Laboratories are hubs of innovation, discovery, and learning, but they also carry inherent risks due to the presence of hazardous materials, complex equipment, and high-energy processes. Ensuring a safe environment is not just a regulatory requirement but a fundamental responsibility that protects researchers, preserves the integrity of scientific work, and minimises environmental impact.
This comprehensive guide explores over 30 essential pieces of lab safety equipment every laboratory should have, highlighting how each contributes to creating a secure, efficient, and compliant research space where safety always comes first.
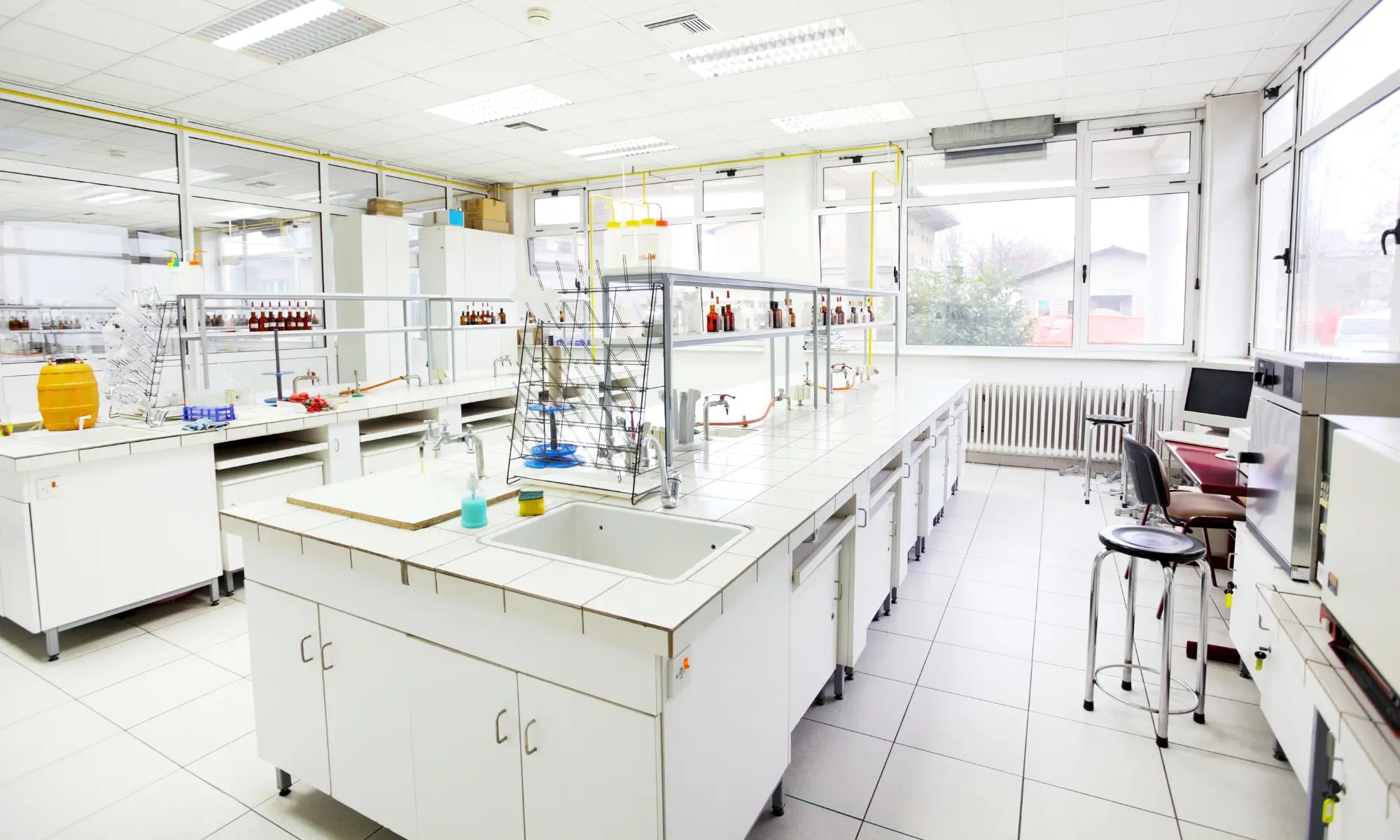
Importance and Purpose Of Lab Safety Equipment
The importance of lab safety cannot be overstated. Laboratories are places where experiments and research are conducted, often involving hazardous materials, high-energy equipment, and potentially dangerous processes. Prioritising safety in these environments helps to:
- Protecting researchers and staff: Ensuring the well-being of those working in the laboratory is the primary concern of lab safety. Proper safety measures help prevent accidents, injuries, and long-term health issues that can arise from exposure to harmful substances or dangerous situations.
- Preserve research integrity: Accidents and mishaps in the laboratory can compromise research outcomes, wasting valuable time, resources, and effort. A safe laboratory environment is crucial to the accuracy, reliability, and validity of research findings.
- Comply with legal and ethical requirements: Many countries have established regulations and guidelines to ensure the safety of laboratory workers and the environment. Adhering to these rules helps maintain a safe workspace, avoids legal consequences, and maintains the institution’s reputation.
- Minimise environmental impact: Proper handling and disposal of hazardous materials and waste are crucial in reducing the environmental impact of laboratory activities. Lab safety measures contribute to a more sustainable and eco-friendly research environment.
Purpose of Lab Safety Equipment
Safety equipment serves several crucial functions in the laboratory:
- Personal protection: Personal protective equipment (PPE) shields researchers and staff from direct exposure to hazardous materials, reducing the risk of injury and contamination. Examples include gloves, safety goggles, lab coats, and respirators.
- Preventing accidents: Equipment such as safety shields, fume hoods, and chemical storage cabinets helps minimise the risk of accidents by containing hazardous materials and controlling potential hazards, such as fires or explosions.
- Emergency response: In the event of an accident or emergency, safety equipment such as eyewash stations, safety showers, fire extinguishers, and spill containment kits enables a quick and efficient response, mitigating harm and minimising damage.
- Maintaining a clean and organised workspace: A well-organised laboratory reduces the chances of accidents and contamination. Items such as storage containers, labels, and waste disposal systems play a crucial role in maintaining order and cleanliness in the laboratory.
Overall, lab safety equipment is crucial in creating a secure, efficient, and responsible research environment, thereby protecting both personnel and the integrity of scientific work.
