Safety light curtains have become a cornerstone of modern industrial safety, offering a non-contact, intelligent solution to protect workers from hazardous machinery without hindering productivity. Unlike traditional physical guards that limit access and slow down operations, light curtains use infrared beams to instantly detect intrusions and trigger safe machine shutdowns.
In this comprehensive guide, we’ll explore safety light curtains, how they work, the different types available, their key features, advanced functions, regulatory compliance, and best practices for effective use, helping you make informed decisions for a safer, more efficient workplace.
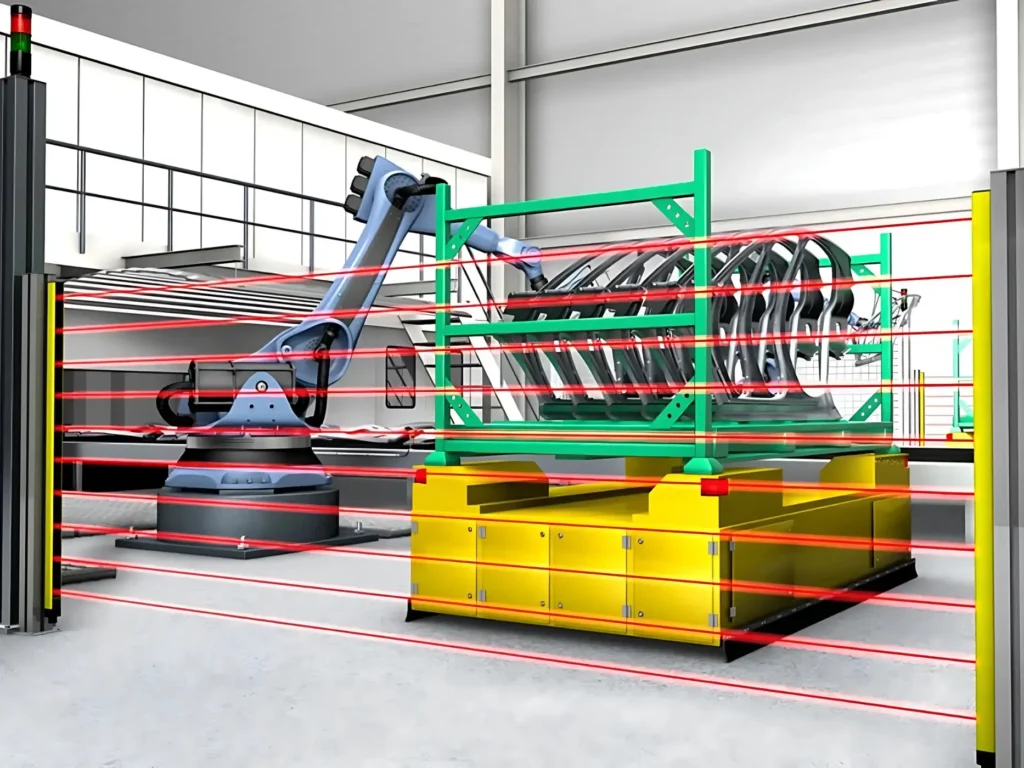
What Is a Safety Light Curtain?
A safety light curtain is an electrosensitive protective device that creates an invisible field of infrared light between two units: a transmitter and a receiver. When any object (like a person’s hand or body) interrupts the light beam, the system immediately triggers a safety response, typically stopping the machine to prevent injury.
Think of it as an invisible fence made of light beams that protects workers from moving parts or dangerous zones in industrial machinery.
Key Characteristics
- Non-contact detection
- Fast response time (usually <20 ms)
- Allows frequent operator access without physical doors
- Configurable for different safety distances and resolutions
Importance Of Safety Light Curtains
Safety light curtains are crucial in modern automation for three main reasons:
- Enhanced Worker Safety: They significantly reduce the risk of crush, shear, or cut injuries in high-risk zones.
- Improved Productivity: Operators don’t have to open physical guards or doors, which speeds up cycle times while keeping safety intact.
- Flexibility in Design: They can be adapted to various machine layouts—great for custom or modular manufacturing setups.
According to OSHA, incorporating automated safety systems like light curtains reduces workplace injuries in machine-heavy industries.
