barrier between the wearer and potential dangers like chemicals, physical impacts, or infectious agents.
The proper use of PPE is fundamental in ensuring the safety and health of workers across diverse industries, including construction, healthcare, and manufacturing. By wearing appropriate protective gear, individuals can significantly reduce the likelihood of injuries and illnesses, thereby promoting a safer and more productive work environment. Additionally, adherence to PPE guidelines helps organizations comply with safety regulations and standards, ultimately contributing to overall operational effectiveness and employee well-being.
Types of PPE (Personal Protective Equipment)
OSHA standards require using PPE to reduce employee exposure to hazards when engineering and administrative controls are not feasible or effective in reducing these exposures to acceptable levels. Employers are required to determine if PPE should be used to protect their workers. They must also ensure employees use and maintain PPE in a sanitary and reliable condition.
Personal protective equipment (PPE) is an important part of safety measures in any workplace. It protects individuals from potential risks, such as exposure to infectious diseases, hazardous materials, and other physical hazards. Different types of PPE are available, depending on the specific application or risk. Let’s take a look at the different types of PPE:
1. Eye and Face Protection
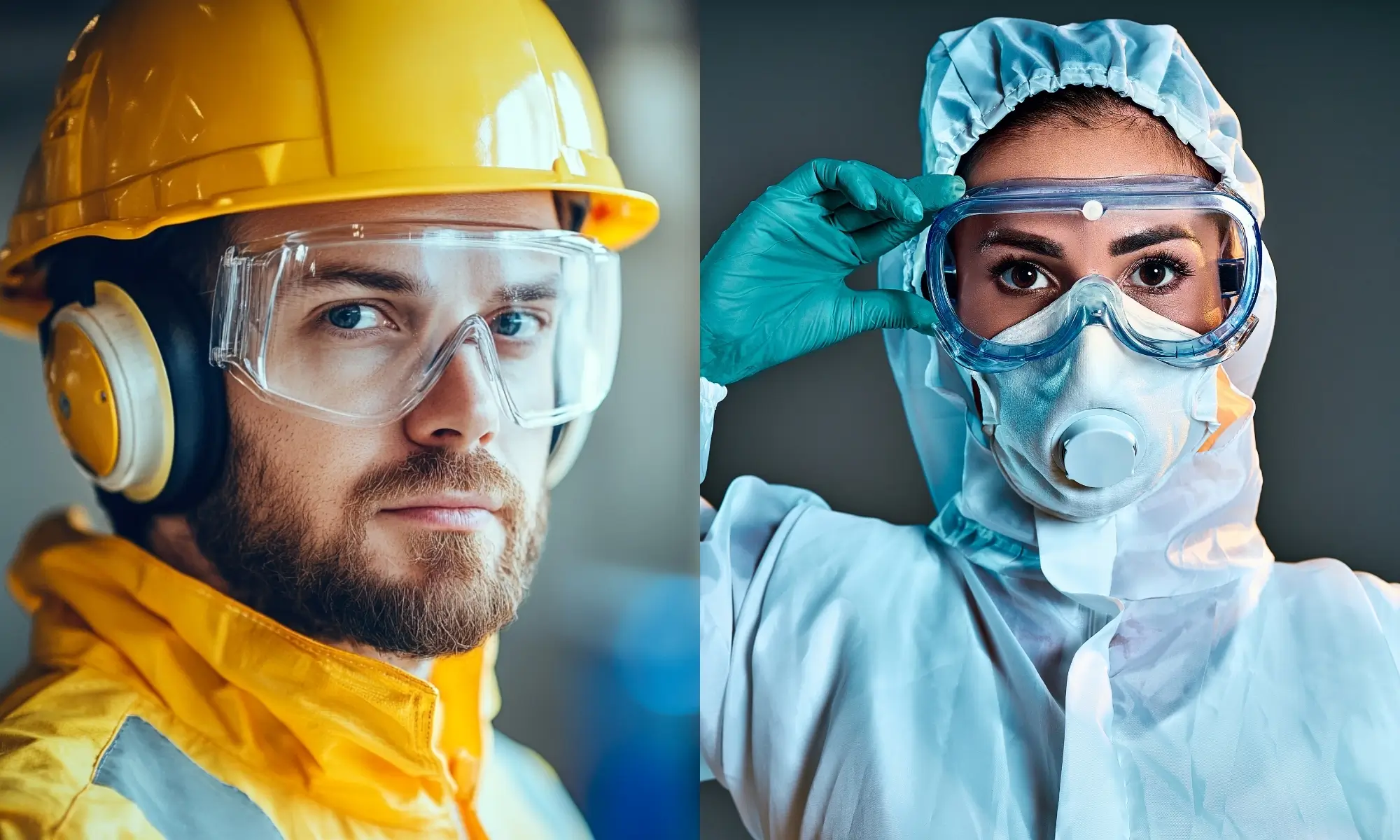
Protective eye and face devices must comply with ANZI Z87.1, “American National Standard Practice for Occupational and Educational Eye and Face Protection,” and OSHA Standard 1910.133, Eye and Face Protection.
Glasses
Protective eyeglasses or spectacles are made with safety frames, tempered glass or plastic lenses, temples, and side shields, which provide eye protection from moderate impact and particles encountered in job tasks such as carpentry, woodworking, grinding, scaling, etc. Safety glasses are also available in prescription form for those persons who need corrective lenses.