30+ Lab Safety Equipment Every Laboratory Should Have
Every laboratory should have several pieces of laboratory safety equipment to minimise the risk of accidents and ensure the safety of laboratory workers. Here are some of the most important types of lab safety equipment:
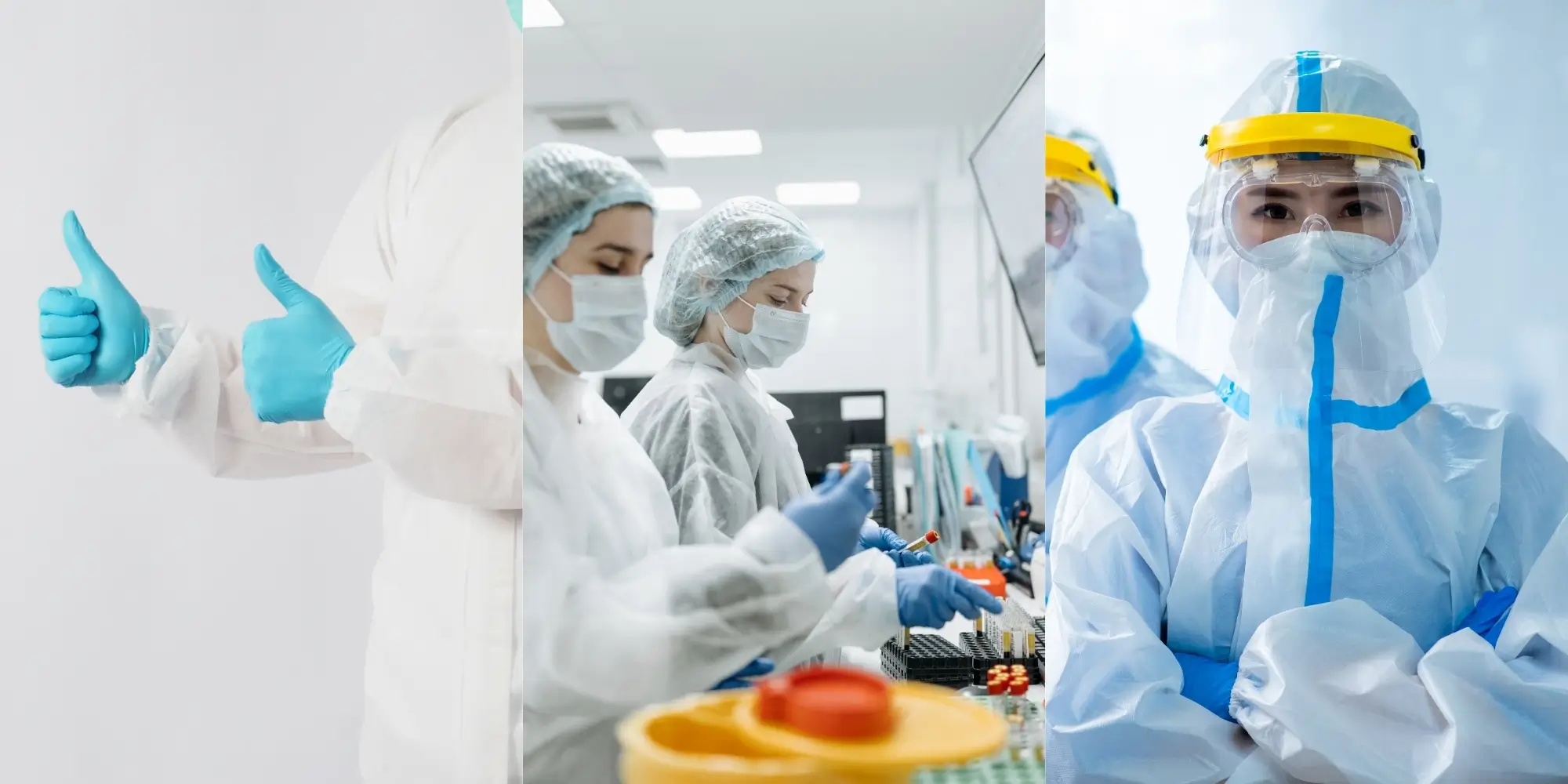
1. Personal Protective Equipment (PPE)
Personal Protective Equipment (PPE) is crucial for laboratory safety, as it helps to protect workers from potential hazards that could cause injury or illness. Some of the essential PPE items that every laboratory should have include the following:
- Safety goggles protect the eyes from chemical splashes, flying debris, and other hazards that could cause eye injuries. It is essential to select goggles that are suitable for the specific hazards present in the laboratory.
- Lab coats: These provide protection for the skin and clothing from chemical spills and splashes. They should be made of a suitable material, such as cotton or polyester, and cover the entire torso and arms.
- Gloves: Various gloves are available for different hazards, including those resistant to chemicals, cuts, and heat. The gloves should be selected based on the specific hazards present in the laboratory.
- Face masks and respirators: These protect the respiratory system from airborne hazards, such as dust, fumes, and vapours. The selection of the appropriate face mask or respirator depends on the specific hazards present in the laboratory.
- Closed-toe shoes: These provide protection for the feet from chemical spills and falling objects. The shoes should be made of a suitable material, such as leather or rubber.
- Hearing protection: In laboratories with loud noises, workers should use earplugs or earmuffs to protect their hearing.
It is essential to note that PPE alone is insufficient to ensure laboratory safety. It’s also essential to follow proper laboratory procedures, such as handling chemicals safely, using equipment correctly, and maintaining a clean and organised workspace. Regular training and communication among lab personnel are critical to maintaining a safe working environment.
