In the dynamic world of construction and logistics, cranes play a vital role in lifting, moving, and handling heavy loads. With their impressive power and versatility, cranes have become essential for various industries. Cranes are at the forefront of modern engineering and construction, from towering skyscrapers to intricate manufacturing processes.
This comprehensive guide will explore the world of cranes and their diverse applications. We will uncover the fundamental principles behind cranes, their components, and the intricate mechanisms that enable them to perform extraordinary tasks. Additionally, we will look closer at 15 different types of cranes used worldwide, each tailored to specific needs and environments. From the towering presence of tower cranes on bustling construction sites to the nimble mobility of mobile cranes, we will explore how each crane type has revolutionized how we build, transport, and handle heavy loads.
Whether you are a construction professional, a logistics enthusiast, or simply curious about the engineering marvels that cranes represent, this guide will provide valuable insights into the world of cranes. Join us on this journey as we unravel the mysteries behind cranes, their functions, and their incredible impact on the modern world. Let’s dive into the fascinating realm of cranes and discover the types shaping industries worldwide.
What is Crane?
A crane is a type of heavy machinery specifically designed for lifting, lowering, and moving heavy items using pulleys and cables. Cranes are essential tools in various industries, such as construction, manufacturing, and transportation, due to their capability to handle heavy loads and materials. They can vary greatly in size and functionality, with small cranes used for tasks such as vehicle recovery. In contrast, massive tower cranes construct tall buildings or bridges.
Cranes usually consist of several key components:
- Boom: This is the crane’s long arm. Some cranes have a fixed boom, while others, like the telescopic crane, have booms that can be extended and contracted to reach various heights and lengths.
- Jib: The jib is an extension of the boom. Not all cranes have a jib, but when they do, it allows the crane to reach further and move loads beyond the capabilities of the boom alone.
- Hooks and Wires: These are used to attach the material lifted by the crane. The wires can be reeled in or out to lift or lower the load, and the hooks secure the load to the wire.
- Controls: The crane operator uses these to direct the movement of the load. Some cranes are operated from a cab attached to the crane, while others may be operated remotely.
- Outriggers and Counterweights: These are used to stabilize the crane while it’s lifting heavy loads. Outriggers extend from the base of the crane to increase its footprint and balance, while counterweights are added to balance the weight of the load.
Cranes are indispensable tools in many industries, including construction, where they are used to move heavy construction materials; shipping, where they load and unload heavy cargo; and manufacturing, where they can move heavy parts or machinery. Due to their crucial role and the potential dangers involved with their operation, rigorous safety protocols and training are required for crane operators.
15 Different Types Of Cranes
Cranes are powerful machines used for lifting and moving heavy objects or materials. Several types of cranes are available, each designed for specific applications and operating conditions. Here are some of the most common types of cranes:
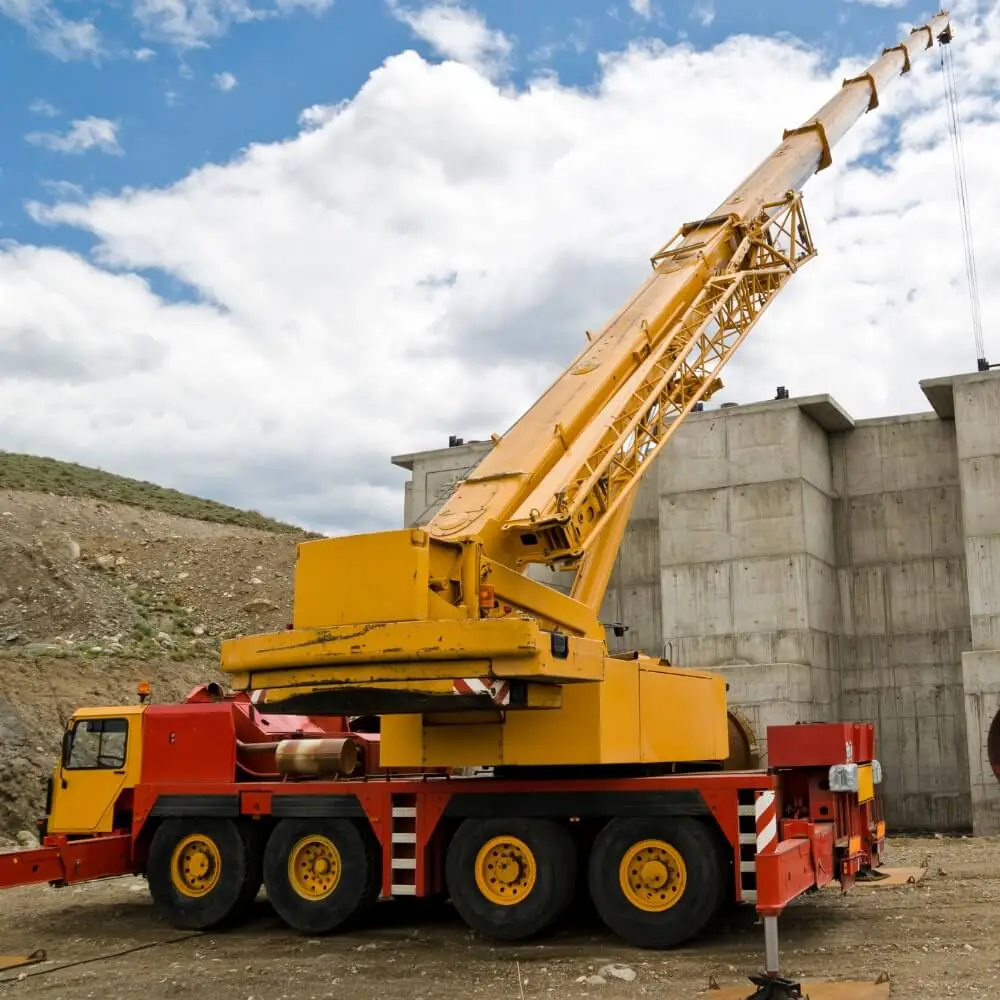
1. Mobile Crane
A mobile crane is designed for easy transport and mobility, allowing it to reach various locations and perform lifting operations without the need for permanent installation. Mobile cranes are versatile and essential in various industries, such as construction, manufacturing, transportation, etc.
Here are some key features and components of mobile cranes:
- Boom: This is the long arm of the crane that performs the actual lifting. The boom can be telescopic, allowing for adjustable length, or it may be a lattice structure that can be extended with additional sections.
- Counterweights: These are weights placed on the back of the crane to balance the load being lifted. The counterweight helps prevent the crane from tipping over under the weight of the load.
- Outriggers: These are extendable legs that provide stability to the crane while lifting heavy loads. They distribute the crane’s weight over a larger area, reducing ground pressure and enhancing stability.
- Cab: This is where the operator controls the crane. It has various controls and instruments for operating the boom, movement, and other functions.
- Engine and Drivetrain: Mobile cranes are typically powered by internal combustion engines. The drivetrain allows for movement and power of the hydraulic systems operating the boom and other functions.
- Hydraulic System: This system uses hydraulic fluid to create pressure and power the movement of the boom and other mechanical aspects of the crane.
- Hoist and Wire Ropes: These lift and lower the loads. The hoist is a winch that winds the wire rope, while the wire ropes are strong cables used to lift the load.
- Hooks and Load Handling Devices: At the end of the boom, various hooks and devices can be attached to handle different types of loads.

2. Tower Crane
A tower crane is a type of crane used primarily in the construction industry for lifting and moving heavy materials. Tower cranes are essential in constructing tall buildings as they can reach heights and have a large lifting capacity. They are fixed to the ground or attached to the side of a structure during construction.
Here are some key components and features of tower cranes:
- Base: The base of the tower crane is usually anchored to a large concrete pad to ensure stability and is responsible for supporting the crane. In some cases, the crane may be attached to the side of a building as the building rises.
- Tower Mast: This vertical section gives the tower crane its height. It’s typically a lattice structure, although some modern cranes use a telescopic system to adjust the height.
- Slewing Unit: This is located at the top of the tower mast and contains the gears and motors that enable the crane to rotate. It allows the crane to swing in a circular motion and move the load to the desired location.
- Jib: The jib, or operating arm, extends horizontally from the crane. Tower cranes usually have a long jib to provide a wide radius of action.
- Counter Jib: This extends in the opposite direction of the jib and holds counterweights. These counterweights balance the loads that the crane lifts.
- Hoist Winch: This is the mechanism for lifting and lowering the load. It is usually on the counter jib and uses wire ropes and pulleys.
- Trolley: This is a carriage that moves along the length of the jib, and can be used to adjust the position of the load relative to the tower.
- Operator’s Cab: This is where the crane operator controls the crane’s movements. It’s usually situated just above the slewing unit and contains controls and instrumentation for operating the crane.
- Hooks and Load Handling Devices: These are attached at the end of the hoist lines for handling different types of loads.
Tower cranes are known for their height and lifting capacity advantages but are relatively immobile once installed. They require a significant amount of time and effort to be set up and disassembled and, as such, are usually used for long-term construction projects where their capacity can be fully utilized.
