Crane operations are critical to many industries, including construction, shipping, and logistics. These towering structures bear enormous weight and are meticulously engineered for safe and efficient load handling. However, as robust as these machines may be, they are not immune to failure. Given their pivotal role, any failure can result in significant downtime, costly repairs, and catastrophic accidents leading to loss of life in worst-case scenarios.
In this blog post, we will explore the five most common causes of crane failure – wire issues, slew bearing failures, sheave problems, mishandling, and misconceptions about maintenance – in detail. We will also discuss the often-overlooked factors that can lead to these issues, emphasizing the crucial role of preventive measures in mitigating the risk of crane failure. With an understanding of these common issues and preventative strategies, owners and operators can ensure safer and more reliable crane operations.
Whether you’re a crane operator, a ship owner, a safety officer, or just someone curious about the intricacies of these mechanical giants, this post will provide insights and practical tips to help understand and prevent crane failures. Let’s start our deep dive into the world of crane safety.
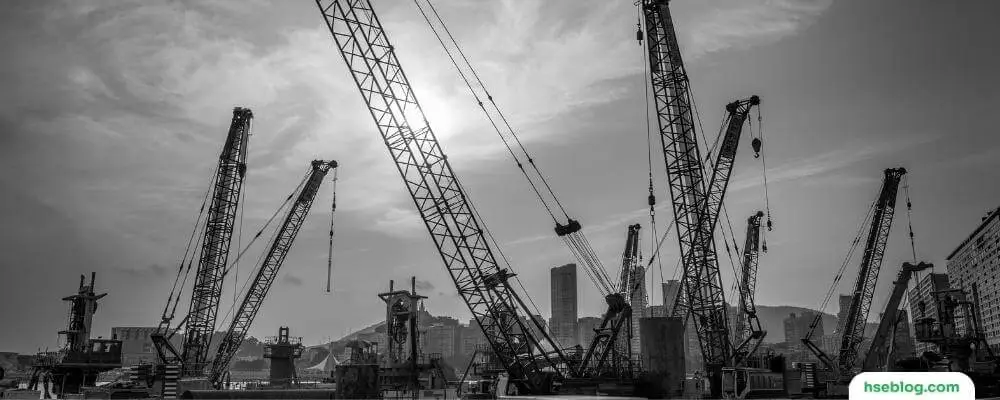
Five Common Causes of Crane Failure
Crane failure can occur for various reasons, including mechanical failures, structural issues, operator errors, environmental factors, and inadequate maintenance. Here are five common causes of crane failure:
1. Wires
Crane wires, often referred to as wire ropes, play a vital role in the functioning of cranes. They bear the load and facilitate the movement of the crane arm. However, several reasons can lead to wire failures:
- Overloading: Cranes are designed to lift specific maximum loads. Exceeding this limit can cause undue stress on the wire ropes, leading to premature failure. This is often the result of operational errors or a lack of understanding of the crane’s capabilities.
- Fatigue: Wire ropes are subject to wear and tear over time, like any mechanical component. They are under constant tension, and every bend, every load lifted, induces stress. Over time, this can lead to the development of internal or external fractures, reducing their load-bearing capability and potentially leading to failure.
- Pre-existing defects: Sometimes, wire ropes can come with defects from the manufacturing process. These could include improper construction, inclusions, or wire or rope structure inconsistencies. Such defects may go unnoticed until put under stress during operation.
- Deterioration: Environmental factors can significantly affect the life span of wire ropes. For instance, exposure to corrosive substances or harsh weather conditions can cause the metal to deteriorate. This deterioration reduces the strength of the wire, making it more prone to snapping or breaking.
When wire failure occurs, the consequences can be severe. Most notably, whatever load the crane is lifting at the time can be dropped without warning, potentially causing damage to property or injury to personnel below. The failure can also damage the crane, requiring costly repairs or replacements. Therefore, regular wire ropes inspection and maintenance are crucial to prevent such incidents.
2. Slew Bearings
Slew bearings, sometimes called swing bearings, are critical components of a crane’s structure. They are large-diameter bearings that enable the crane to rotate horizontally. They bear the load of the crane’s superstructure and transfer the load to the undercarriage or mount, all while allowing the crane to rotate. Slew bearings must withstand enormous pressure and tension, so their failure can have serious consequences.