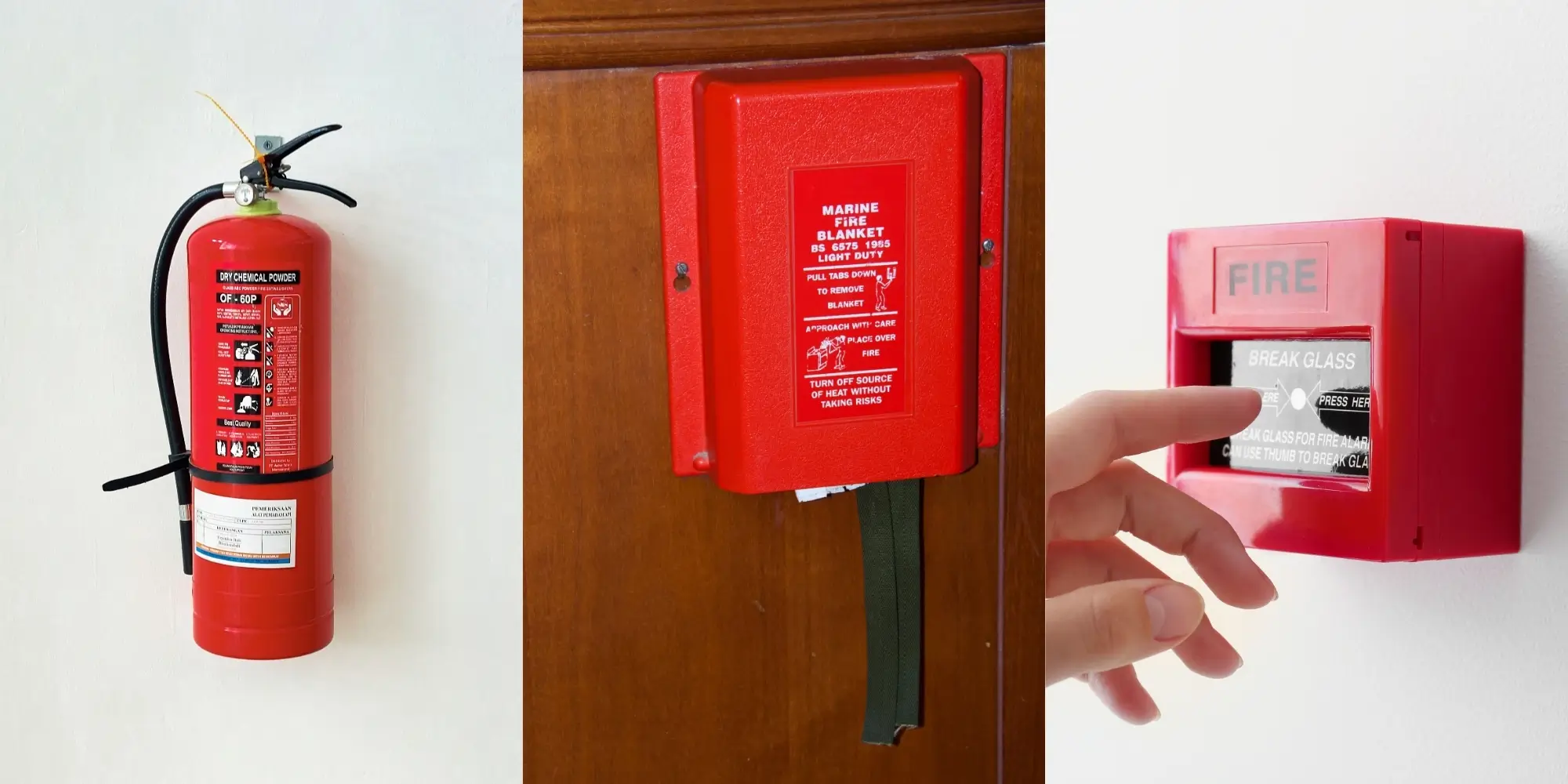
2. Fire Safety Equipment
Fire safety equipment is crucial in any laboratory, as fires can be caused by various hazards, such as electrical equipment, flammable chemicals, or heating sources. The following are some of the essential fire safety equipment that every laboratory should have:
- Fire extinguishers: These are used to extinguish small fires. The fire extinguisher required depends on the type of fire that could occur. For example, Class A extinguishers are used for fires involving ordinary combustibles, while Class C extinguishers are used for fires involving electrical equipment.
- Fire blankets: These are used to smother small fires, particularly those involving clothing or skin. Fire blankets should be made of a suitable material, such as fibreglass, and should be easily accessible in case of an emergency.
- Fire alarm systems are used to alert laboratory personnel in the event of a fire. The alarm should be loud enough to be heard throughout the laboratory, and clear instructions should be provided on what to do in the event of an emergency.
- Emergency exits and signage: There should be clearly marked emergency exits that are easily accessible and unobstructed. The exits should be well-lit and have appropriate signage to direct personnel to safety.
In addition to the above equipment, it is essential to have a fire safety plan that outlines the specific procedures to follow in the event of a fire. The plan should include procedures for evacuating the laboratory, contacting emergency services, and shutting down equipment if necessary. Regular fire drills should be conducted to ensure that all personnel are familiar with emergency procedures and can evacuate the laboratory safely and efficiently in the event of a fire.
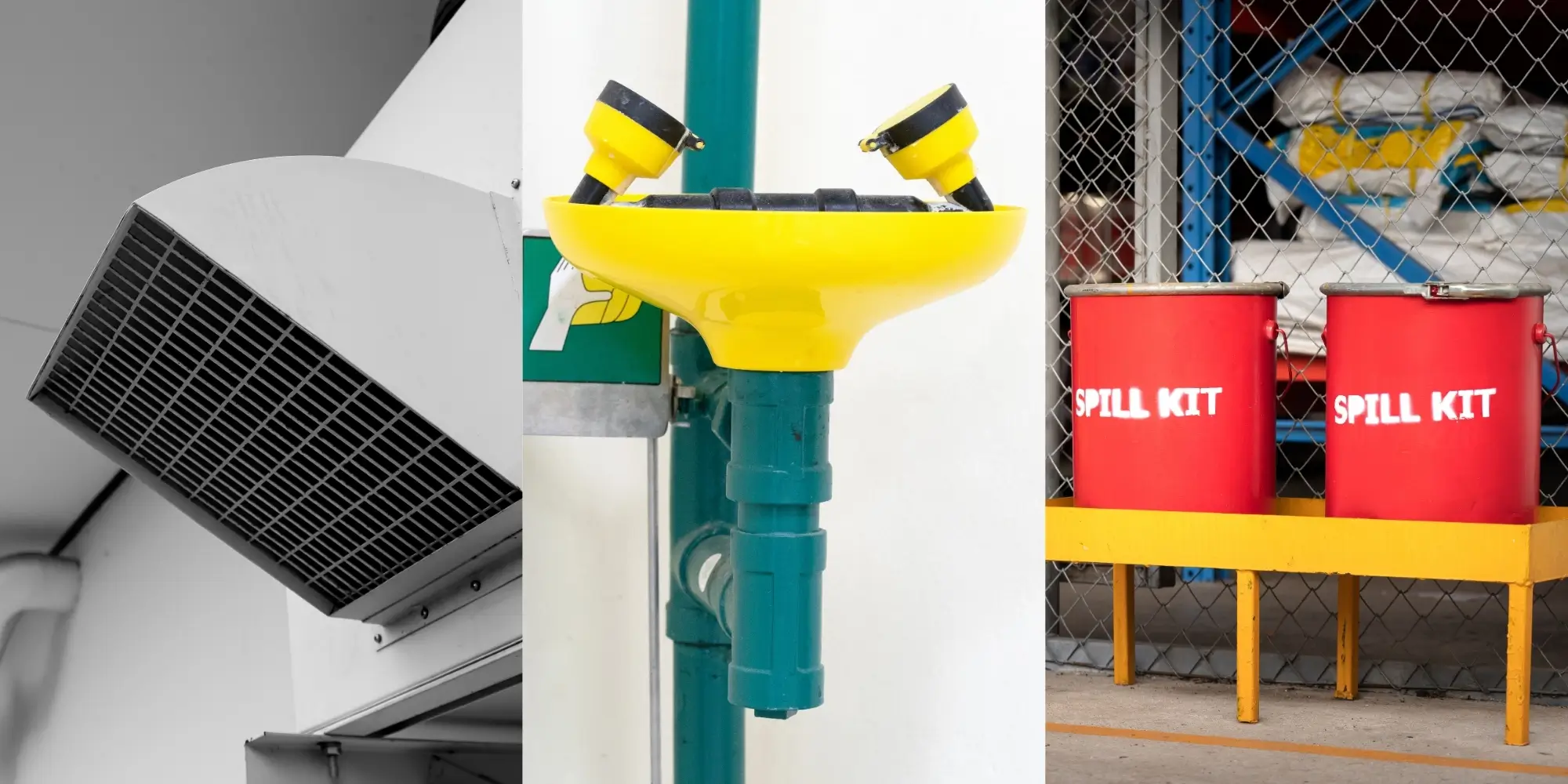
3. Chemical Safety Equipment
Chemical safety equipment is crucial in any laboratory where hazardous substances are present, especially when dealing with various types of chemicals that require different handling and storage measures. The following are some of the essential chemical safety equipment that every laboratory should have:
- Fume hoods and ventilation systems: These are used to remove hazardous chemical fumes and vapours from the laboratory. Fume hoods should be kept free of clutter and used only for their intended purposes. The ventilation system should be properly maintained and tested to ensure it works effectively.