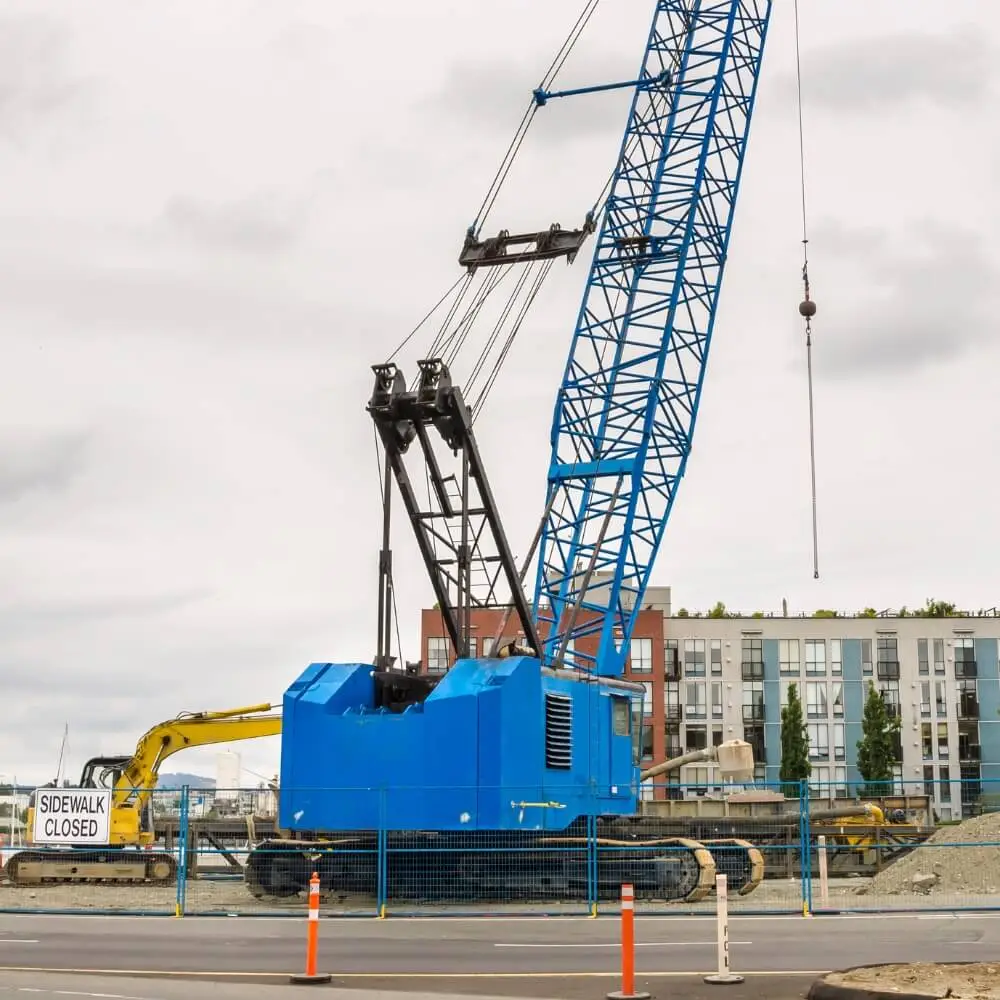
3. Crawler Crane
A crawler crane is a type of crane that is designed for stability, mobility, and lifting heavy loads, particularly on sites with uneven or rough terrain. It features an upper carriage with a control cabin, engine, boom, counterweights, and lifting mechanisms, and this upper carriage is mounted on a crawler undercarriage.
Here are the key components and features of a crawler crane:
- Crawler Undercarriage: The most distinguishing feature of a crawler crane is its crawler tracks, similar to those on a tank. These tracks provide excellent stability and allow the crane to easily move across uneven surfaces without outriggers.
- Upper Carriage: This is mounted on the crawler undercarriage and rotates 360 degrees. It contains the engine, operator’s cabin and the working components of the crane.
- Boom: This is the long arm used for lifting and can be either a lattice structure or a telescopic boom. Lattice booms are lighter and can reach greater heights, while telescopic booms are more versatile and can be adjusted in length more easily.
- Jib: This is an optional boom extension that can be added to increase the crane’s reach. It can be particularly useful in reaching over obstacles or extending the crane’s height.
- Hoist and Wire Ropes: The hoist is the winch mechanism that winds and unwinds the wire ropes, allowing the crane to lift and lower loads. These ropes run from the hoist up through the boom and/or jib.
- Lifting Implements: At the end of the wire rope, various implements such as hooks, grapples, clamshells, or magnets can be attached depending on the nature of the load to be lifted or moved.
- Counterweights: These are heavy weights placed on the back of the upper carriage to balance the load being lifted. This is crucial in preventing the crane from tipping over under the weight of the load.
- Operator’s Cabin: The operator controls the crane from a cabin in the upper carriage. This cabin contains controls and instrumentation for operating the crane’s movements and lifts.
- Engine: Typically, a powerful internal combustion engine provides the necessary power for the movements and operations of the crane.
Crawler cranes are used for various applications, including construction, bridge building, heavy lifting and moving, and other industries requiring the movement of heavy materials. Their ability to traverse rough terrain and carry heavy lifts makes them indispensable in many projects. However, they must be operated and maintained carefully, as the heavy loads and machinery pose potential hazards to operators and personnel on-site.
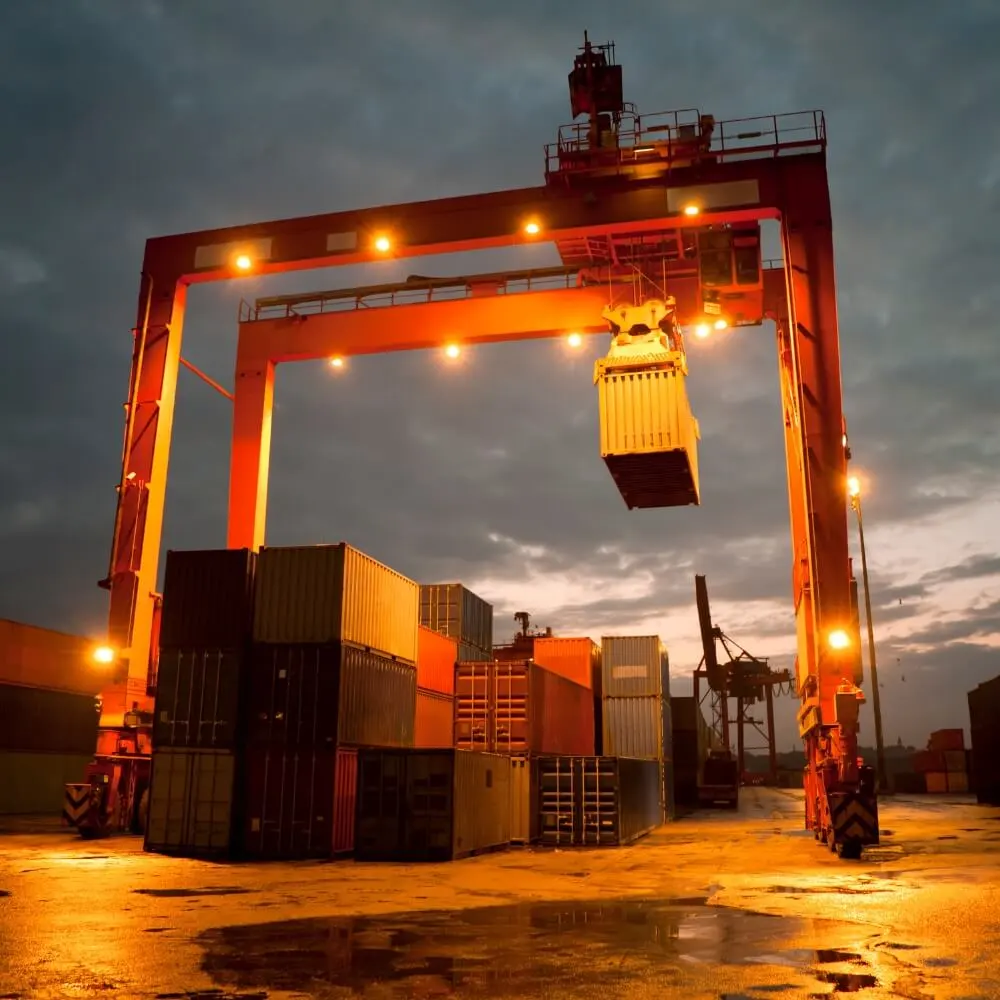
4. Overhead Crane
An overhead crane, also known as a bridge crane, is used for lifting and moving heavy materials horizontally within a restricted area, usually inside a facility. As the name suggests, it is typically positioned overhead, often mounted on rails attached to the ceiling or on elevated structures. This ensures efficient use of space and keeps the floor area unobstructed.
Here are the key components and features of an overhead crane:
- Bridge: The bridge is the primary structure that spans across the workspace. It usually consists of one or more beams that are positioned overhead.
- Hoist and Trolley: The hoist is the mechanism used for lifting and lowering loads. It is mounted on a trolley, which moves back and forth across the bridge. This combination allows for vertical as well as horizontal movement of materials.
