Creating a safe and healthy work environment is a fundamental responsibility for every organization. To achieve this, safety professionals use a structured framework known as the Hierarchy of Control Measures. This systematic approach prioritizes methods for minimizing or eliminating workplace hazards, ranking them from the most effective to the least effective.
Understanding and applying the hierarchy allows employers to make smarter, more strategic decisions about hazard control, focusing first on the methods that offer the highest level of protection. While the ultimate goal is to remove hazards entirely, it’s not always possible — and in many cases, a combination of measures may be necessary to ensure maximum safety.
In this guide, we will explore the five levels of the Hierarchy of Control Measures—Elimination, Substitution, Engineering Controls, Administrative Controls, and Personal Protective Equipment (PPE). Each level plays a critical role in protecting workers and building a culture of safety. By the end, you’ll be equipped with the knowledge to better identify hazards, assess risks, and choose the most effective control measures for your workplace.
What’s the Hierarchy of Control?
The Hierarchy of Control Measures is a systematic approach to minimizing or eliminating workplace hazards and associated risks. This approach categorizes various control measures in order of their effectiveness, from the most effective to the least effective. By understanding and applying this hierarchy, employers can create a safer work environment and protect the health and well-being of their employees.
The Hierarchy of Control Measures comprises five levels, in decreasing order of preference and effectiveness:
- Elimination
- Substitution
- Engineering Controls
- Administrative Controls
- Personal Protective Equipment (PPE)
As we move through each level of the hierarchy, the control measures become less effective in mitigating risks. Therefore, the goal is to implement solutions as high in the hierarchy as possible. However, it is essential to understand that the most effective solution may not always be feasible or practical, and a combination of control measures might be necessary.
In the following sections, we will delve into each level of the Hierarchy of Control Measures, providing a clear understanding of each step and its importance in creating a safer workplace. By the end of this article, you will have the knowledge to effectively identify hazards, assess risks, and implement the most suitable control measures for your work environment.
Hierarchy Of Control Measures: 5 Levels