- Chemical storage cabinets: These are used to store hazardous chemicals safely. The cabinets should be made of a suitable material, such as metal, and labelled appropriately to indicate the contents. Chemicals should be stored according to their compatibility and hazard classification.
- Spill kits: These are used to clean up chemical spills. The spill kit should contain absorbent materials, such as vermiculite or sand, and should be easily accessible in case of an emergency. Spill kits should be properly maintained and regularly inspected to ensure they’re ready for use.
- Eyewash stations and safety showers are used to rinse chemicals from the eyes and skin in the event of a chemical splash or spill. They should be located in easily accessible areas and regularly tested to ensure they function properly.
- Labelling of chemicals: All hazardous chemicals must be properly labelled, including the name of the chemical, its hazard classification, and any specific instructions for handling or storage.
It is essential to note that the above equipment is only a part of a comprehensive chemical safety program. Proper handling, storage, and disposal of hazardous chemicals, along with regular training and communication among lab personnel, are essential for maintaining a safe working environment.
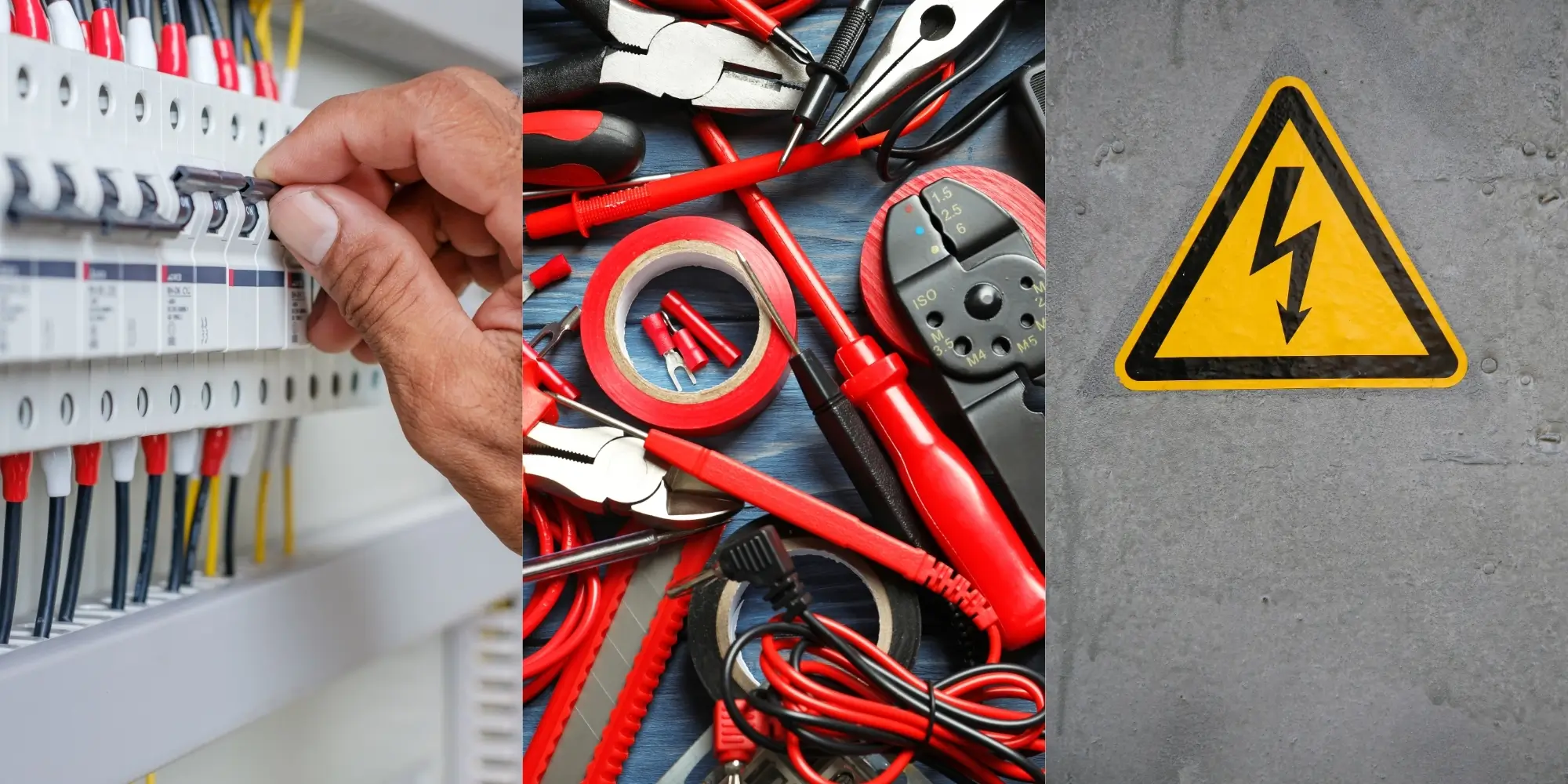
4. Electrical Safety Equipment
Electrical safety equipment is crucial in any laboratory where electrical equipment is used, as electrical hazards can cause serious injury or even death. The following are some of the essential electrical safety equipment that every laboratory should have:
- Ground fault circuit interrupters (GFCI): These are used to protect against electrical shock. GFCI monitor the flow of electricity and shut off power if there’s a ground fault or electrical leakage.