Goggles
- Vinyl-framed goggles of soft, pliable body design provide adequate eye protection from many hazards. These goggles are available with clear or tinted lenses and perforated, port-vented, or non-vented frames.
- Single-lens goggles provide similar protection to spectacles and may be worn with spectacles or corrective lenses to ensure protection and good vision.
- Welders’ goggles provide protection from sparking, scaling, or splashing metals and harmful light rays. Lenses are impact resistant and are available in graduated shades of filtration.
- Chipper/Grinder goggles provide eye protection from flying particles. The dual protective eye cups house impact-resistant clear lenses with individual cover plates.
Face Shields
These usually consist of an adjustable headgear and face shield of tinted/transparent acetate, polycarbonate materials, or a wire screen. Face shields are available in various sizes, tensile strength, impact/heat resistance, and light ray-filtering capacity. Face shields will be used in operations when the entire face needs protection. They should be worn to protect the eyes and face against flying particles, metal sparks, and chemical/biological splashes.
Welding Shields
These shield assemblies consist of the following:
- Vulcanized fiber or glass fiber body
- A ratchet/button type adjustable headgear or cap attachment
- A filter and cover plate holder
These shields will be provided to protect worker’s eyes and faces from infrared and ultraviolet light burns to the retina, flying sparks, metal spatter, and slag chips encountered during the:
- Welding;
- Brazing;
- Soldering;
- Resistance welding;
- Bare or shielded electric arc welding;
- Oxyacetylene welding; or
- Cutting operations.
2. Respiratory Protection
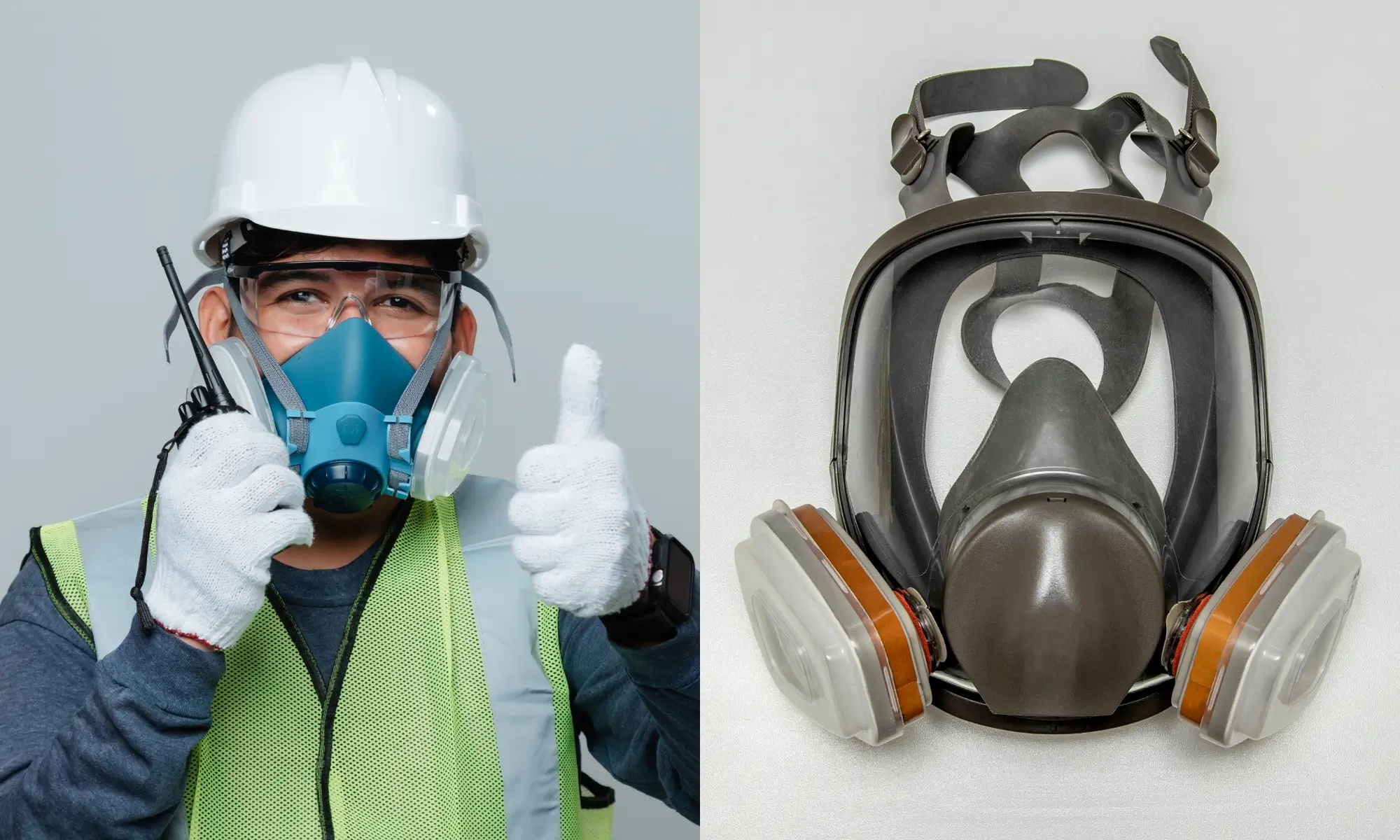
Respiratory Protection is essential when employees are exposed to potentially hazardous atmospheres. Respirator use must conform to ANSI/ASSE Z88.2, Practices for Respiratory Protection, and OSHA Standard 1910.134, Respiratory Protection.
