Workplace safety is of paramount importance for any organization, as it not only ensures the well-being of employees but also contributes to overall productivity and efficiency. While proactive safety measures aim to prevent accidents and incidents from occurring in the first place, reactive monitoring methods focus on learning from events that have already taken place to prevent recurrence and improve safety practices.
In this blog, we will explore 15 different types of reactive monitoring methods that can help organizations identify potential hazards, uncover root causes, and implement effective corrective actions to enhance workplace safety. By understanding and employing these methods, businesses can create a safer work environment, reduce the risk of accidents and injuries, and demonstrate a strong commitment to employee well-being.
15 Different Types Of Reactive Monitoring Methods
Reactive monitoring refers to the process of reviewing and analyzing incidents, accidents, or near-misses that have already occurred in a workplace to identify potential hazards, determine root causes, and implement corrective actions. The primary goal of reactive monitoring is to learn from these events and improve safety practices to prevent similar occurrences in the future.
Here are 15 different types of reactive monitoring methods:
1. Analysing Trends of Accidents
This method begins with systematically collecting data on workplace accidents, including details such as the type of accident, location, time, equipment involved, and any contributing factors. This information should be recorded and maintained in a centralized database for easy access and analysis.
Once sufficient data is gathered, organizations can analyze the data to identify patterns or trends. This may involve examining the frequency of accidents, common contributing factors, or correlations between specific variables (e.g., accidents occurring more frequently during certain shifts or with specific equipment).
Statistical analysis tools can provide deeper insights into the data, such as identifying seasonal fluctuations, potential outliers, or emerging patterns. Visualization techniques, like graphs and charts, can also help understand the trends more easily.
By understanding these trends, organizations can develop targeted strategies to address the root causes of accidents. For example, suppose data analysis reveals that many accidents occur due to a lack of training or inadequate safety equipment. In that case, the organization can prioritize investments in training programs or equipment upgrades.
Moreover, analyzing accident trends can also help set safety performance goals and evaluate the effectiveness of existing safety policies and procedures. Regularly reviewing and updating the analysis ensures that organizations can continually adapt and improve their safety measures based on the latest data.
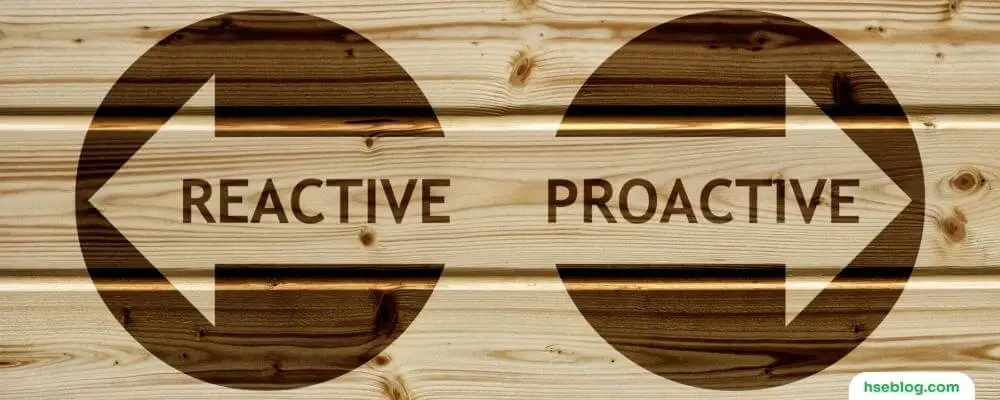
2. Analysing Patterns of Accidents
This method aims to identify shared features or characteristics among various accidents, which can provide valuable insights into the underlying issues that contribute to these incidents. This analysis can be broken down into several steps:
- Data Collection: Gather detailed information on each accident, including factors such as location, time, equipment involved, personnel involved, and any contributing factors. This data should be recorded in a centralized database to facilitate analysis.
- Categorization: Organize the collected data into categories, such as types of accidents (e.g., slips, trips, and falls), locations (e.g., specific work areas or departments), and equipment or processes involved. This categorization helps to group similar accidents together for further analysis.
- Identification of Common Characteristics: Examine each category to identify shared features among the accidents. These commonalities could include similar equipment failures, environmental factors, human behaviors, or procedural deficiencies.
- Analysis of Contributing Factors: Investigate the factors contributing to the identified patterns. This might involve looking at training and competence levels, equipment maintenance and inspection, workplace layout, or communication issues.
- Development of Targeted Solutions: Based on the analysis, develop appropriate measures to address the identified patterns. This may involve implementing new training programs, modifying equipment or processes, enhancing communication channels, or improving workplace layout and design.