- Circuit breakers: These are used to protect electrical circuits from overload or short-circuiting. Circuit breakers should be properly rated for the equipment they protect and regularly tested to ensure they are functioning properly.
- Insulated tools and equipment: These are used to protect against electrical shock. Tools and equipment should be properly insulated and maintained to prevent electrical leakage.
- Electrical safety signs and labels are used to indicate the location of electrical equipment and to warn personnel of potential electrical hazards.
It is essential to note that electrical safety equipment alone is insufficient to ensure laboratory safety. Proper electrical wiring, grounding, and equipment installation are also crucial for maintaining a safe working environment. Regular inspection and testing of electrical equipment, as well as regular training and communication among lab personnel, are also crucial in promoting electrical safety in the laboratory.
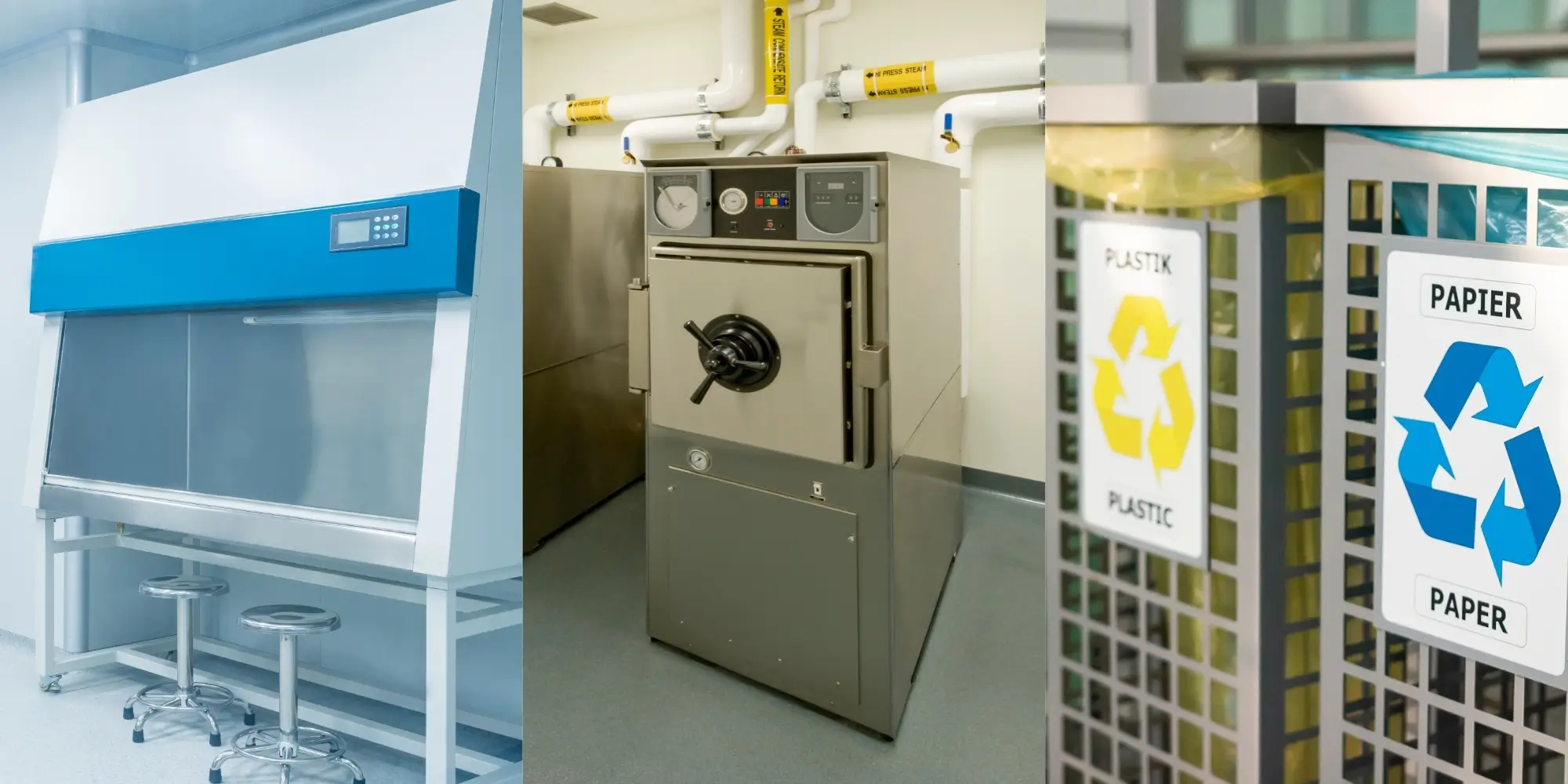
5. Biological Safety Equipment
Biological safety equipment is essential in any laboratory where biological materials are handled or processed, as these materials can pose a risk to both laboratory personnel and the environment. The following are some of the essential biological safety equipment that every laboratory should have:
- Biosafety cabinets: These are used to contain and control the release of biological materials. Biosafety cabinets should be properly maintained and tested to ensure they work effectively.
- Autoclaves: These are used to sterilise biological materials, such as cultures or equipment, before disposal or reuse. Autoclaves should be properly maintained and tested to ensure they work effectively.
- Proper waste disposal systems: Biological waste should be disposed of properly in designated hazardous waste containers, typically after being autoclaved for sterilisation before disposal. Sharps containers should be used to dispose of sharp objects, such as needles or scalpel blades.
It is essential to note that the above equipment is only a part of a comprehensive biological safety program. Proper handling, storage, and disposal of biological materials, along with regular training and communication among lab personnel, are essential for maintaining a safe working environment. Additionally, it is essential to follow appropriate biosafety guidelines, such as those established by the Centres for Disease Control and Prevention (CDC), to prevent the spread of infectious agents or other biological hazards.