The hierarchy of control measures is a system that outlines the order in which control measures should be implemented to minimize or eliminate workplace hazards. There are five levels in the hierarchy of control measures, listed in order of priority:
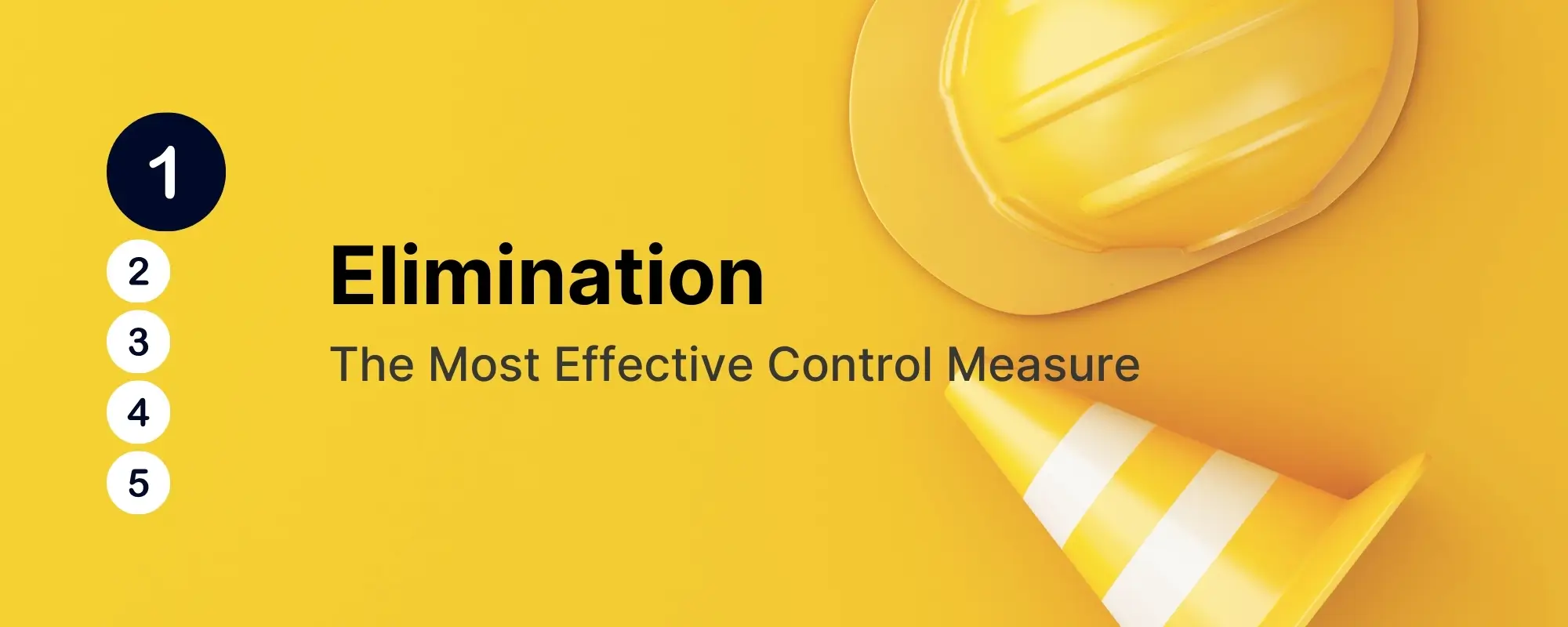
1. Elimination – The Most Effective Control Measure
Elimination is the highest level in the Hierarchy of Control Measures, and it involves completely removing the hazard from the workplace. This means the hazard is no longer present, and no control measures are necessary. Elimination is the most effective control measure as it eliminates the risk of exposure to the hazard, ensuring that workers are safe from harm.
Examples of elimination may include:
- Replacing a hazardous substance with a less hazardous alternative.
- Automating a task that requires workers to be exposed to a hazardous environment.
- Removing a piece of machinery or equipment that poses a safety risk.
Benefits of elimination as the most effective control measure:
- Complete elimination of the hazard: Elimination eliminates the hazard from the workplace, ensuring that workers are not exposed to any risks associated with the hazard.
- Cost-effective: Elimination is often the most cost effective solution as it reduces the need for other control measures, such as engineering controls or personal protective equipment.
- Reduced liability: Elimination reduces the risk of accidents and injuries, reducing an organization’s liability for compensation claims and legal action.
Strategies for implementing elimination:
- Identify the hazard: The first step in implementing elimination is to identify the hazard in the workplace. This may involve conducting a hazard assessment or consulting with safety professionals.
- Consider alternatives: Once the hazard has been identified, consider alternatives to completely eliminate the hazard from the workplace. This may involve finding less hazardous alternatives or redesigning processes to remove the need for hazardous substances.
- Implementation plan: Once an alternative has been identified, plan for its implementation. This may involve working with suppliers or redesigning processes to ensure the alternative suits the task.
- Monitor and review: Finally, monitor and review the elimination strategy to ensure it is effective and sustainable. This may involve regular testing or inspections to ensure that the alternative works as intended and that workers are not exposed to new hazards.
Elimination is the most effective control measure in the Hierarchy of Control Measures. By identifying hazards and considering alternatives, organizations can eliminate hazards from the workplace, ensuring worker safety and reducing liability. While not always feasible, elimination should always be the first option when implementing control measures.