- Monitoring and Evaluation: Continuously monitor the effectiveness of the implemented solutions and evaluate their impact on reducing accident occurrences. Adjustments to the solutions may be necessary to achieve optimal results.
By pinpointing accident patterns and addressing the underlying issues, companies can create a safer work environment and reduce the likelihood of future accidents. This proactive approach to accident analysis can help organizations minimize risks, lower costs associated with accidents, and enhance overall workplace safety.
3. Analysis of Worker’s Complaints in Committee Meetings
This method acknowledges the importance of employee input in identifying and addressing safety concerns within the workplace. Workers often have firsthand knowledge of potential hazards and can provide valuable insights into areas that require improvement. The process of analyzing worker’s complaints in committee meetings involves the following steps:
- Encouraging Open Communication: Create an environment where employees feel comfortable sharing their concerns and complaints without fear of retaliation or negative consequences. This may involve establishing anonymous reporting channels or ensuring that safety committee meetings are open and welcoming forums for discussion.
- Documentation: Record and maintain a comprehensive log of all worker’s complaints and concerns raised during safety committee meetings. This documentation should include details such as the date, description of the concern, and the person or department responsible for addressing the issue.
- Categorization and Prioritization: Organize the collected complaints into categories based on the nature of the concern (e.g., equipment-related, procedural, environmental). Prioritize the complaints based on factors such as severity, potential impact on safety, and feasibility of addressing the issue.
- Investigation and Analysis: Investigate each complaint to determine its validity and the underlying factors contributing to the concern. This may involve conducting workplace inspections, interviewing employees, or reviewing relevant documentation.
- Development and Implementation of Solutions: Based on the investigation and analysis, develop appropriate solutions to address the identified concerns. These solutions may involve updating safety policies, improving training programs, or modifying equipment or processes.
- Follow-up and Feedback: Communicate the results of the investigation and the implemented solutions to the employees who raised the concerns. Provide regular updates on addressing the complaints and solicit feedback to ensure the solutions effectively resolve the issues.
- Continuous Improvement: Regularly review and analyze workers’ complaints to identify emerging trends and potential areas for improvement. This process should be integrated into the organization’s overall safety management system to ensure continuous improvement of workplace safety.
By addressing worker’s complaints in committee meetings, organizations can proactively address potential hazards, enhance employee engagement in safety initiatives, and ultimately improve workplace safety.
4. Meetings After Receiving Enforcement Notices
When companies receive enforcement notices from regulatory authorities, it is crucial to address the identified violations promptly and thoroughly. Holding meetings after receiving such notices serves as an effective way to ensure compliance and improve workplace safety. The process can be broken down into the following steps:
- Distribute Enforcement Notice Information: Share the enforcement notice details with relevant personnel, including management, supervisors, and affected employees. This ensures that all relevant parties are aware of the issue and can contribute to the discussion during the meeting.
- Schedule a Meeting: Meet with key stakeholders, such as management, safety officers, supervisors, and affected employees. After receiving the enforcement notice, the meeting should be scheduled as soon as possible to ensure timely action.
- Review the Enforcement Notice: Begin the meeting by reviewing the enforcement notice in detail, discussing the specific violations, potential causes, and the regulatory requirements that were not met.
- Analyze the Root Causes: Conduct a thorough analysis to determine the underlying factors that led to the violations. This may involve examining workplace processes, equipment, training programs, or management practices.
- Develop Corrective Actions: Based on the root cause analysis, develop a plan for corrective actions to address the identified violations. This may include updating safety procedures, providing additional training, or making changes to the work environment.
- Establish a Timeline and Assign Responsibilities: Create a timeline for implementing the corrective actions and assign specific responsibilities to relevant personnel. This helps ensure that the required actions are completed in a timely manner and that everyone involved is held accountable.
- Monitor Progress: Regularly monitor the progress of the corrective actions and provide updates to all relevant parties. This helps ensure that the actions are being implemented effectively and that any challenges or issues that arise are addressed promptly.
- Evaluate Effectiveness: Once the corrective actions have been completed, evaluate their effectiveness in addressing the violations and improving workplace safety. This may involve conducting workplace inspections, reviewing safety records, or soliciting feedback from employees.
- Develop Preventative Strategies: Based on the lessons learned from the enforcement notice and the corrective actions, develop strategies to prevent similar occurrences. This may include updating safety policies, enhancing training programs, or improving communication channels.
By conducting meetings after receiving enforcement notices, companies can effectively address violations, implement corrective actions, and develop strategies to prevent future occurrences, ultimately improving workplace safety and compliance with regulatory requirements.