- Runways: These are the rails or tracks on which the bridge moves. They are usually mounted on the sides of the facility or on elevated structures. This allows the entire crane to move along the length of the workspace.
- Controls: The operations of the overhead crane can be controlled through various means. Some cranes feature a cabin from which an operator controls the movements. In contrast, others might be operated through a remote control or a pendant control station that can be operated from the ground.
- End Trucks: These are located on either side of the bridge and contain wheels that enable the bridge’s movement along the runways.
- Hook or Lifting Attachment: At the end of the hoist, a hook or other lifting attachment is used to secure the materials being lifted. Depending on the material to be handled, there are various attachments like magnets, clamps, or grabs.
- Power Source: Overhead cranes are usually powered by electricity, and the power supply is often delivered through cables or bus bars.
Overhead cranes are highly valued for their efficiency and safety, as they can quickly move heavy loads and are especially useful in environments where it’s unsafe for humans to carry materials. They are widely used in various industries such as manufacturing, warehousing, automotive, and any application where heavy materials must be moved horizontally across a facility. Customization options in size, shape, and lifting capacity allow businesses to choose overhead cranes best suited for their specific material handling needs.

5. Floating Crane
A floating crane is a specialized type of crane that is mounted on a barge or a boat, allowing it to perform heavy lifting tasks in water-based environments. They are essential equipment for maritime construction projects, port activities, and offshore industries.
Key Components and Features:
- Floating Platform: The crane is mounted on a floating platform such as a pontoon, barge, or specially designed vessel. This platform needs to be stable and sturdy enough to withstand the weight and operation of the crane and the additional load of the materials being lifted.
- Crane Structure: The crane can have various designs, including lattice boom, telescopic boom, or tower crane. The choice depends on the nature of the work, the weight of the loads, and the height and reach required.
- Swing Base: Some floating cranes are mounted on a swing base, allowing the crane to rotate in a full circle and provide versatile lifting and moving capabilities.
- Power Source: Floating cranes often have diesel generators to power the crane’s operations. Some are equipped with different propulsion systems that allow the vessel to navigate water bodies.
- Controls and Operator Cabin: The crane is operated from a cabin on the crane structure, with controls for lifting, lowering, swinging, and other crane movements.
- Counterweights: Like all cranes, floating cranes use counterweights to balance the load and prevent the crane from tipping.
Floating cranes are primarily used in offshore construction, such as the building of bridges, ports, and oil rigs. Their lifting capacity and ability to operate in water make them indispensable in these sectors. They’re also used for loading and unloading heavy cargo in ports or for salvaging sunken ships or objects.
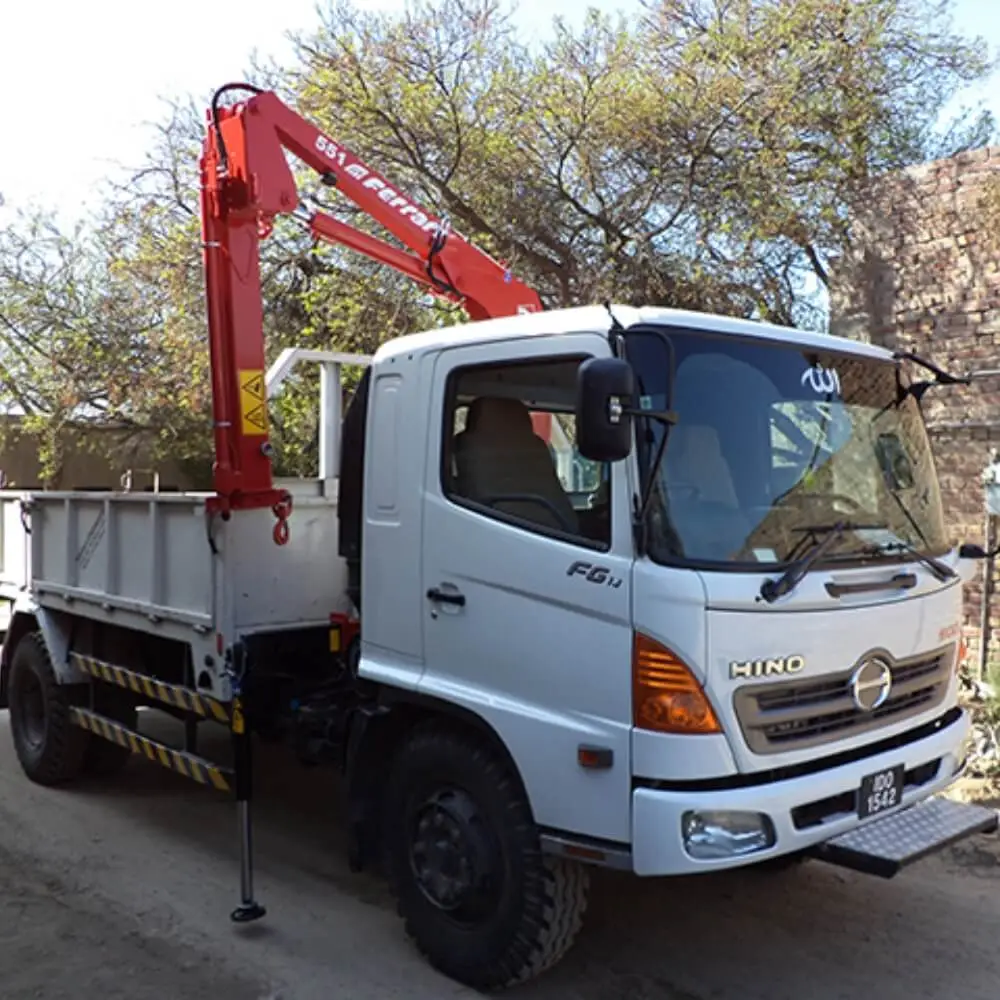
6. Truck Mounted Crane
A Truck Mounted Crane, also known as a lorry loader crane or a boom truck, is a truck that has a crane mounted on its chassis, typically just behind the cab or at the rear. It’s a versatile piece of equipment that combines the functionalities of a truck and a crane, and is used for loading, unloading, and transporting goods.
Here are the key components and features:
- Truck Chassis: The base of a truck-mounted crane is a standard truck chassis modified to bear the weight of the crane and the load it will lift.
- Crane: The crane is usually a hydraulic crane that is either telescopic for handling loads in a confined space or articulated for added flexibility.
- Operator’s Cabin: Depending on the design, the operator might control the crane from inside the truck’s cabin, or a separate operator’s seat might be attached to the crane.
- Stabilizing Outriggers: These are extendable legs that move vertically or horizontally and stabilize and level the crane during hoisting operations. They are crucial for safety.
- Loading Area: The truck has a deck or loading area for carrying goods. The crane can load and unload goods onto this area at the destination.
- Power Source: The crane is usually powered by the truck’s engine through a hydraulic pump, though some models have a different engine for the crane.
Truck Mounted Cranes are classified into three types based on the chassis:
- Single Vehicle: The crane is mounted on a regular truck or a specialized vehicle like a flatbed. This type is known for its maneuverability and is suitable for locations with narrow or winding roads.
- Semi-Trailer Type: In this type, the crane is mounted on a semi-trailer towed by a tractor. The crane usually gets hydraulic power from the tractor. This type can handle heavier loads but is less maneuverable than the single-vehicle type.
- Semi-Trailer Tractor Type: The crane is installed on the tractor itself, allowing it to be more independent. The crane used in this type is often foldable due to the space constraints caused by the towed vehicle (semi-trailer).
Truck-mounted cranes are widely used in various industries, including construction, logistics, and manufacturing. They are favored for their ability to quickly move to different locations and immediately carry out lifting operations without requiring extensive setup.
