Robots have become integral to numerous industries in the contemporary era of rapid technological advancement. Robotic systems are revolutionizing our work from manufacturing and logistics to healthcare and customer service. However, with the extensive benefits that robots bring, various challenges and risks come.
This blog delves into the captivating world of robotics in the workplace, its potential hazards, and the various causes of accidents. We aim to equip you with the knowledge and awareness necessary to create a safe and productive environment for humans and robots. Whether you are an employer looking to integrate robotics into your business, an employee working alongside these incredible machines, or just a curious reader, this article promises to be an enlightening journey through the complex dynamics of modern robotics. So, fasten your seat belts as we explore the fascinating intersection of technology and safety in the workplace.
Robots In The Workplace | Hazards and Causes Of Accidents
In the era of automation, robots have become an integral part of the workplace, especially in manufacturing, warehousing, and logistics. While they offer several benefits like increased productivity, efficiency, and often improved safety, their presence can also introduce new hazards. Understanding these hazards and the causes of accidents involving robots is essential to mitigate risks and ensure a safe working environment.
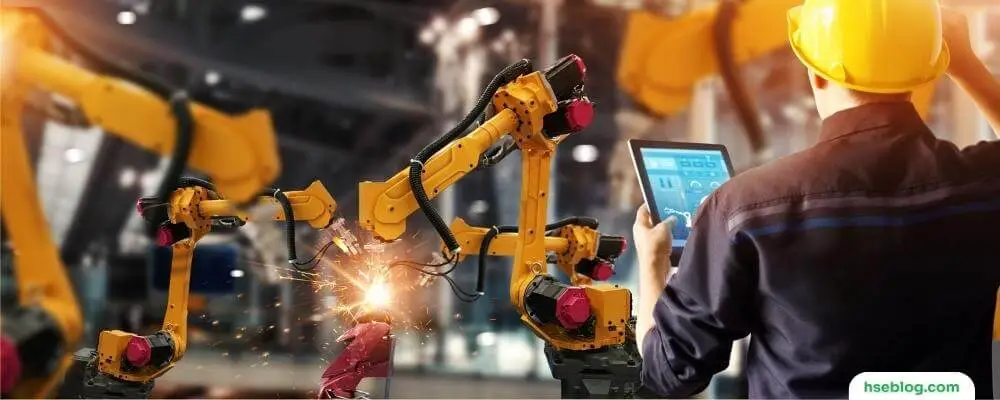
Types of Hazards Involving Robots in the Workplace
Robots are increasingly used in workplaces to automate tasks, increase efficiency, and improve productivity. However, they can also introduce new hazards and risks to the work environment. Here are some types of hazards involving robots in the workplace:
- Collision with Equipment: Robots may not be able to detect obstacles in their path, particularly if they are operating based on predefined programming. This can lead to collisions with machinery, storage racks, or other objects in the workplace. Such collisions can cause damage to equipment, create debris, or knock over heavy objects that could injure nearby workers.
- Human-robot Interaction: When robots and humans share the same workspace without sufficient safety measures, humans risk being struck by robotic arms or caught between the robot and other objects. This can result in injuries ranging from minor bruises to severe crushing injuries.
- Mechanical Failures: Robots have many moving parts. Mechanical failure in any of these parts, like a loose arm or a failed gripper, can cause unexpected movements or the release of parts. For example, a gripper malfunction could cause the robot to drop a heavy object, posing a risk to anyone below.
- Electrical Hazards: Robots rely on electrical systems for power and control. Malfunctioning components, frayed cables, or short circuits can cause electrical shocks to anyone who comes into contact with the robot. Electrical malfunctions can also lead to fires, especially in environments with flammable materials.
- Programming Errors: If a robot is programmed incorrectly, it may move in unexpected ways or perform actions that are not safe. For example, an incorrectly programmed robot might move too fast or follow a path that brings it into contact with workers or equipment.
- Release of Substances: Robots handling chemicals, hot liquids, or gases might inadvertently release these substances if not handled correctly or if a container is damaged. Such releases can cause chemical burns, fires, or harmful exposure to toxic substances.
- Ergonomic Hazards: If the design of workstations where humans interact with robots is not ergonomic, it can cause strains and musculoskeletal disorders. For example, if workers need to reach or bend awkwardly to interface with a robot, this can lead to long-term injuries.
- Cybersecurity Threats: Robots, especially those connected to networks, can be vulnerable to hacking or malware. A compromised robot can behave unpredictably or maliciously, posing physical threats to workers or other equipment.
- Noise Pollution: Robots, particularly industrial ones, can be quite noisy. Continuous exposure to high noise levels can lead to hearing loss or other auditory problems among workers.
- Vibrations: Certain robots generate vibrations during operation. Prolonged exposure to these vibrations can cause health issues for nearby workers, including hand-arm or whole-body vibration syndrome.
To mitigate these hazards, it is essential to conduct risk assessments, provide adequate training, implement safety measures such as barriers and emergency stop systems, and ensure regular maintenance and monitoring of robotic systems.