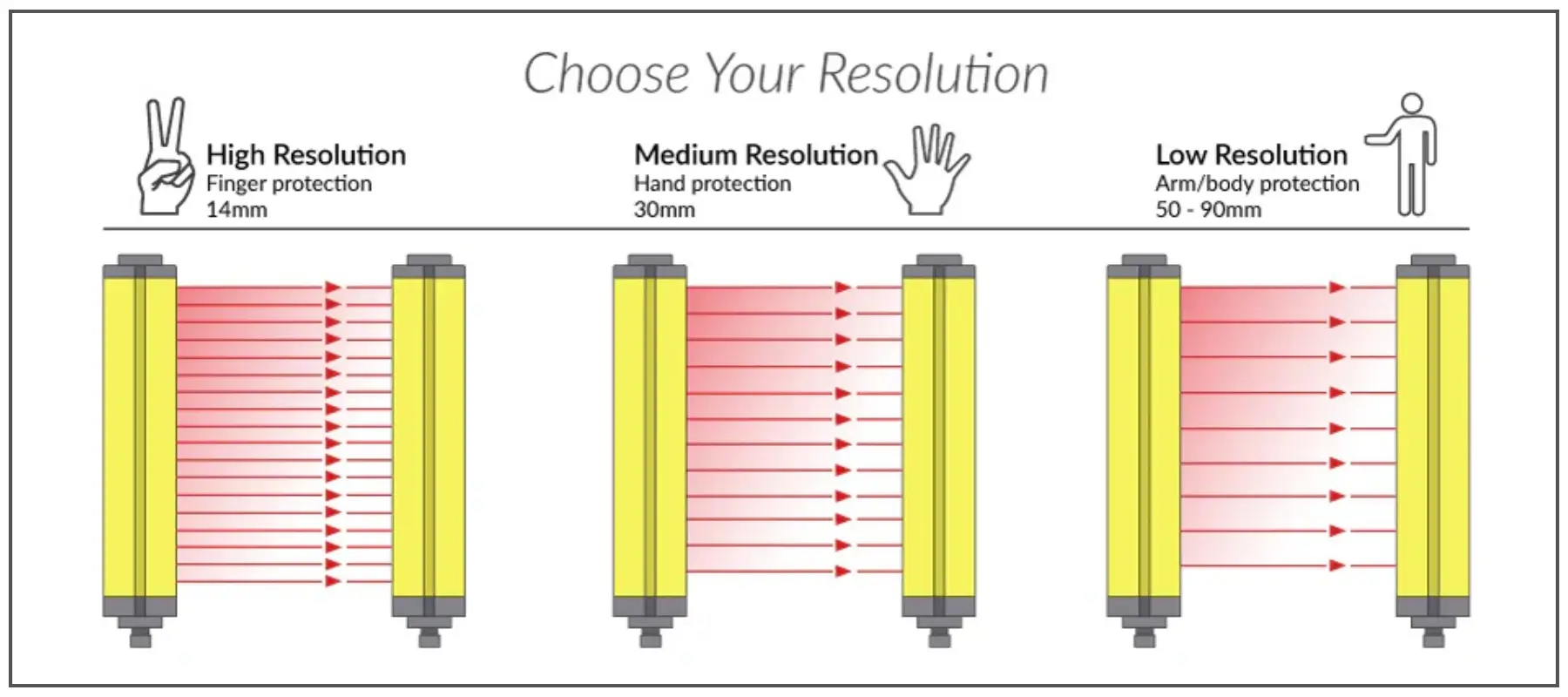
Types of Safety Light Curtains
Let’s explore the different types of safety light curtains, including their functions, design purposes, and ideal applications.
1. Type 2 Safety Light Curtains (PL c / SIL 1)
Type 2 light curtains are basic safety devices intended for low-risk applications. They operate with single-channel fault detection, meaning they may not detect certain internal faults. As a result, they should only be used in environments where the hazard is minimal and the consequences of failure are not severe.
Key Features:
- Performance Level (PL): c
- Safety Integrity Level (SIL): 1
- Compliance: ISO 13849-1, IEC 61496-1/2 (Type 2)
- Lower cost than Type 4 devices
Best For:
- Light-duty automation
- Packaging equipment without dangerous motion
- Areas with low exposure frequency to hazards
Not suitable for applications where serious injury or death could occur.
2. Type 4 Safety Light Curtains (PL e / SIL 3)
Type 4 light curtains are high-reliability safety devices designed for high-risk applications. They incorporate dual-channel fault detection and self-checking systems. Any fault or interruption, even in the electronics, will trigger a safe stop.
Key Features:
- Performance Level (PL): e
- Safety Integrity Level (SIL): 3
- Compliance: ISO 13849-1, IEC 61496-1/2 (Type 4)
- Capable of advanced features like muting, blanking, and EDM
- Required for most industrial machine guarding applications
Best For:
- Press brakes
- Punching and shearing machines
- Robotic arms and automated assembly systems
- Machinery with frequent human interaction near hazardous motion
The industry standard for most machine safety systems.