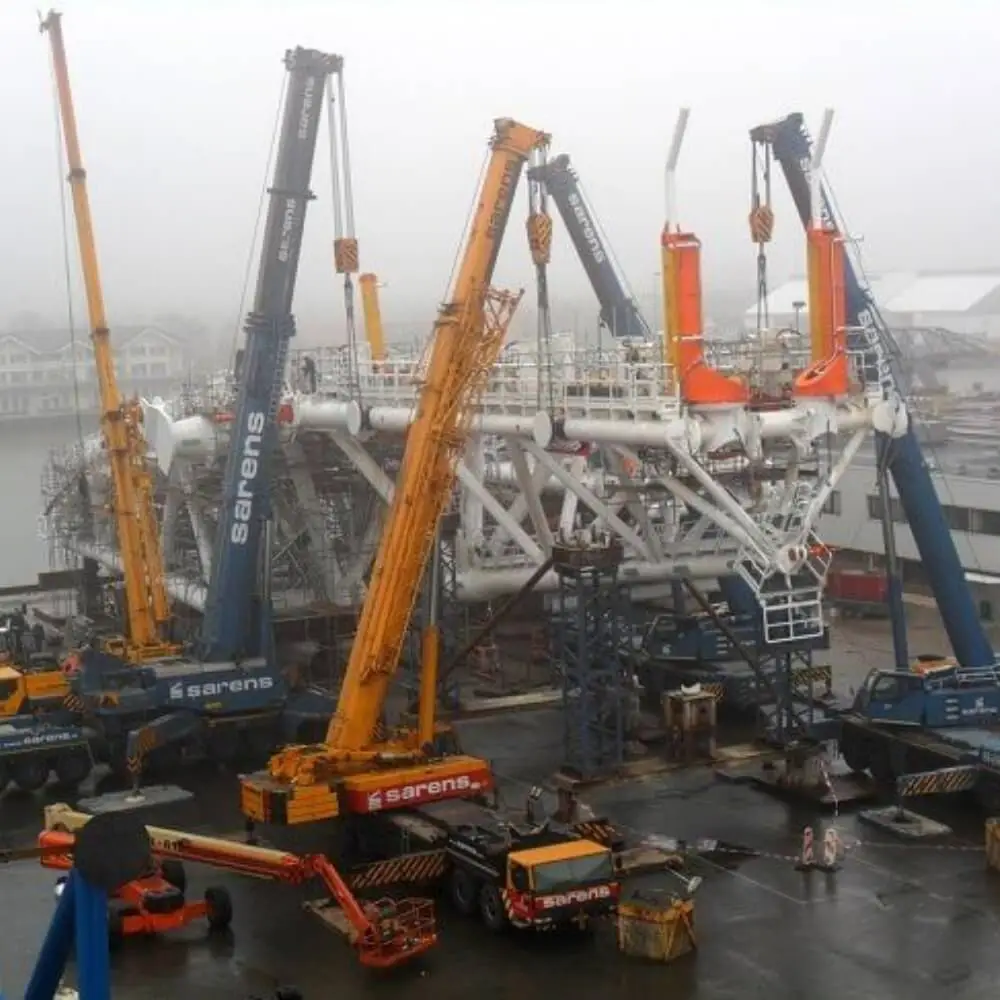
7. Telescopic Crane
A telescopic crane is a type of crane that is used for hoisting and moving loads. Its primary feature is its telescopic boom, which can extend or retract to change the overall length and reach of the crane. This adaptability makes it extremely versatile, particularly in applications requiring varying heights and distances.
Here are the key components and features of a telescopic crane:
- Telescopic Boom: The most distinctive feature of a telescopic crane is its boom, which comprises several tubes fitted inside each other. These can be extended or retracted hydraulically, allowing the crane to change its height and reach.
- Mobile Chassis: Most telescopic cranes are mounted on a mobile chassis, either a truck or a crawler base. This makes them highly mobile and able to quickly move to different locations.
- Counterweights and Outriggers: Telescopic cranes are equipped with counterweights and extendable outriggers to stabilize the crane during lifting operations. This ensures the safety and stability of the crane, especially when the boom is fully extended.
- Operator’s Cabin: The crane is operated from a cabin, where the operator has controls to manage the movement of the crane, the extension of the boom, and the hoisting operations.
- Hoist and Hook: The end of the boom is equipped with a hoist and hook, which is used to lift and move loads. The hoist is generally a wire rope wound around a drum, and the hook attaches the load.
- Hydraulic System: The extension and retraction of the telescopic boom are achieved through a hydraulic system. The hydraulics provide the necessary force to move the sections of the boom.
Telescopic cranes are widely used in various industries, including construction, shipping, and logistics. They are particularly valuable in shipping ports due to their flexibility and efficiency. Ports are places where cargo is constantly being loaded and unloaded, often with varying sizes and weights. The ability of telescopic cranes to quickly adjust their boom length makes them ideal for handling different types of cargo. Furthermore, their mobility allows them to move around the port easily, transporting goods from ships to storage areas or vice versa. This combination of features makes telescopic cranes an essential tool in shipping ports’ efficient and smooth operation.
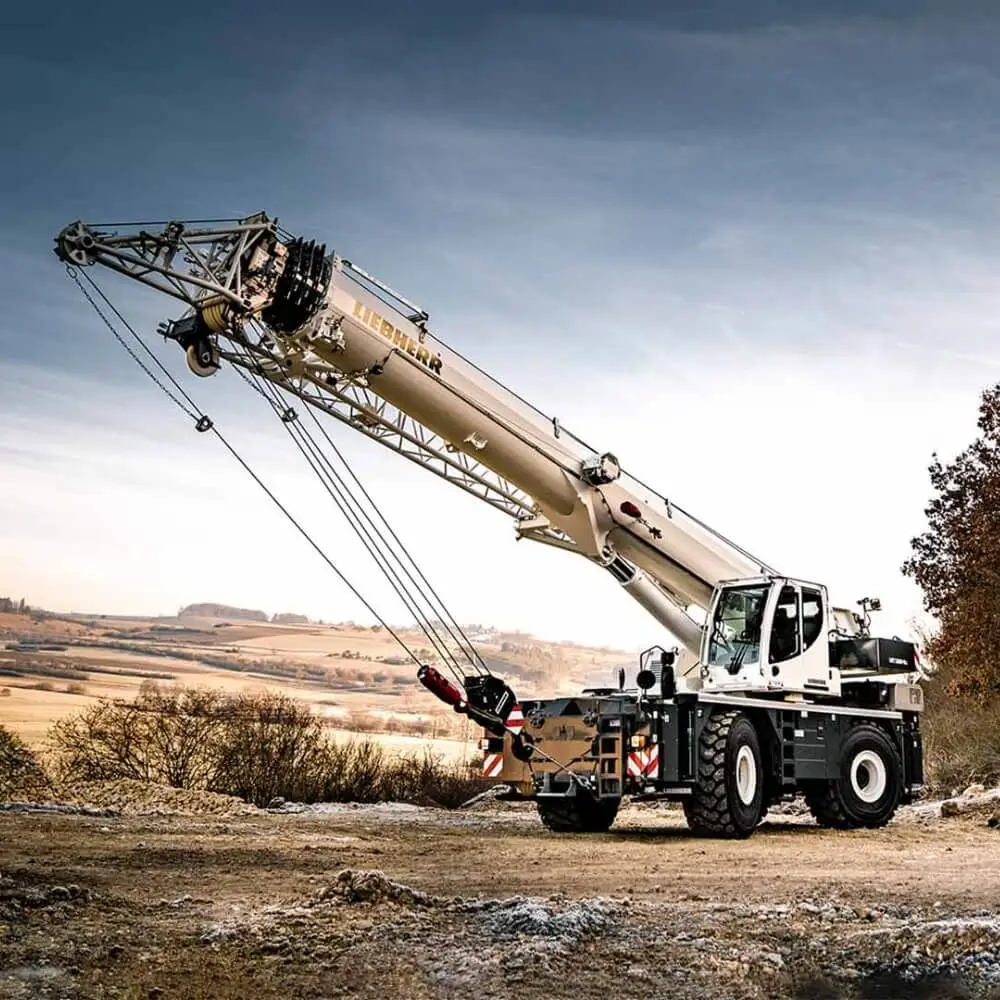
8. Rough Terrain Crane
A Rough Terrain Crane is a specialized crane designed specifically for operating on rough and uneven surfaces, usually in off-road applications such as construction sites. Its main features are its robust construction, high ground clearance, and ability to perform lifting operations in challenging environments. Here are the key components and features:
- Four-Wheeled Undercarriage: The rough terrain crane is mounted on a four-wheeled undercarriage with large, robust tires. These tires are generally wider and taller compared to standard tires to ensure better stability and higher ground clearance, which are crucial for navigating rugged terrain.
- Single Engine: Unlike some other types of cranes, rough terrain cranes typically have a single engine that powers both the crane and the undercarriage. This helps to reduce the crane’s weight and makes it more compact.
- Telescopic Boom: Similar to telescopic cranes, rough terrain cranes are equipped with a telescopic boom that can extend and retract to achieve varying heights and reaches. This is particularly useful in construction sites where space and access can be restricted.
- Outriggers: To ensure stability during lifting operations, rough terrain cranes are equipped with outriggers that extend horizontally and vertically from the base of the crane. These outriggers provide a stable platform and distribute the crane’s load over a larger area.
- Operator’s Cabin: Rough terrain cranes have a single, small cabin from where the operator can control both the movement of the crane and the lifting operations. This is in contrast to some larger cranes that have separate cabins for driving and for crane operations.
- Four-Wheel Drive and Steering: To navigate uneven ground, rough terrain cranes are equipped with four-wheel drive for better traction and power steering for maneuverability.
- Limited Road Mobility: One of the limitations of rough terrain cranes is that they are not designed for high-speed travel on public roads. This is due to their specialized tires and chassis which are optimized for stability on rough ground rather than speed. Consequently, they often need to be transported to and from job sites using other vehicles.
Rough terrain cranes are ideal for construction sites with uneven, unpaved surfaces and are particularly valuable in projects that involve the lifting and placement of heavy objects in such environments. Their combination of mobility, power, and stability makes them a versatile and invaluable piece of equipment in the construction industry.