Respirator Types
To understand how respirators can be used to protect employees, it is essential to understand what a respirator is and is not. A respirator protects against respiratory hazards by removing specific air contaminants from the ambient (surrounding) air or supplying breathable air from a safe source.
- Air-purifying respirators: Respirators that remove contaminants from the ambient air are called air-purifying respirators. Particulate respirators are a type of air-purifying respirator. The part of a respirator that forms a protective barrier between the user’s respiratory tract and air contaminants is called an inlet covering. Most inlet coverings are classified as either tight-fitting or loose-fitting.
- Tight-fitting respirator: A tight-fitting respirator has an inlet covering, also called a face piece or mask, designed to form a seal with the face of the wearer. It is available in three types: quarter mask, half mask, and full-face piece.
- Loose-fitting respirator: A loose-fitting respirator has an inlet covering that typically covers the user’s head and may extend over the shoulders. It is designed to form a partial seal with the face. These include loose-fitting face pieces, hoods, helmets, or full suits, all of which cover the head completely.
- Atmosphere-supplying respirators: Respirators that supply air from a safe source other than the ambient air are called atmosphere-supplying respirators. There are two types of atmosphere-supplying respirators: Supplied-Air Respirators (SARs) and Self-Contained Breathing Apparatuses (SCBA).
3. Head Protection
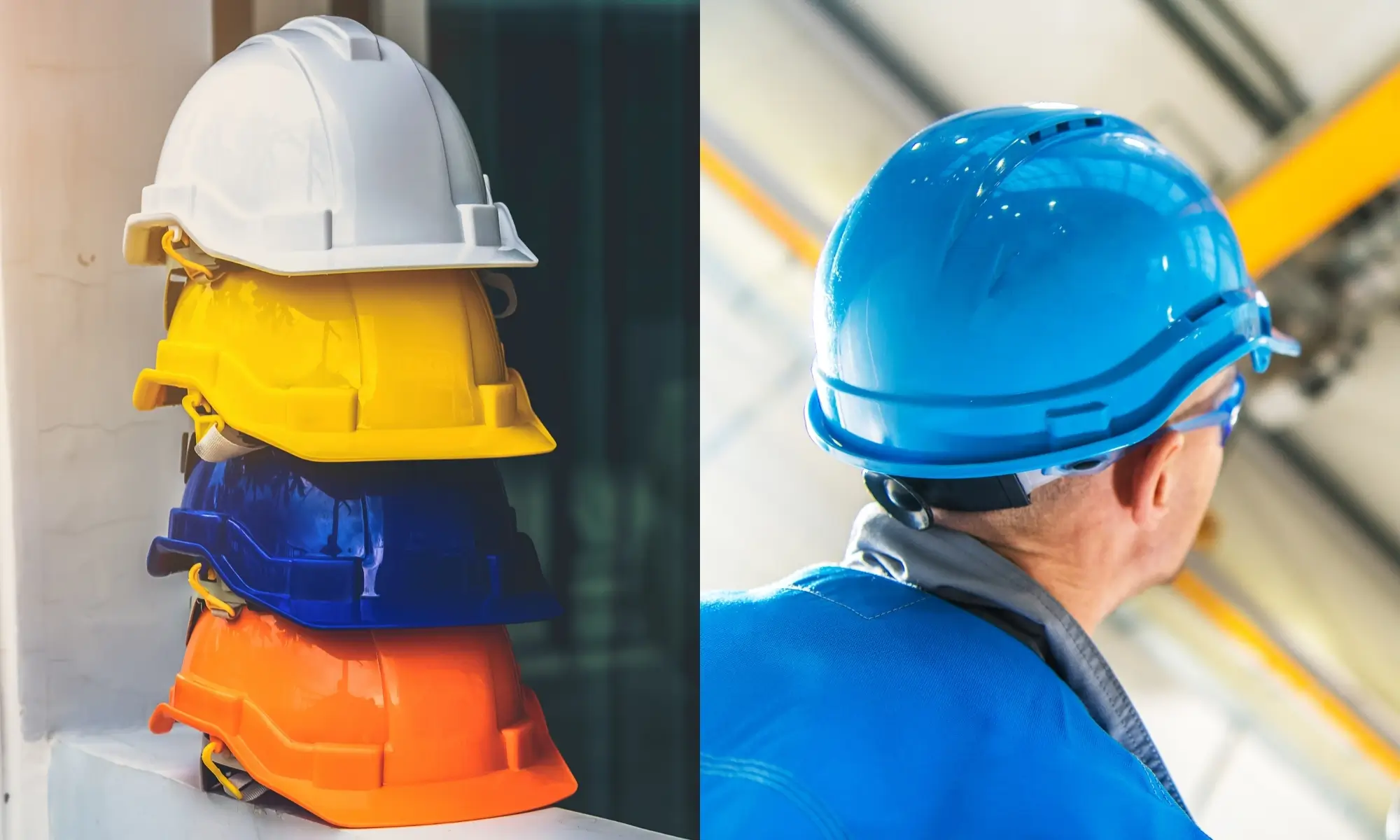
Head protection Personal Protective Equipment (PPE) is essential to protecting workers in hazardous work environments. It includes a wide range of products, from hard hats and face shields to welding helmets and respirators, designed to reduce the risk of injury from head trauma, excessive noise, exposure to dangerous fumes and chemicals, and other hazards. Here is an overview of the different types of head protection PPE available:
Hard Hats: Hard hats are the most recognizable type of head protection PPE and are designed to protect against blows to the head from falling objects, bumps, and other impacts. They are made of a hard plastic shell with inner padding for cushioning and come in various colors for easy identification by employers.