3. Finger Protection Light Curtains
These are high-resolution light curtains (typically 14 mm spacing) designed to detect very small objects, such as fingers. Their fine resolution allows the system to trigger a shutdown even when the smallest body part enters the danger zone.
Key Features:
- Beam spacing: ~14 mm
- Detection capability: Fingers and small tools
- Requires close positioning to the hazard
Best For:
- Precision machinery
- Small-part presses
- Punch presses
- Light-duty assembly equipment
Ideal when operators work very close to cutting or pressing zones.
4. Hand Protection Light Curtains
With medium resolution (around 30 mm beam spacing), these curtains detect a full hand entering the hazardous area. They’re used when the risk of finger injury is minimal, but hand entry still poses danger.
Key Features:
- Beam spacing: ~30 mm
- Detection capability: Hands and larger objects
- Slightly longer safety distance than finger detection models
Best For:
- Conveyor systems
- Pick-and-place robots
- General machine guarding where hands may reach into the hazard
Good balance of safety and flexibility for hand-level interaction.
5. Body Protection or Access Control Light Curtains
These light curtains have a wider beam spacing (typically 50–90 mm) and are taller to detect the presence of a full human body. They’re typically used for perimeter guarding or to prevent access into a dangerous zone altogether.
Key Features:
- Beam spacing: 50 mm or more
- Detection capability: Full-body
- Tall protective height (up to 1800 mm or more)
Best For:
- Perimeter and area protection
- Robot enclosures
- AGV (Automated Guided Vehicle) interaction zones
- Machine access points
Functions like an invisible safety fence.
6. Multibeam Safety Devices (Light Barriers)
Unlike traditional light curtains, multibeam systems use a few beams (typically 1 to 4) positioned at specific heights. They’re commonly referred to as light barriers and are used for point-of-entry protection rather than guarding a vertical plane.
Key Features:
- Limited number of beams
- Point detection instead of full curtain
- Simple and cost-effective
Best For:
- Loading docks
- Vehicle passageways
- Gate monitoring
- Storage/retrieval systems
Ideal for basic access control or low-complexity safety zones.
7. Cascadable Light Curtains
These are modular systems that allow multiple light curtains to be connected in series using a single control interface. Cascading reduces wiring and simplifies installation across multi-sided or irregular guarding zones.
Key Features:
- Multiple emitter/receiver pairs connected
- Synchronized coverage across multiple planes
- Centralized wiring and diagnostics
Best For:
- L-shaped or U-shaped machine layouts
- Complex robotic cells
- Large multi-access machines
Efficient for large or multi-directional guarding requirements.
8. Smart / Advanced Light Curtains
Modern smart light curtains integrate with digital networks, support real-time diagnostics, and offer advanced configuration through software. These are used in Industry 4.0 and smart factory environments where performance monitoring and system integration are critical.
Key Features:
- IO-Link, EtherCAT, Profisafe, or Ethernet/IP support
- Built-in muting, blanking, EDM, and diagnostics
- Software-configurable detection zones
- Predictive maintenance alerts
Best For:
- Highly automated manufacturing plants
- Smart robotics
- Environments with rapid changeovers or configuration needs
Best for future-proof safety integration with full transparency and control.