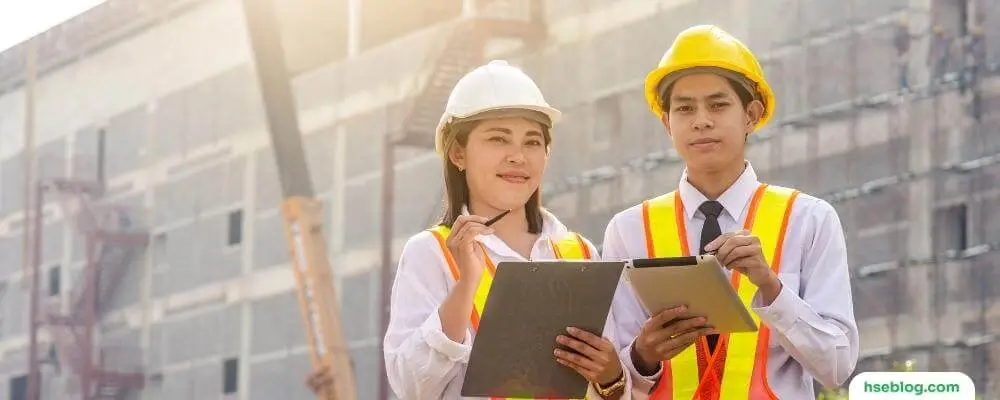
5. Incident Investigations
Incident investigations are a crucial part of an organization’s safety management system. These investigations help identify the underlying causes of accidents or incidents and develop appropriate measures to prevent future occurrences. A comprehensive incident investigation process includes the following steps:
- Immediate Response: As soon as an incident occurs, ensure that any injured individuals receive medical attention and secure the scene to prevent further harm.
- Gather Information: Collect as much information as possible about the incident, including photographs of the scene, witness statements, and any relevant documentation (e.g., maintenance logs, safety procedures, or training records).
- Assemble an Investigation Team: Form a team of individuals with relevant expertise, such as safety officers, supervisors, and technical experts, to investigate the incident. The team should be unbiased and focused on determining the root causes of the incident.
- Interview Witnesses: Conduct interviews with individuals who witnessed the incident or were involved in it. Ask open-ended questions and encourage witnesses to provide as much detail as possible. Record all witness statements for future reference.
- Examine the Scene: Inspect the accident scene and any equipment or materials involved in the incident. Look for any signs of damage, wear, or malfunction that could have contributed to the incident.
- Analyze Information: Review all collected information, including witness statements, photographs, and documentation, to identify possible contributing factors and root causes. Consider human factors, equipment issues, environmental conditions, and procedural deficiencies.
- Identify Root Causes: Determine the underlying causes of the incident, focusing on systemic issues rather than individual mistakes. Root causes may include inadequate training, poor communication, equipment malfunction, or procedural failures.
- Develop Corrective Actions: Based on the root cause analysis, develop and implement corrective actions to address the identified issues and prevent recurrence. These actions may include revising safety procedures, updating training programs, repairing or replacing equipment, or improving communication channels.
- Communicate Findings: Share the investigation findings and corrective actions with relevant personnel, including management, supervisors, and affected employees. This helps to raise awareness of the incident, promote learning, and reinforce the organization’s commitment to safety.
- Monitor and Evaluate: Continuously monitor the effectiveness of the corrective actions and evaluate their impact on preventing similar incidents in the future. Adjust the corrective actions as necessary to achieve the desired results.
By conducting thorough incident investigations, organizations can gain a deeper understanding of the factors that contribute to accidents or incidents and implement effective solutions to prevent their recurrence, ultimately improving workplace safety.
6. Root Cause Analysis
Root cause analysis (RCA) is a problem-solving technique that aims to identify the fundamental reasons behind accidents, incidents, or failures in an organization. By understanding and addressing the root causes, organizations can implement lasting solutions that prevent similar issues from recurring. The process typically involves the following steps:
- Define the Problem: Clearly state the problem or incident that occurred. This includes describing the event, the consequences, and the specific aspects that require investigation.
- Gather Data: Collect all relevant information related to the incident, such as incident reports, witness statements, photographs, equipment maintenance logs, and any other pertinent documentation.
- Analyze the Data: Review the collected data to identify possible contributing factors, including human factors, equipment failures, environmental conditions, and procedural deficiencies. Look for patterns and trends that may indicate systemic issues.
- Identify Possible Causes: Develop a list of potential causes for the incident based on the data analysis. Consider all plausible explanations, even those that may seem unlikely at first glance.
- Determine Root Causes: Using a systematic approach, such as the “5 Whys” technique or a cause-and-effect diagram (also known as a fishbone diagram or Ishikawa diagram), investigate each potential cause to determine the root causes of the incident. Root causes are the underlying issues that, if addressed, will prevent the problem from recurring.
- Develop Corrective Actions: Based on the identified root causes, develop targeted corrective actions to address the underlying issues. These actions may involve updating safety procedures, improving training programs, modifying equipment or processes, or enhancing communication and reporting systems.