There are primarily two situations when employees must wear protective helmets.
1. Falling Objects
When there is a potential for injury to the head from falling objects in the workplace, the employer must ensure that each affected employee wears a protective helmet.
Some examples of work that might require helmets to protect from falling objects include:
- Working below other workers who are using tools and materials which could fall;
- Working around or under conveyor belts that are carrying parts or materials; and
- Working below machinery or processes might cause materials or objects to fall.
Some examples of occupations for which head protection should be routinely considered are:
- Carpenters
- Electricians
- Linemen
- Mechanics and repairers
- Plumbers and pipe fitters
- Assemblers
- Packers
- Wrappers
- Sawyers
- Welders
- Laborers
- Freight handlers
- Timber cutting and logging
- Stock handlers
- Warehouse laborers
2. Electrical Hazards
The second situation requiring a helmet is to protect the worker from electrical hazards. Whenever an employee works near exposed electrical conductors that could contact the head, the employer must ensure that the employee wears a protective helmet to reduce electrical shock hazards.
The employer should also furnish and ensure all employees and contractors engaged in construction and other miscellaneous work use proper head protection. Engineers, inspectors, and visitors at construction sites must wear protective helmets when hazards from falling, fixed objects, or electrical shock are present.
Criteria for Protective Helmets
Protective helmets with OSHA 1910.135, Head Protection states that helmets purchased after July 5, 1994, must comply with ANSI Z89.1 or must be demonstrated by the employer to be equally effective. Purchasing helmets that meet these standards ensures that appropriate testing has been conducted and that the quality of the materials (webbing and shell) is adequate.
Selection Guidelines for Head Protection
Knowledge of the potential for falling objects and electrical hazards is essential when selecting head protection. When it’s determined that these hazards exist, choose the most appropriate helmet from the categories listed below.
Impact Type Helmets
- Type I: A helmet of Type I is designed to provide protection only to the top of the head. It is not intended to provide impact from side impacts. (This is by far the most commonly used type of hard hat.)
- Type II: A Type II helmet is designed to protect against top and side impacts.
Electrical Classes
- Class G (General): Class G helmets are intended to reduce the danger of contact exposure to low-voltage conductors. Test samples are proof-tested at 2200 volts (phase to ground). However, this voltage does not indicate the voltage at which the helmet protects the wearer.
- Class E (Electrical): Class E helmets are intended to reduce the danger of exposure to high-voltage conductors. Test samples are proof-tested at 20,000 volts (phase to ground). However, this voltage does not indicate the voltage at which the helmet protects the wearer.
- Class C (Conductive): Class C helmets are not intended to provide protection against contact with electrical conductors.
Bump caps or skull guards should be issued and worn for protection against scalp lacerations from contact with sharp objects. However, it’s essential to understand that they must not be worn as substitutes for safety caps/hats because they do not provide protection from impact forces or penetration by falling objects.
4. Hand Protection
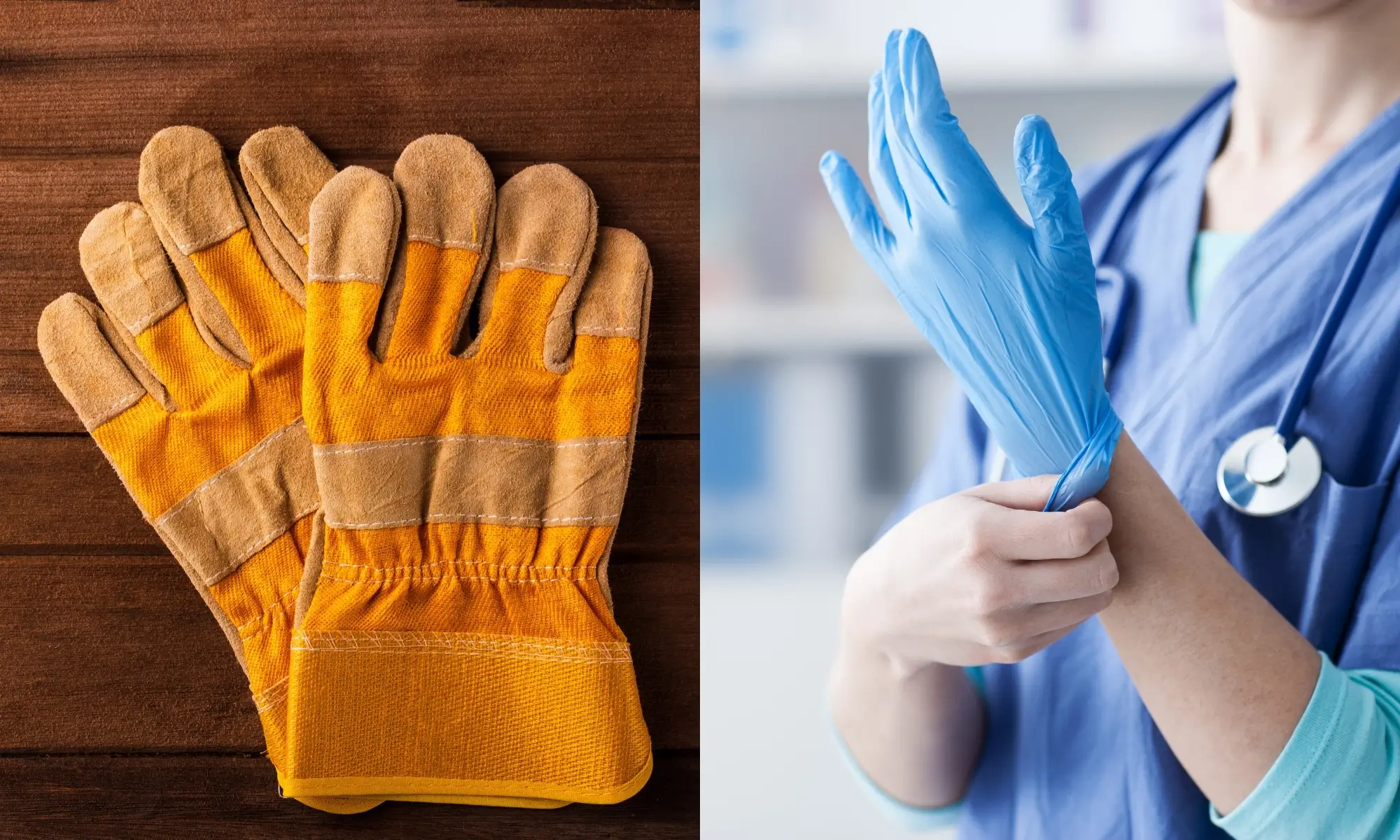
Employers must select and require employees to use appropriate hand protection when exposed to any of the hazards listed below:
- hazardous chemicals that can cause burns, rashes, and internal injury;
- cuts or lacerations;
- abrasions; • punctures;
- thermal burns; and
- harmful temperature extremes.