When choosing a safety light curtain type, always match:
- Risk level (low vs. high)
- Required detection resolution (finger, hand, body)
- Layout complexity (single access point vs. multi-sided)
- Compliance standards (Type 2 for PL c / SIL 1; Type 4 for PL e / SIL 3)
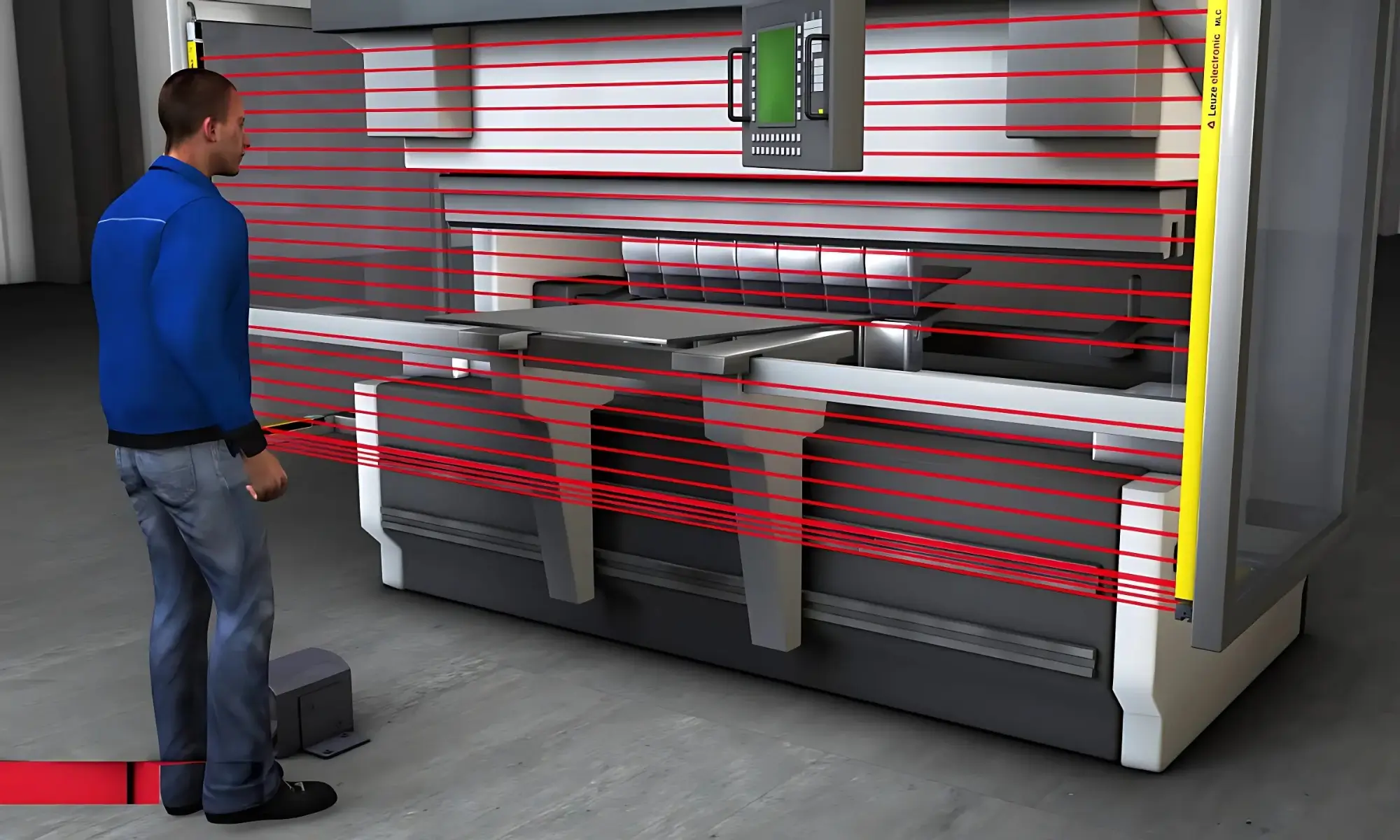
How Do Safety Light Curtains Work?
Safety light curtains operate using a combination of infrared light beams and electronic control systems to detect the presence of people or objects in hazardous areas around machinery. Here’s a step-by-step breakdown of how they work:
1. Transmitter Emits Infrared Beams
The transmitter unit contains multiple infrared LEDs that project a parallel array of invisible light beams across a protected area. These beams form an optical barrier.
2. Receiver Detects the Beams
Opposite the transmitter, the receiver unit contains photoelectric sensors (like photodiodes or phototransistors) aligned with each beam. As long as every beam is received without interruption, the system confirms that the area is safe.
3. Monitoring the Beam Pattern
The light curtain system continuously monitors whether the beams are received in a precise sequence and timing. This helps eliminate false signals from external light sources or interference.
4. Interruption Triggers a Safety Response
When a solid object—such as a hand, tool, or body part—enters the beam field and blocks one or more light rays, the receiver detects this interruption.
5. Signal Sent to Stop the Machine
Once the interruption is detected, the control unit (often integrated with a safety relay or controller) sends a stop signal to the connected machinery. The system may enter a safe state, such as:
- Halting motion
- Locking out further operation
- Requiring a manual reset before resuming
Additional Safety Features in Operation
Modern safety light curtains also include:
- Self-checking circuits to detect internal faults.
- EDM (External Device Monitoring) to verify whether connected devices like relays or contactors have been adequately deactivated.
- Restart Interlocks prevent automatic machine restart until the area is clear and manually confirmed.
- Muting or Blanking temporarily disables some beams to allow material flow without triggering shutdown.
This non-contact, automatic detection system makes safety light curtains ideal for dynamic production environments where worker protection and operational efficiency coexist.

Where Are Safety Light Curtains Used?