- Implement Corrective Actions: Put the corrective actions into practice, ensuring that all relevant personnel are informed and trained as necessary. Monitor the implementation process to ensure that the actions are carried out effectively.
- Evaluate the Effectiveness: Regularly assess the effectiveness of the implemented corrective actions in preventing similar incidents from occurring. This may involve tracking incident rates, conducting audits, or soliciting feedback from employees. Adjust the corrective actions as necessary to achieve optimal results.
- Document and Communicate Findings: Record the findings of the root cause analysis, including the identified root causes and corrective actions. Share this information with relevant personnel to promote learning and awareness and to demonstrate the organization’s commitment to continuous improvement.
By conducting a root cause analysis, organizations can address the underlying issues that contribute to accidents or incidents rather than merely treating the symptoms. This approach leads to more effective long-term solutions and promotes a safer work environment.
7. Near-miss Reporting and Analysis
Near-miss incidents, sometimes called close calls, are situations where an accident could have occurred but was averted, often due to chance or quick action by the individuals involved. Analyzing these events is a proactive approach to improving workplace safety, as it allows organizations to identify potential hazards and implement corrective actions before an actual accident takes place. The process involves the following steps:
- Encourage Reporting: Create a culture where employees feel comfortable reporting near-miss incidents without fear of punishment or negative consequences. Make the reporting process simple and accessible, and consider establishing anonymous reporting channels.
- Document Near-miss Incidents: Record and maintain a log of all near-miss incidents, including details such as date, location, individuals involved, description of the event, and any contributing factors. This information should be stored in a centralized database for easy access and analysis.
- Categorize and Prioritize: Organize the near-miss incidents into categories based on factors such as type of hazard, location, and potential severity. Prioritize incidents that pose the greatest risk or have the highest potential for serious consequences.
- Investigate Near-miss Incidents: Conduct thorough investigations of reported near-miss incidents, examining factors such as equipment, processes, environmental conditions, and human behavior. Look for patterns or trends that may indicate underlying issues.
- Identify Root Causes: Determine the underlying causes of the near-miss incidents by using root cause analysis techniques, such as the “5 Whys” or fishbone diagrams. This helps to pinpoint systemic issues that need to be addressed.
- Develop and Implement Preventative Measures: Based on the root cause analysis, develop targeted solutions to address the identified issues and prevent future near-miss incidents or accidents. These measures may include updating safety policies, enhancing training programs, modifying equipment or processes, or improving communication channels.
- Monitor and Evaluate: Continuously monitor the effectiveness of the implemented preventative measures and evaluate their impact on reducing near-miss incidents and accidents. Adjust the measures as necessary to achieve optimal results.
- Share Lessons Learned: Communicate the findings from near-miss reporting and analysis to all relevant personnel, highlighting the importance of reporting and the value of learning from these incidents. This helps to reinforce the organization’s commitment to safety and encourages continued reporting of near-miss incidents.
By analyzing near-miss reports, organizations can proactively identify potential hazards and implement preventative measures before an accident occurs, ultimately creating a safer work environment and reducing the risk of accidents.

8. Post-accident Employee’s Suggestions and Recommendations
Involving employees in the aftermath of an accident is crucial for identifying areas of improvement and fostering a sense of ownership over workplace safety. Employees often have firsthand knowledge of the work environment, equipment, and processes and can provide valuable suggestions and recommendations for preventing similar incidents. The process of obtaining and implementing employee suggestions and recommendations involves the following steps:
- Encourage Open Communication: Create a culture where employees feel comfortable sharing their thoughts, suggestions, and recommendations after an accident. Assure them that their input is valued and that they will not face negative consequences for speaking up.
- Collect Employee Feedback: Provide channels for employees to share their suggestions and recommendations after an accident. This can be done through anonymous reporting systems, suggestion boxes, or open forums where employees can discuss their ideas.
- Review and Categorize Suggestions: Review all employee suggestions and recommendations, organizing them into categories based on their focus, such as equipment, training, communication, or procedures. This helps to identify areas that require improvement and prioritize actions.
- Evaluate Feasibility: Assess the feasibility of implementing the suggested changes, taking into consideration factors such as cost, time, and potential impact on workplace safety. Some suggestions may require further investigation or analysis before being implemented.
- Develop and Implement Solutions: Based on the employee suggestions and recommendations, develop appropriate solutions to address the identified issues. This may involve updating safety policies, enhancing training programs, modifying equipment or processes, or improving communication channels.
- Communicate and Involve Employees: Keep employees informed about the progress of implementing their suggestions and recommendations. Involve them in the development and implementation process, as this can help to ensure the changes are effective and sustainable.