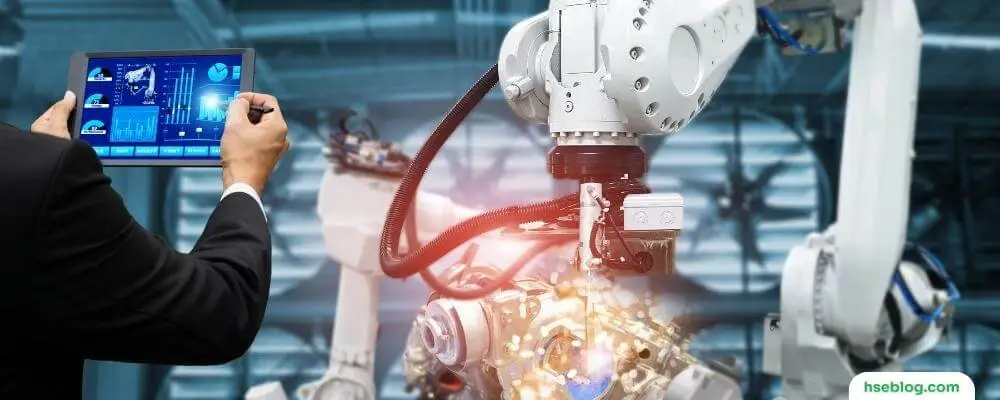
Causes of Accidents Involving Robots
Accidents involving robots in the workplace can occur due to various causes. Here are some common factors that can contribute to accidents involving robots:
- Lack of Training: Proper training is essential for employees working with or near robots. Without adequate training, employees may not understand how robots operate, their potential dangers, or the proper procedures to ensure safety. For example, an untrained employee might not know the safe distance to keep from a robot or how to shut down a robot in case of an emergency.
- Inadequate Safety Measures: When a workplace does not have sufficient safety barriers, sensors, or emergency stop functions, it increases the risk of accidents. These measures are designed to prevent or quickly halt unsafe situations. For example, without light curtains or sensors, a robot may not stop when a human inadvertently enters its operating space.
- Human Error: Even well-trained individuals can make mistakes, such as miscalculating a robot’s range of motion, forgetting to enable safety settings, or entering a robot’s work area without proper clearance. These errors can result in collisions, entrapments, or other accidents.
- Software Glitches: Robotic operations are often governed by complex software. Bugs, errors, or unintended interactions within this software can cause robots to move unpredictably, ignore safety settings, or otherwise operate unsafely.
- Improper Maintenance: Robots require regular maintenance to operate safely. Failure to properly maintain robots can result in worn components, misaligned sensors, or other issues that can lead to accidents. For instance, a failing motor might cause a robot arm to swing unpredictably.
- Communication Failures: In modern automated systems, robots or central control systems may communicate. If there’s a breakdown in this communication, robots might not synchronize their movements correctly, possibly resulting in collisions or other unsafe situations.
- Environmental Factors: Environmental changes, such as lighting, temperature, or contaminants, can affect the robot’s performance. For instance, a sensor might malfunction in high heat or excessive dust, causing the robot to not recognize obstacles or stop when needed.
- Overriding Safety Protocols: Sometimes, employees might deliberately override safety protocols to speed up production or troubleshooting. This can put them and others at risk as safety mechanisms like emergency stops or barriers may not work as intended.
- Incompatible Components or Peripherals: If a robot is fitted with tools or peripherals that it’s not compatible with or that haven’t been properly tested, it could behave unpredictably. For example, an inappropriately heavy tool might unbalance a robot arm, causing it to swing or move erratically.
- Poor Risk Assessment and Planning: A thorough risk assessment and planning process should be carried out before introducing robots into the workplace. Failure to identify risks or plan for different scenarios can lead to safety procedure and protocol gaps.
Recognizing these causes and implementing comprehensive training, safety measures, maintenance schedules, and proper planning can significantly reduce the risk of accidents involving robots in the workplace. Also, fostering a safety culture and open communication allows for continuous improvement in risk management.
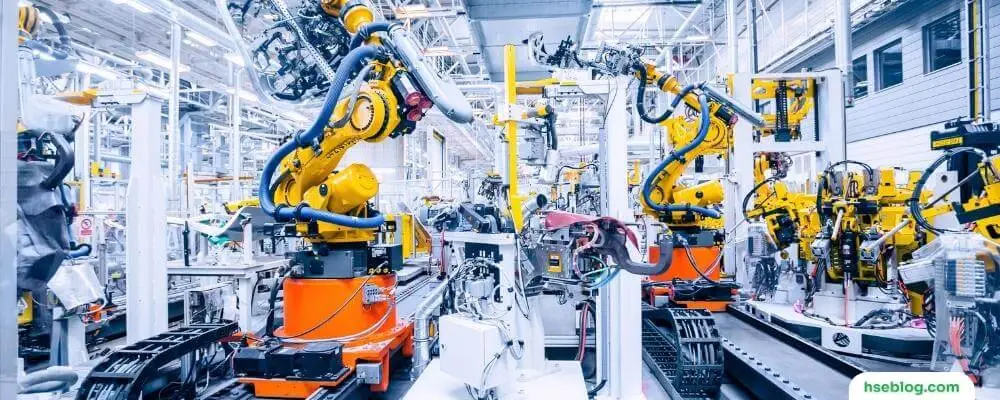
Steps for Minimizing Hazards and Preventing Accidents
Minimizing hazards and preventing accidents involving robots in the workplace requires a proactive approach to safety. Here are some steps to consider:
Regular Training and Education:
Continuous training and education ensure employees know the robots they work with or around. This includes understanding the robots’ functionalities, limitations, and potential hazards. Training should also encompass best practices in operating and maintaining robots and emergency procedures. Regular refresher courses should be scheduled to ensure that employees’ knowledge remains current, especially when there are technological updates or changes.