Safety light curtains are widely used in industrial and manufacturing settings where operators need to be protected from hazardous machine movements, without slowing down productivity. Their flexibility, speed, and non-intrusive design make them ideal for areas requiring frequent human access near dangerous equipment. Here are the most common applications:
1. Press Brakes and Cutting Machines
Operators working close to press brakes, shears, or stamping machines face serious injury risks. Light curtains protect the zone near the point of operation, instantly stopping the machine if hands or limbs enter the danger area.
2. Robotic Workcells
In robotic automation zones, light curtains monitor entry and exit points to prevent accidental contact with moving robotic arms. This allows safe human-machine collaboration during maintenance or material loading.
3. Conveyor Systems
Light curtains at transfer points or automated conveyors detect if someone reaches into pinch points or if foreign objects disrupt the line. They can trigger automatic stops to prevent injury or damage.
4. Packaging and Palletising Equipment
High-speed packaging lines use safety light curtains to guard the moving parts of wrapping machines, sealers, and palletizers, especially where workers need to feed materials or remove finished goods.
5. Injection Moulding Machines
Light curtains ensure safety during mould changes or maintenance by securing the clamp and ejection areas of injection moulding machines, which involve high-pressure mechanisms.
6. Automated Assembly Lines
In assembly operations with pick-and-place systems or part feeders, light curtains allow for safe intervention without dismantling guards, minimising downtime.
7. Material Handling and Loading Zones
Where forklifts or automated guided vehicles (AGVs) interact with fixed machines, safety light curtains provide a buffer zone to prevent collisions or human entry into restricted areas.
Why These Environments Rely on Light Curtains
- Non-contact safety: No need for gates or mechanical guards
- Quick response: Machine stops in milliseconds
- Operator convenience: Easier access for routine tasks
- Space-saving design: Slim profiles fit tight layouts
In essence, anywhere there’s a hazardous motion and human interaction, safety light curtains provide a fast, flexible, and reliable solution that meets productivity and compliance goals.
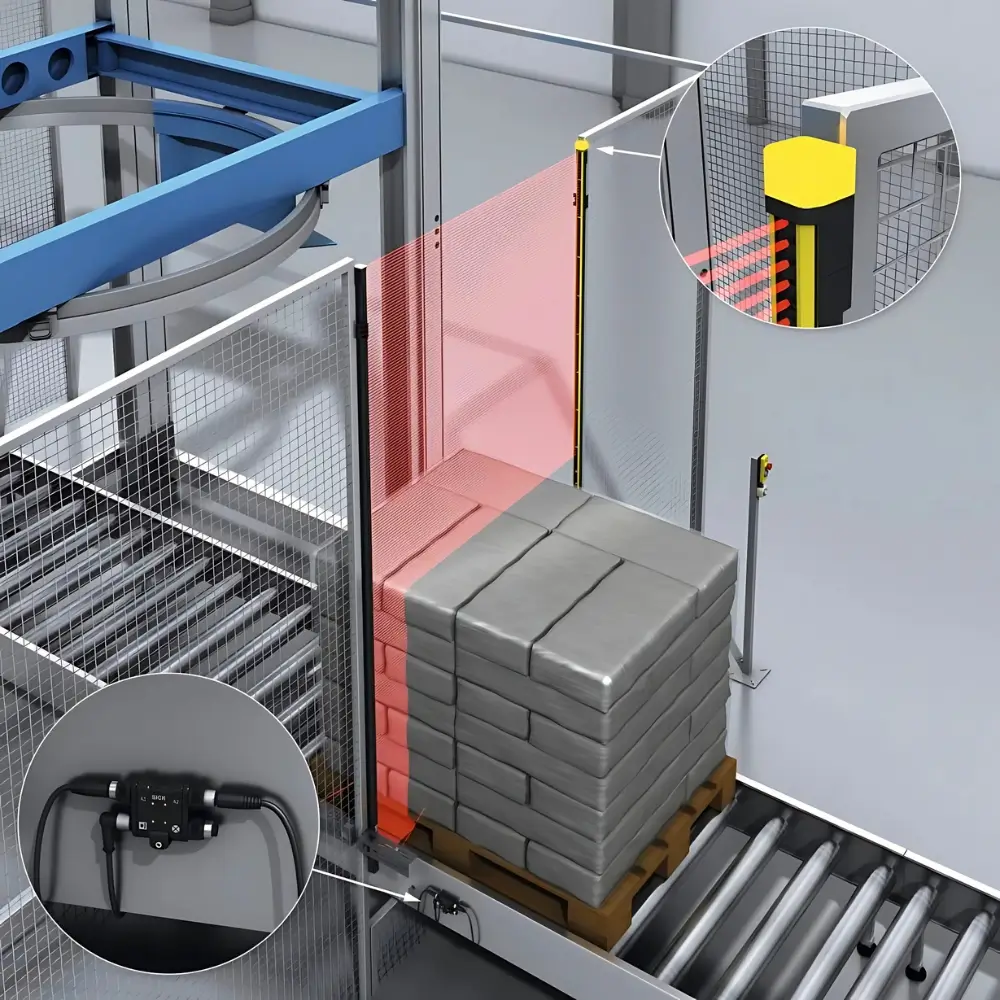
Key Features to Look for in a Safety Light Curtain
Here is a clear table-only format of the key features to look for in a safety light curtain:
Feature | Description | Purpose/Benefit |
---|---|---|
Resolution | Minimum object size detectable (e.g., 14 mm for fingers, 30 mm for hands) | Ensures proper detection based on body part at risk |
Protective Height | Vertical coverage of the light curtain’s sensing field | Matches the size of the access or hazard area |
Operating Range | Distance between transmitter and receiver (up to 20+ meters) | Suitable for narrow or wide machine openings |
Response Time | Time to trigger machine stop after beam interruption (typically <20 ms) | Reduces minimum safety distance and increases reaction speed |
Safety Category / PL | Safety integrity level (e.g., Type 4 / PL e / SIL 3 for high-risk environments) | Aligns with risk level per ISO 13849-1 and IEC 61508 |