Glove Guide
Below is a guide to the most common types of protective work gloves and the types of hazards they can guard against:
- Disposable Gloves: Disposable gloves, usually lightweight plastic, can help guard against mild irritants.
- Fabric Gloves: These gloves are made of cotton or fabric blends. They’re generally used to improve grip when handling slippery objects. They also help insulate hands from mild heat or cold.
- Leather Gloves: These gloves guard against injuries from sparks or scraping against rough surfaces. They are also used with an insulated liner when working with electricity.
- Metal Mesh Gloves: These gloves protect hands from accidental cuts and scratches. People commonly use them with cutting tools or other sharp instruments.
- Aluminized Gloves: These gloves made of aluminized fabric are designed to insulate hands from intense heat. These gloves are most commonly used by persons working with molten materials.
- Chemical Resistance Gloves: These gloves may be rubber, neoprene, polyvinyl alcohol or vinyl, etc. The gloves protect hands from corrosives, oils, and solvents. When selecting chemical resistance gloves, consult the manufacturer’s recommendations, especially if the gloved hand is immersed in the chemical.
Selection of Hand Protection
Employers must work closely with their PPE suppliers to select appropriate hand protection based on an evaluation of the performance characteristics of the hand protection. The employer needs to look at each of the following:
- Specific task(s) being performed;
- Environmental conditions present;
- Duration of hand protection use while performing the task;
- The actual hazards; and
- Potential hazards.
The work activities of the employee should also be studied to determine the following:
- The degree of dexterity required;
- The duration of the task;
- The frequency of the task;
- Degree of exposure to the hazard; and
- The physical stresses that will be applied.
Gloves should be replaced periodically, depending on the frequency of use and permeability to the substance(s) handled. Gloves overtly contaminated should be rinsed and then carefully removed after use. With this in mind, there are two essential characteristics of gloves to consider.
- Permeation rate: The permeation rate measures the time it takes a given material (glove) to become saturated by the chemical through absorption.
- Breakthrough or Penetration rate: The penetration rate measures the speed with which a given chemical breaks through the layer(s) of the glove to contact the skin.
Gloves should also be worn whenever it is necessary to handle rough or sharp-edged objects and very hot or cold materials. The type of glove material used in these situations includes leather, welder gloves, aluminum-backed gloves, and other insulated gloves.
Glove Selection Chart
You can use the chart on the next page to help select the proper gloves for the job. It may serve as a guide to the different types of glove materials and the chemicals they can be used against.