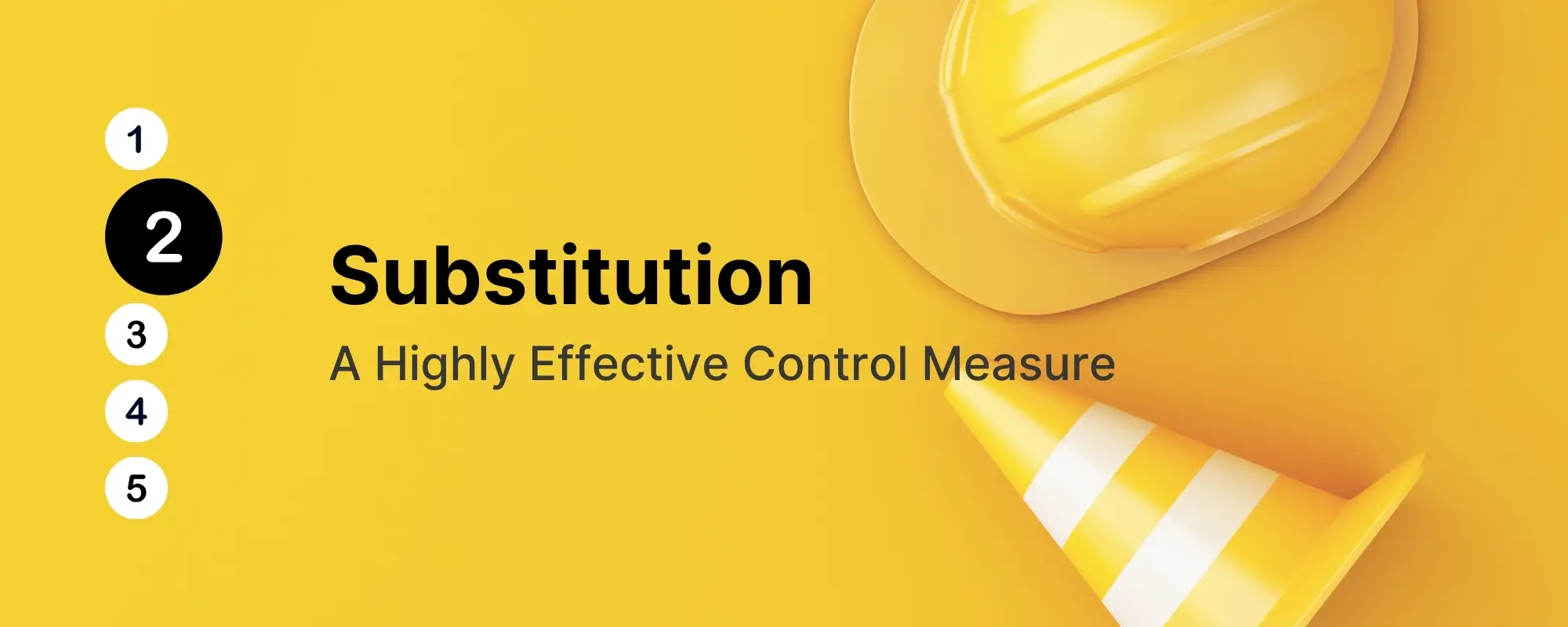
2. Substitution – A Highly Effective Control Measure
Substitution is the second level in the Hierarchy of Control Measures, and it involves replacing a hazardous substance or process with a less hazardous alternative. This means that the risk of exposure to the hazard is reduced, but the hazard is not entirely eliminated, as in the case of the elimination control measure.
Examples of substitution may include:
- Replacing a hazardous chemical with a less toxic alternative
- Replacing a manual task with an automated one
- Using non-slip flooring in place of slippery flooring to reduce the risk of falls
Benefits of substitution as a control measure:
- Reduced risk: Substitution reduces the risk of exposure to hazardous substances or processes by replacing them with less hazardous alternatives.
- Improved health and safety: By reducing exposure to hazards, substitution improves the health and safety of workers.
- Cost-effective: Substitution can be a cost-effective solution, as it often reduces the need for other control measures, such as engineering controls or personal protective equipment.
Factors to consider when selecting substitutes:
- Chemical properties: When selecting substitutes for hazardous chemicals, it is essential to consider their chemical properties, including toxicity, flammability, and reactivity.
- Performance: Substitutes should be evaluated for their effectiveness in performing the same or similar tasks as the hazardous substance or process.
- Compatibility: Substitutes should be compatible with existing equipment, processes, and procedures in the workplace.
- Environmental impact: It is essential to consider the environmental impact of the substitute, including its potential for creating new hazards or environmental pollution.
- Cost: The cost of the substitute should be considered, including any costs associated with training, installation, and maintenance.
Substitution is a highly effective control measure that involves replacing hazardous substances or processes with less hazardous alternatives. By considering factors such as chemical properties, performance, compatibility, environmental impact, and cost, organizations can select suitable substitutes to reduce the risk of exposure to hazards in the workplace. While not as effective as elimination, substitution is an essential control measure in creating a safer work environment.