Muting | Temporarily disables detection for material flow | Maintains safety while allowing automated processes to continue |
Blanking | Ignores specific beams (fixed or floating) | Avoids false trips from permanent or moving obstructions |
Cascading | Allows connection of multiple curtains | Covers multiple sides or complex machine geometries |
EDM | Monitors external safety device status (e.g., relays) | Requires manual reset to verify the area is safe before resuming |
Restart Interlock | Prevents automatic restart after interruption | Requires manual reset to verify area is safe before resuming |
Advanced Functions of Modern Light Curtains
Modern safety light curtains go far beyond simple on/off protection. Today’s systems are equipped with intelligent features that enhance flexibility, maintain workflow efficiency, and provide detailed diagnostics. These advanced functions allow light curtains to integrate seamlessly into complex industrial environments without compromising safety. Here’s a summary of the main advanced functions:
Function | Description | Benefit |
---|---|---|
Muting | Temporarily disables specific beams to allow non-hazardous objects (like pallets or materials) to pass without triggering a stop signal. | Allows safe material flow in/out of hazardous zones without halting the machine. |
Blanking | Ignores certain beams that are permanently or temporarily blocked. Can be fixed (static obstruction) or floating (moving within limits). | Prevents unnecessary shutdowns due to known or acceptable obstructions. |
Cascading | Connects multiple light curtain sets in series to protect multiple sides or complex zones using a single control system. | Enables coverage of large or irregularly shaped areas with minimal wiring. |
EDM (External Device Monitoring) | Verifies that external safety devices (like contactors or relays) respond correctly when the light curtain is triggered. | Ensures complete safety system reliability and alerts on device failure. |
Manual/Automatic Restart Interlock | Controls whether the machine can restart automatically or requires manual confirmation after beam interruption. | Prevents accidental restarts; enforces safety checks before resuming work. |
Alignment Indicators | Visual LED guides or signal outputs that help installers align the transmitter and receiver accurately. | Reduces installation time and avoids operational misalignment. |
Built-in Diagnostics | Displays fault codes, beam status, or cause of machine stop directly on the light curtain or via software. | Speeds up troubleshooting and reduces system downtime. |
Communication Interfaces | Integration with industrial networks (e.g., Ethernet/IP, IO-Link, Profisafe) for data exchange and monitoring. | Enhances system transparency and allows real-time performance tracking. |
Safety Distance Calculation Tools | Some manufacturers provide digital tools or embedded logic to calculate minimum safe distance automatically. | Ensures correct installation and regulatory compliance. |
Protective Field Customization | Ability to customize detection zones using software (in some models). | Tailors protection to specific application needs without hardware changes. |
These features make modern light curtains not just safety devices, but smart automation tools that adapt to the demands of Industry 4.0.