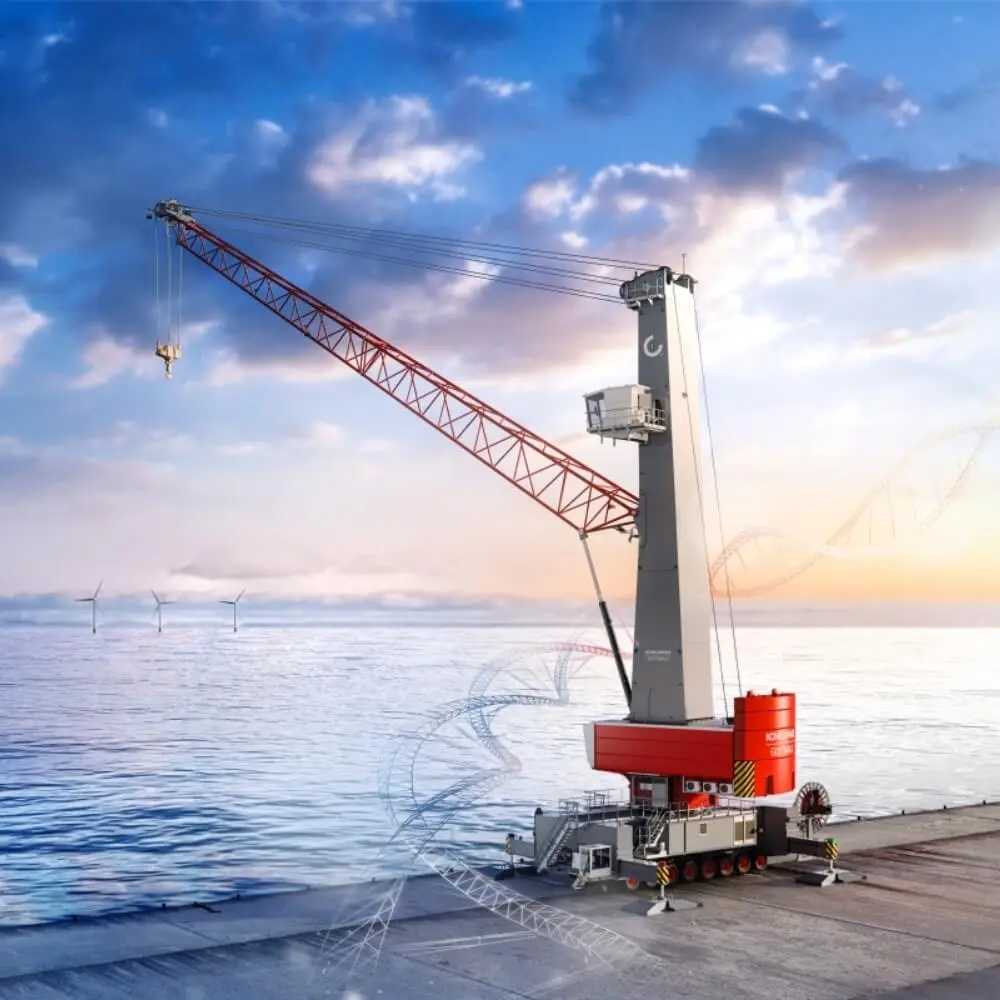
9. Harbor Crane
A harbor crane, often called a mobile harbor crane, is a type of crane specifically designed for use in port and harbor environments. It plays a crucial role in the loading and unloading of cargo from ships and is instrumental in the efficient functioning of seaports.
Here are the key components and features of harbor cranes:
- Mobility: Harbor cranes are often mobile, allowing them to move along the dock or port area. This mobility is essential for serving multiple berths or being repositioned based on the needs of the port.
- Versatility: Harbor cranes are versatile and can handle many cargo types, including containers, bulk materials, and general cargo. This makes them particularly valuable in ports that handle diverse shipping activities.
- High Lifting Capacity: Harbor cranes are known for their high lifting capacities, which are necessary for handling the large and heavy loads often associated with maritime shipping.
- Large Operating Range: Harbor cranes are equipped with long booms, which give them a large operating range. This allows them to reach across the width of large ships, making them capable of unloading cargo from vessels of various sizes, including capesize bulk carriers.
- Specialized Attachments: Depending on the type of cargo being handled, harbor cranes can be equipped with various attachments such as hooks, grabs, or spreaders. For instance, grabs are often used for handling bulk materials, while spreaders are used for shipping containers.
- Advanced Control Systems: Modern harbor cranes often feature advanced control systems that increase efficiency and safety. These systems can include automation features, precise control for handling delicate cargo, and safety systems to prevent accidents.
- Customization and Scalability: Harbor cranes come in different sizes and configurations, which can be chosen based on the specific requirements of the port. This includes cranes optimized for smaller vessels and those capable of handling the largest ships in the world.
In conclusion, harbor cranes are essential port equipment for efficient and safe cargo handling. Their mobility, versatility, and high lifting capacities make them ideally suited for the diverse range of tasks required in a port environment.
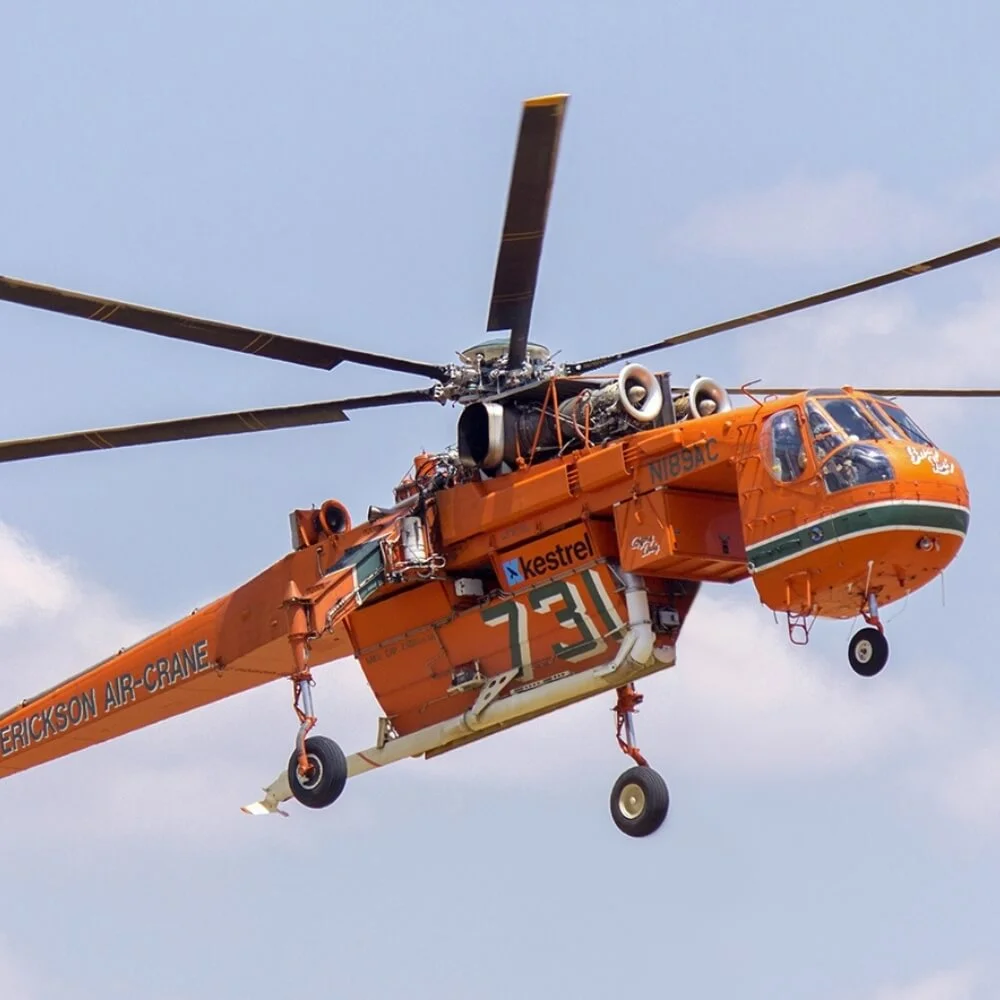
10. Aerial Crane
An aerial crane, a helicopter or sky crane, is modified or specially designed to lift and transport heavy loads. Unlike ground-based cranes, aerial cranes can quickly and efficiently move loads to and from inaccessible or impractical locations for conventional cranes or vehicles. Here are some key components and attributes of aerial cranes:
- Helicopter Base: The fundamental component of an aerial crane is a helicopter. The helicopter provides the lift and aerial mobility needed to transport heavy loads through the air.
- Lifting Gear: Attached to the helicopter is various lifting equipment, including hoists, hooks, cables, nets, and slings. These securely attach the cargo to the helicopter, ensuring it can be safely lifted and transported.
- High Lifting Capacity: Modern aerial cranes can lift very heavy loads. Initially, helicopters were limited in their lifting capacities, but technological advancements have led to the development of aerial cranes that can lift loads weighing up to 20 tons or more.
- Precision: One of the strengths of aerial cranes is their ability to precisely place loads, even in challenging or remote locations. This precision is facilitated by the maneuverability of the helicopter and the expertise of the pilot and crew.
- Versatile Applications: Aerial cranes are used in various sectors, including construction, utility, forestry, and disaster relief. They are particularly valuable for placing heavy equipment on rooftops, installing power line towers, or delivering supplies to remote areas.