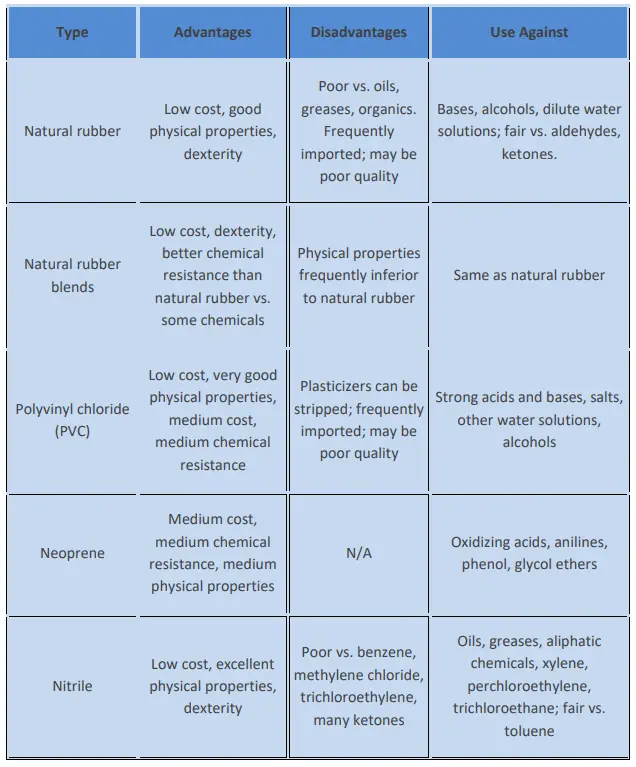
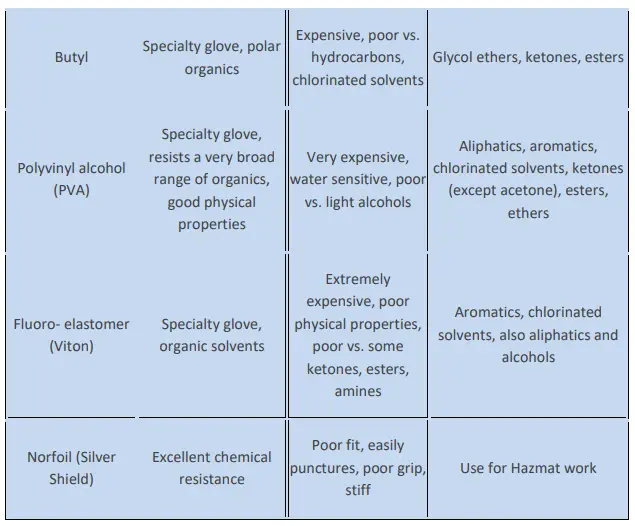
5. Foot Protection
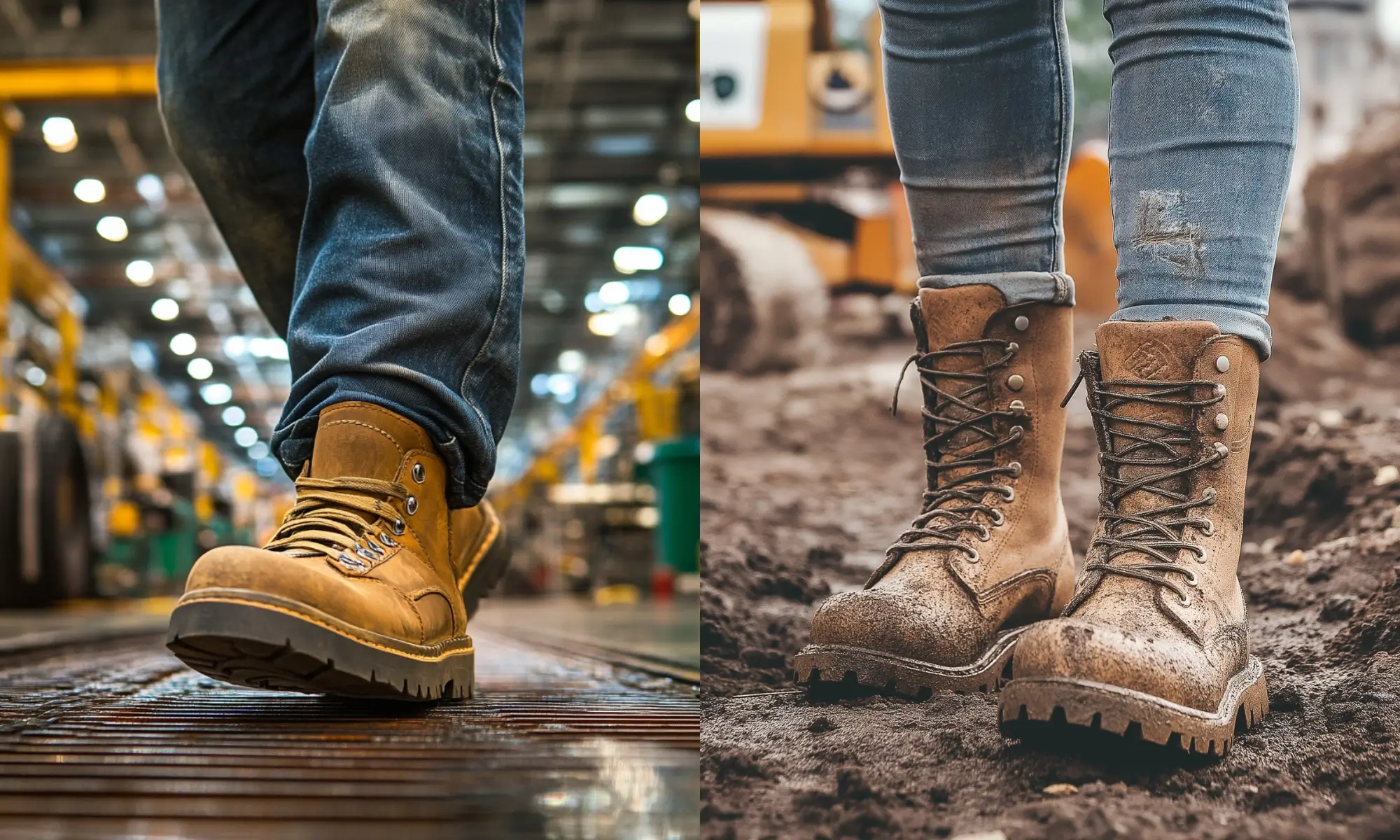
The employer must make sure that each affected employee uses protective footwear when working in areas where there is a danger of foot injuries due to the following:
- Falling or rolling objects;
- Objects piercing the sole; and/or
- Where feet are exposed to electrical hazards.