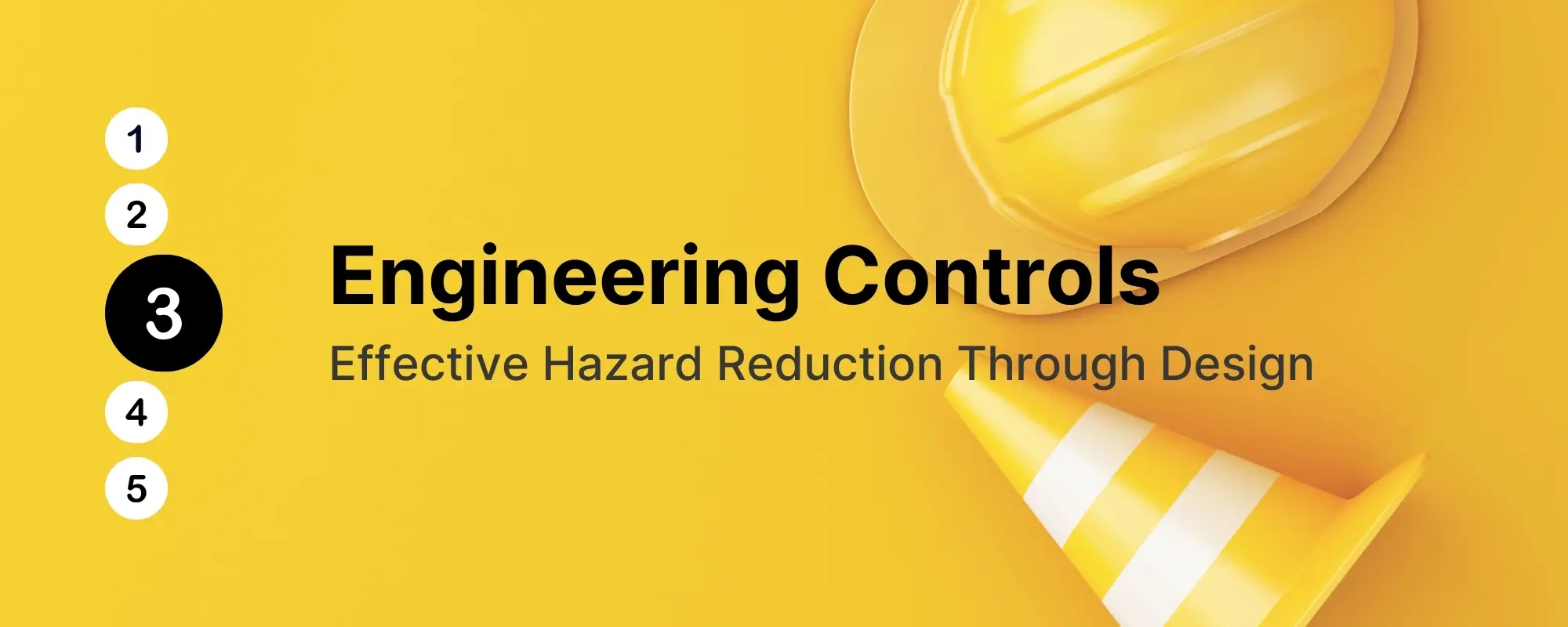
3. Engineering Controls – Effective Hazard Reduction Through Design
Engineering controls are physical or mechanical systems designed to minimize or eliminate exposure to hazards in the workplace. They are the third level in the Hierarchy of Control Measures and include measures such as process controls, enclosures, and ventilation.
Examples of engineering controls may include:
- Installing barriers or shields to prevent contact with moving machinery parts
- Using ventilation systems to remove hazardous airborne particles
- Implementing ergonomic workstation designs to reduce physical strain on workers
Types of engineering controls:
- Process control: This type of engineering control involves modifying the work process to reduce or eliminate exposure to hazards. Examples of process controls include using automated machinery to eliminate the need for manual tasks or implementing job rotation to reduce repetitive strain injuries.
- Enclosure: Enclosures involve using barriers, enclosures, or other physical means to isolate the hazard from the worker. Examples of enclosures include fume hoods, glove boxes, or machine guarding.