- Monitor and Evaluate: Continuously monitor the effectiveness of the implemented changes and evaluate their impact on preventing similar accidents in the future. Adjust the solutions as necessary to achieve optimal results.
- Recognize and Reward Employee Contributions: Acknowledge and reward employees for their contributions to improving workplace safety. This can be done through formal recognition programs, informal praise, or tangible rewards, such as bonuses or gift cards.
By encouraging post-accident employee suggestions and recommendations, organizations can tap into the valuable insights of their workforce, leading to more effective safety practices and a safer work environment.
9. Examination of Equipment Failure and Maintenance Records
Equipment failure can be a significant contributor to workplace accidents. By regularly reviewing equipment failure and maintenance records, organizations can identify trends, potential issues, and areas for improvement, ultimately reducing the risk of accidents and enhancing workplace safety. The process involves the following steps:
- Establish a Record-keeping System: Implement a standardized record-keeping system for equipment failure and maintenance activities. Ensure that all relevant personnel are trained on the system and understand the importance of accurate and timely documentation.
- Collect and Organize Data: Gather data from equipment failure and maintenance records, including information on the type and frequency of failures, maintenance activities performed, and any identified issues or concerns.
- Analyze Data and Identify Trends: Analyze the collected data to identify trends or patterns, such as specific equipment types with a high rate of failure, recurring issues, or maintenance tasks that are frequently performed. Look for correlations between equipment failures and other factors, such as age, usage, or environmental conditions.
- Investigate Root Causes: Conduct a root cause analysis of identified trends or issues to determine the underlying factors contributing to equipment failure. This may involve examining equipment design, maintenance procedures, or operator training and performance.
- Develop and Implement Corrective Actions: Based on the root cause analysis, develop targeted corrective actions to address the identified issues and prevent future equipment failures. These actions may include updating maintenance procedures, improving operator training, replacing aging equipment, or modifying equipment design.
- Monitor and Evaluate: Continuously monitor the effectiveness of the implemented corrective actions and evaluate their impact on reducing equipment failure and related accidents. Adjust the corrective actions as necessary to achieve optimal results.
- Communicate Findings and Lessons Learned: Share the findings from the examination of equipment failure and maintenance records with relevant personnel. This helps to raise awareness of the issues and promote a culture of continuous improvement.
- Schedule Regular Reviews: Establish a schedule for regularly reviewing equipment failure and maintenance records, ensuring that the process is ongoing and proactive. This helps to identify and address potential issues before they lead to accidents.
By regularly examining equipment failure and maintenance records, organizations can proactively identify and address potential issues, ultimately reducing the risk of accidents and improving workplace safety.
10. Review of Safety Data Sheets (SDS) After Hazardous Material Incident
Safety Data Sheets (SDS) contain important information about hazardous materials, including their properties, potential hazards, safe handling procedures, and emergency response measures. After a hazardous material incident, reviewing the associated SDS can provide valuable insights into the cause of the incident and help identify areas for improvement. The process involves the following steps:
- Obtain the Relevant SDS: After a hazardous material incident, obtain the SDS for the involved substance(s). Ensure that the SDS is up-to-date and complies with the applicable regulations.
- Review the SDS: Carefully review the SDS, paying close attention to sections that may be relevant to the incident, such as hazard identification, first-aid measures, fire-fighting measures, accidental release measures, handling and storage, exposure controls and personal protection, and disposal considerations.
- Identify Potential Issues: Based on the SDS review, identify any potential issues or discrepancies that may have contributed to the hazardous material incident. This could include improper handling procedures, inadequate storage conditions, or failure to follow recommended personal protective equipment (PPE) guidelines.
- Investigate Root Causes: Conduct a root cause analysis to determine the underlying factors that led to the hazardous material incident. Consider whether inadequate training, insufficient communication, procedural failures, or other factors contributed to the issues identified in the SDS review.
- Develop and Implement Corrective Actions: Based on the root cause analysis, develop targeted corrective actions to address the identified issues and prevent future hazardous material incidents. These actions may include updating safety procedures, enhancing employee training, improving storage facilities, or modifying disposal practices.
- Update SDS and Procedures: If the review of the SDS reveals inaccuracies or outdated information, update the SDS as necessary and ensure that all relevant personnel are informed of the changes. Additionally, update internal procedures and guidelines to reflect the lessons learned from the incident.
- Monitor and Evaluate: Continuously monitor the effectiveness of the implemented corrective actions and evaluate their impact on preventing future hazardous material incidents. Adjust the corrective actions as necessary to achieve optimal results.
- Communicate Findings and Lessons Learned: Share the findings from the SDS review and the hazardous material incident with relevant personnel. This helps to raise awareness of the issues, promote learning, and reinforce the organization’s commitment to safety.