Problems with slew bearings generally stem from the following factors:
- Incorrect specification: The requirements of slew bearings differ depending on the crane’s operational requirements, such as load capacity, rotational speed, type of movement, and environmental conditions. If the slew bearing is not specified correctly to meet these requirements, it can lead to premature failure.
- Insufficient monitoring: Bearings need regular monitoring to ensure they are functioning correctly. This can involve regular inspection for visible signs of wear and tear, checking for unusual noise or vibrations, and monitoring temperature changes. If these signs of potential failure are not detected and addressed early, it could lead to catastrophic failure.
- Inadequate maintenance: To reduce friction and wear, slew bearings must be regularly lubricated. If this doesn’t happen, or if dirt and debris are allowed to accumulate, it can lead to increased wear and, ultimately, failure.
Failure of slew bearings can be severe, as they are critical for maintaining the balance of the crane. If they fail, it can cause the crane to lose its ability to distribute load evenly and in extreme cases, cause the crane to topple over. This can result in serious safety risks, including injury to personnel and significant property damage, as well as major financial implications due to the cost of repairing or replacing the crane, downtime, and potential lawsuits.
Therefore, it’s imperative to specify the right slew bearings for the intended use of the crane, monitor them closely during operation, and maintain them properly to ensure their longevity and reliability.
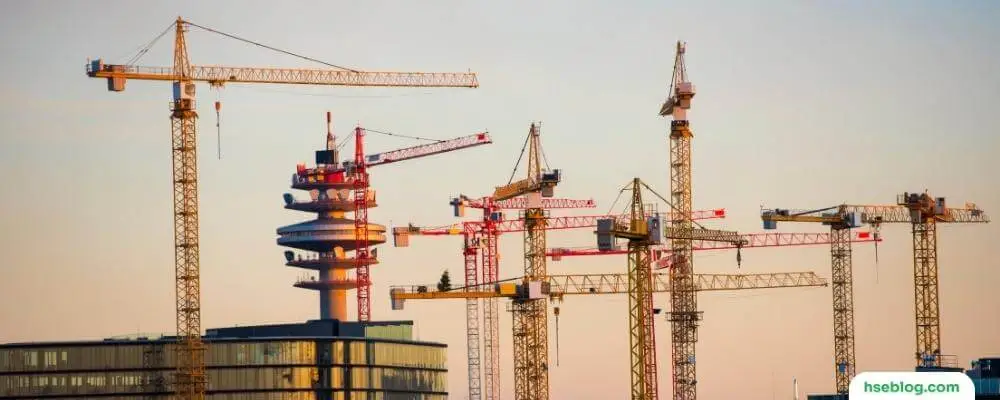
3. Sheaves
Sheaves are wheel-like parts of a crane where the wire rope runs. They help direct the wire rope and multiply the lifting force. The sheaves’ bearings need regular lubrication to reduce friction, prevent overheating, and prolong their service life. If this maintenance is neglected, it can lead to increased wear and tear on both the sheave bearings and the wire rope, potentially resulting in crane failure.
Remote greasing systems are often used to lubricate these bearings because they are typically located in high or hard-to-reach places on the crane. However, if these systems fall into disrepair, the task of greasing the bearings becomes much more complex and hazardous, requiring personnel to physically access the sheaves. This often involves the use of rigging to climb up the crane, which can be time-consuming and dangerous.
Unfortunately, when maintenance tasks become difficult, they are more likely to be overlooked or postponed. This can result in the bearings not receiving the necessary lubrication, causing them to wear out faster. Poor maintenance can also lead to misalignment of the sheaves, promoting abnormal and accelerated wire rope wear.
It’s important to note that sheave and wire rope wear are closely linked. Excessive wear or damage to the sheave can cause irregular wear or damage to the wire rope and vice versa. This is because the wire rope and sheave must fit together properly for the crane to operate efficiently and safely.
Therefore, it’s crucial that sheave maintenance is performed regularly and remote greasing systems are kept in good working condition to facilitate this. Otherwise, the risk of crane failure increases, potentially leading to significant financial losses, downtime, and even serious safety hazards.
4. Mishandling
Mishandling is another common cause of crane failure. The crane operators’ actions are critical in maintaining the safety and integrity of the crane operations. If not operated correctly, cranes can suffer various issues, including structural damage and failure, leading to dangerous and potentially disastrous consequences.
- Swinging Load: Swinging or sudden movements can cause the load to sway, which could destabilize the crane, and in the worst-case scenario, could lead to the crane toppling over. It also stresses the crane’s structural components and the wire ropes, leading to accelerated wear and tear and potential failure.