- Ventilation: Ventilation systems use air movement to remove hazardous substances or contaminants from the workplace. Examples of ventilation include local exhaust ventilation systems, which remove airborne contaminants at the source, and dilution ventilation systems, which remove contaminants by mixing them with fresh air.
Benefits:
- Effective hazard reduction: Engineering controls are highly effective in reducing or eliminating exposure to workplace hazards.
- Long-term solutions: Unlike administrative controls and personal protective equipment, engineering controls are permanent solutions that require less ongoing maintenance and monitoring.
- Improved productivity: Engineering controls can also increase productivity by improving the work environment and reducing worker fatigue and strain.
Limitations:
- Upfront costs: Engineering controls can be expensive to install initially, requiring significant upfront costs.
- Limited application: Engineering controls may not be applicable in all work environments, and some hazards may require multiple engineering controls to address effectively.
- Maintenance and upkeep: Engineering controls require ongoing maintenance and upkeep to ensure they work effectively.
Engineering controls are a highly effective control measure in the Hierarchy of Control Measures. By designing physical or mechanical systems to minimize or eliminate exposure to hazards in the workplace, organizations can create a safer work environment for their employees. While upfront costs and ongoing maintenance can be a limitation, the long-term benefits of engineering controls in reducing workplace hazards and improving productivity make them a valuable investment.
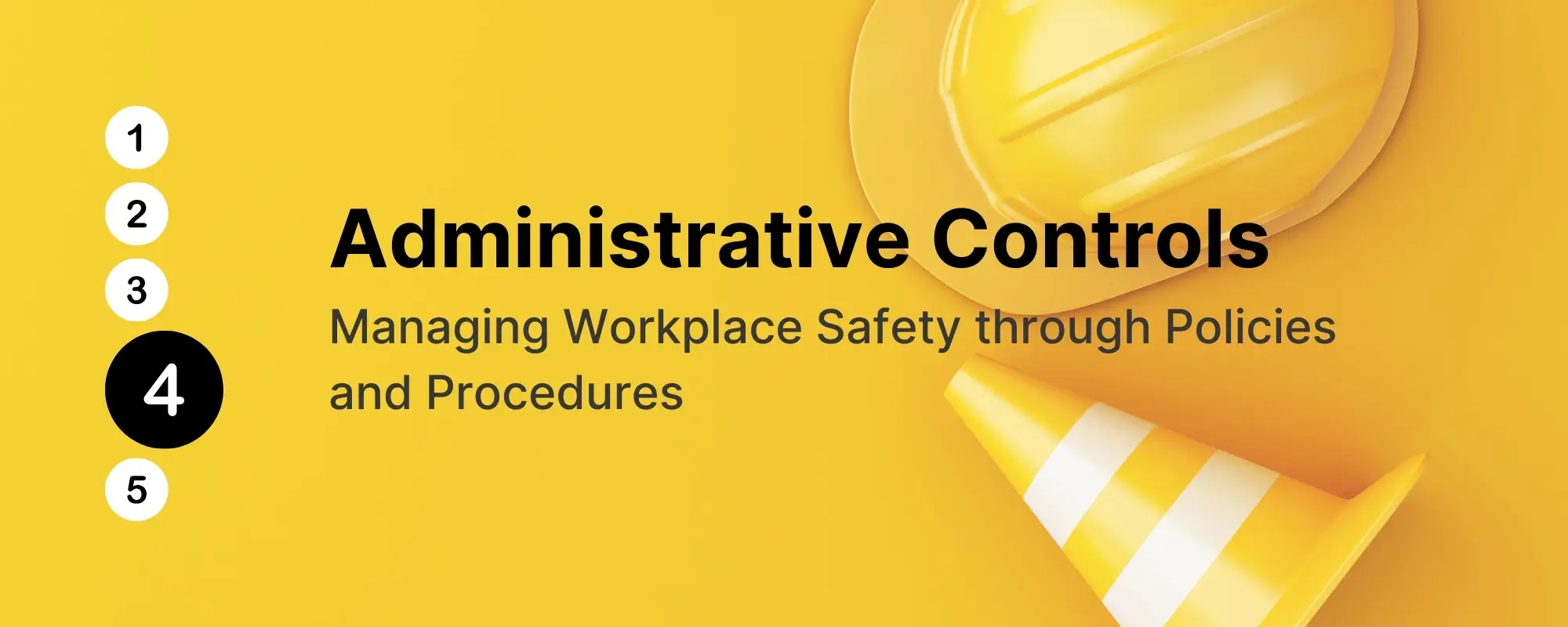
4. Administrative Controls – Managing Workplace Safety through Policies and Procedures
Administrative controls focus on changing work practices or policies to minimize the risk of exposure to workplace hazards. They are the fourth level in the Hierarchy of Control Measures and include measures such as work practices, training, and maintenance.