By reviewing Safety Data Sheets (SDS) after a hazardous material incident, organizations can identify potential issues with handling, storage, or disposal and implement corrective actions to prevent similar incidents in the future. This proactive approach can help improve overall workplace safety and reduce the risk of accidents involving hazardous materials.
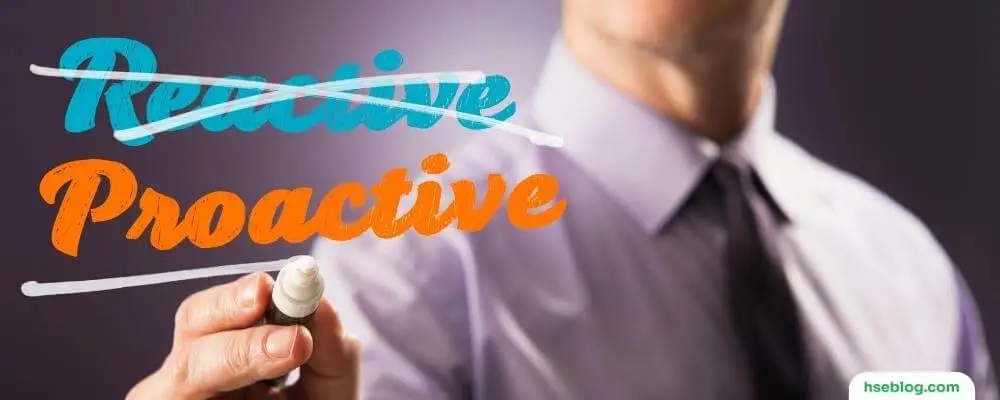
11. Assessment of First Aid Logs and Injury Records
Regularly reviewing first aid logs and injury records can provide valuable insights into the overall safety of a workplace. By identifying trends and patterns in minor injuries, organizations can address potential safety concerns before they escalate into more serious incidents. The process involves the following steps:
- Establish a Record-keeping System: Implement a standardized system for documenting first aid treatments and minor injuries. Ensure that all relevant personnel are trained on the system and understand the importance of accurate and timely documentation.
- Collect and Organize Data: Gather data from first aid logs and injury records, including information on the type and frequency of injuries, the circumstances surrounding each incident, and any identified contributing factors.
- Analyze Data and Identify Trends: Analyze the collected data to identify trends or patterns, such as specific types of injuries that occur frequently, locations with a high rate of incidents, or activities that are commonly associated with injuries. Look for correlations between injuries and other factors, such as equipment, processes, or environmental conditions.
- Investigate Root Causes: Conduct a root cause analysis of identified trends or issues to determine the underlying factors contributing to the injuries. This may involve examining safety procedures, equipment, or training programs.
- Develop and Implement Corrective Actions: Based on the root cause analysis, develop targeted corrective actions to address the identified issues and prevent future injuries. These actions may include updating safety policies, enhancing training programs, modifying equipment or processes, or improving workplace conditions.
- Monitor and Evaluate: Continuously monitor the effectiveness of the implemented corrective actions and evaluate their impact on reducing minor injuries and improving workplace safety. Adjust the corrective actions as necessary to achieve optimal results.
- Communicate Findings and Lessons Learned: Share the findings from the assessment of first aid logs and injury records with relevant personnel. This helps to raise awareness of the issues, promote learning, and reinforce the organization’s commitment to safety.
- Schedule Regular Reviews: Establish a schedule for regularly reviewing first aid logs and injury records, ensuring that the process is ongoing and proactive. This helps to identify and address potential safety concerns before they lead to more serious incidents.
By examining first aid logs and injury records, organizations can proactively identify trends in minor injuries and implement corrective actions to address underlying safety concerns, ultimately creating a safer work environment and reducing the risk of more serious accidents.
12. Evaluation of Post-incident Stress Management Programs
Following a major incident, employees may experience varying degrees of stress, anxiety, or even trauma. Post-incident stress management programs aim to provide appropriate support and assistance to help employees cope with and recover from these experiences. Evaluating the effectiveness of these programs is crucial to ensuring the well-being of employees and maintaining a healthy work environment. The process involves the following steps:
- Establish Program Objectives: Clearly define the objectives of the post-incident stress management program, such as reducing stress levels, improving coping skills, or preventing long-term psychological effects.
- Identify Key Performance Indicators (KPIs): Determine the KPIs that will be used to measure the effectiveness of the program, such as the number of employees utilizing the program, changes in self-reported stress levels, or improvements in work performance.
- Collect Data: Gather data on the program’s performance, including employee participation rates, feedback from participants, and any observed changes in stress levels or work performance.