- Cost and Time Efficient: For certain applications, using an aerial crane can be more time and cost-effective than building access roads or setting up ground-based cranes.
- Military Origins: As mentioned, the military initially used aerial cranes for lifting and transporting heavy loads. This technology was later adapted for civilian uses as its mobility and lifting capacity benefits were recognized.
- Safety and Regulations: Operating an aerial crane requires adherence to stringent safety standards and regulations. The safety considerations include not only the operation of the helicopter but also the secure attachment and handling of the loads being lifted.
In summary, an aerial crane combines a crane’s lifting capabilities with a helicopter’s mobility and flexibility. This combination makes it a powerful tool for a wide range of applications, especially where access is difficult, or speed is of the essence.
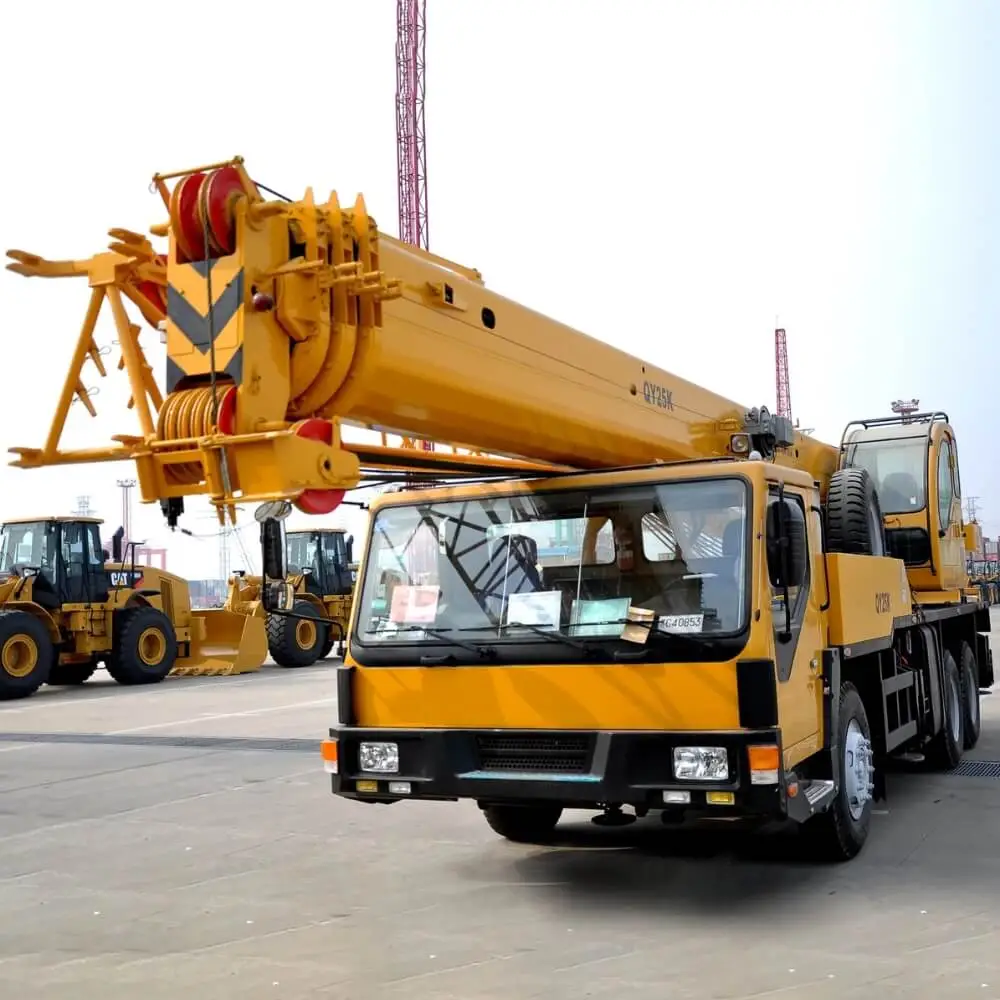
11. Hydraulic Crane
A hydraulic crane is a type of crane that uses a hydraulic system to generate the force needed to lift heavy loads. This type of crane is widely used in construction, transportation, and other industries due to its reliability and capacity to lift heavy materials. Below are the key components and characteristics of hydraulic cranes:
- Hydraulic System: The most defining feature of a hydraulic crane is its hydraulic system. The system includes a pump that moves hydraulic fluid (usually oil), cylinders that use the fluid to create mechanical force, and various valves to control the fluid flow. Since fluids are nearly incompressible, hydraulic systems are highly efficient at transferring force.
- Boom: The hydraulic crane has an arm, known as a boom, used to lift and lower materials. Some hydraulic cranes have a telescopic boom that can be extended to reach greater distances and heights.
- Operator’s Cab: The operator’s cab is where the crane operator sits and controls the crane’s movements. It is equipped with controls to operate the boom and the hydraulic system.
- Base and Mobility: Hydraulic cranes can be stationary or mobile. Mobile hydraulic cranes are mounted on tracks or wheels, which allow them to be moved to different locations. The crane base is usually equipped with outriggers to stabilize the crane during lifting operations.
- Lifting Mechanism: A set of cables, hooks, and sometimes a winch is attached to the boom. These components are used to attach the load to the crane and to lift or lower it.
- Power Source: A hydraulic crane is powered by an engine that drives the pump. The pump pressurizes the hydraulic fluid, creating the force needed for the crane’s movements.
- Load Capacity: Hydraulic cranes are rated based on their maximum lifting capacity. The crane mustn’t be overloaded beyond its rated capacity, as it can cause catastrophic failure.
- Versatility and Applications: Hydraulic cranes can be used in various applications, including construction, shipping, manufacturing, and more. Their ability to lift heavy loads makes them invaluable in settings where large, heavy objects need to be moved.
- Safety Concerns: Operating a hydraulic crane requires specialized training. Given their loads’ large size and weight, any mistakes can have serious consequences. Safety procedures and proper maintenance are crucial for safely operating hydraulic cranes.
In summary, a hydraulic crane is a powerful piece of equipment that utilizes a hydraulic system to lift and move heavy loads. Its strength and versatility make it an essential tool in various industries, but it also requires careful handling and operation due to the inherent risks associated with lifting heavy objects.
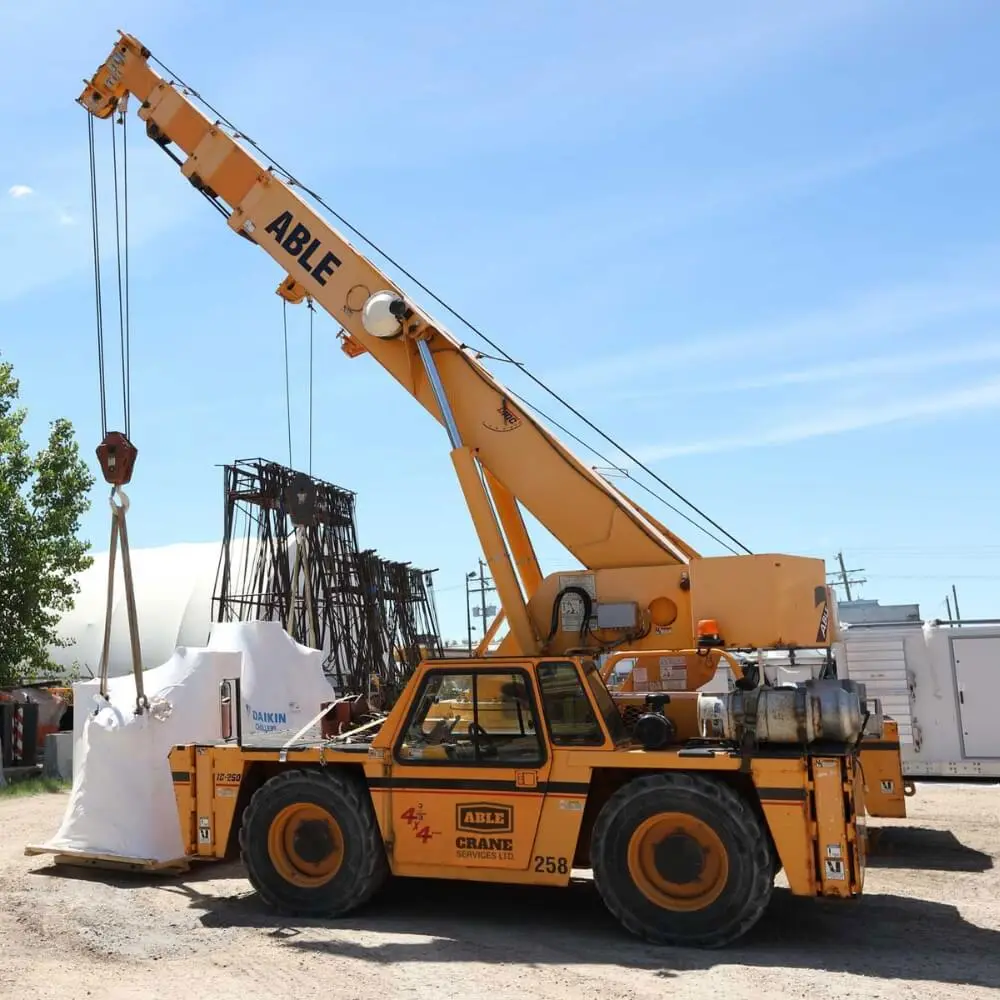
12. Carry Deck Crane
A Carry Deck Crane is a type of mobile crane that is compact, versatile, and designed for lifting material in tight spaces where traditional cranes wouldn’t fit. The defining features of a Carry Deck Crane include a 360-degree rotating boom, a flat deck, a compact design, and the ability to maneuver in confined spaces. Below is an explanation of its key components and functionalities:
- 360-Degree Rotating Boom: One of the primary features of a Carry Deck Crane is its centrally-located boom that can rotate 360 degrees. This offers excellent maneuverability and flexibility in lifting and placing loads precisely.