Examples of administrative controls may include:
- Implementing a policy for working alone in hazardous areas
- Providing training on safe work practices for handling hazardous materials
- Implementing a maintenance program to ensure that equipment is properly maintained and inspected regularly
Types of administrative controls:
- Work practices refer to how work is performed to minimize or eliminate exposure to hazards. Examples of work practices include safe lifting techniques or requiring the use of personal protective equipment.
- Training: Training provides information and instructions to workers on how to perform work safely. Examples of training include hazard communication training or emergency response training.
- Maintenance involves keeping equipment, machinery, or facilities in good working condition to minimize the risk of exposure to hazards. Examples of maintenance include regular inspections, repairs, and replacements.
Benefits:
- Flexibility: Administrative controls can be implemented quickly and easily, making them a flexible and adaptable solution for managing workplace hazards.
- Low cost: Administrative controls can be implemented at a lower cost than engineering controls or personal protective equipment.
- Improved worker participation: Administrative controls often involve workers developing policies and procedures, increasing worker participation and engagement.
Limitations:
- Limited effectiveness: Administrative controls may not always minimise or eliminate exposure to hazards, as they rely on human behaviour and compliance.
- Dependence on training: Administrative controls’ effectiveness depends on effective training, which can be time-consuming and expensive.
- Maintenance and monitoring: Like engineering controls, administrative controls require ongoing maintenance and monitoring to ensure effectiveness.
Administrative controls are important in the Hierarchy of Control Measures. Organizations can manage workplace hazards by changing work practices or policies, providing training, and implementing maintenance programs. While administrative controls may not be as effective as elimination or substitution, they can be a flexible and cost-effective solution for managing workplace safety.
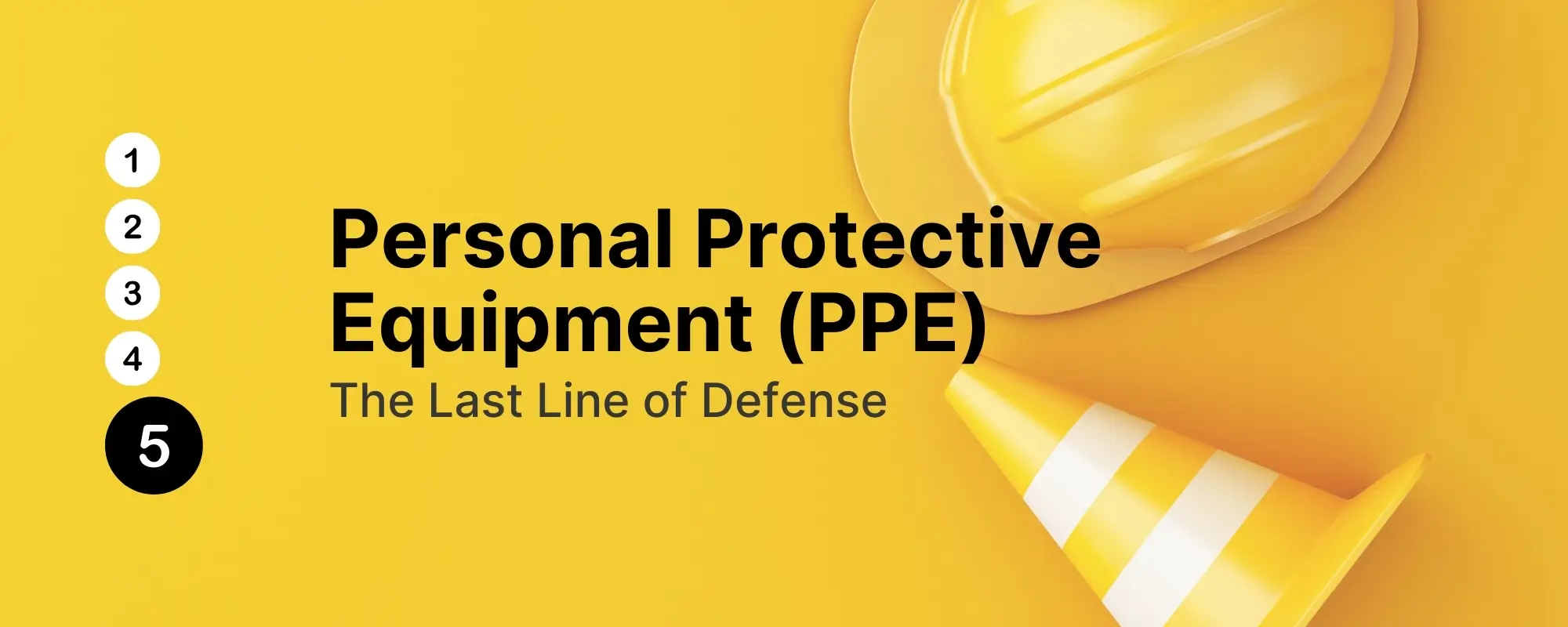
5. Personal Protective Equipment (PPE) – The Last Line of Defense
Personal Protective Equipment (PPE) is the fifth and last level in the Hierarchy of Control Measures, and it includes clothing and equipment designed to protect workers from workplace hazards. PPE is considered the last line of defence against hazards and is only implemented when elimination, substitution, engineering controls, or administrative controls are not feasible or insufficient to ensure worker safety.
Examples of PPE may include:
- Eye protection, such as safety glasses or goggles
- Hearing protection such as earplugs or earmuffs
- Respiratory protection such as respirators or masks