Regulations & Compliance for Safety Light Curtains
Safety light curtains are regulated by international and national safety standards to ensure they provide reliable protection in industrial environments. Compliance with these standards is essential for both legal liability and operator safety. Here’s a clear overview of the key regulations and their meanings:
Standard/Regulation | Purpose | What It Covers |
---|---|---|
IEC 61496-1 / IEC 61496-2 | International standard for electrosensitive protective equipment (ESPE). | Defines design and testing requirements for light curtains; ensures reliable operation. |
ISO 13849-1 | Standard for the safety of machinery using control systems. | Determines the Performance Level (PL) needed based on risk analysis and system architecture. |
IEC 61508 | Functional safety for electrical/electronic systems. | Covers system design to achieve a specific Safety Integrity Level (SIL). |
IEC 62061 | Functional safety of safety-related control systems. | Focuses on SIL for control systems in machinery applications. |
OSHA 1910 Subpart O (U.S.) | U.S. regulation for machinery and machine guarding. | Requires machine guarding methods that include light curtains where appropriate. |
ANSI B11.19 | U.S. national standard for safeguarding methods. | Provides guidelines on how to apply light curtains and ensure their proper use. |
EN/ISO 12100 | Safety of machinery—Risk assessment and risk reduction. | Framework for identifying hazards and applying appropriate safeguarding measures. |
Why Compliance Matters
- Legal Protection: Non-compliance can result in regulatory penalties or lawsuits.
- Worker Safety: Properly rated equipment ensures injury prevention.
- Insurance & Audits: Verified compliance improves outcomes in workplace audits and claim investigations.
- Global Trade: Meeting international standards ensures your equipment can be sold or operated globally.
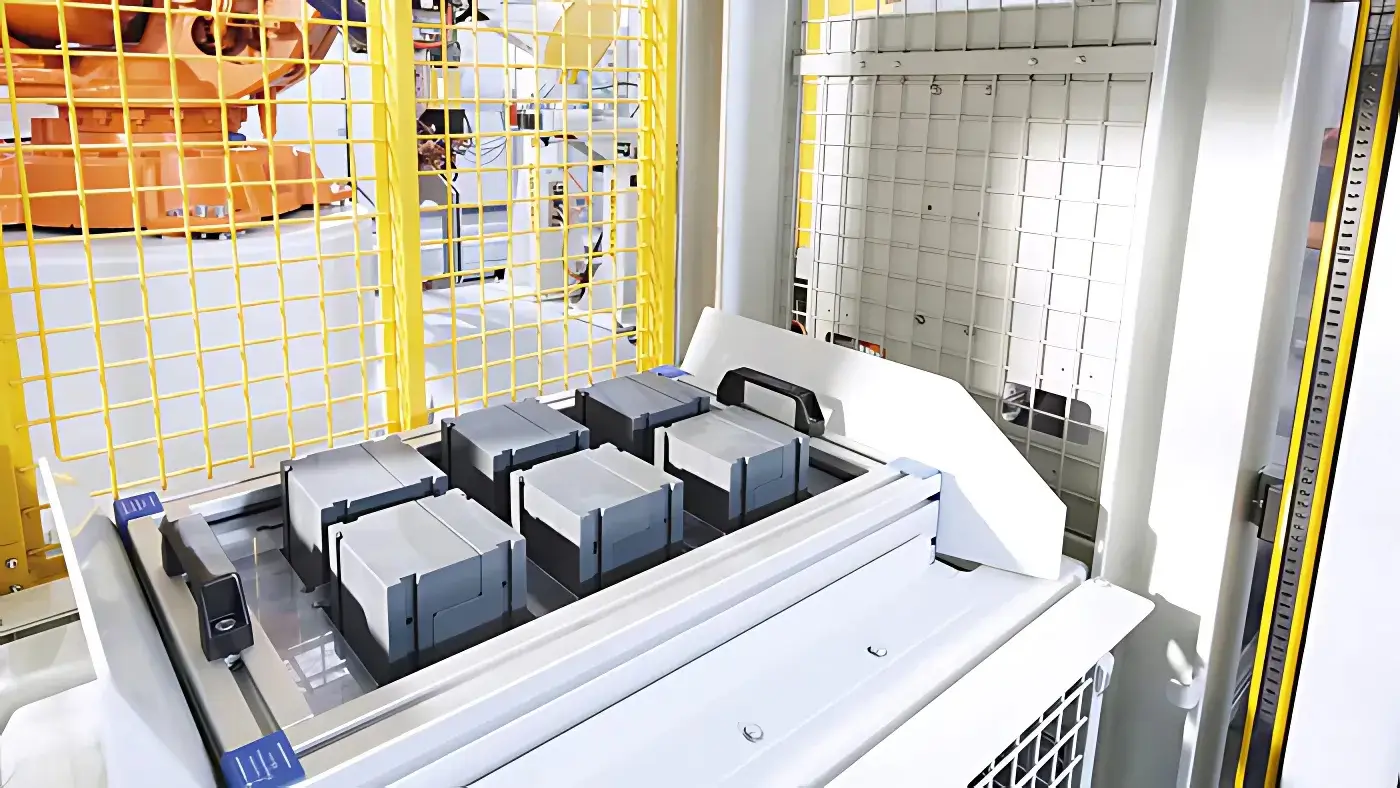
Common Myths About Light Curtains
Despite being widely used in industrial safety, light curtains are often misunderstood. These misconceptions can lead to poor implementation, underutilization, or even unsafe practices. Here’s a look at some common myths and the facts that disprove them:
Myth | Reality |
---|---|
Light curtains are complicated to install. | Modern models are plug-and-play, with alignment indicators and simple wiring that reduce setup time. |
They slow down production. | Light curtains actually increase efficiency by eliminating the need for physical barriers or gates. |
They only protect hands and fingers. | With different resolutions available, they can detect anything from a finger to a full body. |
All light curtains offer the same protection. | Performance varies greatly. Always check for Type 2 vs. Type 4 classification and PL/SIL ratings. |
Once installed, no maintenance is needed. | Regular inspections and cleaning are essential to avoid misalignment or contamination. |
Muting or blanking reduces safety. | When properly configured, these features allow safe material flow without compromising protection. |
Light curtains don’t work in dirty environments. | Many models are IP-rated and designed to withstand dust, oil, and industrial conditions. |
They can be easily bypassed. | Certified systems include tamper-proof designs and restart interlocks to prevent misuse. |
They aren’t compatible with smart systems. | Advanced light curtains support IO-Link, Ethernet/IP, and Profisafe for full integration. |
Only large machines need them. | Even small presses or assembly stations benefit from compact light curtain models. |
Understanding the truth behind these myths helps you get the most value and protection out of your safety light curtain investment.