Criteria for Protective Footwear
Protective footwear purchased after July 5, 1994, must comply with ANSI Z41-1991, ANSI Z41- 1999, or ASTM F-2413-2005, “Standard Specification for Performance Requirements for Protective Footwear” (before July 5, 1994 – ANSI Z41.1-1967) or must be demonstrated by the employer to be equally effective. Footwear that meets established safety standards will have an American National Standards Institute (ANSI) label inside each shoe.
Types of Footwear
1. Steel-Reinforced Safety Shoes: These shoes protect feet from common machinery hazards such as falling or rolling objects, cuts, and punctures. The entire toe box and insole are reinforced with steel, and the instep is protected by steel, aluminum, or plastic materials. Safety shoes are also designed to insulate against temperature extremes and may be equipped with unique soles to guard against slips, chemicals, and/or electrical hazards.
2. Safety Boots: Safety boots offer more protection when splash or spark hazards (chemicals, molten materials) are present.
- When working with corrosives, caustics, cutting oils, and petroleum products, neoprene or nitrile boots are often required to prevent penetration.
- Foundry or “Gaiter” style boots feature quick-release fasteners or elasticized insets to allow speedy removal should any hazardous substances get into the boot.
- Special electrical hazard boots are available when working with electricity and are designed with no conductive materials other than the steel toe (which is properly insulated).
Electrical Protective Equipment : All electrical protective equipment must be maintained in a safe and reliable condition to prevent injury from exposure to electrical conductors. Electrical protective equipment includes the following:
- Insulating blankets;
- Covers;
- Line hose;
- Gloves; and
- Sleeves made of rubber.
All electrical protective equipment made of rubber should meet the established safety standards and specifications discussed below.
Inspecting Equipment: To ensure electrical protective equipment performs as designed, it must be inspected for damage before each day’s use and immediately following any incident that can reasonably be suspected of having caused damage. Insulating gloves must be given an air test along with the inspection.
Defects: Insulating equipment must not be used if any of the following defects are detected:
- a hole, tear, puncture, or cut;
- ozone cutting or ozone checking (the cutting action produced by ozone on rubber under mechanical stress into a series of interlacing cracks);
- an embedded foreign object;
- changes in the texture,, including swelling, softening, hardening, or becoming sticky or inelastic; or
- any other defect that damages the insulating properties.
Electrical Protective Gloves: Protector gloves must be worn over insulating gloves. An exception is using Class 0 gloves under limited-use conditions, where small equipment and parts manipulation necessitate unusually high finger dexterity. But, it’s important to note that extra care must be taken while visually examining the glove. Also, make sure to avoid handling sharp objects.
Any other glove class may be used for similar work without protector gloves if the employer can demonstrate that the possibility of physical damage to the gloves is slight and if the glove class is one class higher than that required for the voltage involved. Insulating gloves that have been used without protector gloves may not be used at a higher voltage until they have been tested.
Testing: Electrical protective equipment must be subjected to periodic electrical tests. Maximum
intervals between tests must be by the following table.
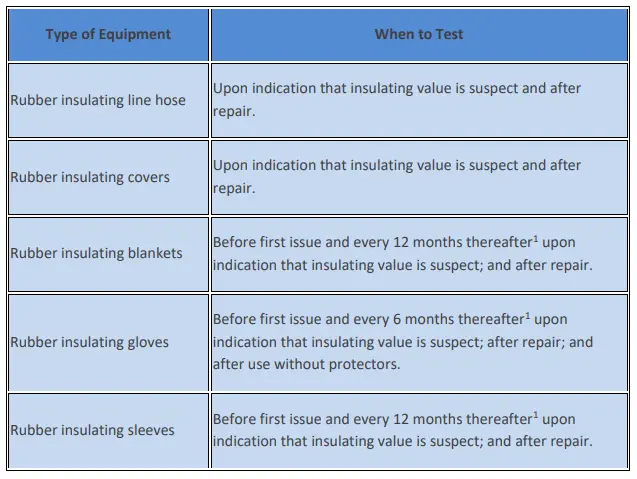
If the insulating equipment has been electrically tested but not issued for service, the
insulating equipment may not be placed into service unless it has been electrically tested within the previous 12 months.
