In the ever-evolving world of construction and engineering, excavation is pivotal in shaping the foundation of countless projects. Whether it’s the groundwork for a residential building or laying the infrastructure for a complex industrial site, excavation is often the first step in bringing a concept to life. However, as with any construction activity, excavation has its fair share of risks and challenges. Ensuring workers’ safety and the excavated area’s stability is paramount. Trench collapses, falling debris, and other related hazards have the potential to cause serious harm, making excavation protection an indispensable aspect of any excavation project.
This enlightening blog post will delve into the three primary methods of excavation protection – Sloping, Shoring, and Shielding. Each technique serves a unique purpose and comes with its own considerations. From understanding the nuances of soil types and trench depths to selecting the most appropriate protective gear and equipment, this guide will equip you with the knowledge to make informed decisions and prioritize safety in your excavation endeavours. Join us as we dig deep into the world of excavation protection!
Excavation Protection Methods | Sloping, Shoring & Shielding
When doing excavation work, protecting workers from potential hazards is important. There are three primary methods of excavation protection: sloping, shoring, and shielding.
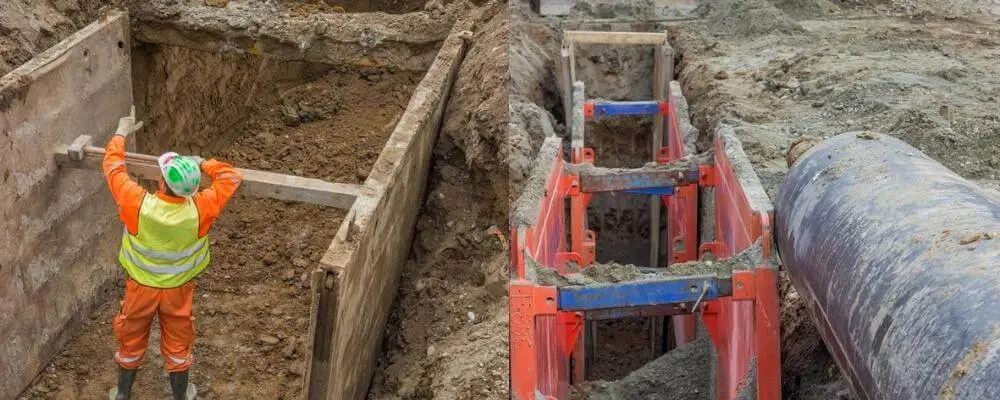
1. Sloping
Sloping is cutting back the trench wall at an angle inclined away from the excavation. Sloping is typically used to improve stability and prevent collapse. It can also be used to improve drainage and reduce the risk of waterlogging. Slopes can be created using various methods, including manual labour, machinery, or a combination.
Sloping is an important part of trenching operations and should be carried out carefully to ensure workers’ safety and the trench’s stability. Sloping can be complex, and several factors must be considered before starting work.
- The angle of the slope,
- The type of soil,
- The depth of the trench, and
- The weather conditions all need to be taken into account.
Sloping should only be carried out by experienced workers familiar with the risks involved.
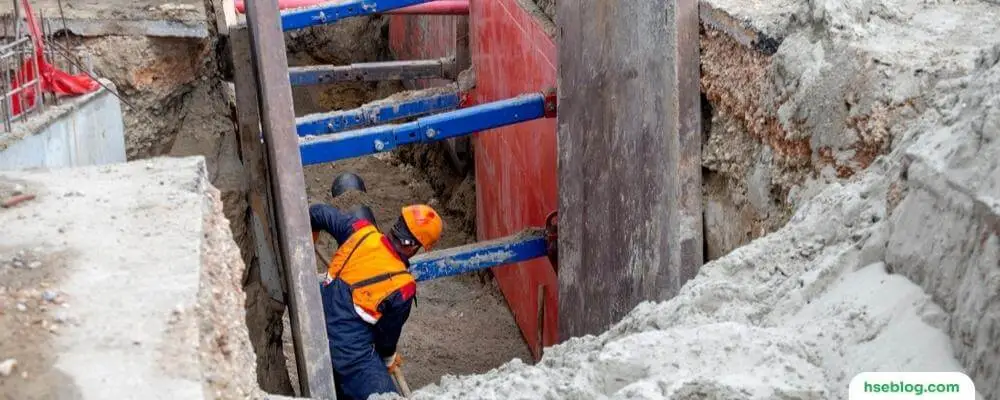
2. Shoring
Shoring is the process of installing aluminium hydraulic or other types of supports to prevent soil movement and cave-ins. This is often necessary when excavating a trench or working where the ground may give way. Shoring can also stabilize a structure damaged by an earthquake or other disaster.