- Analyze Data and Evaluate Program Effectiveness: Analyze the collected data to determine whether the program is meeting its objectives and delivering the desired outcomes. Consider both quantitative and qualitative data, such as participation rates, employee feedback, and observed changes in stress levels or work performance.
- Identify Areas for Improvement: Based on the evaluation, identify any areas where the program could be improved, such as increasing awareness of the program, adjusting the types of support offered, or enhancing the training of program facilitators.
- Implement Changes and Monitor Progress: Make any necessary changes to the program based on the identified areas for improvement. Continuously monitor the program’s performance to assess the impact of these changes and ensure ongoing effectiveness.
- Communicate Results and Lessons Learned: Share the findings from the evaluation with relevant stakeholders, including management and employees. This helps to reinforce the importance of the program, demonstrate the organization’s commitment to employee well-being, and encourage ongoing participation and support.
- Schedule Regular Evaluations: Establish a schedule for regularly evaluating the post-incident stress management program, ensuring that the process is ongoing and proactive. This helps to identify and address potential issues or areas for improvement and ensures that the program remains effective over time.
By evaluating post-incident stress management programs, organizations can ensure that employees receive appropriate support and assistance following major incidents, ultimately promoting their well-being and maintaining a healthy work environment.
13. Consideration of Civil Claims
Civil claims may arise from incidents where an organization’s actions or negligence have resulted in injury, property damage, or other harm. Reviewing civil claims made against the organization can help identify potential safety issues or areas of liability, allowing the company to address these concerns proactively and improve safety practices. The process involves the following steps:
- Establish a Record-keeping System: Implement a standardized system for documenting and tracking civil claims made against the organization. Ensure that all relevant personnel are trained on the system and understand the importance of accurate and timely documentation.
- Collect and Organize Data: Gather data on civil claims, including information on the type and frequency of claims, the circumstances surrounding each claim, and any identified contributing factors or areas of liability.
- Analyze Data and Identify Trends: Analyze the collected data to identify trends or patterns, such as specific types of claims that occur frequently, locations with a high rate of incidents, or activities that are commonly associated with claims. Look for correlations between claims and other factors, such as safety procedures, equipment, or environmental conditions.
- Investigate Root Causes: Conduct a root cause analysis of identified trends or issues to determine the underlying factors contributing to the civil claims. This may involve examining safety policies, procedures, equipment, or training programs.
- Develop and Implement Corrective Actions: Based on the root cause analysis, develop targeted corrective actions to address the identified issues and reduce the risk of future claims. These actions may include updating safety policies, enhancing training programs, modifying equipment or processes, or improving workplace conditions.
- Monitor and Evaluate: Continuously monitor the effectiveness of the implemented corrective actions and evaluate their impact on reducing civil claims and improving workplace safety. Adjust the corrective actions as necessary to achieve optimal results.
- Communicate Findings and Lessons Learned: Share the findings from the consideration of civil claims with relevant personnel, including management and employees. This helps to raise awareness of the issues, promote learning, and reinforce the organization’s commitment to safety.
- Schedule Regular Reviews: Establish a schedule for regularly reviewing civil claims made against the organization, ensuring that the process is ongoing and proactive. This helps to identify and address potential safety concerns and reduce the risk of future claims.
By considering civil claims, organizations can gain valuable insights into potential safety issues or areas of liability, allowing them to proactively address these concerns and improve safety practices. This can ultimately reduce the risk of future claims and contribute to a safer work environment.
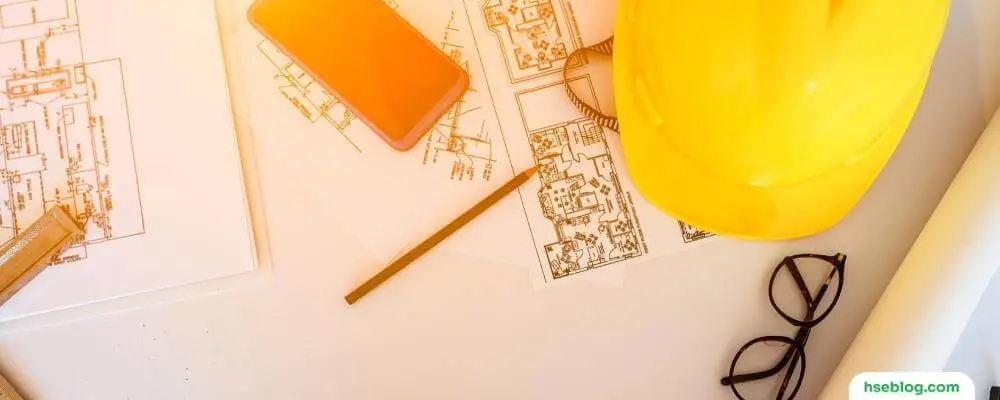
14. Monitoring of Occupational Illness Reports and Trends
This method focuses on tracking and analyzing reports of occupational illnesses among employees to identify patterns and potential hazards in the workplace. The process of monitoring occupational illness reports and trends typically involves the following steps:
- Establishing a Reporting System: Develop a system for reporting and documenting occupational illnesses. This could include medical screenings, employee surveys, or regular health check-ins.