- Carry Deck: As its name suggests, the crane features a flat deck that can carry materials. This is particularly useful in transporting loads in confined spaces or moving materials short distances on a job site.
- Compact Design and Low Profile: Carry Deck Cranes are known for their compact design and low profile, which allows them to operate in tight spaces and navigate under overhead obstructions such as building eaves or power lines.
- Operator Cab: Typically located at one end of the crane, the operator cab is where the crane operator controls the machine. It is equipped with controls for operating the crane’s boom, deck, and movement.
- Hydraulic Controls: These cranes are often equipped with hydraulic controls that provide smooth and precise boom operation and other functionalities. This allows for accurate placement of loads even in constrained environments.
- Load Capacity: Carry Deck Cranes can typically handle loads of several tons. They are designed for lifting and carrying heavy materials, and their capacities can vary depending on the model and configuration.
- Versatility in Applications: Due to their compact design and ability to maneuver in tight spaces, Carry Deck Cranes are highly versatile and are used in various applications, including construction sites, industrial environments, and any setting where space is limited.
- Mobility and Navigation: The four wheels and steering capabilities allow for ease of mobility around the job site. Carry Deck Cranes can be quickly repositioned to perform various tasks without requiring extensive setup.
- Material Handling and Transport: One of the primary uses of Carry Deck Cranes is material handling and transport within a job site. Materials can be lifted using the boom and placed directly onto the deck for transport to another location.
In summary, a Carry Deck Crane is a highly versatile and compact mobile crane designed for lifting and transporting materials in environments where space is limited. Its ability to rotate its boom 360 degrees and its low profile and flat deck for carrying materials make it an invaluable tool for many construction and industrial applications.
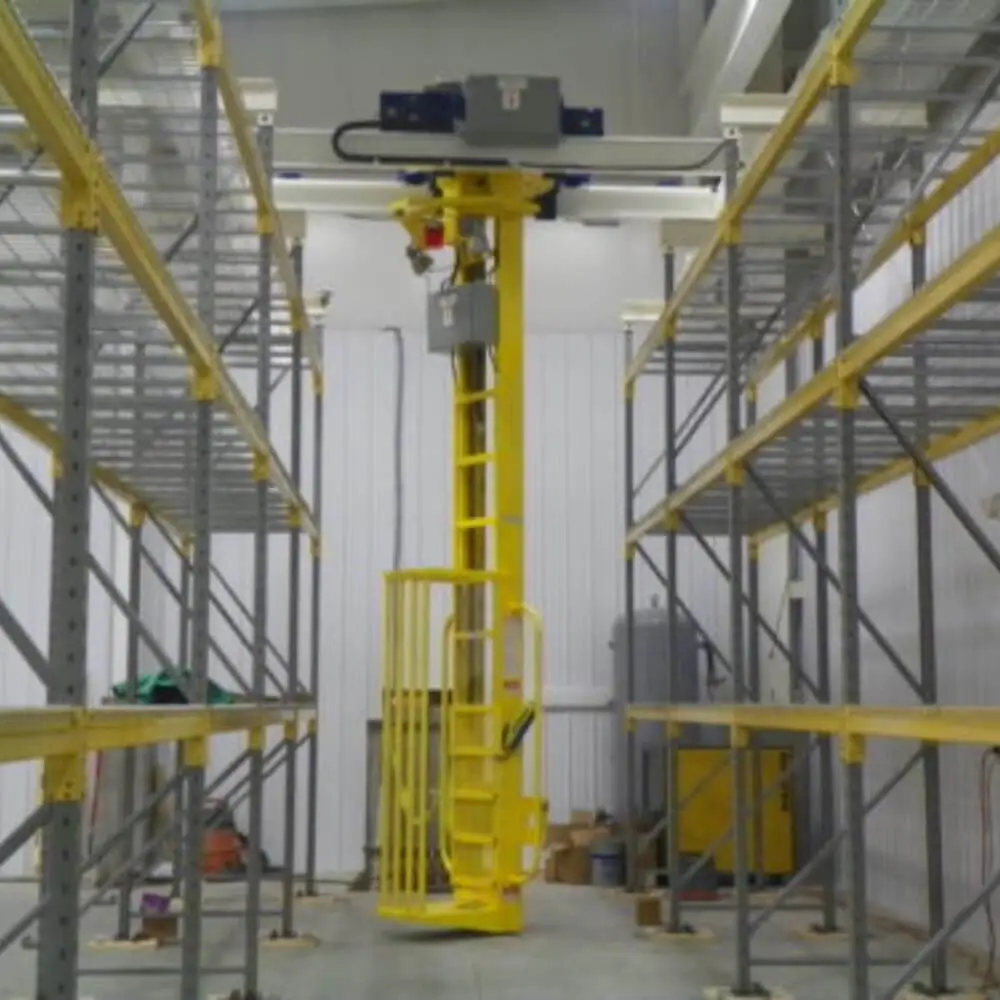
13. Stacker Crane
A stacker crane is a specialized piece of equipment used primarily in automated storage and retrieval systems (AS/RS) within warehouses and distribution centers. Its main purpose is to place and retrieve goods from storage shelves or racks efficiently and precisely. Here are the key components and functionalities of a stacker crane:
- Load Handling Device: The stacker crane usually has a non-hoist load handling device mounted on a mast, such as forks or a gripper. This device is designed to pick up, carry, and place items on storage racks.
- Guide Rails: Stacker cranes operate along guide rails usually mounted within the storage aisles. These rails ensure that the crane moves precisely and safely along predetermined paths.
- Bridge Trolley: The mast or load-handling device is typically suspended from a bridge trolley that moves horizontally along the crane’s bridge. This trolley enables the crane to reach different positions within the aisle.
- Vertical Mast: The vertical mast allows the load-handling device to move up and down to reach different heights within the storage racks. This is essential for making use of vertical space in warehouses.
- Electrical Supply System: Stacker cranes are typically electrically powered and have a supply system that provides power to the motors and control systems. This allows for continuous operation without the need for refueling or recharging.
- Data Transmission/Control System: One of the defining features of a stacker crane is its integration with automated control systems. These cranes can be controlled remotely or programmed to perform tasks autonomously based on data from the warehouse management system. This automation is crucial for improving efficiency, accuracy, and throughput in modern warehouses.
- Travel Motion: Stacker cranes are capable of horizontal (along the aisle) and vertical (up and down) movements. This allows them to access storage locations at various heights and positions within the storage racks.
- Safety and Precision: These cranes are designed for high levels of precision and safety. They often include sensors and safety systems to avoid collisions and handle loads securely.
In summary, a stacker crane is an integral part of automated storage and retrieval systems, designed to handle goods in warehouses with high efficiency, accuracy, and safety. By automating the process of storing and retrieving items, stacker cranes can significantly improve the utilization of space and streamline warehouse operations.