- Improper Load Handling: Overloading or improperly rigging a load can also lead to crane failure. Cranes are designed for specific maximum loads. Exceeding this limit can cause undue stress on the structure, leading to potential failure. Similarly, improperly rigged loads can cause uneven stress distribution, risking structural failure.
- Rapid Movements: Rapid or jerky movements can put sudden and excessive stress on the crane’s mechanical components, leading to premature wear and tear and potentially leading to structural failures.
- Lack of Maintenance: While not directly resulting from mishandling, poor maintenance habits often coincide with improper handling. A lack of regular inspections and maintenance can lead to small issues becoming major problems if left unaddressed.
To prevent mishandling, proper training for crane operators is essential. They should be fully aware of the crane’s operational limits and how to handle it correctly. Additionally, the actions of crane operators often stevedores in maritime settings, should be supervised and controlled by experienced personnel on board to ensure safe and correct operations. Regular maintenance and inspections also play a crucial role in preventing mishandling-related crane failures.
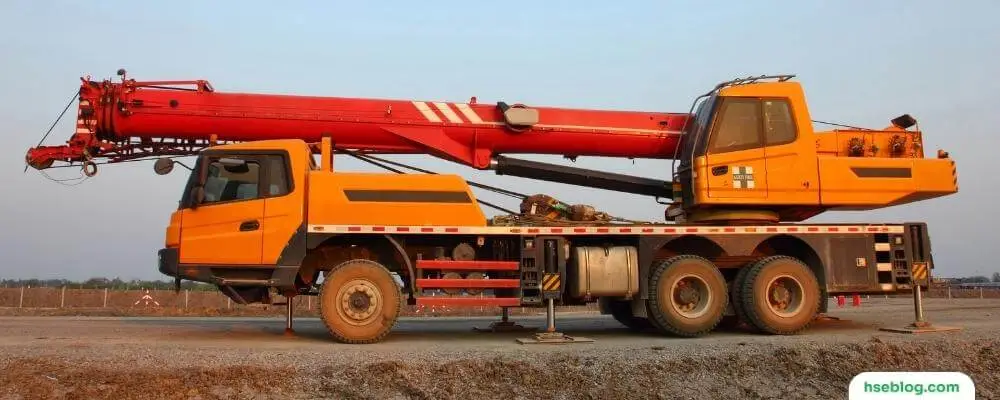
5. Maintenance Misconceptions
The term “maintenance-free” can sometimes be misleading regarding crane operation and care. While certain components may be designed to require minimal maintenance, it does not mean they are exempt from regular inspection or occasional overhaul. Misconceptions surrounding these terms can lead to neglect, which, over time, could result in crane failure.
Here are a few points explaining why this misunderstanding can be detrimental:
- Lifespan Expectations: While certain components might be described as maintenance-free, they still have a finite service life. Over time, even the most robust and well-made components can experience wear and tear and might eventually need to be replaced.
- Overlooked Inspections: When a part is labeled maintenance-free, operators might neglect regular inspections, assuming the part will always function as expected. However, regular inspections are vital for early detection of potential problems. Just because a component does not require frequent maintenance doesn’t mean it isn’t subject to possible failure.
- Environmental Factors: Maintenance-free components are usually designed under ideal operational conditions. However, in the real world, cranes are exposed to harsh environmental conditions like temperature extremes, precipitation, salinity, dust, and more. These can accelerate wear and cause premature failure, even in maintenance-free components.
- Interconnected Systems: Cranes are complex machines where the failure of a single part can impact the whole system. A component marked as maintenance-free might still be affected by the failure of another interconnected part that requires regular maintenance.
Therefore, it’s crucial to interpret manufacturers’ guidelines correctly. Even if a component is labeled as maintenance-free, it should still be regularly inspected and possibly overhauled as part of a comprehensive maintenance plan. Misunderstanding this can lead to serious crane failures, posing potential safety risks and financial loss.
Underlying Issues
Crane failures, as we have pointed out, are often avoidable. The root of many such failures lies in neglect, misconceptions about maintenance requirements, and economic pressures that can influence decision-making.
- Prioritization Issues: Cranes are sometimes overlooked despite being essential equipment because they are not constantly used like a ship’s engine. They are only required during specific operations, such as loading or unloading cargo. This intermittent use can lead to a lower perceived priority regarding maintenance and inspections. However, this perception is incorrect and can lead to catastrophic failure if key components degrade and fail.