- Collecting Data: Gather detailed information on each reported illness, including factors such as the type of illness, the date of onset, and the employee’s job description and work history. This data should be recorded in a centralized database for easy analysis.
- Categorization and Analysis: Organize the collected data into categories, such as the type of illness or the department in which the employee worked. Analyze the data to identify patterns and trends in the incidence of occupational illnesses.
- Identification of Contributing Factors: Investigate the factors contributing to the identified patterns, such as exposure to hazardous materials or poor ventilation. This may involve conducting workplace inspections, environmental monitoring, or reviewing relevant documentation.
- Development of Solutions: Based on the analysis and investigation, develop appropriate solutions to address the identified hazards. This may involve implementing new safety procedures, modifying equipment or processes, or providing additional training to employees.
- Evaluation of Solutions: Continuously monitor the effectiveness of the implemented solutions and evaluate their impact on reducing the incidence of occupational illnesses. Adjustments to the solutions may be necessary to achieve optimal results.
By tracking and analyzing occupational illness reports and trends, organizations can proactively identify potential workplace hazards and take appropriate measures to mitigate their impact. This can lead to a safer work environment, improved employee health, and reduced costs associated with occupational illnesses.
15. Accident Costs
This method involves analyzing the costs associated with workplace accidents, such as medical expenses, lost wages, property damage, and insurance premiums. By understanding the financial impact of accidents, organizations can develop strategies to reduce costs and improve safety practices.
Accident costs can be categorized into direct and indirect costs. Direct costs include medical expenses, workers’ compensation payments, and damage to equipment or property. Indirect costs are less tangible but can be significant, such as lost productivity, decreased employee morale, and the cost of hiring and training replacement workers.
The process of analyzing accident costs involves the following steps:
- Collect and Organize Data: Gather data on the costs associated with workplace accidents, including direct and indirect costs, as well as any associated insurance premiums.
- Analyze Data and Identify Trends: Analyze the collected data to identify trends or patterns, such as specific types of accidents that result in the highest costs, departments or locations with a high rate of accidents, or activities that are commonly associated with accidents.
- Investigate Root Causes: Conduct a root cause analysis of identified trends or issues to determine the underlying factors contributing to accidents and associated costs. This may involve examining safety policies, procedures, equipment, or training programs.
- Develop and Implement Corrective Actions: Based on the root cause analysis, develop targeted corrective actions to address the identified issues and reduce accident costs. These actions may include updating safety policies, enhancing training programs, modifying equipment or processes, or improving workplace conditions.
- Monitor and Evaluate: Continuously monitor the effectiveness of the implemented corrective actions and evaluate their impact on reducing accident costs and improving workplace safety. Adjust the corrective actions as necessary to achieve optimal results.
- Communicate Findings and Lessons Learned: Share the findings from the analysis of accident costs with relevant personnel, including management and employees. This helps to raise awareness of the issues, promote learning, and reinforce the organization’s commitment to safety.
- Schedule Regular Reviews: Establish a schedule for regularly reviewing accident costs, ensuring that the process is ongoing and proactive. This helps to identify and address potential safety concerns and reduce accident costs.
By analyzing accident costs, organizations can gain valuable insights into the financial impact of workplace accidents and develop targeted strategies to reduce costs and improve safety practices. This can ultimately create a safer work environment, reduce the risk of accidents and injuries, and contribute to overall productivity and efficiency.
Conclusion
In today’s fast-paced work environments, safety must always be a top priority for any organization. Proactive safety measures aim to prevent accidents and incidents from occurring. Still, when incidents do happen, reactive monitoring methods become crucial to identifying potential hazards, determining root causes, and implementing effective corrective actions to enhance workplace safety.
In this blog post, we have explored 15 different types of reactive monitoring methods that organizations can use to learn from incidents and improve safety practices. These methods range from analyzing trends and patterns of accidents to evaluating post-incident stress management programs and considering accident costs. By employing these methods, businesses can create a safer work environment, reduce the risk of accidents and injuries, and demonstrate a strong commitment to employee well-being.
The key takeaway from this blog post is that safety is an ongoing process that requires constant attention and effort. Organizations that prioritize safety and invest in reactive monitoring methods can not only prevent accidents but also enhance their overall productivity and efficiency. By taking a comprehensive and systematic approach to safety, organizations can create a culture of safety that benefits everyone in the workplace.