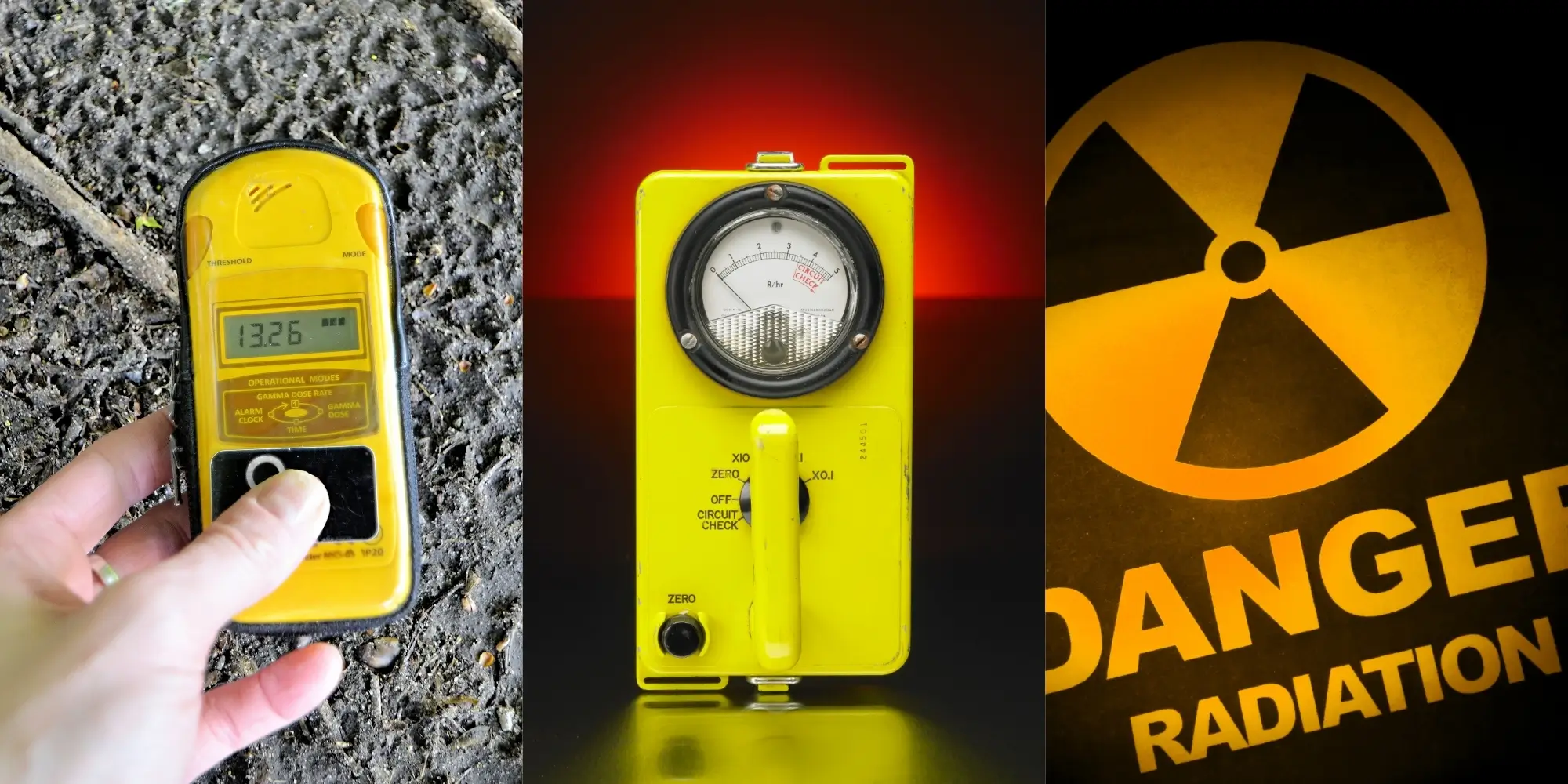
6. Radiation Safety Equipment
Radiation safety equipment is crucial in any laboratory where radiation sources are used or handled, as exposure to radiation can cause serious injury or even death. The following are some of the essential radiation safety equipment that every laboratory should have:
- Lead shielding: This is used to block radiation and protect personnel from exposure. Lead shielding should be properly designed and installed to ensure effectiveness.
- Geiger counters: These are used to detect the presence and intensity of radiation. Geiger counters should be calibrated and regularly tested to ensure they work properly.
- Dosimeters: These are used to measure the radiation exposure personnel have received. Dosimeters should be worn by personnel working with radiation sources and should be regularly checked to ensure they are functioning properly.
- Radiation warning signs and labels: These are used to indicate the presence of radiation sources and to warn personnel of potential radiation hazards.
It is essential to recognise that radiation safety equipment alone is insufficient to ensure laboratory safety. Proper handling, storage, and disposal of radioactive materials, as well as regular training and communication among lab personnel, are also crucial for maintaining a safe working environment. Additionally, it is essential to follow appropriate radiation safety guidelines, such as those established by the Nuclear Regulatory Commission (NRC), to prevent exposure to ionising radiation.
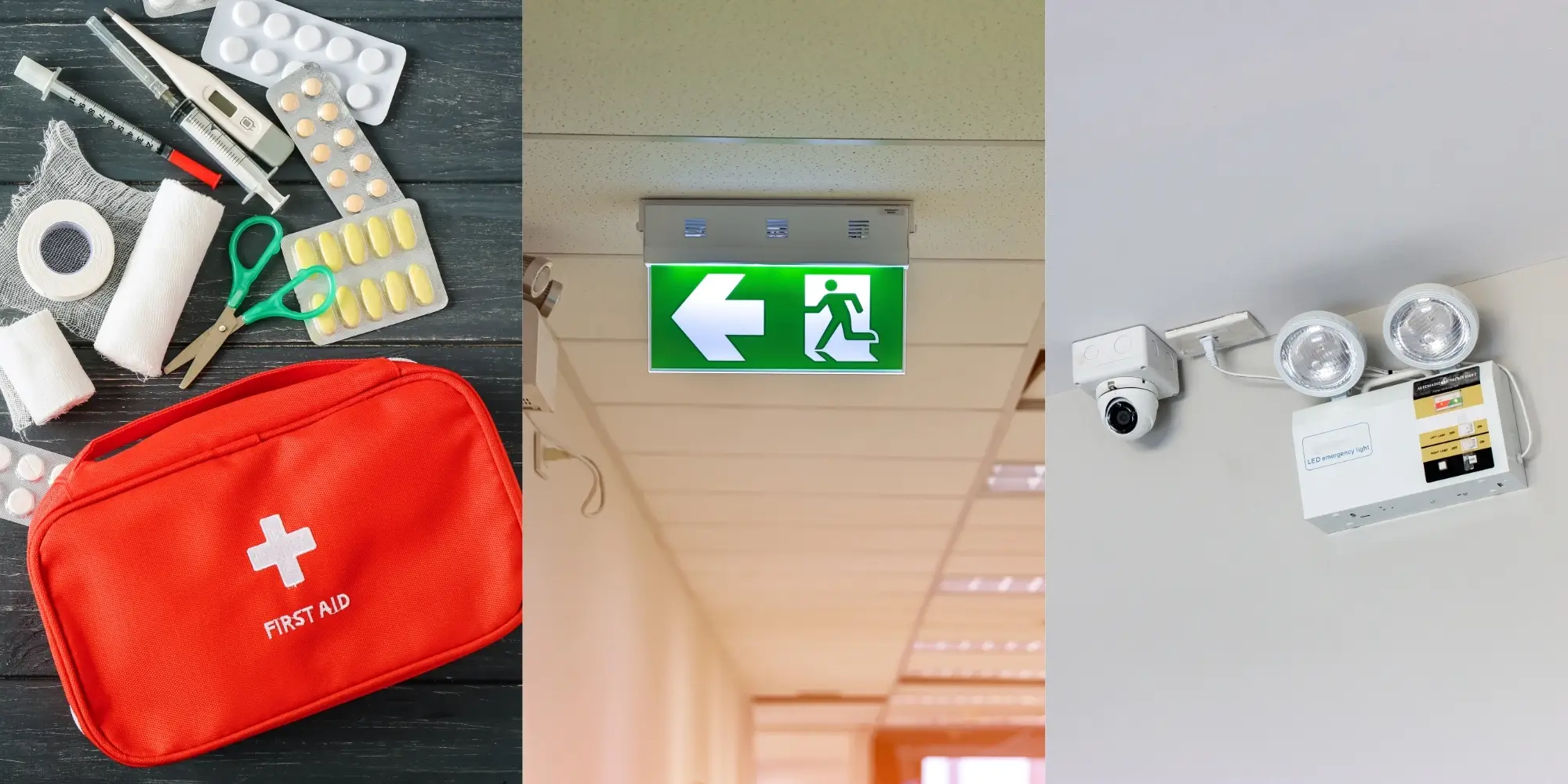
7. Emergency Response Equipment
Emergency response equipment is crucial in any laboratory, as accidents or incidents can occur at any time. The following are some of the essential emergency response equipment that every laboratory should have:
- First aid kits should be easily accessible and stocked with appropriate supplies, including bandages, antiseptics, and other essential first-aid items.