Shoring is a critical part of construction and should only be done by trained professionals. Improper shoring can lead to serious injuries or even death. If you plan to do excavation work, ensure that you have a shoring plan in place and that all workers know the dangers involved.
Types of Shoring Methods
Common shoring methods include:
- Soldier Pile and Lagging
- Pressure / Chemical Grouting
- Soil Nails and ShotCrete
- Hydraulic Shoring
- Pneumatic Shoring
- A choice of Timber or Aluminium materials
- Soldier Pile and Lagging: This traditional shoring method has been used for centuries. Soldier piles are driven into the ground, and then lagging (planks of wood) are placed between the piles to create a wall. This method is often used in deep excavations or where there is a risk of the soil collapsing.
- Pressure / Chemical Grouting: This method involves injecting grout (concrete) into the soil to fill voids and cracks. This helps to stabilize the soil and prevent it from moving. Chemical grouting is often used in areas with a risk of sinkholes forming.
- Soil Nails and ShotCrete: Soil nails are metal rods driven into the ground. Shotcrete is then applied to the face of the excavation. This method is often used in areas with rockfalls or unstable soil risk.
- Hydraulic Shoring: Hydraulic shoring uses hydraulic jacks to support the sides of an excavation. This method is often used in deep excavations or where there is a risk of the soil collapsing.
- Pneumatic Shoring: Pneumatic shoring uses airbags to support the sides of an excavation. This method is often used in deep excavations or where there is a risk of the soil collapsing.
- Timber or Aluminium: Timber is the most common shoring material, but aluminium is sometimes used. Timber is cheaper than aluminium and is easier to work with, but it is not as strong. Aluminium is more expensive but much stronger and can be used in areas where timber is unsuitable.
When choosing a shoring method, you need to consider the following factors:
- The type of soil you are dealing with
- The depth of the excavation
- The width of the excavation
- The risk of the soil collapsing
- The weight of the equipment and materials that will be stored in the excavation
- The length of time the shoring will be needed for
- Your budget
- Your experience level
If you plan to do excavation work, ensure that you have a shoring plan in place and that all workers know the dangers involved. Improper shoring can lead to serious injuries or even death.
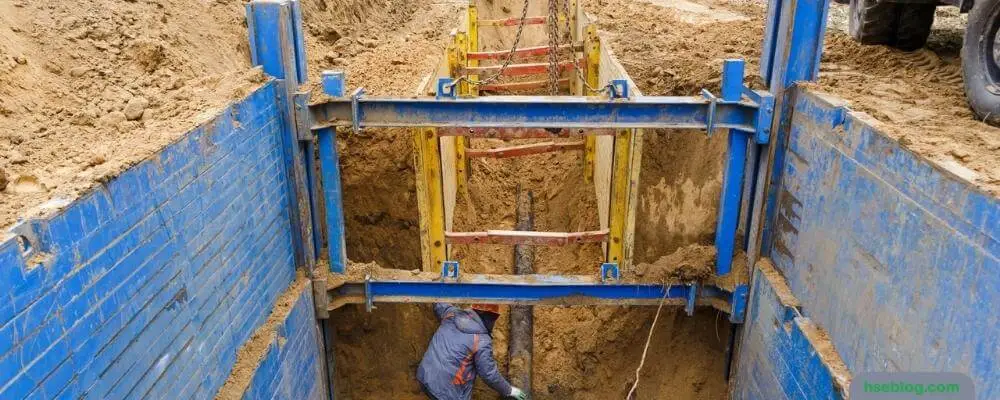
3. Shielding
Shielding is the process of protecting workers from falling debris or being hit by equipment. Shielding can be done with barriers, nets, or other protective devices.