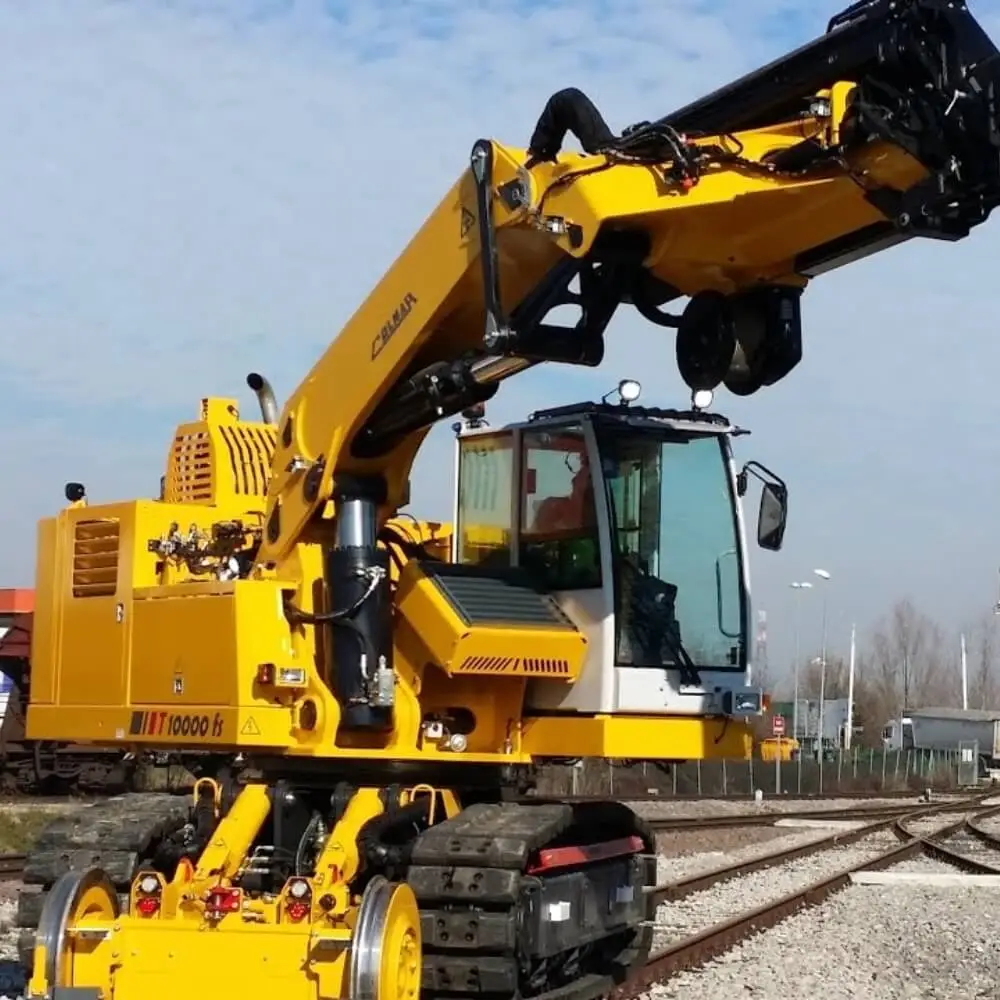
14. Railroad Crane
A railroad crane, often called a crane car, is a specialized crane designed for use on railway tracks. It serves various purposes, including accident recovery, track maintenance, and freight handling at goods yards. Here are the key components and functionalities of a railroad crane:
- Rotating Crane Body: The railroad crane features a rotating crane body mounted on a sturdy chassis. This body houses the operating mechanisms and supports the boom, allowing it to swivel and reach different areas around the tracks.
- Boom: Similar to other types of cranes, the railroad crane has a boom which is an extendable and often adjustable arm used for lifting and moving materials. The boom can be telescopic or lattice depending on the design and requirement.
- Chassis with Railway Gear: The chassis of the railroad crane is specifically designed to be used on railway tracks. It has railway wheels and gear that allow it to move along the tracks. This enables the crane to be transported to different locations along the railway where its services are needed.
- Power Source and Propulsion: Some railroad cranes are self-propelled, meaning they have their own engines and can move independently, while others need to be moved by a locomotive. The self-propelled versions offer more flexibility and can be used more efficiently for maintenance and repair tasks.
- Controls and Cabin: The crane is operated from a cabin that is usually located on the rotating crane body. This cabin houses the controls for operating the boom, rotating the crane, and sometimes for moving the crane along the tracks.
- High Lifting Capacity: Railroad cranes are typically designed to deal with heavy loads with high lifting capacities. This is particularly important in accident recovery situations, where they may be required to lift derailed train cars or in goods yards to load and unload heavy freight.
- Stabilizers and Outriggers: To ensure stability during lifting operations, especially heavy lifting, railroad cranes are equipped with stabilizers or outriggers that can be extended to provide a more stable base for the crane.
- Uses: The primary uses of railroad cranes include recovery work following accidents (such as re-railing derailed train cars), maintenance of the tracks and surrounding infrastructure, and loading and unloading of freight in goods yards.
In summary, a railroad crane is an essential piece of equipment for railway operations, providing the necessary lifting power and mobility to handle various tasks along railway tracks efficiently and safely.
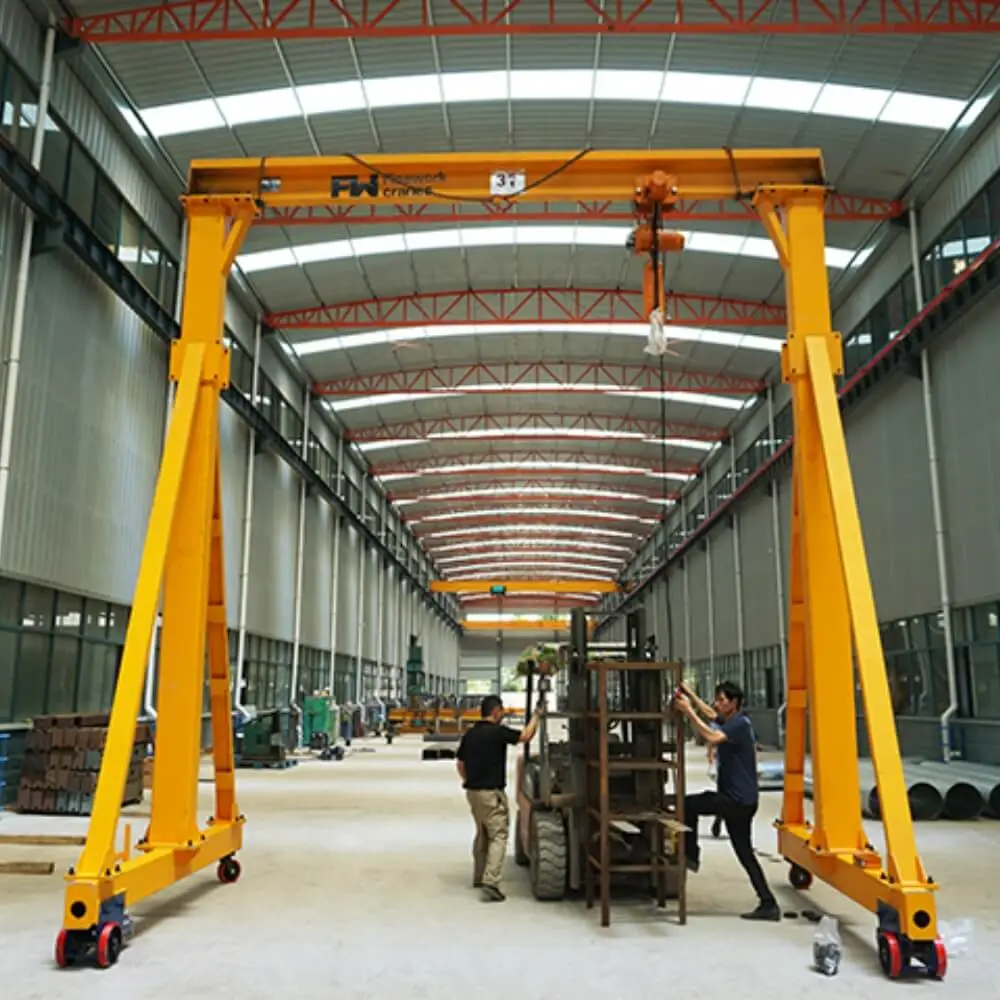
15. Gantry Crane
A Gantry Crane is a type of overhead crane that is used to lift and move heavy objects. It is characterized by a large, tall frame consisting of two or more legs running on rails or wheels, with a bridge across the top.
Here are the key features and applications of Gantry Cranes:
- Structure: The gantry crane’s structure is essentially a large frame or a gantry that supports a hoist, trolley, and other lifting mechanisms. This frame is positioned above the area where the lifting is required, and the trolley moves back and forth along the bridge. The legs of the gantry crane run parallel to the ground and can be mounted on rails or wheels to allow for lateral movement.
- Types and Sizes: There are various gantry cranes, including full gantry cranes, semi-gantry cranes, portable gantry cranes, and adjustable gantry cranes. Full gantry cranes have a bridge supported by legs running on rails, while semi-gantry cranes have one leg running on a rail and the other supported by a structure like a wall or building. The sizes can range from small, portable units used in workshops to enormous cranes used in shipyards for lifting large containers and ship parts.
- Applications: Gantry cranes are widely used in various industries, such as shipping, construction, and manufacturing. They are especially useful in applications where heavy loads, such as shipyards, warehouses, and industrial plants, must be moved over a defined area. In shipyards, they are often used to lift containers on and off ships. In manufacturing, they are used for assembling heavy machinery or moving materials.
- Capacity and Safety: Gantry cranes can lift heavy loads, often several tons or more. Safety is a crucial concern with gantry cranes because of the heavy loads and heights. Operators must be well-trained, and the cranes must be regularly maintained and inspected to ensure they are in good working condition.
- Advantages: Gantry cranes offer several advantages, including high lifting capacities, the ability to cover a large area, and versatility in handling different loads. They can be especially useful when an overhead building structure is unavailable to support an overhead crane.
Conclusion
In conclusion, cranes are an integral part of the construction, manufacturing, and logistics industries, providing the capability to lift, move, and handle heavy loads with precision and efficiency. Throughout this guide, we have explored 15 different types of cranes used worldwide, each tailored to specific tasks and environments. From towering tower cranes that oversee the construction of skyscrapers to agile mobile cranes that navigate various terrains, these engineering marvels have transformed how we build and transport. With their diverse capabilities and applications, cranes continue to play a crucial role in shaping industries around the globe, facilitating the development of monumental structures and the smooth flow of goods and materials.