- Emergency eyewash stations and safety showers should be located in easily accessible areas and tested regularly to ensure they are functioning properly. They should be able to deliver a sufficient water flow for at least 15 minutes.
- Emergency escape equipment includes ladders, ropes, and harnesses that can be used to evacuate the laboratory in the event of an emergency. They should be easily accessible and regularly inspected to ensure they’re in good condition.
- Emergency lighting and signage are used to indicate the location of emergency exits and escape routes, as well as to provide adequate lighting in the event of a power outage.
It is essential to note that emergency response equipment alone is insufficient to ensure laboratory safety. A comprehensive emergency response plan should also be in place, outlining the specific procedures to follow in the event of an emergency. The plan should include procedures for evacuating the laboratory, contacting emergency services, and providing first aid or other necessary medical treatment.
Regular training and communication among lab personnel are also crucial for ensuring that everyone is aware of the emergency response procedures and can respond appropriately in the event of an emergency.
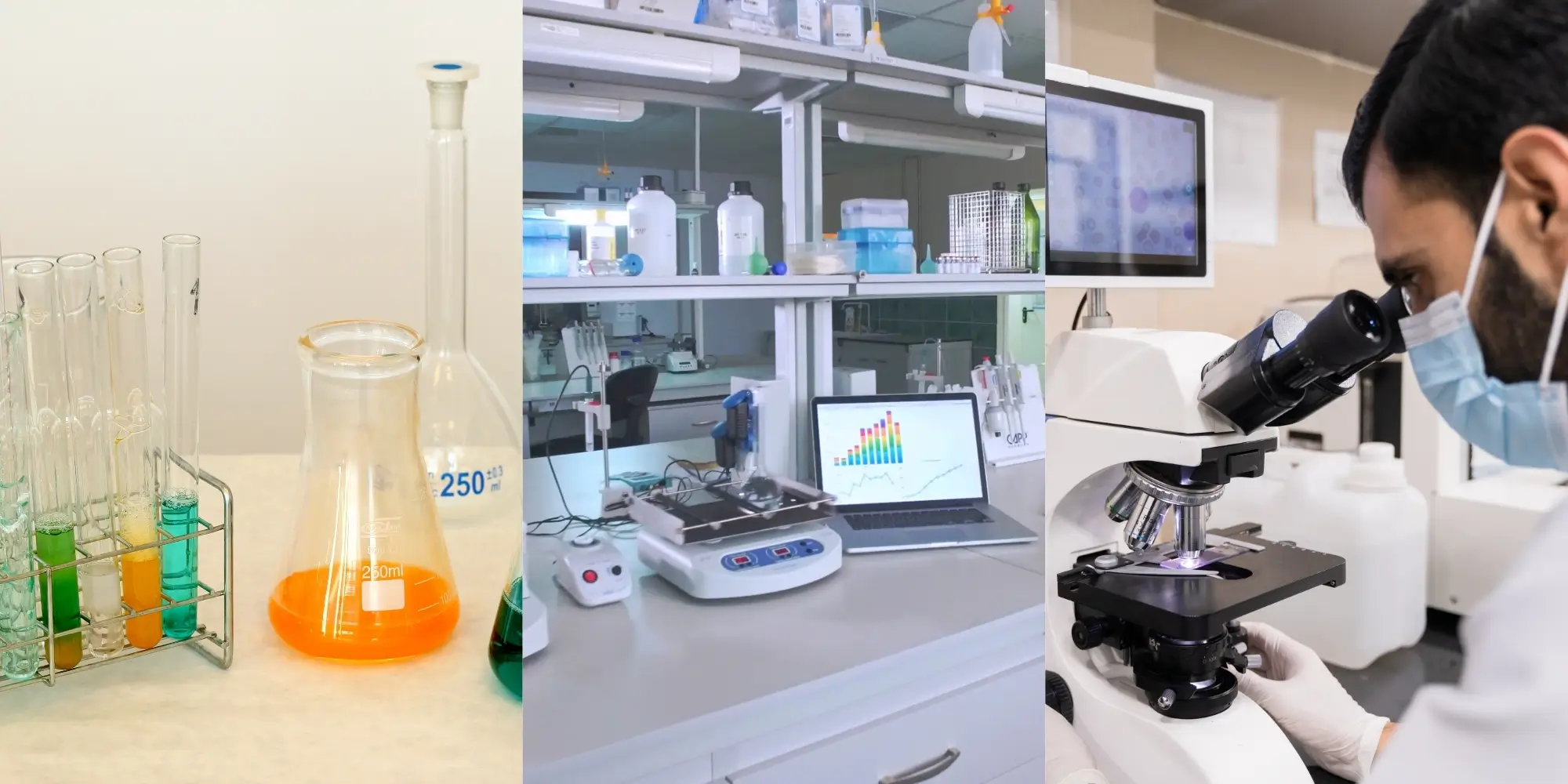
8. General Laboratory Safety Equipment
General laboratory safety equipment is crucial in any laboratory to ensure a safe work environment for all personnel. The following are some of the essential general laboratory safety equipment that every laboratory should have:
- Slip-resistant flooring is essential in preventing slips, trips, and falls, which can lead to serious injuries. The flooring should be slip-resistant, and spills should be cleaned up immediately.