- Barriers: Barriers can be made of wood, metal, or concrete. They are placed around the perimeter of an excavation to prevent people and equipment from falling into the hole.
- Nets: Nets are made of strong, flexible material around an excavation’s perimeter. They catch falling debris and prevent it from hitting people or equipment.
- Protective Devices: Protective devices shield workers from falling debris or being hit by equipment. These devices can be made of wood, metal, or concrete.
There are many ways to protect workers from the dangers of cave-ins while working in an excavation. One common method is to use trench boxes or other types of supports to prevent the soil from caving in. Trench boxes are metal or wooden structures placed around an excavation’s perimeter. They act as a barrier between the workers and the soil, preventing the soil from collapsing and burying the workers.
Other supports that can be used to prevent cave-ins include shoring, a system of support beams placed around the perimeter of an excavation, and nets placed over the top of the excavation to catch any falling soil. Cave-ins are a serious hazard in excavation work, but they can be prevented using proper safety precautions. Workers can stay safe and avoid being buried alive using trench boxes or other types of support.
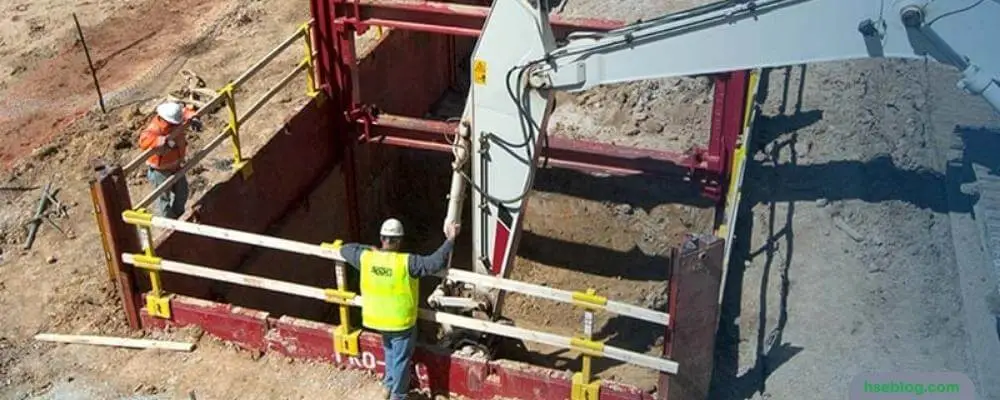
Shielding Types
- Trench Boxes: Trench Boxes differ from shoring because they are intended primarily to protect workers from cave-ins and similar incidents instead of shoring up or supporting the trench face. The excavated area between the trench box’s outside and the trench’s face should be as small as possible. The space between the trench boxes and the excavation site is backfilled to prevent lateral movement of the box. Shields may not be subjected to loads exceeding the system’s designed to withstand.
- Combined Use: Trench boxes are generally used in open areas but may also be used with sloping and benching. The box should extend at least 18 in (0.45 m) above the surrounding area if there is sloping toward the excavation. This can be accomplished by providing a benched area adjacent to the box.
Earth excavation to a depth of 2 ft (0.61 m) below the shield is permitted, but only if the shield is designed to resist the forces calculated for the full depth of the trench and there are no indications. In contrast, the trench is open to possible soil loss from behind or below the bottom of the support system. Conditions of this type require observation of the effects of bulging, heaving, and boiling, as well as surcharging, vibration, adjacent structures, etc., on excavating below the bottom of a shield. Careful visual inspection of the above conditions is the primary and most prudent approach to hazard identification and control.
Conclusion
In conclusion, prioritizing safety and stability is non-negotiable regarding excavation. By adeptly applying sloping, shoring, and shielding, one can significantly mitigate the risks associated with excavation projects. By understanding the site’s characteristics, including soil type and weather conditions, and by employing the appropriate protection methods, construction professionals can create a secure environment for workers and ensure the structural integrity of the excavation.
Continuous assessment and adherence to safety standards are crucial in navigating the complexities of excavation work, making these protection methods essential tools in the arsenal of any construction or engineering project.