6. Hearing Protection
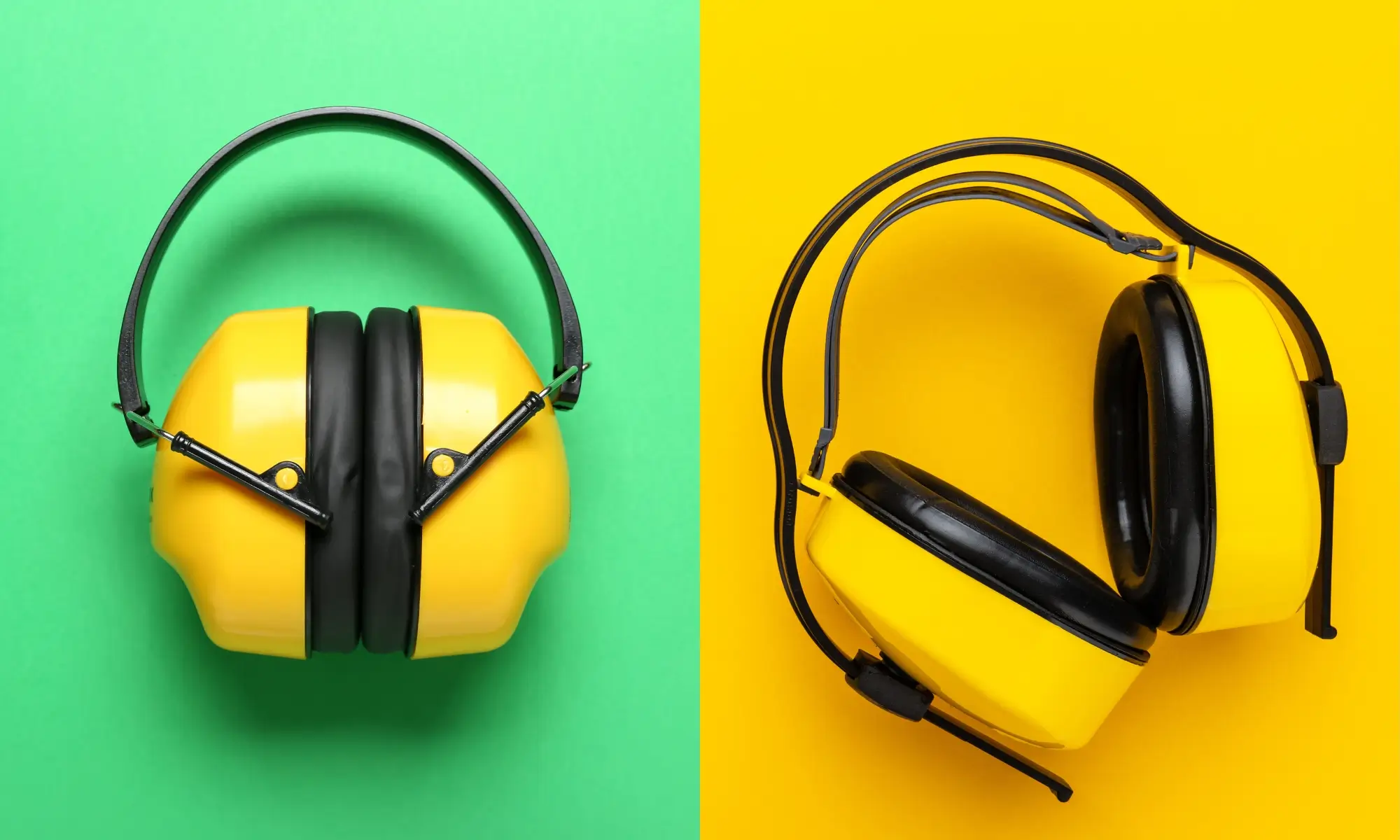
Noise-induced hearing loss is the term for hearing damaged by exposure to excessive noise. The damage to hearing caused by excessive noise at work may not be apparent for years. Hearing loss can’t be treated or cured but can be prevented.
Sound and Noise
- Sound is what you hear. Our sensation of very small, rapid changes in air pressure.
- Noise is any sound that you don’t want to hear. Sound is measured in two ways: decibels and frequency.
- Decibels indicate the pressure of sound. Sound waves transfer that pressure from place to place and are expressed in units on a logarithmic scale.
- Frequency is related to a sound’s pitch and is measured in units called hertz (Hz), or cycles per second. The pitch of a sound – how high or low it seems – is how you perceive its frequency.
Human hearing is most sensitive to frequencies between 3,000 and 4,000 Hz. That’s why people with damaged hearing have difficulty understanding higher-pitched voices and other sounds in this range.
Hearing Conservation Program
Your workplace must have a hearing conservation program if employees are exposed to noise levels equal to or greater than 85 dBA average over eight hours (called the 8- Hour Time Weighted Average). This is called the “Action Level.” Check out course 751, Hearing Conservation Program Management, for more in-depth information regarding hearing conservation.
Hearing Protectors
As you are probably aware, there are four types of hearing protectors.
- Moulded earplugs are usually made of plastic or silicone rubber. They are available in various shapes and sizes and are usually characterized by one or more ribs or contours. They are considered multiple uses; therefore, they must be cleaned and properly stored after each use.
- Custom-moulded earplugs are generally made of plastic and are designed from a moulded wax insert of the wearer’s ears. They are considered multiple uses but cannot be switched ear to ear.
- Self-moulded earplugs are generally made of mineral down or plastic foam and are moulded or formed by the wearer. Generally, one size fits all and may be either single or multiple users.
- Earmuffs are designed for multiple uses and may be worn with the harness over or behind the head or below the chin. They are generally more comfortable but usually provide less noise reduction, thus less protection, than ear plugs.
Conclusion
In conclusion, Personal Protective Equipment (PPE) is an invaluable tool in our efforts to ensure workplace safety across a multitude of industries. From steel-reinforced safety shoes to custom-moulded earplugs, the diverse range of PPE is a testament to our commitment to safeguarding workers from the potential dangers they face daily. The six types of PPE we’ve explored—eye and face protection, respiratory protection, head protection, hand protection, foot protection, and hearing protection—are each critical elements in this commitment.
As we’ve delved into each category, we’ve gained a greater understanding of the immense thought, research, and technology that goes into designing these life-saving products. But it’s important to remember that using PPE is only one component of a comprehensive safety plan. Employers should prioritize the implementation of hazard controls and safety training alongside the provision of PPE to establish a safety culture.
The right PPE can protect workers from immediate danger, but it is through knowledge, preparation, and prevention that we can reduce those dangers in the first place. Let this exploration of PPE be a stepping stone in your journey to creating a safer work environment. Remember, the safety of every worker is paramount, and it’s our collective responsibility to ensure that they have the best protection possible, every day.