Best Practices for Using Safety Light Curtains
To get the most out of your safety light curtains—and ensure maximum protection and compliance—follow these best practices from installation through maintenance:
1. Start with a Risk Assessment
Before choosing or installing a light curtain, conduct a thorough risk assessment. Identify the type of hazard, frequency of access, and the potential severity of injury. This helps determine the required safety category (Type 2 or Type 4) and performance level (PL).
2. Choose the Right Resolution and Range
Select a resolution that matches the level of protection needed—finger, hand, or body detection. Also, consider the operating range to ensure the transmitter and receiver can be correctly aligned within your machine layout.
3. Position Light Curtains Correctly
Mount the light curtain far enough from the hazard to allow the machine to stop before someone can reach the danger zone. This distance depends on the response time of the curtain and the machine’s stopping time. Use safety distance formulas to calculate proper placement.
4. Align with Safety Standards
Always install light curtains according to applicable regulations such as ISO 13849-1, IEC 61496, and OSHA 1910. Ensure that both the product and the installation meet the safety requirements for your industry.
5. Enable Advanced Features Wisely
Use muting and blanking functions only when necessary and configure them properly to avoid compromising protection. These features are great for automated material flow, but must not create safety loopholes.
6. Integrate with Safety Controllers
Pair light curtains with certified safety relays or programmable safety controllers. This ensures that when a beam is broken, the correct machine-stopping logic is reliably executed.
7. Test After Installation
After setup, thoroughly test the system by interrupting the light curtain with various objects. Make sure the machine stops every time and that the restart interlocks function as intended.
8. Train Operators and Maintenance Teams
Ensure all workers who interact with the machine understand how the light curtain works, what its signals mean, and how to safely reset or troubleshoot the system.
9. Perform Regular Inspections
Periodically check for misalignment, contamination (like oil, dust, or debris), or physical damage to the emitter or receiver. Regular maintenance ensures the system remains functional and compliant.
10. Document Everything
Keep detailed records of installation, testing, training, and maintenance. This documentation helps during audits, inspections, and in proving compliance in the event of an incident.
Using safety light curtains effectively isn’t just about turning them on—it’s about ensuring they’re correctly chosen, installed, and maintained as part of a broader safety strategy. Done right, they help you protect people without slowing down your process.
Conclusion
Safety light curtains are more than just protective barriers—they are intelligent, adaptable safety solutions that enhance both worker protection and operational efficiency. By using invisible infrared beams to monitor access to hazardous zones, they allow for safe human interaction with machines while reducing downtime and improving workflow.
With various types, features, and advanced functions available, these devices can be tailored to meet the specific needs of any industrial environment. When properly selected, installed, and maintained in accordance with safety standards, light curtains not only ensure compliance but also foster a proactive safety culture that benefits both employees and productivity.