Risk Assessments:
Conducting a comprehensive risk assessment is important before robots are integrated into the workplace. This involves analyzing the workplace environment, the tasks the robots perform, and the interaction between robots and humans. Identifying potential hazards helps in developing strategies to mitigate or eliminate these risks. Risk assessments should be ongoing, with regular reviews and updates as conditions change.
Implement Safety Devices:
Safety devices such as light curtains, interlocking guards, and emergency stop buttons are crucial in preventing accidents. Light curtains, for example, create an invisible barrier that, when broken, immediately stops a robot’s movement, preventing potential collisions with humans. Interlocking guards ensure that robots can only operate when protective guards are in place, and emergency stop buttons allow for an immediate shutdown of robotic systems in case of a malfunction or hazard.
Safety Barriers:
Physical barriers such as fences or partitions separate robots from human work areas, especially in high-risk zones. These barriers ensure that even if a robot malfunctions, the chances of it causing harm to human workers are significantly reduced. The design and material of these barriers should be tailored to the specific type of robotic system and the nature of the work being performed.
Regular Maintenance and Inspection:
Regular maintenance and inspection of mechanical and electrical components are necessary to ensure that robots function properly and safely. This includes checking for wear and tear, calibrating sensors, and ensuring all safety devices function properly. A maintenance log should be kept to track any issues and the actions taken to resolve them.
Clear Communication Protocols:
Clear communication protocols are vital in environments where multiple robots and human workers operate. This includes ensuring that robots can communicate with each other to avoid collisions and that human workers are informed of the robots’ statuses and movements. Communication protocols also encompass reporting and addressing any safety concerns promptly.
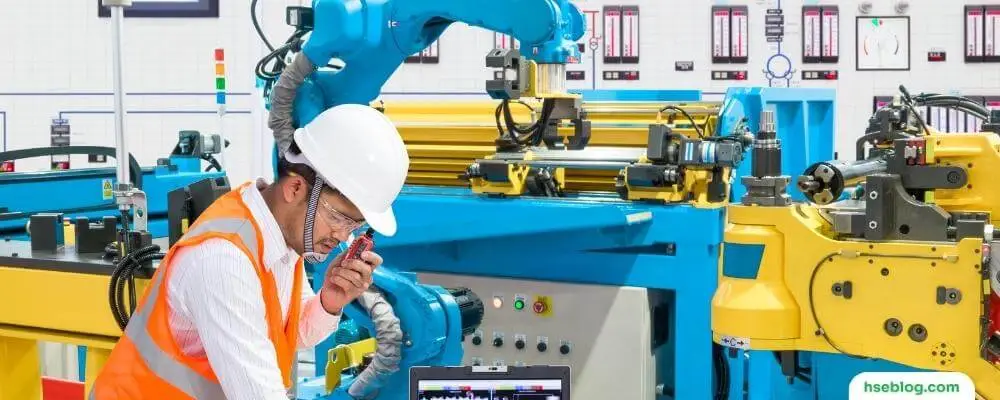
Software Updates and Monitoring:
Keeping the robots’ software up to date is important to ensure that they are equipped with the latest safety features and that any known bugs or issues have been addressed. In addition, continuous monitoring of the robots’ behaviors and performance can help detect any anomalies that could indicate a malfunction or security breach early.
Emergency Protocols:
Establishing emergency protocols helps ensure that in the event of power failures, malfunctions, or accidents, actions are taken swiftly to minimize damage and protect human workers. This includes knowing how to shut down robots safely, evacuate the area, and administer first aid if needed. Regular drills and training on these emergency protocols are essential to prepare workers to act effectively in crises.
By combining these steps with a strong safety culture and the involvement of employees in safety planning and implementation, employers can create a safer working environment with robots.
Conclusion
In conclusion, as robots increasingly become a staple in various industries, it is imperative to recognize and address the potential hazards and causes of accidents associated with their integration into the workplace. By prioritizing safety through proper training, risk assessments, maintenance, and implementing protective measures, we can harness the remarkable efficiencies and capabilities that robots offer while ensuring a secure and harmonious coexistence with human employees. Being proactive and informed is the key to unlocking the full potential of robotics without compromising safety and well-being.