- Environmental Wear: Even when not in use, cranes, especially on ships, are exposed to harsh marine environments. Salty air, humidity, and other weather conditions can cause degradation to crane components, including ropes and wires. This constant exposure makes regular inspection and maintenance critical regardless of active use.
- Cost Reduction Efforts: In challenging financial climates, owners and operators often look for ways to reduce operational costs. Unfortunately, maintenance regimes and proactive overhauls are sometimes seen as areas where costs can be cut. However, this short-term saving can result in far more costly repairs or replacements if a crane fails, not to mention the potential for downtime, cargo damage, and even injury or loss of life.
To mitigate these issues, it is crucial to emphasize the importance of regular and thorough crane maintenance and inspections, regardless of the crane’s operational frequency. Balancing cost-saving efforts with safety and long-term equipment health considerations is also important. While reducing costs is understandably a priority, this should not be achieved at the risk of major equipment failure or compromising safety. Proper education about “maintenance-free” components and their actual care requirements is also key in preventing failures due to misconceptions.
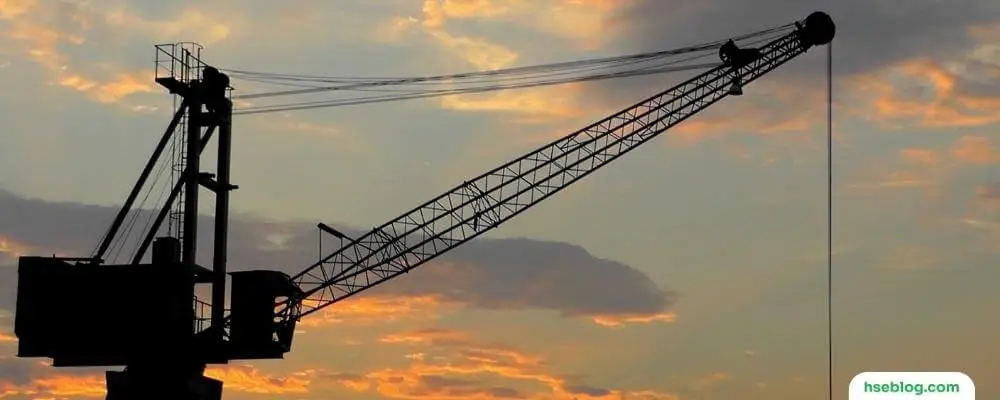
Prevention
Preventative maintenance is indeed key to minimizing the risk of crane failures. Your suggestion of regular, specialized inspections and hydraulic oil analysis is an effective strategy for maintaining crane health. Here’s a more detailed look at these preventative measures:
- Planned Maintenance Regime: A planned maintenance schedule should include regular inspections and care of all crane components. This regimen helps identify potential issues early, allowing for proactive solutions before the problems become severe. Additionally, adhering to manufacturers’ maintenance guidelines ensures the crane operates within its designed parameters, which is crucial for its long-term service life.
- Specialized Inspections: Having the manufacturer or a specialist crane service engineer inspect the ship’s crane every five years can provide a comprehensive assessment of the crane’s condition. Specialists are trained to identify subtle signs of wear or potential issues that may be missed during regular inspections. Including the crane’s hydraulic pumps and motors in these inspections is crucial since these components are vital for the crane’s operation.
- Hydraulic Oil Analysis: The condition of the hydraulic oil can offer valuable insights into the internal condition of the hydraulic pumps and motors. By sending oil samples to a shore-based laboratory for analysis, contaminants and wear debris can be identified. These elements could indicate internal wear or other issues within the hydraulic system. If problems are suspected, further investigations can be carried out, and remedial actions can be taken.
Following these preventative measures can help reduce the risk of crane failures significantly. Although these strategies might require an upfront investment in time and cost, the long-term benefits of preventing costly failures and potential accidents make it worthwhile.
Conclusion
While disruptive and potentially dangerous, crane failures are largely preventable through understanding common causes—wire issues, slew-bearing problems, sheave concerns, mishandling, and maintenance misconceptions—and employing proactive preventive measures. Even in challenging economic climates, it’s critical not to overlook the importance of regular and specialist inspections, maintenance, and strategies like hydraulic oil analysis.
These measures may require an upfront investment but can prevent major failures, ensuring safe, efficient operations and significant long-term savings. Understanding these factors and implementing preventive measures are essential for safer and more reliable crane operations.