- Proper storage systems are necessary to keep the laboratory organised and clutter-free. All equipment and materials should be stored in designated locations, and flammable materials should be kept away from ignition sources.
- Well-maintained and regularly inspected equipment: All laboratory equipment should be properly maintained and regularly inspected to ensure it’s in good working condition. Any equipment that’s damaged or malfunctioning should be repaired or replaced immediately.
- Safety signs and labels: Safety signs and labels should be placed in appropriate locations throughout the laboratory to indicate potential hazards and to provide instructions on safe handling procedures.
- Laboratory Safety Manuals and Training: All laboratory personnel should receive regular safety training, and a laboratory safety manual should be readily available for reference. The manual should outline the specific hazards present in the laboratory and the procedures for handling them.
It is essential to note that the above equipment is only a part of a comprehensive laboratory safety program. Regular training and communication among lab personnel, along with proper hazard identification and risk assessment, are crucial for maintaining a safe working environment. Additionally, ongoing evaluation and improvement of the laboratory safety program is necessary to ensure it remains effective over time.
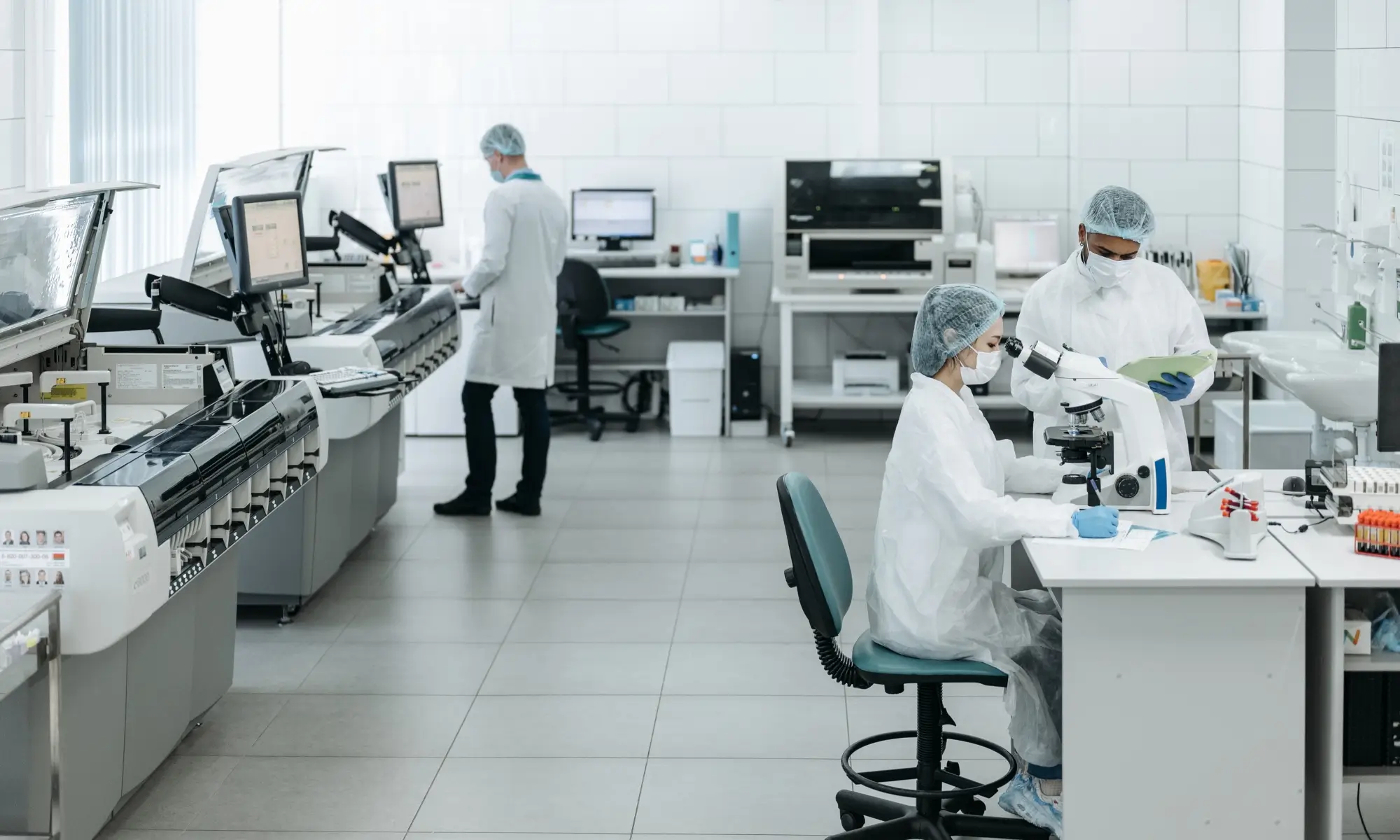
Regular Maintenance and Inspections Of Lab Safety Equipment
Regular maintenance and inspections are essential to ensure that laboratory equipment and safety systems function properly and that the work environment remains safe for all personnel. The following are some of the key considerations for regular maintenance and inspections:
- The importance of regular maintenance: Regular maintenance is crucial to ensure that equipment is in good working condition and to prevent breakdowns or malfunctions that could lead to accidents or incidents.
- Routine inspection procedures: Inspection should be conducted on equipment, safety systems, and the work environment to identify potential hazards or problems. Inspection procedures should be well-documented and should include specific checklists or protocols.
- Record-keeping and documentation: Records of all maintenance and inspection activities should be kept, including any repairs or replacements. This information can be used to identify patterns or trends in equipment performance and improve the laboratory safety program.
It is essential to note that regular maintenance and inspections should be conducted by qualified personnel trained to identify potential hazards and make necessary repairs or replacements. Maintenance and inspections should also be conducted in accordance with the manufacturer’s specifications and applicable regulations or guidelines.
Regular training and communication among lab personnel are also crucial for ensuring that everyone understands the importance of regular maintenance and inspections and is committed to maintaining a safe working environment.
Conclusion
Laboratory safety is not optional—it is essential. Equipping your lab with the right safety equipment, maintaining it properly, and ensuring all personnel are trained in its use are critical steps in protecting lives, preserving research integrity, and meeting legal and ethical standards. From personal protective gear to emergency response tools, every piece of equipment plays a vital role in minimising risks and promoting a safe, productive environment. By making safety a daily priority and fostering a strong safety culture, laboratories can support innovation while ensuring the safety of everyone involved.