- Protective clothing such as gloves, aprons, or full-body suits
Types of PPE:
- Eye protection: Eye protection protects the eyes from hazards such as flying debris, dust, or chemicals. Examples of eye protection include safety glasses, goggles, and face shields.
- Hearing protection: Hearing protection is designed to protect the ears from loud noises that can cause hearing damage. Examples of hearing protection include earplugs and earmuffs.
- Respiratory protection protects the lungs from airborne hazards such as dust, fumes, or vapours. Examples of respiratory protection include respirators, masks, and air-purifying respirators.
- Protective clothing protects the skin from physical, chemical, or biological hazards. Examples of protective clothing include gloves, aprons, and full-body suits.
Selection, use, and limitations of PPE:
- Selection: The selection of PPE should be based on the type of hazard and the degree of protection required. The PPE should be appropriate for the task and provide a comfortable fit for the worker.
- Use: PPE should be worn correctly and consistently to provide the necessary protection. Workers should be trained on the proper use, care, and maintenance of PPE.
- Limitations: PPE has limitations and may not provide complete protection from hazards. It can be uncomfortable and may limit mobility, vision, or communication. PPE must be inspected regularly to ensure it is in good condition and functioning effectively.
Personal Protective Equipment (PPE) is the last line of defence in the Hierarchy of Control Measures. While not as effective as elimination, substitution, engineering, or administrative controls, PPE can provide valuable protection against workplace hazards. Proper selection, use, and maintenance of PPE are essential to ensure its effectiveness in protecting workers from harm.
Conclusion
The Hierarchy of Control Measures provides a clear, systematic framework for reducing workplace hazards and protecting employee health and safety. By understanding and applying the five levels—Elimination, Substitution, Engineering Controls, Administrative Controls, and Personal Protective Equipment (PPE)—organizations can prioritize the most effective strategies first and create safer work environments.
While elimination and substitution offer the highest levels of protection, it is not always possible to remove all hazards. In such cases, combining multiple control measures is often necessary to achieve the best outcomes. Importantly, reliance on lower-level controls like administrative practices and PPE should be seen as a last resort, not a primary solution.
Ultimately, adopting a proactive approach to hazard control not only ensures regulatory compliance but also fosters a strong safety culture, boosts worker morale, and enhances operational efficiency. By consistently applying the Hierarchy of Control, businesses can protect their most valuable asset — their people.